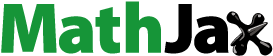
Abstract
Precision machine tool structures require enhanced stability with higher static stiffness and increased damping. Granite epoxy (G-E) composite offers improved damping properties and is a promising alternative material. This study evaluates the mechanical strength and damping of G-E hybrid polymer composites with varying percentages of cast iron (CI) filler. Experimental and finite element (FE) analyses were conducted on hybrid composite samples incorporating 5, 10 and 15 wt% CI filler particles. Results show that a 70:30 ratio of G-E with 10% CI filler enhances compressive strength. Tensile and flexural behaviors are influenced by epoxy content, with minimal effects from CI filler. Both experimental and numerical simulations show significant improvement in stiffness and damping properties with higher quantities of granite particulates (80 wt%) and 5 wt% CI filler. Modal analysis confirms higher natural frequencies in all modes. This hybrid composite configuration presents a viable alternative for machine tool structures, offering increased structural damping.
1. Introduction
Currently, polymer matrix composites (PMC) with granite reinforcement material of varying granular sizes and epoxy matrix are being considered as a potential alternative for foundations of precision machining structures typically made of CI and other metal alloys. The support components such as base and columns with high structural stiffness and good damping play a pivotal role in producing parts with high precision. The vibrational properties of the base support directly impact the performance of the machining precision of the tool (Suh & Lee, Citation2008; Munoa et al., Citation2016). Static and dynamic characteristics of these structures rely on the mechanical properties of the materials utilized for building such machine structure bases. Materials for machine tools need to exhibit higher modulus of elasticity, yield strength, improved toughness and superior damping properties. Benefits of PMC with granular granite particulates include significantly improved damping properties (8 times that of CI), enhanced thermal stability and geometric flexibility during fabrication facilitated by the polymeric matrix (Heisel & Gringel, Citation1996; Möhring et al., Citation2015).
Conventional usage of gray CI as a typical material for machine tools falls short in effectively suppressing dynamic vibrations, leading to lower product quality. Chuang and Chen (Chuang & Chen, Citation2022) suggested the adoption of an alternate composite material with granite particles to replace conventional CI in the base structures of precision machines. Granite epoxy (G-E) composite reinforced with carbon fibers and additional filler particles aimed to improve the structural performance of machine tools. G-E composite consisting of only 1/3rd density of gray CI was able to withstand higher compressive stresses. A drastic improvement in the stability and precision of the machine tool was noted with around 69% and 73% reduction in stress and strain applied on the machine structures. Haddad and Al Kobaisi (Citation2013) considered a blend of cement concrete with granite content for construction of lathe base. A notable improvement in anti-vibrational properties and machining precision of CNC machine tools was observed. However, certain drawbacks were also noted with cement concrete due to its tendency to develop voids, holes and surface cracks. Pawar et al. (Citation2017) focused on developing polymeric composites made of jute epoxy filled with granite powder for wind turbine blade applications. Detailed analysis on mechanical, fracture and thermo-mechanical characteristics of the jute epoxy composite with fiber loading from 10 to 50 wt% has been carried out. With the increase in fiber loading, a notable reduction in void content, improved tensile and flexural strength was observed. However, mechanical properties were found to have minimal improvement on the increase in filler content. Mechanical property assessment on hybrid composites made from jute and rock wool in phenol formaldehyde matrix indicated an improvement only after the addition of solid filler materials in the composite (Öztürk, Citation2010). Filler particles, such as cenosphere and silicon carbide were found to increase both the tensile and impact strength of composite material (Ravichandran & Sasikumar, Citation2016; Çallıoğlu et al., Citation2011). For epoxy-filled green composite materials, silica rich granite particles were incorporated as fillers with jute fiber as reinforcement material. Along with mechanical and physical property assessment, both electrical resistance and thermal properties of the composite specimens were tested by Chaturvedi et al. (Citation2022). Such hybrid composites were also tested for its mechanical characteristics by incorporating kenaf fiber and glass fiber as reinforcement material (Raja et al., Citation2022; Ray et al., Citation2017).
Subhash et al. (Citation2018) developed a granite particulate reinforced epoxy composite considering its eco-friendly nature with filler material varied from 10 to 50 wt%. Hardness and moisture absorption tests indicated an enhancement in mechanical properties for epoxy resin around 60–70 wt%. Gomes et al. (Citation2021) developed an artificial granite stone with 85:15 G-E ratio using a series of vacuum, vibration and compression techniques. A significant increase in mechanical and physical properties, improved resistance to temperature variations were noted in comparison with natural granite material. Using the design of experiments approach, a series of tests, such as tensile, flexural and damping tests were conducted on G-E composite with 890 wt% of granite content of fine to coarse grain particulates. From Taguchi analysis of the means and signal to noise ratios, an optimal composition (80:20 G–E ratio) was identified with 50:50 proportion of small and coarse granite aggregates (Shanmugam et al., Citation2017; Piratelli-Filho & Shimabukuro, Citation2008). Similarly, Piratelli-Filho and Levy-Neto (Citation2010) conducted vibration analysis on prismatic bar specimens of G-E composite. Damping factor and logarithmic decrement values were recorded for varied G-E weight percentages. For damping characteristics, 80:20 G-E ratio was identified as the optimal composition with epoxy resin identified as a better matrix material than polyester resin. In analyzing the physico-chemical properties, a further improvement in void content, tensile and flexural behavior was also noted for G-E composite containing epoxy resin integrated with Hydroxyl-terminated polyurethane of varied proportions and silane coupling agent treated granite particulates (Shetty Ravindra & Rai, Citation2008; Bakar et al., Citation2009).
Although G-E structure exhibits superior damping capacity, its structural stiffness is 1/3rd to that found in CI. Considering such variations in structural rigidity, Venugopal et al. (Citation2019) and Venugopal et al. (Citation2020) focused on redesigning the vertical machine center (VMC) column by adding different configurations of steel reinforcements in G-E structure. Both numerical and experimental studies were conducted to optimize the designs of VMC columns with improved structural rigidity. Using modal analysis, finite element (FE) models of different G-E column designs were analyzed and compared with steady state and dynamic properties of CI column. An optimized model with 20% higher natural frequency than CI column was finalized as a suitable model to attain higher structural damping and stiffness properties (Shanmugam et al., Citation2022). A similar approach of redesigning was also performed on a VMC base using steel reinforcement in G-E structure. A design configuration with L-channels was identified as an optimum model that could limit deformation by 56% considering different machining operations. Free vibration analysis were performed on a modified form of toolholder made of G-E composite (Kashyzadeh & Ghorbani, Citation2020; Abdellah et al., Citation2022). Around 10% reduction in 1st and 2nd natural frequencies were noted by the usage of G-E in cutting tool head than compared with conventional tool material.
Using FEA approach, Chinnuraj et al. (Citation2020) and Chinnuraj et al. (Citation2021) analyzed the torsional rigidity and natural frequency variations generated in a lathe bed constructed using G-E composite reinforced with structural steel. For varied designs of steel reinforcements, around 10% reduction in structural stiffness and 22% decrease in mass of lathe bed in comparison to CI material. Optimum steel reinforcement design configurations to attain improved stiffness and damping ratio were also identified through topology optimization (Dhanabal et al., Citation2023). FEA analysis performed on machine tool structures made of granite composite without additional reinforcements indicated an improvement in dynamic characteristics. This proves that granite material is a suitable alternative for CI due to its superior damping capability (Chen et al., Citation2016; Zhou, Hutsch, et al., Citation2023; Zhou, Tian, et al., 2023; Zhou, Zhang, Zhang, Liu, et al., Citation2023; Zhou, Zhang, Zhang, Li, et al., Citation2023). For the epoxy granite composite developed for better stability characteristics, Arun Ramnath et al. (Citation2021) conducted milling operations by identifying optimal machining parameter combinations using decision-making model and analytical hierarchy procedure. Optimal machining conditions of speed, feed rate and fiber content percentage were identified from the experimental investigations. The restorative properties of the epoxy resin were tested on cracked granite samples of varied widths to evaluate its tensile repair strength using acoustic emission and digital image correlation techniques (Zhou, Hutsch, et al., Citation2023; Zhou, Tian, et al., 2023; Zhou, Zhang, Zhang, Liu, et al., Citation2023; Zhou, Zhang, Zhang, Li, et al., Citation2023).
Detailed studies have also been conducted on hybrid epoxy granite composite structures to analyze the thermal-based errors and design methods adopted for thermal compensation. Thermal errors developed in machine tool structures may arise from the influence of temperature distribution and displacements at the tool center point (Mula et al., Citation2023). Madhusudhan et al. (Citation2022) and Reddy et al. (Citation2022) developed a hybrid composite by utilizing granite powder blended with Cordia Dichotoma fiber content of 20 wt.%. Tensile, flexural and impact behavior of the composite specimens were tested for varied granite particulate percentages to analyze the effectiveness of filler particles on betterment of mechanical properties. Scanning electron microscopy (SEM) was employed to examine the bonding and distribution of granite powder in the fabricated composite material and chemical functional groups were detected using Infrared Spectroscopy. Effectiveness of alternate hybrid composite materials has been studied by utilizing silk sisal fibers and palm stalk fiber reinforced with granite particulate filler materials in epoxy resin (Sripriyan & Karthick, Citation2024; Ojha & Biswal, Citation2019). Bhanuprakash et al. (Citation2023) investigated the strength, wear and fatigue characteristics of aluminum matrix composites blended with synthetic granite and granite fine particulates as strengthening material. For an increase in granite reinforcement concentration, a notable enhancement in hardness was observed. Also, the reinforcement material was found to function as energy attenuators which help to disperse the applied forces and reduce the probability of failure conditions.
In this study, the vibrational behavior and mechanical properties of G-E hybrid composite with CI particulates were experimentally studied and the damping behavior was further validated using FE analysis. This study is conducted to evaluate the effectiveness of G-E hybrid composite as an alternate material to CI-based foundations in machine tool structures. Inclusion of CI filler particles has potential to further enhance the damping and mechanical behavior of the hybrid composite, which is not yet explored in any of the research studies. Mechanical properties, such as compressive, tensile and flexural strength were assessed for varied weight concentrations of epoxy resin reinforced with granite particles (0–85 wt%) and cast-iron filler (5–15 wt%). Dynamic analysis was carried out to evaluate the damping behavior of developed hybrid composites. A notable reduction in natural frequencies was observed for specimens with higher epoxy resin content. Inclusion of optimal quantity of granite content and cast-iron filler in composite mixture was found to improve the stiffness and damping properties of G-E composite than compared with conventional material used in machine tool structures.
2. Materials and methods
2.1. Mold fabrication
Different types of mechanical property assessment and damping analysis tests are outlined to be performed on G-E composites with and without the addition of CI particulates as filler material. Hence, molds required to fabricate the composite specimens are prepared according to the required dimensions of the proposed tests. As per the ASTM standards, the definitive dimensions of each test specimen vary for different tests. Nylon material was selected for mold fabrication since it does not bind with epoxy resin after the curing process. It also enables easy removal of composite specimens from the mold. A circular nylon rod procured was subjected to numerous machining processes such as shaping, drilling and slitting operations to fabricate the required dimensional mold cavities.
details the different types of molds prepared for composite specimen fabrication. The compression mold was manufactured as per ASTM D695 standards. Around 10 holes were drilled into the mold of required dimension to prepare ten specimens at a time and to increase the production rate. For easy removal of composite specimens, the mold was cut into two equal halves through slitting operation and the two halves are bolted together for specimen fabrication. For the fabrication of tensile and flexural mold, a flat nylon plate was machined to incorporate multiple test specimens. The specimens with exact geometry can be obtained by imparting required shrinkage allowances to the specimens. The mold material used accredits easy removal of specimens from the mold cavities. The damping specimen sizes are decided as 20 mm*20mm*200 mm, which is as per the requirement at the test center. Using machining process, the circular nylon rod is machined into a square shape and the required mold cavity is engraved in the mold by performing milling operation. The mold is split into two equal halves for smoother removal of specimens and is bolted for fabrication of composite specimens.
2.2. Material selection
Epoxy resin (LAPOX L-12) is used as the matrix material in the composite preparation. K-6 curing agent is the most suitable hardener for expediting the curing process of resin at room temperature (Bisen et al., Citation2020). The optimal hardening agent for expediting the curing process of resin at room temperature is the K-6 curing agent (Mula et al., Citation2023). Epoxy resin has higher viscosity compared to that of hardener, and the recommended blending ratio is 10 parts epoxy resin to 1 part hardener. Employing suitable fabrication techniques can significantly reduce the formation of bubbles in the composite mixture.
Black granite in particulate form is selected as the reinforcement material to fabricate the hybrid composite. The granite particles consist of different grain sizes and these granules are differentiated corresponding to the grain size requirements for experimental tests. From literature review, a particular range of grit size is preferred for its superior properties compared to other grain sizes. Hence, granular size ranging from 424 to 599 µm is selected (Omar et al., Citation2021). By considering the fact that with the use of one particular grain size, the extent of porosity level in the specimens may be high. To reduce the issue, smaller grain size particles were also chosen in a range of 53–149 µm. As a result, the combination of fine and coarse granules allows for enhanced compaction, effectively minimizing porosity levels. These two granule size ranges were mixed in equal proportion of 50:50. The granite powder mesh sizes, such as 53–74 µm, 75–105 µm, 106–149 µm and 424–599 µm used for composite fabrication are shown in . Sieve shaker machine is used for the differentiation of granite particulates in numerous mesh sizes.
Cast iron (CI) in powdered form is used as the filler material. From analyzing the literatures, CI particles with grain size ranging from 0 to 90 µm were used. CI particulates as filler were incorporated in the composite mixture in terms of 5%, 10% and 15% of the total volume of granite particulates. The CI particles blend easily with granite content and improve the overall compaction of G-E composite.
2.3. Material preparation and fabrication
Initially, different G-E mixing ratios are decided from the analysis of literature study carried out. The weight fraction of granite particles was estimated based on the total volume of the composite specimen to be fabricated. Further, it is weighed and blended in equal proportion of varied grit sizes for better compaction and reduced porosity effects. Detailed fabrication procedure adopted in this study is illustrated in . In the G-E polymer matrix composite, varied weight percentages of CI particulates was] blended with granite particles. Measured quantity of epoxy resin is blended with hardener in a 10:1 proportion. The stirring process persisted until the mixture achieved a pale-yellow color. Subsequently, the granite particulate mixture was incorporated into the resin and stirred thoroughly for approximately 10 min to ensure the uniform blending of the composite mixture. The resulting mixture was then poured into the respective molds before reaching the gel time of the epoxy resin.
and list the material composition of G-E specimens fabricated with and without the inclusion of CI filler. As shown in , compression test specimens of G-E mixture with and without the presence of CI filler particles are fabricated. The granite particles utilized were in the range of 424–599 µm and 53–149 µm mixed in 50:50 proportion. Hybrid composite specimens were developed for varied epoxy resin content of 15–100 wt%. CI filler particles were integrated to the hybrid composite specimens in terms of 5, 10 and 15 wt%. The hybrid mixture prepared has been poured into the mold cavity and subjected to pressure for compaction. The material is allowed to cure at room temperature for 1 d and further placed in hot air oven at 600 °C for 4 h for expediting the curing process. Subsequently, the specimens were stored at room temperature for 7 d to ensure complete curing. For each weight percentage composition, a set of 4 compressive specimens were fabricated to measure its compressive strength and modulus of elasticity.
Figure 4. Specimens for compression and tensile experimental tests (a) compression specimens; (b) Composite mixture poured into mold cavity; (c) Tensile test specimens of G-E composite; (d) Tensile test specimens of G-E composite with CI filler material.
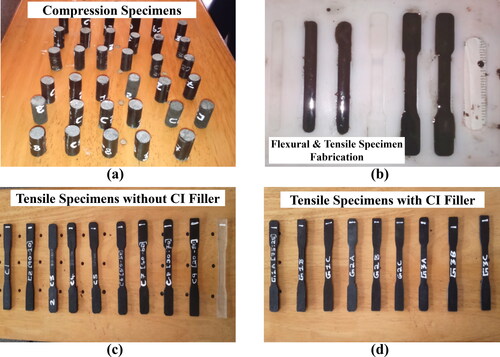
Table 1. Material composition for granite epoxy (G-E) specimens without cast iron filler particulates.
Table 2. Material composition for granite epoxy (G-E) specimens with cast iron filler particulates.
The mechanical properties of composite specimens are determined by conducting tensile and flexural tests. These properties are essential for carrying out the modal and transient analysis of composite specimen using ANSYS Workbench software. Modulus of elasticity of the specimens obtained from flexural tests is used for the validation of dynamic analysis, since the analysis is carried out in flexural mode as a cantilever beam. Fabricated specimens for tensile, flexural and damping tests are described in and . The tensile and flexural behavior of the fabricated G-E specimens without CI filler is investigated and compared with the behavior of G-E specimens with CI filler material. In each ratio, three tensile and flexural specimens are fabricated. Damping specimens with and without CI particles as filler are also prepared for different weight percentages. The natural frequency of the fabricated specimens is determined by subjecting the prismatic bar specimens to free vibration or impact hammer tests. Also, the damping factor and logarithmic decrement of specimens are determined. During fabrication, the specimens were allowed to cure in the mold for 24 h and the curing rate is accelerated by placing in a hot air oven at 600 °c for 4 h. Later the specimens are kept at room temperature for 7 d to complete the curing process.
2.4. Experimental study
The G-E composite specimens are prepared for all the compositions (1–14) listed in and with and without the inclusion of CI particles as filler material. Detailed compression, tensile, flexural and damping analysis tests are conducted to assess the mechanical and damping behavior of the fabricated G-E composite specimens.
2.4.1. Compression test
The compression test specimens were fabricated as per ASTM D695 and the length to diameter ratio is maintained as 2. The height of the specimen is 25.4 mm with 12.7 mm diameter. The compression tests are carried out on a 75 kN dual column universal testing machine of Tinius Olsen make. The speed of the test is fixed to 0.5 mm/min. As shown in , the specimens are placed between two flat compression fixtures and subjected to a progressive load. The compressive behavior of the composite specimens tested is recorded. The test is carried out until the specimen reaches its maximum load capacity and results in fracture. The modulus of elasticity and compressive strength of the specimens was measured as a function of epoxy percentages. The graph generated was recorded using HORIZON software incorporated with the UTM.
2.4.2. Tensile test
Tensile test specimens prepared as per ASTM D638 is clamped between the two fixtures on a Tinius Olsen UTM as shown in . The gauge length of the specimen is 57 mm and the rate of testing was fixed at 2 mm/min by using HORIZON software interfaced with UTM. A gradual increase in load was applied to the specimen until maximum load capacity was attained and fracture occurs. The elastic modulus, maximum stress and break elongation percentage of various specimens are recorded in the software. For each composition, three tensile specimens are tested, and average values are taken. This procedure is carried out for all tensile specimens and their behavior is investigated.
2.4.3. Flexural test
Flexural specimens were prepared as per ASTM D790. As shown in , the flexural test fixtures are fitted into the machine mountings and rollers are placed in the respective positions of the fixtures. The span length of the bottom fixture is fixed at 72 mm. The test speed is maintained constant at 2 mm/min. The specimens were placed on a 3-point contact flexural fixtures. The test is performed until the specimens reach their failure point. The elastic modulus, flexural strength and maximum load attained are recorded using the computer interface. The graphs are plotted as a function of various epoxy weight percentages and the behavior is analyzed.
2.4.4. Density test
Density test of prepared composite specimens is mainly carried out for specifying the density values for modal and transient analysis using ANSYS Workbench software. The density values of damping specimens are determined in this test. Test conduction is carried out by filling water in a measuring flask up to a mark where the specimen gets completely submerged. Specimen is then immersed into the flask and the overall volume of water displaced is noted down. The density values are computed by taking account of the mass of the specimens.
2.4.5. Damping test
Damping test is performed in the Solve Lab at NITK Surathkal with a cantilever type setup. According to the requirements of the setup at the testing center, prismatic bar specimens of G-E composite were prepared. The cantilever setup is installed with a heavily loaded basement limiting the effect of noise on the system. One end of the specimen is fixed and an accelerometer of KISTLER Company make is placed on the free end of the specimen. The schematic representation of the damping test is illustrated in . The sensitivity of the accelerometer is 101 mV/gm and the measuring range is between ±50 g. Accelerometer is connected to a data acquisition system (DAQ) of National instruments which in turn is connected to a computer interface. As shown in , an impact hammer connected to DAQ is used with a metal tip to impart excitation to the composite specimens.
Impact hammer test is carried out by providing a unit force at the free end of the specimen. The accelerometer quantifies the vibration signal created and passes the signal to the DAQ. DAQ is an interface between analog signals and computer software. After signal conditioning, data is fed to LABVIEW software where the data processing occurs and the magnitude v/s frequency response curves are generated. Thus, the natural frequency of the specimen can be determined. The damping factor and logarithmic decrement of the specimens are calculated by applying half power bandwidth method to the frequency curve. The same procedure is carried out for all the fabricated specimens and the response curves are recorded.
(1)
(1)
where
(2)
(2)
is the difference between two frequencies at the amplitude equal to maximum amplitude divided by √2. f0 is the fundamental frequency.
Also,
(3)
(3)
2.5. Numerical computation to estimate the fundamental frequency of G-E composite
The natural frequencies of the G-E composite specimen fabricated can be estimated analytically using EquationEquations (4)–(8). The values, such as elastic modulus (E), density (ρ) and dimensions of the specimens (Area ‘A’ and length ‘L’) are the input variables required for computation.
(4)
(4)
(5)
(5)
(6)
(6)
(7)
(7)
(8)
(8)
3. Results and discussions
3.1. Assessment of mechanical strength of granite epoxy composite
Detailed experimental analysis was performed on various sets of G-E composite specimens with and without the inclusion of CI filler to assess its mechanical strength. shows the compressive strength and modulus of elasticity variation obtained from the compression tests conducted on G-E composite specimens. In , for G-E composite with 0% CI filler added, the compressive strength was found to have a significant increase for 70:30 G-E content and further reduces with the increase in epoxy weight percentage. Specimens containing 85% granite content exhibited lower compressive strength, attributed to insufficient bonding between the granite particles and epoxy resin. The decrease in bonding is caused by the elevated granite concentration, potentially resulting in inadequate interlocking and adhesion between the particles and the resin matrix. Consequently, this compromise in bonding can undermine the overall structural integrity and compressive strength of the material. For varied composite mixture ratios, maximum compressive strength of 112 MPa was attained for 70:30 G-E ratio.
Figure 10. Compression test results. (a,b) Compressive strength of G-E specimens (0, 5%, 10% and 15% CI Filler) (c,d) Modulus of Elasticity of G-E specimens (0, 5%, 10% and 15% CI Filler).
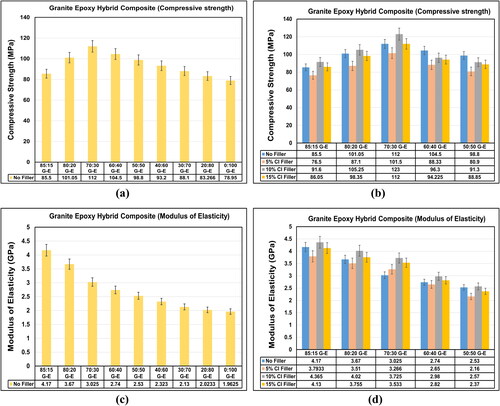
For G-E composite with 5, 10 and 15% CI filler added shown in , a further increase in compressive strength was noted for specimens with 10% addition of CI filler material. Maximum compressive strength of 123 MPa was noted for 30% of epoxy content with 10% filler material. However, 5% CI filler was found to have minimal influence on compressive strength property. Based on the test analysis, an optimum quantity of CI filler was found to improve the compressive strength behavior of G-E specimens. In , for different epoxy weight percentages, the elastic modulus of compressive specimens was found to peak at 85:15 G-E ratio to 4.17 GPa. With an increase in epoxy weight percentage, there was a significant decrease in elastic modulus observed. This suggests that composite specimens with higher granite content tend to exhibit a stiffer nature. This effect might stem from the more compact arrangement of granite particles within the composite, which increases resistance to deformation and thereby contributes to greater stiffness or reduced elasticity of the material. For the same 10% filler composition in 85:15 G-E ratio, higher modulus of elasticity around 4.365 GPa was attained. This indicates that the addition of CI filler has further increased the stiffness behavior of G-E composite.
The characteristic curve generated for tensile strength of G-E + CI composite specimens is illustrated in . Based on the variation attained, tensile strength of the fabricated specimens was found to increase with higher amount of epoxy content in the composite mixture. Whereas minimal tensile strength was noted for specimens with 85:15 G-E ratio. Such variation implies that the epoxy matrix significantly improves the tensile properties of the composite. The enhanced bonding between the epoxy resin and other components likely enhances resistance against tensile forces, thereby improving tensile strength. Moreover, the flexibility and elasticity conferred by the epoxy resin could further enhance the hybrid composite’s capacity to endure tension. From , it was noted that, higher percentage addition of granite particles resulted in reduction of tensile strength and the specimens indicated a brittle failure proving that the G-E composite is weak in tension. Such variation indicates the weakness of the hybrid composite under tension as it clearly indicates its inability to resist elongation and deformation before fracture occurs. With the addition of CI filler, an improvement in tensile behavior was noted for 5% CI addition than compared with other filler ratios in . A notable reduction in tensile strength was observed with the inclusion of CI filler in the G-E composite specimens. Increase in granite content and addition of CI filler has not effectively improved the tensile behavior of the composite specimens. In , G-E specimens with 80:20 ratio showed around 2.93% increase in elastic modulus than compared with pure epoxy test specimens. In comparison with varying CI filler percentages, higher elastic modulus was attained for 15% addition of CI filler particulates. Higher quantity of granite content and CI filler results in increased resistance to deformation within the elastic limit.
Figure 11. Tensile test results. (a,b) Tensile strength of G-E specimens (0, 5%, 10% and 15% CI Filler) (c,d) Modulus of elasticity of G-E specimens (0, 5%, 10% and 15% CI Filler).
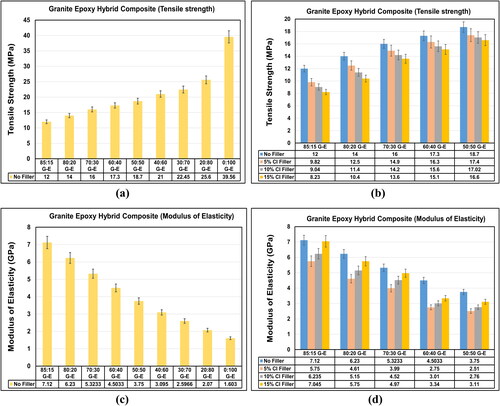
In , an incremental variation in flexural strength is recorded for test specimens of G-E + CI composite with the increase in epoxy weight percentages. G-E ratio of 30:70 attained maximum flexural strength which is 2.07 times higher than noted for 85:15 G-E ratio. An improvement in flexural strength was observed with the reduction of granite content in the G-E composite specimens in . This implies that a decrease in granite concentration facilitates improved dispersion and alignment of reinforcing elements within the hybrid composite matrix. Moreover, it potentially reduces material defects, enhancing its resistance to bending stresses. Additionally, the lower granite content may promote a more uniform distribution of the epoxy resin, further augmenting the overall flexural strength. Similar incremental variation was also attained for G-E specimens with the addition of 5, 10 and 15% CI filler in . Enhanced flexural behavior was noted for minimal percentage addition of CI filler. This indicates that even a small amount of CI filler significantly enhances the composite’s capacity to withstand bending stresses. The inclusion of CI filler likely improves the bond between the composite components, leading to better load distribution and resistance to bending deformation. Additionally, the CI filler may serve as a reinforcing agent, providing extra support and strengthening the composite structure, thereby augmenting its flexural characteristics. In , a gradual decrease in elastic modulus was noted for an increase in epoxy content. Around 5.5% increase in modulus of elasticity was noted for 85:15 G-E ratio than compared with pure epoxy specimens. At higher concentrations of granite particles, minimal variation in elastic modulus was noted for varying percentages of CI filler. However, the stiffness behavior of G-E composite specimens has shown a notable reduction with the inclusion of CI filler. Of 15% addition of CI filler has generated lower elastic modulus than compared with other CI filler ratios.
Figure 12. Flexural test results. (a,b) Flexural strength of G-E specimens (0, 5%, 10% and 15% CI Filler) (c,d) Modulus of Elasticity of G-E specimens (0, 5%, 10% and 15% CI Filler).
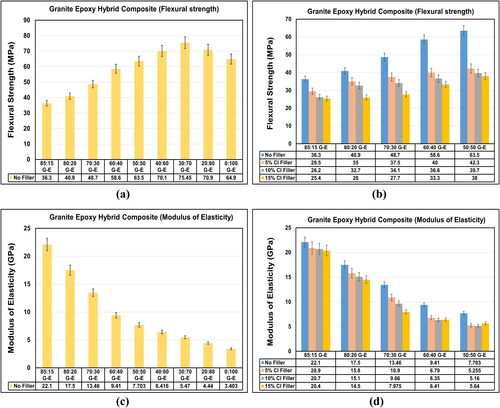
shows the density variation recorded for varying epoxy weight percentages of G-E + CI composite specimen. G-E test specimens with 15% epoxy content generated maximum density value indicating the significant influence of increased granite particle content in the composite mixture. This implies that the greater concentration of granite particles contributes to denser packing within the composite structure. This denser packing likely stems from the increased volume occupied by the granite particles, resulting in a higher mass per unit volume. Moreover, the heightened density suggests improved efficiency in interparticle packing and closer proximity between the particles, potentially enhancing mechanical properties like strength and durability. In , a reducing trend in density was noted for an increase in epoxy weight percentages. With the inclusion of CI particulates in , a notable increase in density was noted for 70:30 G-E ratio. Higher density values were obtained for 15% addition of CI filler material for all tested G-E composite ratios. Such variation indicates the effectiveness of higher percentages of granite and CI filler content in increasing the density of test specimens.
3.2. Assessment of damping behavior of granite epoxy composite
Variation in damping factor and logarithmic decrement for G-E composite with and without the inclusion of CI filler is represented in . In , higher damping values were noted for 85:15 G-E ratio and a significant drop was further noted for an increase in epoxy weight percentage until an equal proportion mixture of G-E was tested. Minimal damping values were noted for 50:50 G-E ratio which is 2.05 times lower than attained for 85:15 G-E ratio. A gradual increase in damping ratio was further noted with an increase in epoxy content in composite mixture. From , with the inclusion of 5%, 10% and 15% CI filler, a significant drop in damping ratio was noted for an increase in CI filler content in test specimens. 5% CI filler addition was found to have higher influence on the damping behavior of G-E composite specimens. The presence of CI filler is likely to enhance the dissipation of energy within the composite material, leading to improved damping properties. This effect may stem from interactions between the CI filler particles and the composite matrix, potentially resulting in increased internal friction and greater absorption of vibrational energy. Moreover, the incorporation of CI filler could induce changes in the microstructure of the composite, such as modifying the distribution of stress and strain within the material, thus further impacting its damping behavior.
Figure 14. Variation in damping ratio and Logarithmic decrement. (a,b) damping ratio of G-E specimens (c,d) Logarithmic decrement of G-E specimens.
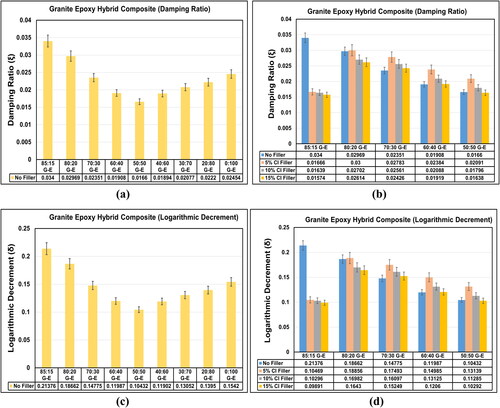
The characteristic curve attained for logarithmic decrement in , indicated maximum values for test specimens with higher granite content. A moderate drop in logarithmic decrement was noted with the increment of filler percentage in the test specimens. The logarithmic decrement curve is similar to the damping curve with higher values attained by the addition of 5% filler particles. The fundamental frequency curves of G-E with and without CI filler particles are illustrated in . For all possible combinations of G-E composite, fundamental frequency variation is illustrated for 85:15 G-E ratio with 0% and 5% CI filler particles. A significant increase in fundamental frequency was noted with the inclusion of 5% CI filler. An optimum quantity of CI filler particulate addition was found to effectively improve the damping behavior and frequencies of G-E composite specimens. Additionally, the modified composite structure arising from the optimal filler addition could contribute to the improved frequency response by influencing the material’s dynamic properties and resonant frequencies.
3.3. Finite element analysis using ANSYS Workbench
Using FE approach, the modal and transient analysis is performed on all the prepared prismatic bar specimens in ANSYS Workbench. The fundamental frequency, damping ratio and logarithmic decrement are analyzed in the software for validation with experimental values.
3.3.1. Modal analysis
This section discusses the suitability of the FE technique for detecting damage in a cantilever beam by analyzing its mode shapes and natural frequencies. The numerical simulation model described in this study has dimensions of 22 mm × 22 mm × 178 mm. illustrates a meshed model with 10,769 elements. Grid independence study was performed to obtain optimum mesh density as shown in . Experimentally measured elastic modulus and density of the specimens are given as input for FE analysis. The natural frequency generated for different mode shape is further validated with the experimental results.
Figure 16. Geometric model of damping specimen after meshing specimen with 5% Cast Iron Filler Material.
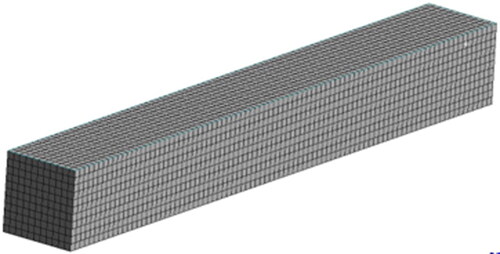
Six different mode shapes generated for G-E specimen of 85:15 ratio with and without the inclusion of 5% CI filler is illustrated in and . The free end of cantilever beam was deflected, moving from one region to another with a maximum amplitude. However, its amplitude was 0 at the fixed end and certain other regions. The free end of the cantilever beam was in one region for the first, third and fifth modes, while it is located in the opposite region for the second, fourth and sixth modes. The curvatures of the mode shape, which correspond to the second derivative of the mode shapes, are computed and depicted in and . The amplitude for every mode shape curvature was one at the fixed end and zero at the free end. The amplitude of the cantilever beam’s free end was 0 for all modes at a specific instant in time, specifically when considering the curvatures of the mode shapes. The mode shape curves were utilized for the purpose of damage detection. The natural frequency generated for each mode shapes of 85:15 G-E ratio with and without 5% CI filler is listed in and .
Figure 18. Six mode shapes of prepared 85:15 granite epoxy composite beam specimen using ANSYS Workbench.
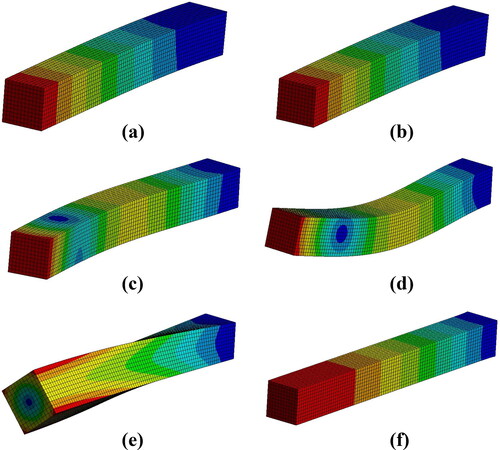
Table 3. Frequency output of modal analysis for 85:15 Granite epoxy composite specimen using ANSYS Workbench.
Table 4. Frequency output of modal analysis for 85:15 Granite epoxy specimen with 5% cast iron filler using ANSYS Workbench.
3.3.2. Transient analysis
Transient analysis was performed to estimate the damping and logarithmic decrement values of the G-E composite specimens with and without CI filler. A time domain graph was generated in transient analysis for the computation of damping values. details the comparative variation in fundamental frequency obtained for G-E + CI filler specimens of varied weight concentrations using FE analysis and experimental investigations. With the increase in epoxy weight percentages, a gradual reduction in fundamental frequencies was noted for different G-E ratios with 5, 10 and 15% CI filler material. Higher content of epoxy resin was found to effectively reduce the natural frequency of the test specimens. In both experimental and numerical simulations, higher weight concentrations of CI filler were found to generate lower frequencies than noted for 5 wt% CI filler. Such variations indicate that increased filler concentration has minimal influence on natural frequency of composite specimens. In , there is close correspondence between experimental results and FE simulations with reasonable variation observed for varied weight concentrations of granite content. With an increase in epoxy weight content, larger percentage variation was observed for G-E specimens without the inclusion of filler. This variation is within the limit considering the extraneous factors influencing the experimental tests. The percentage deviation noted for varied CI filler concentrations in indicates that maximum variation in natural frequencies was observed for epoxy weight percentage of 20 wt% and 30 wt%.
Figure 20. Variation in fundamental frequency and percentage deviation attained for experimental and ANSYS analysis for different compositions of granite epoxy composite specimens.
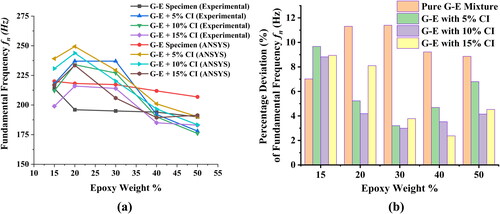
Using numerical solution, variation in damping ratio noted for G-E specimens of varied CI filler concentrations is depicted in . As the granite particulate concentrations were reduced in the composite mixture, a nominal decrease in damping values was observed. A higher quantity of granite particulates can effectively enhance the damping and vibration characteristics of machine tool structures made of proposed hybrid G-E composite. In addition to granite reinforcement material, optimal quantity of 5 wt% CI filler particles was found to improve the damping behavior of the composite specimens. For different epoxy wt%, 80:20 G-E ratio was identified as the optimal composition for which addition of CI filler further enhances the damping properties. Frequency and damping ratio variations recorded for 85:15 G-E ratio was not considered for deciding the optimal material composition influencing the damping behavior due the presence of voids and non-homogeneity caused from the presence of higher quantity of granite particulates and filler particles. A similar trend was also observed for logarithmic decrement variation in , where test specimens incorporating higher weight concentration of granite reinforcement material and 5 wt% filler particles logarithmic values. In and , similar variation in percentage deviation was noted for G-E specimens with and without the inclusion of CI filler for varied epoxy wt%. G-E composite mixture with 5% addition of CI filler was found to have minimal percentage variation than compared with higher percentage of CI filler inclusion. The percentage deviation for both damping ratio and logarithmic decrement was found to be higher for G-E composite with 10% CI filler inclusion. However, the variation showed a reducing trend with the increase in epoxy wt%. In an overall comparison, the percentage deviation data showed a variation limited to 10%, which is deemed acceptable given the influence of external factors on the experimental studies.
4. Conclusions
Mechanical property assessment and damping analysis were carried out on a G-E hybrid composite with CI filler particles using both experimental and FE approach. The compressive strength of the hybrid composite was found to increase with the reduction in granite content. 70:30 G-E ratio with 10 wt% CI filler was found to be the optimum condition generating maximum compressive strength. In terms of tensile strength, an increase in epoxy resin percentage and a minimal quantity of CI filler was found to cause a significant impact. Using 70 wt% epoxy resin in the G-E composite, improved flexural strength was noted compared to specimens with a higher proportion of granite particulates. Inclusion of CI filler particles was found to have less influence on the flexural behavior of the hybrid composite. Higher granite content improved damping behavior in the hybrid composite, while reducing granite particulate concentrations decreased the damping ratio. Adding 5 wt% CI filler further enhanced damping behavior in specimens with higher granite particle concentrations. FE numerical simulations supports experimental findings, affirming enhanced damping behavior in the hybrid composite with optimal CI filler particle inclusion. A higher weight concentration of granite particulate (80 wt%) and 5 wt% addition of CI filler was identified as the optimal combination for enhanced damping behavior.
Author contribution statement
Conceptualization, Girish Hariharan, Ganesha A; Methodology, Girish Hariharan, Gowrishankar MC; Investigation, Girish Hariharan; Supervision, Girish Hariharan, Gowrishankar MC, Balakrishna SS; Data curation, Girish Hariharan, Gowrishankar MC, Nitesh Kumar; Formal Analysis, Girish Hariharan, Ganesha A, Nitesh Kumar; Writing-Original draft, Girish Hariharan, Ganesha A, Gowrishankar MC, Nitesh Kumar; and Writing-review and editing, Girish Hariharan, Gowrishankar MC, Nitesh Kumar, Balakrishna SS. All authors have read and agreed to the published version of the manuscript.
Disclosure statement
The authors declare that they have no known competing financial interests or personal relationships that could have appeared to influence the work reported in this article.
Data availability statement
Data will be made available on request. Author to be contacted for data: Girish Hariharan ([email protected])
Additional information
Funding
References
- Abdellah, M. Y., Abdelhaleem, A., Ghulman, H. A., & Abdel-Jaber, G. T. (2022). Vibration and tribological properties of epoxy-granite composites used as novel foundations for machine elements. Journal of Polymer Engineering, 42(9), 856–867. https://doi.org/10.1515/polyeng-2022-0038
- Arun Ramnath, R., Thyla, P. R., & Harishsharran, A. K. R. (2021). Machining parameter selection in milling epoxy granite composites based on AHP. Materials Today: Proceedings, 42, 319–324. https://doi.org/10.1016/j.matpr.2020.09.340
- Bakar, M., Duk, R., Przybyłek, M., & Kostrzewa, M. (2009). Mechanical and thermal properties of epoxy resin modified with polyurethane. Journal of Reinforced Plastics and Composites, 28(17), 2107–2118. https://doi.org/10.1177/0731684408091703
- Bhanuprakash, L., Thejasree, P., John, F., & Prabha, R. (2023). Study on mechanical and micro-structural properties of aluminium matrix composite reinforced with graphite and granite fillers. Materials Today: Proceedings. https://doi.org/10.1016/j.matpr.2023.06.243
- Bisen, H. B., Hirwani, C. K., Satankar, R. K., Panda, S. K., Mehar, K., & Patel, B. (2020). Numerical study of frequency and deflection responses of natural fiber (Luffa) reinforced polymer composite and experimental validation. Journal of Natural Fibers, 17(4), 505–519. https://doi.org/10.1080/15440478.2018.1503129
- Çallıoğlu, H., Sayer, M., & Demir, E. (2011). Impact behavior of particles filled‐glass/polyester composite plates. Polymer Composites, 32(7), 1125–1133. https://doi.org/10.1002/pc.21130
- Chaturvedi, R., Pappu, A., Tyagi, P., Patidar, R., Khan, A., Mishra, A., Gupta, M. K., & Thakur, V. K. (2022). Next-generation high-performance sustainable hybrid composite materials from silica-rich granite waste particulates and jute textile fibres in epoxy resin. Industrial Crops and Products, 177, 114527. https://doi.org/10.1016/j.indcrop.2022.114527
- Chen, T. C., Chen, Y. J., Hung, M. H., & Hung, J. P. (2016). Design analysis of machine tool structure with artificial granite material. Advances in Mechanical Engineering, 8(7), 168781401665653. https://doi.org/10.1177/1687814016656533
- Chinnuraj, S., Ramaswamy, T. P., Venkatachalam, M. P., Nataraj, M., Murugan, R., Selvakumar, M., Dhandabani, S., & ManojKumar, K. N. (2021). Optimization of process parameters of epoxy granite for strength and damping characteristics using TOPSIS method. Journal of Testing and Evaluation, 49(3), 20190002. https://doi.org/10.1520/JTE20190002
- Chinnuraj, S., Thyla, P. R., Elango, S., Venugopal, P. R., Mohanram, P. V., Nataraj, M., Mohanraj, S., Manojkumar, K. N., & Ayyasamy, S. (2020). Static and dynamic behavior of steel-reinforced epoxy granite CNC lathe bed using finite element analysis. Proceedings of the Institution of Mechanical Engineers, Part L: Journal of Materials: Design and Applications, 234(4), 595–609. https://doi.org/10.1177/1464420720904606
- Chuang, H. C., & Chen, C. R. (2022). Study on the application of a granite composite material in five-axis CNC-VMC machine Tool. Journal of Physics: Conference Series, 2345(1), 012022. https://doi.org/10.1088/1742-6596/2345/1/012022
- Dhanabal, P., Thyla, P., Kalayarasan, M., & Mahendrakumar, N. (2023). The influence of steel reinforcements on static rigidity of epoxy granite spindle head for dynamic performance enhancement of machining center: Experiments and finite element simulation. Proceedings of the Institution of Mechanical Engineers, Part L: Journal of Materials: Design and Applications, 238(5), pp. 875–889.
- Gomes, M. L. P., Carvalho, E. A., Demartini, T. J., de Carvalho, E. A., Colorado, H. A., & Vieira, C. M. F. (2021). Mechanical and physical investigation of an artificial stone produced with granite residue and epoxy resin. Journal of Composite Materials, 55(9), 1247–1254. https://doi.org/10.1177/0021998320968137
- Haddad, H., & Al Kobaisi, M. (2013). Influence of moisture content on the thermal and mechanical properties and curing behavior of polymeric matrix and polymer concrete composite. Materials and Design, 49, 850–856. https://doi.org/10.1016/j.matdes.2013.01.075
- Heisel, U., & Gringel, M. (1996). Machine tool design requirements for high-speed machining. CIRP Annals, 45(1), 389–392. https://doi.org/10.1016/S0007-8506(07)63087-X
- Kashyzadeh, K. R., & Ghorbani, S. (2020). Numerical study of free vibration behaviour of filled tool holder using epoxy-granite. Journal of Physics: Conference Series, 1687(1), 012025. https://doi.org/10.1088/1742-6596/1687/1/012025
- Madhusudhan, R., Suresh Kumar, G., Venkateshwar Reddy, Y., & Venkata Mohana Reddy, P. (2022). Study on the effect of granite powder fillers in surface-treated cordia dichotoma fiber-reinforced epoxy composite. Journal of Natural Fibers, 19, 2002–2017. https://doi.org/10.1080/15440478.2020.1789022
- Möhring, H. C., Brecher, C., Abele, E., Fleischer, J., & Bleicher, F. (2015). Materials in machine tool structures. CIRP Annals, 64(2), 725–748. https://doi.org/10.1016/j.cirp.2015.05.005
- Mula, V. R., Ramachandran, A., & Pudukarai Ramasamy, T. (2023). A review on epoxy granite reinforced polymer composites in machine tool structures – Static, dynamic and thermal characteristics. Polymer Composites, 44(4), 2022–2070. https://doi.org/10.1002/pc.27229
- Munoa, J., Beudaert, X., Dombovari, Z., Altintas, Y., Budak, E., Brecher, C., & Stepan, G. (2016). Chatter suppression techniques in metal cutting. CIRP Annals, 65(2), 785–808. https://doi.org/10.1016/j.cirp.2016.06.004
- Ojha, A. R., & Biswal, S. K. (2019). Thermo physico-mechanical behavior of palm stalk fiber reinforced epoxy composites filled with granite powder. Composites Communications, 16, 158–161. https://doi.org/10.1016/j.coco.2019.10.003
- Omar, M., Abdelrhman, Y., M., Hassab, I., M., & Khierldeen, W. (2021). Experimental study on compressive strength and flexural rigidity of epoxy granite composite material. JES Journal of Engineering Sciences, 49, 198–214. https://doi.org/10.21608/jesaun.2021.61303.1033.
- Öztürk, B. (2010). Hybrid effect in the mechanical properties of jute/rockwool hybrid fibres reinforced phenol formaldehyde composites. Fibers and Polymers, 11(3), 464–473. https://doi.org/10.1007/s12221-010-0464-3
- Pawar, M. J., Patnaik, A., & Nagar, R. (2017). Investigation on mechanical and thermo‐mechanical properties of granite powder filled treated jute fiber reinforced epoxy composite. Polymer Composites, 38(4), 736–748. https://doi.org/10.1002/pc.23633
- Piratelli-Filho, A., & Levy-Neto, F. (2010). Behavior of granite-epoxy composite beams subjected to mechanical vibrations. Materials Research, 13(4), 497–503. https://doi.org/10.1590/S1516-14392010000400012
- Piratelli-Filho, A., & Shimabukuro, F. (2008). Characterization of compression strength of granite-epoxy composites using design of experiments. Materials Research, 11(4), 399–404. https://doi.org/10.1590/S1516-14392008000400003
- Raja, T., Mohanavel, V., Suresh Kumar, S., Rajkumar, S., Ravichandran, M., & Subbiah, R. (2022). Evaluation of mechanical properties on kenaf fiber reinforced granite nano filler particulates hybrid polymer composite. Materials Today: Proceedings, 59, 1345–1348. https://doi.org/10.1016/j.matpr.2021.11.548
- Ravichandran, B., & Sasikumar, M. (2016). Mechanical, ablative, and thermal properties of cenosphere‐filled ceramic/phenolic composites. Polymer Composites, 37(6), 1906–1913. https://doi.org/10.1002/pc.23369
- Ray, S., Rout, A. K., & KuSahoo, A. (2017). A study on tribological behavior of glass-epoxy composite filled with granite dust. IOP Conference Series: Materials Science and Engineering, 225, 012097. https://doi.org/10.1088/1757-899X/225/1/012097
- Reddy, B. M., Reddy, R. M., Reddy, D. M. S., Ananthakrishna, N., & Reddy, P. V. (2022). Development and characterisation of Cordia Dichotoma Fibre/Granite filler reinforced polymer blended (Epoxy/Polyester) hybrid composites. Advances in Materials and Processing Technologies, 8(1), 461–477. https://doi.org/10.1080/2374068X.2020.1815138
- Shanmugam, C., Thyla, P. R., & Dhanabal, P. (2022). Numerical studies on VMC base made of epoxy granite. Materials, Design, and Manufacturing for Sustainable Environment. Select Proceedings of ICMDMSE (pp. 317–327). Springer. https://doi.org/10.1007/978-981-19-3053-9_25.
- Shanmugam, C., Thyla, P. R., Kumar, N. M., Rabik, S. J., Krishna, R. R., & Kumar, S. V. (2017). Experimental studies on mechanical properties of epoxy granite for machine tool structure using design of experiments. The Asian Journal of Research in Social Sciences and Humanities, 7, 1333. https://doi.org/10.5958/2249-7315.2017.00246.5
- Shetty Ravindra, R., & Rai, S. K. (2008). Tensile, flexural, density and void cStudies on granite powder filled hydroxyl terminated polyurethane toughened epoxy composite. Journal of Reinforced Plastics and Composites, 27(15), 1663–1671. https://doi.org/10.1177/0731684408088891
- Sripriyan, K., & Karthick, S. (2024). Effect of granite filler on mechanical properties and free damping of silk-sisal–reinforced epoxy composites. Sustainable machining and green manufacturing (pp. 1–12). John Wiley & Sons, Ltd. https://doi.org/10.1002/9781394197866.ch1.
- Subhash, C., Krishna, M. R., Raj, M. S., Sai, B. H., & Rao, S. R. (2018). Development of granite powder reinforced epoxy composites. Materials Today: Proceedings, 5(5), 13010–13014. https://doi.org/10.1016/j.matpr.2018.02.286
- Suh, J. D., & Lee, D. G. (2008). Design and manufacture of hybrid polymer concrete bed for high-speed CNC milling machine. International Journal of Mechanics and Materials in Design, 4(2), 113–121. https://doi.org/10.1007/s10999-007-9033-3
- Venugopal, P. R., Dhanabal, P., Thyla, P. R., Mohanraj, S., Nataraj, M., Ramu, M., & Sonawane, H. (2020). Design and analysis of epoxy granite vertical machining centre base for improved static and dynamic characteristics. Proceedings of the Institution of Mechanical Engineers, Part L: Journal of Materials: Design and Applications, 234(3), 481–495. https://doi.org/10.1177/1464420719890892
- Venugopal, P. R., Kalayarasan, M., Thyla, P. R., Mohanram, P. V., Nataraj, M., Mohanraj, S., & Sonawane, H. (2019). Structural investigation of steel-reinforced epoxy granite machine tool column by finite element analysis. Proceedings of the Institution of Mechanical Engineers, Part L: Journal of Materials: Design and Applications, 233(11), 2267–2279. https://doi.org/10.1177/1464420719840592
- Zhou, X., Hutsch, T., Penter, L., Rudolph, H., Ihlenfeldt, S., & Weißgärber, T. (2023). Experimental and numerical analysis of damping behavior of iron graphite composite in machine tool joint. Journal of Vibration and Control, 29(23–24), 5586–5597. https://doi.org/10.1177/10775463221138379
- Zhou, Y., Tian, Y., & Yang, B. (2023). Root vegetable side streams as sources of functional ingredients for food, nutraceutical and pharmaceutical applications: The current status and future prospects. Trends in Food Science and Technology, 137, 1–16. https://doi.org/10.1016/j.tifs.2023.05.006
- Zhou, Y., Zhang, J., Zhang, R., Liu, E., Xue, X., Xing, X. and Zhang, Q (2023). Effect of nano-Al2O3/epoxy resin composite on the shear strength recovery of fractured rock masses with various crack widths and SCA interfacial treatments. Case Studies in Construction Materials, 18, e01715. https://doi.org/10.1016/j.cscm.2022.e01715
- Zhou, Y., Zhang, R., Zhang, J., Li, Y., Li, Z., Xing, X., Zhang, Q., & Feng, G. (2023). Brazilian splitting testing of the restorative properties of eco-friendly epoxy resin on cracked granite samples with various widths. Construction and Building Materials, 401, 132907. https://doi.org/10.1016/j.conbuildmat.2023.132907