Abstract
The efficiency of the AC-magnetic field usage for resource-saving activation of the reaction mixture in the ferritization process with the extraction of heavy metals ions from galvanic waste has been confirmed. The one of the key parameters of the ferritization process—the ratio of the concentration of iron ions to the total concentration of other metal ions on the quality of galvanic waste processing has been investigated. It is determined that under the optimal processing conditions (ratio of concentrations of iron ions to other heavy metal ions 3.5 ÷ 4/1) the residual concentrations of heavy metal ions decrease to the values: Fe2+;3+—0,1; Ni2 +—0.26; Cu2 +—0.2; Zn2 +—0.19 mg/dm3. It is established that the AC-magnetic field activation provides the metal ions extraction degree of 99.96%, and also has undeniable energy advantages in comparison with thermal technique: the energy consumption is reduced by more than 60%. This indicates the suitability of purified water for reuse in galvanic production due to the requirements for the heavy metal ions content. Also, the structural studies of ferritic sediments shown that samples obtained at the ratio of heavy metal ions concentrations 4/1 phases characterized by the maximum content of crystalline ferromagnetic ferrite (Ni0.53Cu0.3 Zn0.17Fe2O4) ≥ 76% were detected.
1. Introduction
Among the research priority areas in the field of natural and technogenic safety, the special attention is devoted to the processing and disposal of toxic waste. One of the major environmental issues is the formation and accumulation of the sediments in galvanic plants as a result of the most common alkaline wastewater treatment. These sediments have II–III hazard category (Zueva et al., Citation2021) and consists of various heavy metals hydroxides (nickel, copper, zinc, chromium, cobalt, iron, etc.). The composition of electroplating sludge depends on the following factors: the surface of the processed material; chemical composition of solutions and electrolytes; type of neutralizing or precipitating reagent. According to statistics the volume of galvanic sediments in Eastern Europe reaches 15 million tons and is constantly growing every year, while the rate of their processing and disposal is extremely low (Brožová et al., Citation2020). In addition, during the storage of such toxic sludges on an open surface, under the influence of atmospheric precipitation, ions of heavy metals, due to the easy dissolution of hydroxides in acidic environments, are leached from the places of their accumulation into the soil and water bodies, thereby causing irreparable danger to the entire ecosystem. When the industrial areas placed within the urban zone such sediments are a source of high technogenic impact on the environment and its waste dumping in special disposal sites is unprofitable (Marcus et al., Citation2020). Also, when storing galvanic sludge in accumulators, in addition to damage to the environment, a large amount of valuable raw materials is lost at the same time. Reuse of materials extracted from sludge, on the contrary, makes it possible to save natural resources and reduce the burden on the ecosystem. Therefore, it is essential to develop effective techniques of processing and disposal of waste, especially containing valuable compounds of heavy metals, as the final stage of waste management in the galvanic industry.
The difficulties of sludge utilization are related to their following characteristics: high humidity (90–95%); multicomponent; variable composition depending on the performance of various electroplating processes; large volume; the instability of some compounds, that is, the change in the composition of the sludge over time. The existing techniques of valuable components extracting from the sediments of galvanic production are economically and environmentally inefficient. They require the multi-stage procession with significant amount of reagents, electricity and consume significant capital investment. The results of research on extraction of heavy metal compounds from galvanic sediments by dissolving them in sulfuric acid are presented by Vilarinho et al. (Citation2017). The disadvantage of this technique is using of acid with high ecological dangerous and impossibility to separate the specific components. Fokina et al. (Citation2019) have presented a new direction in solving the problems of chemical stabilization of waste, the ferritization technique. The ferritization process consists of co-precipitation of mixture of bivalent and trivalent iron and other heavy metals while oxidation of the reaction mixture. As a result of using this technique the low toxic chemically stable ferrites of heavy metals (hazard compounds of class IV) are obtained. They can be stored in open sites without danger. Moreover, Igarashi et al. (Citation2020) have showed that this technique provides a high degree of extraction of heavy ions from liquid industrial waste.
Also, it is known that in distinction from the galvanic sludge neutralization, the possibilities of utilization of ferritic sludge are significantly expanded. It can be used in the production of low-coercivity high-frequency materials (OYu et al., Citation2013), ferromagnetic fabrics (Birčáková et al., Citation2019), as well as radio-absorbing coatings (Ying et al., Citation2021). An alternative is also the direct use of ferrite compounds in the production of alkaline cements (Kovalchuk, Kochetov et al., Citation2019a). Previous research has shown that such cements are resistant to aggressive environment and have a significant range of unique operational properties. The alkaline cements are safely secure in their structure radioactive and heavy metals not only on the physical but also on the chemical level (Kovalchuk, Kochetov et. Al, Citation2019b).
The processing of toxic industrial wastewater and galvanic sediments by the traditional technique of hydrophase ferritization is carried out at temperatures above 75°C with process duration of ≥ 1 hour (Frolova et al., Citation2017). The ferritization process is significantly affected by the concentration ratio of iron ions to total concentration of other metal ions extracted from the solution (Zhou et al., Citation2021), pH (Kovalchuk, Kochetov et al., Citation2019a), temperature (Frolova, Citation2019) and the duration of the phase formation process (Khabarov et al., Citation2017). It should be noted that in works (Frolova, Citation2019; Khabarov et al., Citation2017; Ying et al., Citation2021; Zhou et al., Citation2021) the wastewater treatment of copper, nickel plating galvanizing lines by ferritization was studied, but there is no information about the adaptability of this processing to hydroxide galvanic sediments. In addition, ferritization needs not only a large amount of electrical energy and iron sulfate reagent (Frolova et al., Citation2017) but also a significant amount of water to dilute highly concentrated electrolytes (John et al., Citation2019). The processes at ferromagnet-electrolyte interfaces in the presence of an external magnetic field, such as the vortex motion and phase separation of electrolyte, were investigated (Gorobets et al. Citation2008; Derecha et al., Citation2014; Gorobets et al., Citation2019; Gorobets et al., Citation2013). The technique for determining the characteristic frequencies of fluids motion without changing of the electrolyte structure was proposed in work (Derecha et al., Citation2015, Citation2020).
Kochetov et al. (Citation2019) have showed that an alternative to hydrophase thermal ferritization is the activation of the process by AC-magnetic field. The main advantage of this technique is decrease of process temperature from 75 ° C to 20 ° C. The possibility of recycling hydroxide sediments using the ferritization technique remains is unresolved. In addition, the effect of influence for ratio of heavy metal concentrations on the degree of extraction of metal ions and the structural characteristics of ferritic sludge is not studied.
In the previous work (Kochetov et al., Citation2019), optimal modes of electromagnetic activation of the ferritization process were investigated. This work is devoted to the study of the influence of the ratio of iron ions to other heavy metals ions on the extraction efficiency. In connection with it, the aim of the current work is the processing of sediments by ferritization with AC-magnetic field activation in purpose to improve energy safety of hydro phase ferritization process and determine optimal ratio of iron ions to other heavy metals ions on the extraction efficiency in source solution. That ensures reliable disposal of toxic heavy metals with the formation of safe and, at the same time, valuable ferrite compounds.
2. Materials and methods
As raw material for the experimental study the typical waste of reagent purification of spent electrolytes of galvanic production was used. The galvanic waste was obtained from the metalworking factory. The paste-like hydroxide sediment had pH = 9.81 and a humidity of 93%. The concentration of heavy ions was for Ni2 +—4.73; Cu2 +—2.63; Zn2 +—1.42 g/dm3. The sediment was dissolved in water solution of sulfuric acid (concentration 33%, density 1.25 g/sm3). To carry out the ferritization process in the resulting sludge solution was added chemically pure salt FeSO4 • 7H2O. The ferritization process was studied within the ratio of the initial (P) concentrations of iron ions to the total concentrations of ions of other heavy metals from 2 to 6/1, P = (Fe2+)/Σ ((Ni2+) + (Cu2+) + (Zn2+)). The chemical composition of the reaction mixture for the ferritization process is shown in Table .
Table 1. The chemical composition of the reaction mixture for the ferritization process
To comply with the most acceptable conditions of ferritization process (Kochetov et al., Citation2021), raw solution was diluted with technical water to achieve the required total concentration of heavy metal ions in the range from 6.11 to 14.13 g/dm3 with concentration ratio of iron ions to total ions of other heavy metals (Fe2+)/ ∑ ((Ni2 +) + (Cu2 +) + (Zn2 +)) = 2 ÷ 6/1. The pH was adjusted using 25% solution of chemically pure sodium hydroxide. Partial oxidation of Fe2 + to Fe3 + was carried out by aeration of the reaction mixture with oxidation rate of 0.15 m3/h.
Ferritization was carried out under laboratory conditions in a reactor with a working volume of 1 dm3 both with traditional thermal activation (Yemchura et al., Citation2021) at 75°C and with AC-magnetic field activation at 18 ± 2°C (Kochetov et al., Citation2021). The optimal conditions of AC-magnetic field generation: AC-magnetic field magnitude maxima 0.298 T, frequency in range of 0.5–10 Hz.
To generate an alternating magnetic field, we have developed a controlled rectangular pulse generator that allow to create the sequences of AC-magnetic field. As basis of the generator the ATmega328p microcontroller board was used. The squire voltage pulses with intendent frequency and pulse ratio were generated on 8 digital outputs of the board. Each of the digital outputs is controlled separately it allow to create the complex spatial configuration of alternating magnetic field by using of several electromagnets. The output voltage of the pulses at the digital outputs of the controller board was 5 V, the maximum current is up to 20 mA per output. To amplify the voltage and current the two-stage transistor amplifier was used. As the first stage the ULN2803 was used. It is an assembly of 8 Darlington transistors switches each of them can control a 25 W load, and has built-in protection diodes. In addition to amplification, the ULN2803 acts as a buffer between the board and the load that reducing the risk of controller failure. Small electromagnets can be connected directly to the outputs of this chip. The second stage of keys is used to control a more powerful load. We used switches on FET IRF840, which allow to control 4 kW load. The board was software controlled via the RS-485 serial interface (Figure ).
Such scheme allows to generate both a simple signal with intendent frequency and pulse ratio, and complex packets consisting of a certain number of pulses and pauses between them with given duration. It is also, possible to change the amplitude of each pulse in the packet A simple signal is generated directly by the controller board, packet generation is provided by a program on a personal computer. Pulse packets was generated via script files that was real-time executed. The software provides the ability to use a group of scripts. The duration of pulses and pauses was in range from 1 ms to 65,535 ms, which corresponds to frequencies from 0.0076 Hz to 500 Hz. The amplitude of the pulses was controlled by power supply UTP3305C via the RS-232 interface. There are magnetic fields with magnitude from 0.001 T to 0.3 T. Depending on the magnitude, several different types of electromagnets were used—Helmholtz coils and electromagnets with electric steel Eh0300 poletips.
Other technological parameters of ferritization remained stable: pH = 10.5, process time 25 minutes Residual concentrations of heavy ions after sedimentation were determined on the AA-6800 atomic absorption spectrophotometer (Shimadzu, Japan). pH value of reaction mixture was monitored by the pH meter pH-150 (Belarus).
Structural analysis of dried ferrite sediments was performed by the technique of powder X-ray diffraction in stepwise mode with Cu-Kα radiation on a diffractometer Ultima IV (Rigaku, Japan). Shooting was performed in the range of angles 2θ 6 … 70° with a scanning step of 0.05° and an exposure time of 2 s. The scanning electron microscope-analyzer REMMA-101A (SELMI, Ukraine) was used to study the microstructure of sediments. On the results of four measurements at each experimental point with a confidence level of dispersion 0.95 and error band were estimated (Justin, Citation2018).
3. Results and discussion
3.1. Effect of the concentration ratio of the heavy metal ions on purification degree of the galvanic waste
This research focuses on one of the most important technological parameters of ferritization process—the concentration ratio of iron ions to total concentration for ions of other heavy metals. The results of experiments to determine the effect of the ratio of concentrations of heavy metal ions by means of thermal and AC-magnetic field activation of the ferritization process on the efficiency of extraction of Fe, Ni, Cu, Zn ions from the reaction mixture are shown in Figure .
Figure 2. Dependencies of concentrations for residual heavy metal ions in the purified solution: a—iron; b—nickel; c—copper; d—zinc from the ratio of metal concentrations; activation of the ferritization process: 1—thermal; 2—ac-magnetic field.
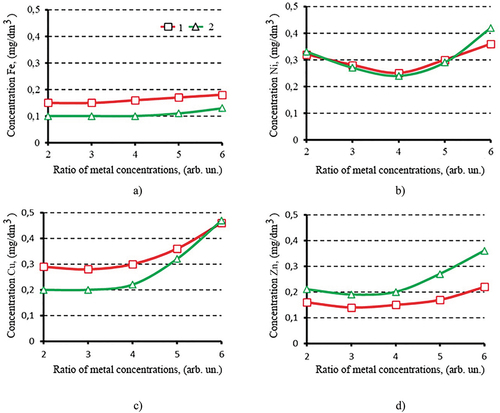
The values of residual concentrations of heavy metals with a relative measurement error not exceeding 4% show that regardless of the ferritization activation technique the residual content of Fe2+, Cu2 +, Zn2 + ions growth with increasing initial concentration ratio of heavy metal ions (Figure ). The residual metal ions content is increased in the concentration ratio ranges 4/1 ÷ 6/1. Exceptions are residual concentrations of Ni2 + ions in the range of 3.5/1 ÷ 4.5/1. Residual concentrations of ions of iron, nickel, copper, zinc in solution after ferritization are in the range of 0.1 ÷ 0.18; 0.24 ÷ 0.42; 0.20 ÷ 0.47; 0.14 ÷ 0.36, respectively. It should be noted that in the case of AC-magnetic field activation with the ratio of metal concentrations in the reaction mixture 6/1, the residual content of Ni2 +, Cu2 +, Zn2 + ions in the purified solution exceeds their concentrations compared to thermal activation. Obviously, this is due to the fact, that at high total concentrations of metals in the reaction mixture (≥ 12 g/dm3) the selected parameters of electromagnetic discharges are not optimal to form the ferrites with dense spinel crystal structure. And according to our assumption, the intermediate solid-phase compounds are formed.
It can be assumed that increasing of AC-magnetic field activation time and reaction mixture aeration velocity the intermediate phases are destroyed and turn into chemically stable ferromagnetic compounds. Then the residual concentrations of metals in the purified solutions will correspond to those for thermal activation of the process. Towards to application issues the purified solution meets the requirements of current European standards for concentration of heavy metals (iron ions—0.3; nickel—5.0; copper—1.0 and zinc—5.0 mg/dm3).
It should be noted that efficiency of metal ions extraction does not depend of activation technique. Same time the AC-magnetic field activation energetically is more efficient. It allows to obtain more perfect crystalline structure. A quality of purified water meets the requirements for galvanic production. In most experiments regardless of ferritization activation technique the efficiency of extraction of metal ions increases: MAC (Maximum Acceptable Concentrations) of Fe2+, Ni2 +, Cu2 +, Zn2 + 0.1 ions; 1.0; 0.3; 1.5 mg/dm3, respectively. In versus to traditional thermal the AC-magnetic field activation of ferritization provides a high degree of extraction of heavy metal ions into environmentally friendly and insoluble compounds with efficiency of 99.997 ÷ 99.998%; 99.957 ÷ 99.962%; 99.953 ÷ 99.960%; 99.903 ÷ 99.942% for 2 +; Ni2 +; Cu2 +; Zn2 + ions, respectively. Thus, the best conditions for the process are achieved at ratios of concentrations of heavy metal ions in the range of 3.5 ÷ 4/1: residual concentrations of heavy metal ions are reduced to the values: Fe2+- 0.1; Ni2 +—0.26; Cu2 +—0.2; Zn2 +—0.19 mg/dm3. Obviously, this is due to the fact that under the influence of different concentration ratios of heavy metals in the solution the dispersed compounds crystallization on the surface of ferromagnetic particles plays leading role but not the sorption of metal ions (Kochetov et al., Citation2021).
3.2. Structure and phase composition of the ferritic sediments
The black-colored dispersed suspension independently of reaction mixture activation is formed. Then its subsequently crystallizes with the dense ferrite structures formation. The structure of sediments obtained at different concentration ratios P = 2/1 ÷ 6/1 and pH value 10.5 was studied.
Structural studies of ferritization sediments indicate their high crystallinity (Figure ). The exception to the above are sediments obtained by electromagnetic pulse activation at ratios of heavy metals 2/1 and 6/1. These sediments are characterized by low intensity and broad reflexes (311, 440, 511). This indicates increasing number of amorphous X-ray phases in these samples compared to others. Diffractograms of sediments with concentrations ratios of heavy metals 4/1, after both techniques of activation are almost identical—the difference in the intensity of reflexes is insignificant. At other ratios of heavy metals concentrations, the samples have a lower degree of crystallinity.
Figure 3. The X-ray diffractograms of sediments obtained at different concentration ratios of iron ions to other heavy metal ions: a—thermal; b—ac-magnetic field activation: —Ni0,53Cu0,3Zn0,17Fe2O4; —(FeNi)O(OH); —Na2SO4.
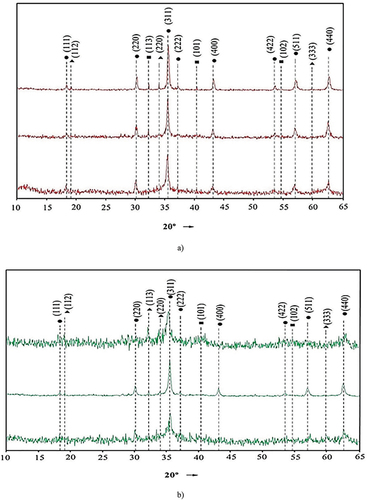
Phase identification in the sediments showed that they contain ferrites of metals with composition Ni0,53Cu0,3Zn0,17Fe2O4. The detected ferrite phases have ferromagnetic properties (Ge et al., Citation2021). Such ferrites of heavy metals, unlike hydroxides, do not dissolve in dilute solutions of strong mineral acids and alkalis at 15–20°C. This is due to the structure of their spinel-type crystal lattice (Zhang et al., Citation2021). It should be noted that in addition to the formation of ferritic phases there are intermediate solid-phases of the ferritization reaction (nickel limonite Fe(Ni)O(OH) with a crystal lattice parameter a = 2.96 Å) remains in the sediment. Detected intermediate Fe(Ni)O(OH) phase with ferromagnetic properties is less stable compared to metal ferrites (Makovskaya & Kostromin, Citation2019). The XRD patterns also showed small quantities of sodium sulfate Na2SO4 with a = 5.84 Å. Its presence is explained by the fact that the obtained ferritic sediments were not washed by distilled water.
The results of quantitative phase analysis (Figure ) showed that increasing concentration ratio of heavy metals ions from 2/1 to 4/1 in the initial solution leads to growth of ferrite phase in the sediment: with the thermal technique of activation by 12.19% and AC-magnetic field—by 19.65%. This in turn reduced the nickel limonite Fe (Ni)O(OH) phase by 8.45% and 12.93%, with thermal and AC-magnetic field activation, respectively, as well as sodium sulfate Na2SO4 by 3.75% and 6.7%, respectively.
Figure 4. Quantitative phase analysis of ferrite sediments obtained at different concentration ratios [Fe2+, 3+]/∑ [Ni2 +] + [Cu2 +] + [Zn2 +] in the reaction mixture: a—thermal, b—ac-magnetic field activation; —Ni0.53Cu0.3 Zn0.17 Fe2O4; —(FeNi)O(OH); —Na2SO4.
![Figure 4. Quantitative phase analysis of ferrite sediments obtained at different concentration ratios [Fe2+, 3+]/∑ [Ni2 +] + [Cu2 +] + [Zn2 +] in the reaction mixture: a—thermal, b—ac-magnetic field activation; —Ni0.53Cu0.3 Zn0.17 Fe2O4; —(FeNi)O(OH); —Na2SO4.](/cms/asset/553d194d-932c-4bcd-a18c-c923464841c7/oaen_a_2143072_f0004_oc.jpg)
A further increase in the concentration ratio of the heavy metals from 4/1 to 6/1 leads to a decrease of the Ni0.53Cu0.3 Zn0.17 Fe2O4 phase in the sediment for the both thermal activation and AC-magnetic field activation by 8.08%, and 26.49%, respectively. On the other hand, the quantity of the (FeNi)O(OH) and Na2SO4 phases increases by 4.96% and 19.18% by 1.12% and 7.31%, for thermal and AC-magnetic field activation, respectively. In addition, the quantitative phase composition of ferritic sediment (Figure ), indicates that the samples obtained by thermal and AC-magnetic field activation and concentrations ratio of heavy metals ions 4/1 has the same phases with the maximum of metal ferrites (more than 76%). It should be noted that in these samples the quantitative phase content is almost the same, the difference does not exceed 1.0%.
It should be noted that the main advantage of the AC-magnetic field activation is its energy efficiency. The energy consumption reduces more than 60% compared to thermal activation (Kochetov et al., Citation2018). In this work, direct measurements of energy consumption were carried out for both thermal and variable AC-magnetic field activation of the process. Measurements showed that the thermal activation of the ferritization process requires 69 W/dm3. At the same time, the activation of such a volume using AC-magnetic field activation requires only 27 W/dm3. That is in good agreement with previous results (Kochetov et al., Citation2019). In this case, the AC-magnetic field activation does not detract of extraction rate and leads to the formation of a sediments with high crystallinity.
The structural analysis correlates with the results of scanning electron microscopy for both types of the process activation (Figure ). These samples contain irregularly spherical crystals with micropores that are formed during the ferrite production process. Thus, they have better sorption capacity for both heavy metal ions and organic matter.
4. Conclusions
Thus, influence of one of the main technological parameters of galvanic waste ferritization—the ratio of concentrations on the degree of removal of heavy metal ions and the quality of ferritic sediments and its suitability for further disposal was studied. The influence of the concentration ratio of iron ions to other heavy metal ions in the reaction mixture with different techniques of activation on the degree of extraction of metals in the ferritization processing of galvanic waste is determined. The optimal concentrations ratios of heavy metal ions are 3.5 ÷ 4/1. Under these concentrations and treatment conditions of pH = 10.5; duration of the ferritization process 15 min; aeration rate 0.15 m3/h the residual concentrations of heavy metal ions decrease to values of Fe2+- 0.1; Ni2 +—0.26; Cu2 +—0.2; Zn2 +—0.19 mg/dm3. The degree of their removal from the reaction mixture is 99.96%. The purified by this technique aqueous solution is suitable for reuse in galvanic production according to the maximum acceptable concentrations content of heavy metal ions.
The structural investigation of the obtained sediments showed the presence of the metal ferrites, iron-nickel oxyhydroxide and sodium sulfate. In the sediments obtained at the concentration ratio of heavy metal ions 4/1, phases characterized by the maximum content of heavy metals ferrite phases (Ni0.53Cu0.3 Zn0.17 Fe2O4) ≥ 76% were detected. These sediments obtained at the best concentrations ratio of heavy metal ions equal 4/1 and different techniques of activation has high chemical resistance compared to sediments obtained by traditional reagent wastewater treatment.
Also, the undoubted technical, economic and environmental advantages of the AC-magnetic field activation, compared to traditional reagent technique of the ferritization process are shown. The efficiency of energy-saving application of AC-magnetic field for ferritization process activation with amplitude of magnetic induction of 0.298 T and frequency from 0.5 to 10 Hz is established. The consumption of electricity for AC-magnetic field activation in comparison with thermal one is reduced by 60%. That makes possible to reduce the cost of this technique, and thus make it attractive for industrial applications. In addition, we consider it expedient to replace the ferrous sulfate in the ferritization process with spent sulfuric acid of steel etching, which is a waste of galvanic production.
Disclosure statement
No potential conflict of interest was reported by the author(s).
Additional information
Funding
Notes on contributors
Dmitry Samchenko
Dmitry Samchenko got his M.Sc. in Kiev National University of Construction and Architecture. In 2017, he received Candidate of engineering degree (PhD) in water supply and sewage specialty. His research interests are nanoparticles and nanocomposites, environmental chemistry, wastewater treatment, environmental engineering, technologies of building materials.
Gennadii Kochetov
Gennadii Kochetov got his M.Sc. in T. Schevchenko Kiev State University. In 2007, he received his D.Sci. in Engineering in water treatment. Since 2012, he is the head of interdepartmental laboratory for water treatment technologies and water quality control. His research interests are water supply, wastewater treatment, waste utilization, environmental engineering.
Dmytro O. Derecha
Dmytro O. Derecha got his M.Sc. in National Technical University of Ukraine Kyiv Polytechnic Institute in the area of material science and engineering. In 2010, he received his Candidate of physico-mathematical sciences degree (PhD) in magnetism. Since 2012 he is the head of nanocrystalline structures laboratory. His research interests are magneto-electrochemistry, material science, surface engineering, nondestructive testing and casting.
Yurii B. Skirta
Yurii B. Skirta got his M.Sc. in T. Schevchenko Kiev State University in the area of medical radiophysics. In 2018, he received his PhD degree in magnetism. His research interests are materials with shape memory and magneto-electrochemistry. Since 2021, he is involved in educational process in National Technical University of Ukraine “Igor Sikorsky Kyiv Polytechnic Institute”.
References
- Birčáková, Z., Füzer, J., Kollár, P., Bureš, R., & Fáberová, M. (2019). Magnetic properties of Fe-based soft magnetic composite with insulation coating by resin bonded Ni-Zn ferrite nanofibres. Journal of Magnetism and Magnetic Materials, 485, 1‒7. https://doi.org/10.1016/j.jmmm.2019.04.060
- Brožová, S., Drápala, J., Miczková, J., & Havránek, J. (2020). Possibilities of obtaining zinc and iron after leaching of galvanic sludges. METAL 2020 - 29th International Conference on Metallurgy and Materials, Conference Proceedings 892–12., https://doi.org/10.37904/metal.2020.3629
- Derecha, D. O., YuB, S., & Gerasimchuk, I. V. (2014). Electrolyte vortex dynamics in the vicinity of a ferromagnetic surface in a direct current magnetic field. The Journal of Physical Chemistry B, 118(50), 14648–14651. https://doi.org/10.1021/jp510275x
- Derecha, D. O., YuB, S., & Gerasimchuk, I. V. (2015). Technique for determining fluids motion characteristics in the vicinity of ferromagnetic solids under magneto-chemical treatment. Nanoscale Research Letters, 10(1), 440–444. https://doi.org/10.1186/s11671-015-1150-6
- Derecha, D. O., YuB, S., Gerasimchuk, I. V., & Hruzevych, A. V. (2020). Statistical and Fourier analysis of the vortex dynamics of fluids in an external magnetic field. Journal of Electroanalytical Chemistry, 873, 114399. https://doi.org/10.1016/j.jelechem.2020.114399
- Fokina, S. B., Petrov, G. V., Sizyakova, E. V., YuV, A., & Kozlovskaya, A. E. (2019). Process solutions of zinc-containing waste disposal in steel industry. International Journal of Civil Engineering and Technology, 10(1), 2083–2089. https://doi.org/10.1007/s13204-018-0767-z
- Frolova, L. A. (2019). The mechanism of nickel ferrite formation by glow discharge effect. Applied Nanoscience (Switzerland), 9(5), 845 ‒ 852. https://doi.org/10.1007/s13204-018-0767-z
- Frolova, L. A., Pivovarov, A. A., Anisimova, L. B., Yakubovskaya, Z. N., & Yakubovskii, A. I. (2017). The extraction of chromium (III) from concentrated solutions by ferrite method. Voprosy Khimii I Khimicheskoi Tekhnologii, 6, 110–115. http://oaji.net/articles/2017/1954-1513764539.pdf
- Ge, J., Ruixi Chen, R., Ren, X., Liu, J., Jun, S., Ong, H., & Xu Z, J. (2021). Ferromagnetic–antiferromagnetic coupling core-shell nanoparticles with spin conservation for water oxidation. Advanced Materials, 33(42), 2101091. https://doi.org/10.1002/adma.202101091
- Gorobets, O.Yu, Gorobets , Yu.I., Bondar, I. A., & Legenkiy Yu, A. (2013). Quasi-stationary heterogeneous states of electrolyte at electrodeposition and etching process in a gradient magnetic field of a magnetized ferromagnetic ball. Journal of Magnetism and Magnetic Materials, 330, 76–80. https://doi.org/10.1016/j.jmmm.2012.10.015
- Gorobets, O.Yo., Gorobets, V.yu, Derecha, D. O., & Brukva, O. M. (2008). Nickel electrodeposition under influence of constant homogeneous and high-gradient magnetic field. The Journal of Physical Chemistry C, 112(9), 3373–3375. https://doi.org/10.1021/jp0762572
- Gorobets, Y., Gorobets, О., Derecha, D. O., Skirta, Y., Gerasimchuk, I. V., Konovalova, V. V., & Kyba, A. A. (2019). Electrolyte–electrolyte phase separation under the influence of a DC magnetic field. Applied Nanoscience, 9(5), 859–863. https://doi.org/10.1007/s13204-018-0827-4
- Igarashi, T., Herrera, P. S., Uchiyama, H., Hashimoto, K., & Tabelin, C. B. (2020). The two-step neutralization ferrite-formation process for sustainable acid mine drainage treatment: Removal of copper, zinc and arsenic, and the influence of coexisting ions on ferritization. Science of the Total Environment, 715, 136877. https://doi.org/10.1016/j.scitotenv.2020.136877
- John, M., Heuss-Assbichler, S., Tandon, K., & Ullrich, A. (2019). Recovery of Ag and Au from synthetic and industrial wastewater by 2-step ferritization and Lt-delafossite process via precipitation. Journal of Water Process Engineering, 30, 100532. https://doi.org/10.1016/j.jwpe.2017.12.001
- Justin, J. M. (2018). On generalized variance functions for sample means and medians Joint Statistical Meeting 2018, July 28 - August 2 584–594 Vancouver, Canada. . https://www.bls.gov/osmr/research-papers/2018/pdf/st180080.pdf
- Khabarov, Y., Veshnyakov, V., Kuzyakov, N., & Pankina, G. (2017). The interaction of iron (II) cations with chromate anions in the presence of lignosulfonates. International Multidisciplinary Scientific Geo Conference Surveying Geology and Mining Ecology Management SGEM, 17(43), 245‒252. https://doi.org/10.5593/sgem2017h/43/s18.031
- Kochetov, G., Prihna, T., Kovalchuk, O., & Samchenko, D. (2018). Research of the treatment of depleted nickel-plating electrolytes by the ferritization method. Eastern-European Journal of Enterprise Technologies, 3(6–93), 52–60. https://doi.org/10.15587/1729-4061.2018.133797
- Kochetov, G., Prihna, T., Samchenko, D., & Kovalchuk, O. (2019). Development of ferritization processing of galvanic wastes with energy saving electromagnetic pulse activation of the process. Eastern-European Journal of Enterprise Technologies, 6(102), 6‒14. https://doi.org/10.15587/1729-4061.2019.184179
- Kochetov, G., Prikhna, T., Samchenko, D., Prysiazhna, O., Monastyrov, M., Moshchil, V., & Mamalis, A. (2021). Resource-efficient ferritization treatment for concentrated wastewater from electroplating production with aftertreatment by nanosorbents. Nanotechnology Perceptions, 17(1), 9‒18. https://doi.org/10.4024/n22ko20a.ntp.17.01
- Kovalchuk, O., Kochetov, G., & Samchenko, D. (2019a). Study of service properties of alkali-activated cement using wastewater treatment residues. IOP Conference Series: Materials Science and Engineering, 708(1), 012087. https://doi.org/10.1088/1757-899X/708/1/012087
- Kovalchuk, O., Kochetov, G., Samchenko, D., & Kolodko, A. (2019b). Development of a technology for utilizing the electroplating wastes by applying a ferritization technique to the alkaline-activated materials. Eastern-European Journal of Enterprise Technologies, 10(98), 27 ‒ 34. https://doi.org/10.15587/1729-4061.2019.160959
- Makovskaya, O. Y., & Kostromin, K. S. (2019). Leaching of non-ferrous metals from galvanic sludges. Materials Science Forum 946 MSF, 591 ‒ 595. https://doi.org/10.4028/www.scientific.net/msf.946.591
- Marcus, M.-I., Vlad, M., Deak, G., Moncea, A., Panait, A.-M., & Movileanu, G. (2020). Thermal stability of inorganic pigments synthesized from galvanic sludge. Revista de Chimie, 71(8), 13 ‒ 20. https://doi.org/10.37358/rc.20.8.8274
- Vilarinho, C., Teixeira, J., Araújo, J., & Carvalho, J. (2017). Effect of time and acid concentration on metal extraction from galvanic sludges. ASME International Mechanical Engineering Congress and Exposition Proceedings (IMECE) IMECE2017-71370, V014T11A018. https://doi.org/10.1115/imece2017-71370
- Yemchura, B., Kochetov, G., Samchenko, D., & Т, P. (2021). Ferritization-based treatment of zinc-containing wastewater flows: Influence of aeration rates. Environmental Science and Engineering (ENVSCIENCE), 171 ‒ 176. https://doi.org/10.1007/978-3-030-51210-1_29
- Ying, Y., Xiong, X., Wang, N., Zheng, J., Yu, J., Li, W., Qiao, L., Cai, W., Li, J., Huang, H., & Che, S. (2021). Low temperature sintered MnZn ferrites for power applications at the frequency of 1 MHz. Journal of the European Ceramic Society, 41(12), 5924 ‒ 5930. https://doi.org/10.1016/j.jeurceramsoc.2021.05.013
- Zhang, Y., He, H., Wang, H., Chen, G., An, X., & Wang, Y. (2021). Evolution of microstructure and mechanical properties of Cr ferrite/martensite steels with different Si content after long-term aging at 550 °C. Journal of Alloys and Compounds, 873, 159817. https://doi.org/10.1016/j.jallcom.2021.159817
- Zhou, X., Wang, J., Zhou, L., Wang, Y., & Yao, D. (2021). Structure, magnetic and microwave absorption properties of NiZnMn ferrite ceramics. Journal of Magnetism and Magnetic Materials, 534, 168043. https://doi.org/10.1016/j.jmmm.2021.168043
- Zueva, S., Ferella, F., Ippolito, N. M., Ruduka, E., & De Michelis, I. (2021). Wastewater treatment from galvanization industry with zinc recovery. E3S Web of Conferences, 247, 01064. https://doi.org/10.1051/e3sconf/202124701064