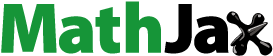
Abstract
In the current study, AISI 4140 steel is subjected to quenching treatment using different oils and quenchants with varying conditions. In this study, emulsions of Coconut, Karanja and Pinnay oil and Brine in different ratios are prepared with and without egg yolk as the emulsifier. The mechanical properties of steel specimens quenched in these emulsions are tested experimentally, analysed statistically and results are validated. Regressions equations are fit to determine the hardness and impact energy of the samples quenched at different conditions. Response Surface Methodology optimization tool is used to obtain the optimized values for viscosity and cooling rate of the solution to obtain the superior combination of hardness and impact energy. Improvement is the hardness is observed for the samples quenched with the emulsions of coconut oil and brine with lower vol% of oil due to their lower viscosity and higher cooling rate.
PUBLIC INTEREST STATEMENT
Steel is commonly used material in various application. Heat treatment and quenching is one of the methods used to improve the mechanical properties of steel. In this study, AISI 4140 steel is subjected to quenching treatment using different oils and quenchants with varying conditions. Emulsions of Coconut, Karanja and Pinnay oil and Brine in different ratios are prepared with and without egg yolk as the emulsifier. The mechanical properties of steel specimens quenched in these emulsions are tested experimentally, analysed statistically and results are validated.
1. Introduction
Steel is one of the most useful metals to fabricate simple structural parts to complicated missile parts. Generally, the steel is alloyed and heat treated for better properties desired for application (Laxmi et al., Citation2022). Such refinement in properties leads to better strength-weight ratio and consequently, better design of parts and machinery as seen in the automobile and aviation industry (Avner, Citation1974). Some common heat treatment processes used to improve the mechanical properties are simple treatments like, annealing, normalizing, quenching, and tempering as well as complicated austempering, maraging and ausaging treatments (Johnson et al., Citation2019).
Quenching is the typical treatment comprising of austenitizing, cooling faster than critical cooling rate to result a harder phase with permissible residual thermal strain for the satisfactory useful time range. In quenching, primarily liquid soaking of the steel is followed in water, brine or higher viscosity oils individually or blended condition. The process has three major stages: the vapour blanket stage, the nucleate boiling stage, and the convection stage during heat dissipation from the metal system (specimen) into surrounding liquid medium. During the vapour blanket stage, the quenchant forms a film of vapour around the specimen and is created because the heat supplied by the part is more than what the quenchant can carry away. The cooling rate in this stage is relatively low, and the heat transfer mechanism is mainly conduction. In the nucleate boiling stage, the vapour film collapses, and the liquid quenchant meets the metal’s hot surface, leading to violent boiling. Heat transfer rates are generally the highest in this stage. The duration and heat transfer of this stage depends on various properties of the quenchant and have a critical effect on the properties of the quenched part. The convective phase begins when the temperature of the specimen reaches the boiling point of the quenchant. Boiling stops and the surface of the specimen is fully wetted by the quenchant. The cooling rate in this phase is lower and is affected by the viscosity of the quenchant (Avner, Citation1974; Chen et al., Citation2017; Totten et al., Citation1993). Viscosity of the quenchant plays an important role in obtaining the desired structure by controlling the rate of heat dissipation in the three stages mentioned.
The rapid cooling during the quenching process favours the growth of martensite microstructures. The extent to which these microstructures grow is directly affected by the cooling rate of the quenchant (Babasafari et al., Citation2020). These microstructural changes are responsible for the change in hardness of the quenched specimen (Avner, Citation1974).
Although quenching is necessary to improve hardness of the steel, it also results in high thermal stresses and transformation stresses. The density and intensity of the stresses developed during quenching depend on the viscosity and thermal properties of the quenchant. These stresses could result in high residual stresses and distortions, increasing the probability of cracking (Canale & Totten, Citation2005). It has been found that a higher heat transfer rate in the high temperature region and martensitic temperature region increased the residual stresses developed in the specimen (Civera et al., Citation2015). Due to its high cooling rate, water is not a preferred quenchant for parts with complex geometries or tight tolerances. Instead, vegetable and mineral oils are popularly used to give a slower and more even cooling, resulting in lesser internal stresses (Johnson et al., Citation2019).
The interest in vegetable oils as quenchants has grown recently due to environmental concerns of the sustainability and disposal of mineral oil quenchants. Mineral oils are toxic, non-biodegradable, and non-renewable. As such, many eco-friendly alternatives have been developed like vegetable oils, polymer quenchants and nanofluids. Some vegetable oils have comparable or better cooling performance than mineral oils. However, difficulties encountered in these oils are their high cost of production, high degradation rates due to oxidation, and precipitation of sludge on the quenched surfaces. These challenges need to be overcome before vegetable oils become viable for use in the industry (Brito et al., Citation2019; Prathviraj et al., Citation2020).
Due to their high viscosity, both mineral oils and natural oils have a lower cooling rate when compared to water. Many aqueous polymer solutions have been studied which have the properties of both oil and water quenchants. However, they suffer from high aging and cost issues (Chen et al., Citation2017; Ikkene et al., Citation2014). Moreover, polymer quenchants with nanofluids and mineral oils are nonbiodegradable in nature (Chen et al., Citation2017). Combining the properties of oil and water may give better results. Since oil and water are immiscible, an interface (emulsifier) will be needed to prepare the emulsion by reducing interfacial tension and hindering droplet enlargement (Bart et al., Citation2013).
An eco-friendly quenchant needs to be biodegradable. Thus, the emulsifier used should also be biodegradable and, preferably, natural. Egg yolk fits this requirement due to its low density lipoproteins and lecithin which give its emulsifying properties. In neutral solutions (pH = 7), egg yolk works best with higher ionic concentrations (>0.3 M NaCl; Anton & Gandemer, Citation1997). Moreover, the presence of NaCl is beneficial for the cooling rate. The (5–10 wt%) NaCl solution in water is known as brine solution which has the capacity to increase the cooling rate in vapour blanket stage of cooling process. The NaCl ions present in the solution breaks up the air packets (blanket) present on the surface of the specimen submerged in the quenchant to facilitate new liquid particles which inhibits the formation of the vapour blanket and thus results in a homogeneous cooling of the specimen (Pizetta Zordão et al., Citation2019). To get added advantages on improving the existing properties during quenching, small amount of NaCl is added.
Based on the literature review, in the present study, emulsions of Coconut, Karanja, Pinnay oil (readily available vegetable oils) and Brine in different ratios are prepared with and without egg yolk as the emulsifier. The mechanical properties of the AISI 4140 steel specimens quenched in these emulsions are tested experimentally, analysed statistically and results are validated.
2. Materials and methods
2.1. Material composition
Three cylindrical AISI 4140 steel rods of diameter 16 mm and length 1 meter were bought, and their chemical composition was tested for confirmation. Table provides the chemical composition.
Table 1. Chemical composition
2.2. Quenchants
Emulsions of water and coconut oil were made in 3 different ratios: 1-part oil to 3-parts water (E1), 1-part oil to 1 part water (E2), and 3 parts oil to 1 part water (E3). In all the quenchants except pure coconut oil, NaCl was added to a concentration of 0.45 M. In each case, emulsifier is added at 5 volume%. Pinnay and Karanja oils are used as quenchants with and without emulsifier (egg yolk). The constituents were mixed in a blender to prepare the emulsion. The viscosity of all these quenchants were measured using a Rheometer between shear rates ranging from 1s−1 to 35s−1.
2.3. Emulsification
Emulsification is carried out using the sonicator. Sonication is a process in which ultrasonic waves are used to agitate the solution sample. The samples after diamond polishing are treated in sonicator with acetone to remove any micron sized particles adhering to the surface of the specimen. Once the specimens are dipped into the solution, sonicator probe is actuated. The following parameters are set for sonication.
Time duration: 3 minutes, amplitude: 30%, pulse: continuous.
2.4. Specimen preparation
Standard specimens of AISI 4140 steel were machined from the cylindrical rods using the band saw, lathe, vertical machining center, shaper, and wire EDM for the impact test, hardness test and microstructure evaluation.
2.4.1. Specimens for Izod impact test
The specimens for the Izod Impact test were prepared in accordance with the ASTM E23 standard. Bars of dimensions 75 × 10 x 10 mm were machined from the 16 mm diameter cylindrical rod using the lathe and vertical machining center. The V-notch of depth 2 mm, 45° angle, tip radius of 0.25 mm, and at 28 mm from the top face was made using a shaper.
2.4.2. Specimens for Rockwell hardness test
Hardness test specimens of length 20 mm and diameter 16 mm were cut from the cylindrical rod using a band saw. After the requisite heat treatment, the carbon layer on the specimen’s cross-section was removed using emery paper of grits 120, 240, and 400 micron size.
2.4.3. Specimens for microstructure study
The specimens for the microstructure study were machined using CNC lathe to a diameter of 10 mm and cut using the wire EDM. Emery papers of grits 120, 240, 400, 600, 800, 1000, 1200, 1500, 2000, and 2500 were used to prepare the specimens for the Scanning Electron Microscope (SEM) analysis. Then they were polished using a velvet cloth and alumina powder to obtain a mirror finish. The surface was etched by dipping it in Nital solution (concentrated nitric acid and methanol solution with 90 % volume water) for 15 seconds, dried after rinsing with ethyl alcohol. These samples are observed using Inverted metallurgical microscope (Model: IM 7000). SEM (Model: JEOL JSM 840A) with Energy Dispersive X-ray (EDX).
2.5. Heat treatment procedure
All specimens, excluding specimens for the as-Bought (AB) condition, were subject to normalizing. They were heated in the Muffle furnace to 900°C for 2 hours, then taken out of the furnace and left to cool down in the air to room temperature. The normalized (N) specimens set were kept aside. The remaining specimens were again heated to 900°C in the muffle furnace for 2 hours and then quenched in 3 litres of their respective quenchants. They were then taken out, cleaned and dried before testing.
2.6. Testing
The specimens were subjected to their respective test. Hardness tests were conducted on the Rockwell hardness tester fitted with a diamond cone indenter and a load of 150 kgf in accordance with the ASTM E18 standard. The hardness readings were taken on three different points on the cross section of the specimen to ensure accurate results. The impact tests were conducted on the Izod impact testing machine. For each quenching condition, three impact test specimens were prepared. Their readings were noted, and the average taken. The microstructure analysis was carried out by using SEM to know the presence of different phases.
2.7. Statistical analysis
The obtained results are subjected to statistical analysis using Minitab software. The Response Surface Optimization is used to obtain the superior combination of hardness and impact energy. Regression equations are fit to predict the hardness and impact energy for the samples quenched in various oils with different viscosity.
3. Results and discussion
3.1. Microstructure analysis
AB specimens (Figure ) shows coarse pearlite lamellae with larger proeutectoid colonies of ferrite. This indicates that the AB specimen is of hot worked or cooled slowly after pouring to the mould. Coarse proeutectoid colonies of ferrite indicate that the melt is cooled slowly after pouring into the melt or specimen was subjected to hot rolling and cooled in controlled rate to generate coarser lamellae of pearlite. The normalized specimen (Figure ) shows finer pearlite lamellae and finer colonies of pearlite. Normalizing is the grain refinement heat treatment in which individual phase grains are reducing in size due to increase in the rate of nucleation by faster cooling rate. During normalizing the parent phase converts into finer pearlite with finer inter lamellar spacing in the fine pearlite colony, that is, network of alternate layers of ferrite and cementite (Figure ). The coconut oil quench specimen (Figure ) shows a typical martensite structure. This is the coarse martensite without any proeutectoid ferritic phase. This implies that the cooling rate of coconut oil quench is faster than critical cooling rate. At this cooling rate, the decomposition of the austenite into pearlite or separation of proeutectoid ferrite is not taking place. It implies that the martensite transformation is by shear process-controlled nucleation and does not carry any incubation period. Figures also show the SEM images of coconut oil and oil plus salt solution quench specimens. As the oil volume% decreases in the quenchant, the cooling rate increases, resulting finer martensite platelets. Figures are the SEM images of Karanja and Pinnay oil quenched specimens. We have also tried the microstructures of Karanja and Pinnay oil blends with brine and egg yolk emulsions as quenchant. Similar structures to coconut oil blend quench are obtained
Figure 1. Samples treated with various conditions (a) As bought (b) Normalized (c) Quenched in pure oil (d) 75 % Oil (e) 50 % Oil (f) 25 % Oil (g) Quenched in salt water (h) Quenched in pure karanja Oil (i) Quenced in pure Pinnay oil.
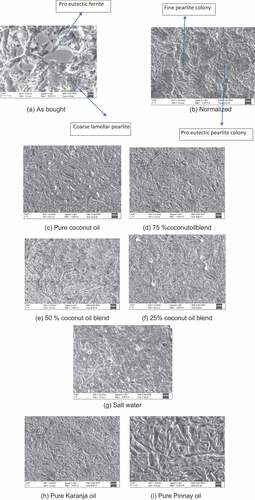
with these oil blends too. Coconut oil viscosity is in between that of Karanja and Pinnay oils. These oil quenched samples also display martensitic structure. The martensitic structure obtained in the oil shows coarse martensite plates if viscosity is less whereas finer martensite plates when viscosity of the oil increases. Accordingly, high viscosity Pinnay oil quenched specimen shows coarse plates of martensite (Figure ). In the cases of quenching, no indication of pearlite or proeutectoid phase formation is observed.
3.2. Statistical analysis
3.2.1. Calculating optimum parameters
Viscosity and cooling rate data is available for the pure liquids (Individually for water and respective oils; Avner, Citation1974) the statistical analysis is carried out with experimental readings of hardness and impact strength of individual quenchants with and without emulsifier. Since the quantity of salt (NaCl) and emulsifier (Egg yolk) is small, the direct effect on the properties can be neglected during statistical analysis. The quench results obtained for the hardness and impact tests of specimens in the media with and without emulsifier are shown in the Tables , respectively. The results are subjected to statistical analysis using Minitab software.
Table 2. Hardness and impact test results with emulsifier
Table 3. Hardness and impact test results without emulsifier (Avner, Citation1974)
To obtain the optimum combination of hardness and impact energy, Response Surface Optimization is carried out.
Figure shows the combined optimization results obtained from the RSM optimization using Minitab Software. The following are the optimized parameters for the samples quenched using the quenchants with emulsifier.
Figure 2. Combined optimization for hardness and impact energy for samples quenched using quenchants with emulsification.
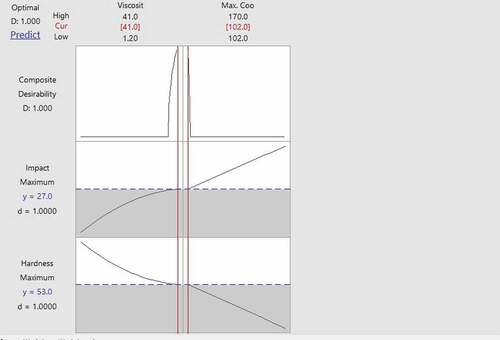
Viscosity: 41 cSt
Cooling rate: 102 oC/h
Figure shows the optimum parameters for obtaining maximum hardness and impact energy combination is determined using RSM optimization.
Figure 3. Combined optimization for hardness and impact energy for samples quenched using quenchants without emulsification.
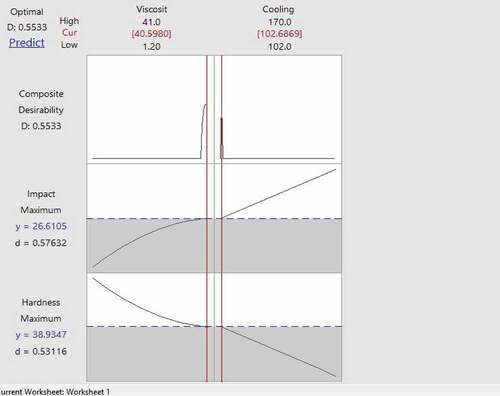
The following are the optimized parameters for the samples quenched using the quenchants without emulsifier.
Viscosity: 40.5 cSt
Cooling rate: 102.68 °C/h
Validation experiment:
Validation experiment is performed by preparing the coconut oil with brine solution having viscosity 40.5 cSt with cooling rate 102.68 oC/h. The Hardness and impact energy obtained are 49 HRC and 26 J, respectively. This shows the superior combination of hardness and impact energy values at the optimized condition of viscosity and cooling rate.
Regression equation is fit to predict the hardness and impact energy of the samples, which involves the viscosity and cooling rate within the range of values considered for the study.
EquationEquations 1(1)
(1) and Equation2
(2)
(2) are the regression equations generated for the “with emulsifier” condition, whereas Equationequations 3
(3)
(3) and Equation4
(4)
(4) are the regressions equations for the “without emulsifier” condition.
EquationEquations 1(1)
(1) to 4 give the regression equations for impact energy and hardness for different cases as mentioned. The high R squared values indicate that the above equations may be used to predict the hardness and impact energy of the samples which involves the parameters within the range of study.
3.2.2. Experimental results of hardness and impact test
From the Table , the emulsions show improved impact toughness of the materials with required reduction in hardness properties. Table shows the viscosity of different quenchants used in the study with respective cooling rates. The improvement in impact resistance is due to the slight reduction in cooling rate of the emulsification quenchant.
Table 4. Hardness and impact results obtained by coconut oil and salt water combination with or without emulsifier
Table 5. Viscosity and cooling rate for the various conditions
The data obtained for hardness and impact energy for various samples quenched in different emulsions are analysed using a statistical tool. Regression equations are then generated.
EquationEquations 5(5)
(5) and Equation6
(6)
(6) may be used to predict the hardness and impact energy of the samples quenched with different proportion of coconut oil and salt water (brine) solution with emulsion. The high R squared value is an indication of the good fit obtained for the equation.
Optimization is also carried out using the RSM for obtaining the superior combination of hardness and impact energy. The following values are the optimized parameters obtained.
Viscosity: 4.2 cSt
Cooling rate: 95 °C/h
4. Conclusion
The coconut oil emulsions proved to be effective in hardening AISI 4140 steel. The 25 vol% coconut oil emulsion resulted in the highest hardness, but the lowest impact strength among the emulsions. The viscosity of the quenchants is shown to greatly influence the strength of the quenched specimens. Through the statistical analysis, a pure oil with viscosity of 40.5 cSt and cooling rate 102.68°C/h is found to be an optimal quenchant.
The emulsions of coconut oil and brine with lower vol% of oil resulted in higher hardness due to their lower viscosity and higher cooling rate. The regression equations formed predict the likely values for the hardness and impact strength for a given emulsion, if the viscosity and maximum cooling rate is known.
Disclosure statement
The authors declare that they have no known competing financial interests or personal relationships that could have appeared to influence the work reported in this paper.
Additional information
Funding
Notes on contributors
Sathyashankara Sharma
Sathyashankara Sharma is working as Professor and Head in the Department of Mechanical & Manufacturing Engineering, MIT, MAHE, Manipal. He holds B.E. (Industrial and Production Engineering), M.Tech. (Materials Engineering) and Ph.D. (Materials Engineering) degrees. He has 33 years of teaching experience. His area of interest includes Engineering materials, Heat treatment of metals and composites, Machinability and Deformation behaviour of metals and composites. He has published more than 200 papers in journals and conferences.
References
- Anton, M., & Gandemer, G. (1997, May). Composition, solubility and emulsifying properties of granules and plasma of egg yolk. Journal of Food Science, 62(3), 484–11. https://doi.org/10.1111/j.1365-2621.1997.tb04411.x
- Avner, S. H. (1974). Introduction to physical metallurgy (Vol. 2). McGraw Hill Education.
- Babasafari, Z., Pan, A. V., Pahlevani, F., Hossain, R., Sahajwalla, V., du Toit, M., & Dippenaar, R. (2020, November). Effects of austenizing temperature, cooling rate and isothermal temperature on overall phase transformation characteristics in high carbon steel. Journal of Materials Research and Technology, 9(6), 15286–15297. https://doi.org/10.1016/j.jmrt.2020.10.071
- Bart, J. C. J., Gucciardi, E., & Cavallaro, S. (2013). Formulating lubricating oils. In Biolubricants (pp. 351–395). Elsevier.https://doi.org/10.1533/9780857096326.351
- Brito, P., Ramos, P. A., Resende, L. P., de Faria, D. A., & Ribas, O. K. (2019). Experimental investigation of cooling behavior and residual stresses for quenching with vegetable oils at different bath temperatures. Journal of Cleaner Production, 216, 230–238. https://doi.org/10.1016/j.jclepro.2019.01.194
- Chen, X., Zhang, L., Jie, X., Li, Y., & Huang, X. (2017, June). Quenching characteristics of glycerol solution as a potential new quenchant. International Journal of Heat and Mass Transfer, 109, 209–214. https://doi.org/10.1016/j.ijheatmasstransfer.2017.02.013
- Civera, C., Rivolta, B., Simencio-Otero, R. L., Lúcio, J. G., Totten, G. E., & Canale, L. C. F. (2015, January). Vegetable oils as quenchants for steels: residual stresses and dimensional changes. Materials Performance and Characterization, 3 (4), 306–325. https://doi.org/10.1520/MPC20140039
- de C. F. Canale, L., & Totten, G. E. (2005). Overview of distortion and residual stress due to quench processing. Part I: Factors affecting quench distortion. International Journal of Materials and Product Technology, 24(1/2/3/4), 4. https://doi.org/10.1504/IJMPT.2005.007941
- Ikkene, R., Koudil, Z., & Mouzali, M. (2014, November). Cooling characteristic of polymeric quenchant: calculation of HTC and prediction of microstructure and hardness. Journal of Materials Engineering and Performance, 23(11), 3819–3830. https://doi.org/10.1007/s11665-014-1185-3
- Johnson, O. T., Ogunmuyiwa, E. N., Ude, A. U., Gwangwava, N., & Addo-Tenkorang, R. (2019, January). Mechanical properties of heat-treated medium carbon steel in renewable and biodegradable oil. Procedia Manufacturing, 35, 229–235. https://doi.org/10.1016/j.promfg.2019.05.032
- Laxmi, B., Sharma, S., Pk, J., & Hegde, A. (2022, January). Quenchant oil viscosity and tempering temperature effect on mechanical properties of 42CrMo4 steel. Journal of Materials Research and Technology, 16, 581–587. https://doi.org/10.1016/j.jmrt.2021.11.152
- Pizetta Zordão, L. H., Oliveira, V. A., Totten, G. E., & Canale, L. C. F. (2019, September). Quenching power of aqueous salt solution. International Journal of Heat and Mass Transfer, 140, 807–818. https://doi.org/10.1016/j.ijheatmasstransfer.2019.06.036
- Prathviraj, M. P., Samuel, A., & Narayan Prabhu, K. (2020, October). Reprocessed waste sunflower cooking oil as quenchant for heat treatment. Journal of Cleaner Production, 269, 122276. https://doi.org/10.1016/j.jclepro.2020.122276
- Totten, G. E., Bates, C. E., & Clinton, N. A. (1993). Handbook of quenchants and quenching technology. ASM international.