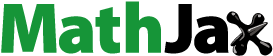
Abstract
Heat together with mass transfer of magnetohydrodynamics (MHD) non-Newtonian nanofluid flow over an inclined plate embedded in a porous medium with influence of thermophoresis and Soret-Dufour is studied. The novelty of this study is the combined effects of Soret, Dufour and thermophoresis with nanofluid flow on heat together with mass transfer. The flow is considered over an inclined plate embedded in a porous medium. Appropriate similarity transformations were used to simplify the governing coupled nonlinear partial differential equations into coupled nonlinear ordinary differential equations. A novel and accurate numerical method called spectral homotopy analysis method (SHAM) was used in solving the modelled equations. SHAM is the numerical version of the well-known homotopy analysis method (HAM). It involves the decomposition of the nonlinear equations into linear and nonlinear equations. The decomposed linear equations were solved using Chebyshev pseudospectral method. The findings revealed that the applied magnetic field gives rise to an opposing force which slows the motion of an electrically conducting fluid. Increase in the non-Newtonian Casson fluid parameter increases the skin friction factor and reduces the rate of heat and mass transfer. The present results are compared with existing work and found to be in good agreement.
1. Introduction
Combined effects of heat together with mass transfer problem have received considerable attention by many researchers because of their applications in science and chemical engineering processes. Heat transfer fluids such as oil, water, and ethylene glycol mixtures are poor thermal conductivity and poor heat transfer fluid. As a result of their poor thermal conductivity, they are used as a cooling tool in enhancing manufacturing and costs of operation. Many researchers have attempted the enhancement of these fluids thermal conductivity by suspending nanoparticles in liquids (Abu-Nada, Hakan, and Pop Citation2012). Nanofluids contains Ultrafine nanoparticles suspended in a base fluid, it can be an organic solvent or water (Choi, Citation2009). Rajesh, Chamkha, and Mallesh (Citation2016) presented transient MHD free convection flow and heat transfer of nanofluid using implicit finite difference numerical method. The study concluded that Cu-water nanofluid achieved an improved heat transfer rate compared with the other nanofluid for all values of t. Latiff, Uddin, and Md. Ismail (Citation2016) examined Stefan blowing effect on bioconvective flow of nanofluid over a solid rotating stretchable disk. Their flow equations were solved using Runge-Kutta-Fehlberg method. Heat and mass transfer on mixed convection flow of chemically reacting nanofluid have been considered by Mahanthesh, Gireesha, and Gorla (Citation2016). They used Laplace transform method to obtain a close form solutions. It is noticed in their study that increase in chemical reaction in the presence of nanofluid brings a rapid decrease to the dimensionless concentration profiles. Ullah, Shafie, Khan, and Hsiao (Citation2018) presented Brownian diffusion and thermophoresis mechanism in Casson fluid over a moving wedge. They solved their flow equations numerically using the Keller box method. The study concluded that thermal radiation assisted the heat transfer rate.
Rafique et al. (Citation2019) elucidate solution of Casson nanofluid numerically. It was concluded in the study that thermophoresis factor increases the temperature and decreases concentration profile. Waqas (Citation2020) examined heat transfer analysis of ferromagnetic non-Newtonian liquid with heterogeneous and homogeneous reactions. Their flow equations were solved using bvp4c scheme and their result shows that velocity and thermal fields are having opposite behaviour because of the presence of ferrohydrodynamics interaction parameter. Recently, Ullah, Nadeem, Khan, Ul Haq, and Tlili (Citation2020) studied influence of metallic nanoparticles in water. Their flow equations were solved using shooting method and concluded that increase in the ratio of nanoparticles has a significant increase in temperature. Mondal, Mishra, Kundu, and Sibanda (Citation2020) examined entropy generation of variable viscosity and thermal radiation on magneto nanofluid flow. Their flow equations were solved using spectral quasi-linearization method. They concluded that local Nusselt number decreases with increase in Brownian motion. Naz, Noor, Hayat, Javed, and Alsaedi (Citation2020) solved the dynamism of magnetohydrodynamic cross nanofluid using optimal homotopy analysis method. They concluded in the study that Brownian motion has great effect on the fluid concentration
The study of non-Newtonian fluid flow with heat transport processes are widely considered in recent times due to their applications in engineering. Examples of such fluids include biological fluids (blood, Salvia, etc.), foodstuffs (jellies, jams, soups, etc.) are non-Newtonian fluid because of their behaviour as explained by Xu and Liao (Citation2009). Non-Newtonian fluid finds application in polymer industries, electronic cooling system, heat exchangers and so on. The non-Newtonian fluid of nonlinearity between shear rate and shear stress reforms the behaviour of the fluid flow and hereby affect the ability of the fluid transporting heat. A comparative study of non-Newtonian fluids flow past a stretching sheet was investigated by Ramana Reddy, Anantha Kumar, Sugunamma, and Sandeep (2018). Their flow equations were solved using Runge-Kutta Fehlberg technique and the analysis shows that Casson fluid attains highest velocity when it is compared with Maxwell fluid. Animasaun and Pop (Citation2017) studied non-Newtonian Carreau fluid flow driven by catalytic surface reactions numerically using shooting method. They concluded that the temperature distribution in the flow of viscoelastic Carreau fluid is greater than that of a Newtonian fluid. Gireesha, Ganesh Kumar, Ramesh, and Prasannakumara (Citation2018) studied heat and mass transfer of Oldroyd-B nanofluid over a stretching sheet. Their reduced equations were solved using RKF-45 method and result obtained revealed that nonlinear radiation is more effective than linear radiation.
Animasaun (Citation2015) examined effects of thermophoresis, variable viscosity and thermal conductivity on free convective flow using shooting method. It was concluded in the study that variable viscosity and thermal conductivity has a significant effect on the flow layers. Alao, Fagbade, and Falodun (Citation2016) presented unsteady heat and mass transfer flow of a chemically reacting fluid using spectral relaxation method. They found out that the chemical reaction acts destructively by reducing the concentration fields. Hayat et al. (Citation2016a) explored mixed convection flow of a Burgers nanofluid. Another study of Hayat et al. (Citation2016b) examined 2D stratified flow of Oldroyd-B fluid with chemical reaction. Hayat, Zubair, Waqas, Alsaedi, and Ayub (Citation2017) considered double stratified chemically reactive flow of Powell-Erying liquid. It was concluded in the study that skin friction enhances due to the presence of wall thickness parameter. Khan, Waqas, Hayat, and Alsaedi (Citation2017) considered Soret-Dufour effects on Jeffrey stretching fluid flow. Their flow equations were solved analytically and they concluded that higher Prandtl number leads to reduction in temperature. Mondal, Pal, Chatterjee, and Sibanda (Citation2018) examined MHD mixed convection mass transfer over an inclined plate. It was concluded in the study that as thermophoretic parameter increases, the concentration profile decreases. Fagbade, Falodun, and Omowaye (Citation2018) considered MHD natural convection flow of viscoelastic fluid using spectral homotopy analysis approach.
Double diffusive flow (heat and mass transfer) finds applications in many chemical engineering processes. Heat and mass transfer flow is driven by buoyancy due to both temperature and concentration gradients. The simultaneous occurrence of heat and mass transfer in a fluid on motion results to complications in the relations between the energy fluxes and the driving potentials. Dufour or diffusion-thermal effect is the energy flux caused by composition gradient while Soret or thermal-diffusion effect is the mass fluxes created by temperature gradient. The effect of both Soret and Dufour are mostly neglected in the past due to their smaller order of magnitude as presented by Fick’s laws. Soret effect has been utilized for isotope separation. Alao et al. (Citation2016) explained that the effects of Soret and Dufour on the velocity, temperature and concentration boundary layers are opposite. Omowaye, Fagbade, and Ajayi (Citation2015) presented Dufour and Soret effects on steady MHD convective flow. The study concluded that an increase in the Dufour number reduces the skin friction coefficient and rate of heat transfer. Amanulla, Saleem, Wakif, and AlQarni (Citation2019) studied MHD Prandtl fluid flow past an isothermal permeable sphere with slip effects. Ahmed and Rashed (Citation2019) examined MHD natural convection in a heat generating porous medium-filled wavy enclosures using Buongiorno’s nanofluid model. Hayat et al. presented Soret and Dufour effects on MHD peristaltic flow of Prandtl fluid in a rotating channel.
The objective of this paper is to investigate mechanism of Soret-Dufour and thermophoresis on heat and mass transfer flow of MHD non-Newtonian nanofluid over and inclined plate. To the very best of my knowledge, no studies available in the literature discussing Soret-Dufour and thermophoresis effects on heat and mass transfer flow of MHD non-Newtonian nanofluid. The aim of this paper is to elucidate the flow behaviour of reservoir fluids. The flow behaviour based on the characteristics of the reservoir. Hence, the type of fluid considered in this paper is non-Newtonian Casson fluid and the viscosity and thermal conductivity of the fluid varies. The physical situation that is modelled is the flow of a Casson non-Newtonian model embedded in a porous medium in an inclined plate. The fluid viscosity and thermal conductivity is considered to vary within the boundary layer. The present paper considered the viscosity and thermal conductivity to vary because as the fluid moves in the layers, their viscosity and temperature changes. Hence, it is not realistic to consider the viscosity and thermal conductivity to be constant. The reduced system of ordinary differential equations is solved numerically by using spectral homotopy analysis method (SHAM). The numerical outcomes are obtained for the physical parameters the skin friction, local Nusselt number and local Sherwood number against different values of flow parameters.
2. Flow analysis
Consider a two-dimensional, laminar flow of an incompressible fluid with nanoparticles in an inclined plane. The plate is inclined at an acute angle
to the horizontal. The temperature and concentration of the nanoparticle volume fraction of the plate surface are θw and
respectively. Also, the free stream temperature and concentration of the nanoparticle volume fraction are denoted by
and
respectively (see ). In this paper, we ignored convective acceleration and diffusion so that the porous medium can reduce to the Darcy’s law
The flow direction is towards x-axis at constant wall temperature θw. The fluid considered is water-based which involves solid particles such as
and Ni. The fluid properties are constant except the viscosity and thermal conductivity of the fluid. See for thermophysical properties of modified nanofluid. The porous medium is assumed to be homogeneous and saturated with fluid in local thermodynamic equilibrium. All the properties of the fluid are constant except density in the buoyancy term of momentum equation. A magnetic field of uniform strength B0 is applied in
direction normal to the plate and the magnetic Reynolds number is assumed to be small so that induced magnetic field is neglected. Based on the work of Fredrickson (1964) and the definition of viscosity
the rheological equation of a Casson fluid can be written as:
Table 1. Numerical values of nanoparticles and water.
Under the assumptions above, the simplified governing equations becomes
(5)
(5)
(6)
(6)
(7)
(7)
(8)
(8)
together with the boundary conditions
(9)
(9)
(10)
(10)
In the concentration equation (8), the thermophoretic velocity VT can be written as Alam, Rahman, and Sattar (Citation2009)
(11)
(11)
where kth-thermophoretic coefficient. The kth values as reported by Batchelor and Shen (Citation1985) and discussed by Animasaun (Citation2015) are taking between 0.2 to 1.2 and it is defined from the theory of Talbot, Cheng, Schefer, and Willis (Citation1980) as:
(12)
(12)
where
are constant, λg and λp are the thermal conductivity of both fluid and diffused particles respectively, kn is the Knudsen number.
Suppose that the temperature difference within the flow regime is sufficiently small such that can be expressed as a linear function of
With the expansion of
in Taylor’s series about
and neglecting higher order terms to obtain (Idowu and Falodun, Citation2019).
(13)
(13)
Applying the Roseland approximation, we have the radiative heat flux as
(14)
(14)
where σe-Stefan-Boltmann constant and ke-mean absorption coefficient. The stream function
is defined as
and
thus the stream function automatically satisfied the continuity equation (5). The similarity transformation used in this study are given by
(15)
(15)
Using EquationEquations (11)–(15) on the governing EquationEquations (6)–(8) and the boundary conditions (9) and (10), the transformed momentum, energy and concentration equations with the boundary conditions are
(16)
(16)
(17)
(17)
(18)
(18)
together with the boundary conditions
(19)
(19)
(20)
(20)
Note that: are the variable viscosity parameter, thermal Grashof number, mass Grashof number, magnetic parameter, permeability parameter, variable thermal conductivity parameter, radiation parameter, Prandtl number, heat generation parameter, Eckert number, Dufour number, Brownian motion parameter, thermophoresis parameter, Schmidt number, chemical reaction parameter, Soret number, Lewis number and thermophoretic parameter. The physical quantities of interest are the skin friction, Nusselt number and Sherwood number. The skin friction due to viscous drag in the vicinity of the walls is given as
where
The rate of heat transfer (Nusselt number) due to the heat transfer between the fluid and wall is given as
where
The rate of mass transfer gives rise to the Sherwood number given by
where
3. Solution techniques
In this section, the SHAM is applied on the transformed equations (16)–(18) subject to (19) and (20). SHAM is the discrete version of the traditional homotopy analysis method (HAM). HAM is useful in decomposing system of nonlinear differential equation to linear differential equations. By applying SHAM on the decomposed linear ordinary differential equations, the Chebyshev spectral collocation method is used to solve the resulting equations. The physical region is first transformed from the physical region to the
by using the technique of domain truncation (Sibanda, Motsa, and Makukula, Citation2012). Hence, the problem solution is obtained in the interval
and not
again. It resulted to the use of the following algebraic mapping
(21)
(21)
For convenience we make the boundary conditions homogeneous by applying the transformations
(22)
(22)
substituting EquationEquation (22)
(22)
(22) into (16)–(18) to obtain
(23)
(23)
(24)
(24)
(25)
(25)
Simplifying the above equations by setting
Substituting the above coefficient parameters into EquationEquations (23)–(25) to obtain
(26)
(26)
(27)
(27)
(28)
(28)
EquationEquations (26)–(28) are nonlinear equations. In the application of SHAM, the nonlinear equations are decomposed into linear and nonlinear parts. It should be noted that the derivatives of f, T and C are with respect to ξ defined by:
(29)
(29)
An initial guess is chosen with reference to the boundary conditions (15) and (16) as the following functions
(30)
(30)
The non-homogeneous linear part of EquationEquations (26)–(28) are decomposed from the nonlinear part as the following equations
(31)
(31)
(32)
(32)
(33)
(33)
subject to:
(34)
(34)
The boundary conditions (34) is chosen to be all equals to zero with reference to the transformed domain to be able to implement the linear part SHAM solution. The Chebyshev pseudospectral method is applied on EquationEquations (26)–(28). The unknown functions
and Tl in the EquationEquations (26)–(28) are approximated as a truncated series of Chebyshev polynomials given by Fagbade et al. (Citation2018) as:
(35)
(35)
(36)
(36)
(37)
(37)
where
and
are the kth Chebyshev polynomial and
are Gauss-Lobatto collocation point. The Chebyshev nodes in the transformed domain
are defined by the Gauss-Lobatto collocation points (Trefethen, Citation2000) given by
(38)
(38)
provided
and N + 1 is the number of collocation points. The unknown functions
and
are approximated by the use of Lagrange form of interpolating polynomial which interpolates the unknown functions
and
at the Gauss-Lobatto collocation points as defined in EquationEquation (38)
(38)
(38) .
4. Results and discussion
The transformed governing equations (16)–(18) subject to the boundary conditions (19) and (20) are set of coupled highly non-linear ordinary differential equations. These set of equations were solved numerically using spectral homotopy analysis method. To study the behaviour of various flow parameters such as Casson, heat generation parameter, Soret-Dufour parameter, chemical reaction parameter, radiation parameter, etc, a comprehensive numerical computation is carried out.
represents the effect of Casson non-Newtonian fluid parameter on the velocity, temperature and concentration fields. With increase in β, it is noticed in that transport rate reduces within the thermal boundary layer. A slight decrease in the temperature field is observed as the values of β increases. It worth mentioning that as Casson fluid parameter approaches infinity, the fluid behaves as Newtonian fluid. Because of increase in the elasticity stress parameter, there is thickening of the thermal boundary layer. The graphical results in is in excellent agreement with the previous work of Zaigham Zia, Ullah, Waqas, Alsaedi, and Hayat (Citation2018). illustrates the effect of Dufour parameter
on the velocity, temperature and concentration fields. It is observed that increase in the values of Df increases the velocity, temperature fields, hydrodynamics and thermal boundary layer. Increase in the values of Df is noticed to has no effect on the concentration profile. The effect of Df as presented in is in good agreement with that of Alao et al. (Citation2016). The diffusion-thermal added to the thermal boundary layer influences the temperature field.
Figure 2. Effect of Casson parameter on the (a) velocity, (b) temperature and (c) concentration profiles when
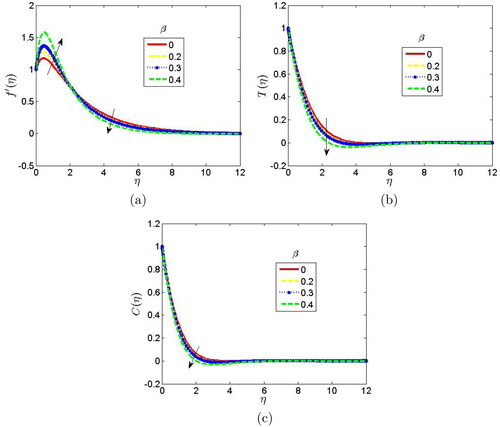
Figure 3. Effect of Dufour parameter on the (a) velocity, (b) temperature and (c) concentration profiles when
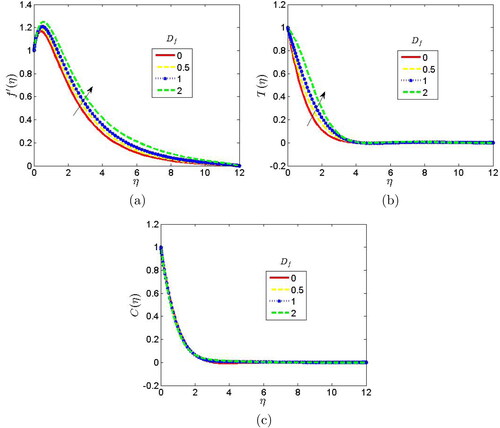
The effect of magnetic parameter (M) on velocity, temperature and concentration fields is shown in . In , increase in the values of magnetic parameter causes a damping effect on the velocity field by producing a drag-like force called Lorentz force. This force acts in the opposite direction and thereby reduces the motion of an electrically conducting fluid. With increasing value of the magnetic parameter, the momentum boundary layer thickness decreases while the thermal boundary layer slightly increases far away from the plate as shown in . This result was found to be in agreement with the previous work of Fagbade et al. (Citation2018). In addition, increase in the values of M has no effect on the concentration field. illustrates the effect of Brownian motion parameter on the velocity, temperature and concentration fields. Increase in the values of Brownian motion parameter within the hydrodynamic boundary layer brings more erratic movement of nanoparticles in the porous medium surroundings. Increase in the values of Nb in is observed to decrease velocity and concentration fields of the fluid nanoparticles. This is as a result of the random collision of the fluid particles which causes reduction on the fluid velocity. It is obvious from that increase in Nb slightly increases temperature and the thermal boundary layer because of the nanofluid porosity in the hydrodynamic and thermal boundary layer. In addition, increase in the values of Nb in the boundary layer decreases the solutal concentration.
Figure 4. Effect of magnetic parameter on the (a) velocity, (b) temperature and (c) concentration profiles when
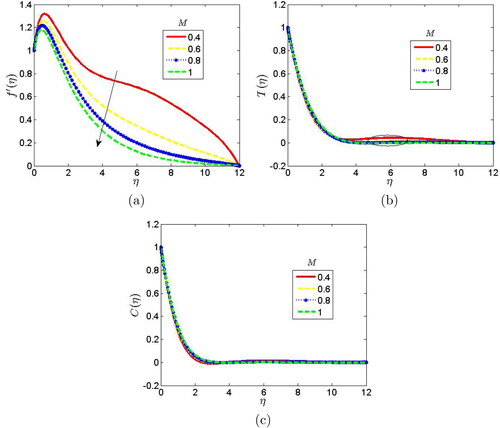
Figure 5. Effect of Brownian motion parameter on the (a) velocity, (b) temperature and (c) concentration profiles when
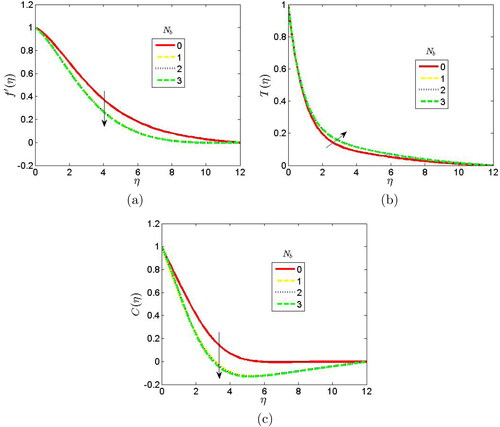
depicts the effect of porosity term on the velocity, temperature and concentration fields. Increasing the porosity expands holes and allows more movement of nanoparticles within the hydrodynamics and thermal boundary layer. Increase in the porosity term Ps brings decrease to the momentum boundary layer thickness and thereby decreases the fluid velocity as shown in . As a result of increase in the porosity term, the thermal boundary layer thickness increases. This result is as shown in . Effect of Ps is negligible on the concentration field. illustrates the effect of radiation parameter
on the velocity, temperature and concentration fields. When the radiation parameter is increased, the fluid temperature, hydrodynamic and thermal boundary layer increases. Physically, increase in Rp added more heat energy to the thermal boundary layer. This gives room for more temperature and thereby increase temperature field. The temperature field as shown in increases the entire thermal boundary layer. Increase in Rp is seen to decrease the nanofluid concentration close to the plate.
Figure 6. Effect of porosity parameter on the (a) velocity, (b) temperature and (c) concentration profiles when
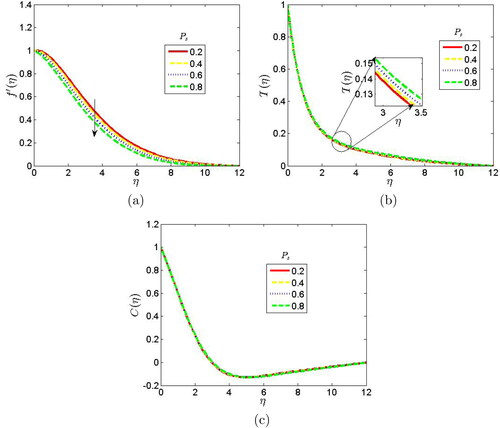
Figure 7. Effect of radiation parameter on the (a) velocity, (b) temperature and (c) concentration profiles when
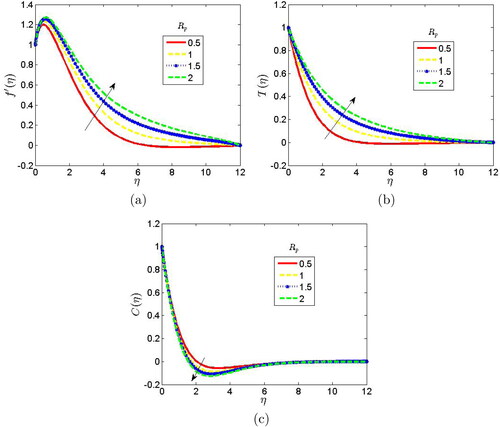
depicts the effect of Soret parameter on the velocity, temperature and concentration fields. Increase in the values of So is noticed to increase the fluid velocity and the momentum boundary layer thickness as shown in . Also, increase in the values of Soret parameter accelerates the concentration field close to the plate and negligible at the free stream. Effect of the Schmidt number
on the velocity, temperature and concentration fields is illustrated in . The Schmidt is a dimensionless number which is defined as the ratio of fluid viscosity to mass diffusivity. Hence, if the viscosity of fluid is greater than mass diffusivity, there is going to be more Schmidt number within the entire boundary layer. It is observed that increase in Sc drastically decrease the velocity and concentration field due to the nanofluid porosity within the hydrodynamic and solutal boundary layer. Increase in the values of Sc, increase the solutal boundary layer. The effect of thermal Grashof number
on the velocity, temperature and concentration field is illustrated in . The buoyancy force acts like as favourable pressure gradient on the fluid flow and increase nanofluid particles within the boundary layer. This is shown in as increase in the thermal Grashof number
increases the momentum boundary layer and slightly reduces the thermal and mass boundary layer.
Figure 8. Effect of Soret parameter on the (a) velocity, (b) temperature and (c) concentration profiles when
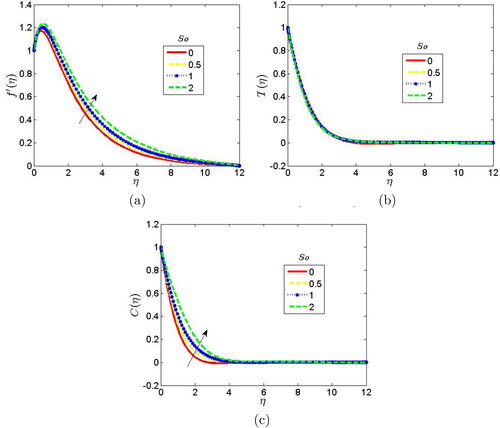
Figure 9. Effect of Schmidt number on the (a) velocity, (b) temperature and (c) concentration profiles when
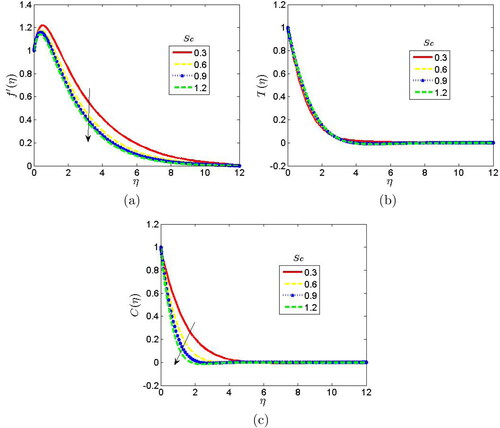
Figure 10. Effect of thermal Grashof number on the (a) velocity, (b) temperature and (c) concentration profiles when
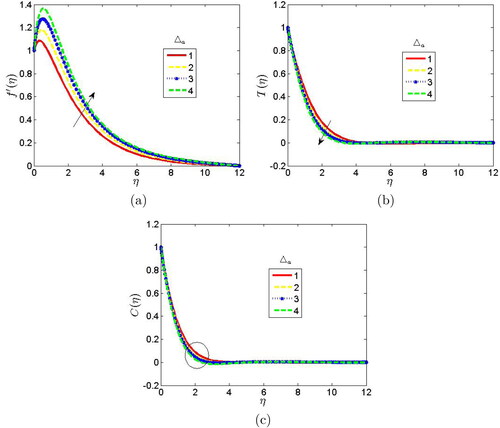
depicts the effect of Prandtl number (Pr) on the velocity, temperature and concentration profiles. The velocity profile is observed to decrease with increase in the values of Prandtl number (Pr). This is because fluids that have higher Pr possess greater viscosities and thereby reduces the fluid velocities and lower the wall skin friction coefficient. In addition, increase in the values of Pr correspond to a decrease in the fluid temperature and the thermal boundary layer thickness. For small values of Pr, that is Pr < 1 the fluid becomes very conductive. Increase in the values of Pr is noticed to increase fluid concentration at the wall.
Figure 11. Effect of Prandtl number on the (a) velocity, (b) temperature and (c) concentration profiles when
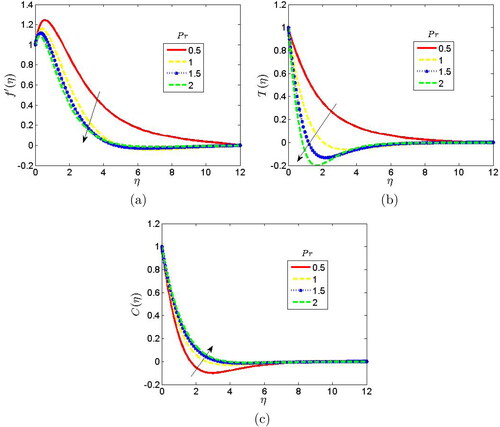
From , increase in the values of Lewis number increases the skin friction coefficient and Sherwood number whereas it decreases the Nusselt number. From , increase in the magnetic parameter (M) decreases the three physical quantities of engineering (that is, skin friction coefficient, Nusselt number and Sherwood number). In , increase in the values of Lewis number (Ln) increases the Nusselt number and decreases the skin friction coefficient and the Sherwood number. In , increase in the values of Brownian motion parameter (Nb) decreases the skin friction coefficient, Nusselt number and Sherwood number. From , increase in the values of Schmidt number decreases the wall skin friction coefficient and the Nusselt number whereas increase in the Sherwood number is noticeable. In , it is noticed that increase in the non-Newtonian fluid parameter increases the Nusselt and Sherwood number but decreases the skin friction coefficient. and shows the comparison of the present results with previous published works and was found to be in good agreement.
Table 2. Computational values for skin friction coefficient Nusselt number
and sherwood number
for different values of Ln and M.
Table 3. Computational values for skin friction coefficient Nusselt number
and sherwood number
for different values of
and β.
Table 4. Comparison of the present result with that of Mondal et al. (Citation2018) when and at constant viscosity and thermal conductivity.
Table 5. Comparison of the present result with that of Rafique et al. (Citation2019) when and at constant viscosity and thermal conductivity.
5. Concluding remarks
This study examined the effects of thermophoresis and Soret-Dufour on heat and mass transfer mixed convective flow of MHD non-Newtonian nanofluid over an inclined plate embedded in a porous medium. The analysis for variable viscosity and thermal conductivity is considered. A parametric study on the velocity, temperature, and concentration. The flow equations were solved numerically using spectral homotopy analysis method. From the results obtained, increase in the non-Newtonian Casson fluid parameter brings increase to the skin friction coefficient and reduces the rate of heat and mass transfer. The results in the present study revealed that the behaviour of the non-Newtonian fluid parameter changes to Newtonian fluid as the Casson fluid parameter approaches infinity. Increase in the magnetic parameter (M) brings a decrease to velocity of the fluid. It is observed that increase in the magnetic parameter brings to the fluid concentration close to the plate and reduces the free stream at the porous medium. The present result gives account to the effect of radiation parameter and it is noticed that increase in radiation parameter gives rise to the fluid temperature and has no effect on the velocity. It is observed that increase in the Schmidt number gives rise to the concentration field at the free stream whereas it increase the fluid temperature close to the plate and reduces it at the free stream. The novelty of this paper the investigation of varying viscosity and thermal conductivity on the flow of Casson non-Newtonian fluid in a porous medium of an inclined plate. The result of this study will be of help in chemical engineering processes and the production of food.
The present study is useful in glass blowing process. In glass blowing process, maintaining the temperature for glass blowing is very important. This is because it requires optimal temperature to make it flexible for blow so as to obtain the required shape. Hence parameters such as thermal radiation and heat generation considered in this study are very important in glass blowing process. Also, at very high temperature the properties of fluid such as viscosity and thermal conductivity may vary. It is observed from this study that increase in viscosity brings decrease to the fluid flow. This allows us to be able to control the flow of the fluid. On the other hand, an increase in thermal conductivity gives rise to the fluid temperature in such a way that it conducts more heat. The use of thermal conductivity in regulating the conducting nature of heat of the fluid also helps in controlling the blowing glass substance temperature. The present study is very useful in many chemical engineering processes such as metallurgical and extrusion of polymer which involves cooling of molten liquid. The polyethylene oxide and polyisobutylene solution in cetane are having electromagnetic properties which are used as cooling liquids because they are regulated by external magnetic fields. Hence, controlling parameters such as thermal radiation, viscous dissipation parameter, magnetic field parameter, chemical reaction parameter etc. considered in this study finds application in chemical engineering processes.
Nomenclature | ||
w | = | velocity components along x-axis (m/s) |
n | = | velocity components along y-axis (m/s) |
g | = | acceleration due to gravity |
k | = | porosity term |
k(T) | = | thermal conductivity ( |
D | = | mass diffusivity |
B0 | = | magnetic field strength |
cp | = | specific heat at constant pressure (J/kgk) |
qr | = | heat flux ( |
DB | = | Brownian coefficient ( |
DT | = | thermophoresis coefficient ( |
kT | = | thermal diffusion ratio |
cs | = | concentration susceptivity |
kl | = | chemical reaction coefficient |
VT | = | thermophoretic velocity |
Sn | = | Schmidt number (dimensionless) |
Cp | = | chemical reaction parameter |
So | = | Soret number (dimensionless) |
Ln | = | Lewis number |
Sw | = | suction velocity (m / s) |
= | dynamic viscosity with respect to temperature (kg / ms) | |
= | volumetric coefficient of thermal expansion and concentration respectively | |
α | = | inclined angle (degree) |
θ | = | fluid temperature (K) |
= | concentration of the fluid | |
= | free stream temperature (K) | |
= | free stream concentration | |
σ | = | electrical conductivity |
ρ | = | fluid density ( |
ν | = | fluid density ( |
ψ | = | stream function ( |
η | = | independent similarity variable (dimensionless) |
θw | = | wall temperature (K) |
= | wall concentration | |
= | dimensionless temperature | |
= | dimensionless concentration |
Disclosure statement
No potential conflict of interest was reported by the authors.
References
- Abu-Nada, E., Hakan, F. O., & Pop, I. (2012). Buoyancy induced flow in a nanofluid filled enclosure partially exposed to forced convection. Superlattices and Microstructures, 51(3), 381–395. doi:10.1016/j.spmi.2012.01.002
- Ahmed, S. E., & Rashed, Z. Z. (2019). MHD natural convection in a heat generating porous medium-filled wavy enclosures using Buongiorno’s nanofluid model. Case Studies in Thermal Engineering, 14, 100430. doi:10.1016/j.csite.2019.100430
- Alam, M. S., Rahman, M. M., & Sattar, M. A. (2009). Transient magnetohydrodynamic free convective heat and mass transfer flow with thermophoresis past a radiate inclined permeable plate dependent viscosity. Nonlinear Analysis: Modelling and Control, 14(1), 3–20. doi:10.15388/NA.2009.14.1.14525
- Alao, F. I., Fagbade, A. I., & Falodun, B. O. (2016). Effects of thermal radiation, Soret and Dufour on an unsteady heat and mass transfer flow of a chemically reacting fluid past a semi-infinite vertical plate with viscous dissipation. Journal of the Nigerian Mathematical Society, 35(1), 142–158. doi:10.1016/j.jnnms.2016.01.002
- Amanulla, C. H., Saleem, S., Wakif, A., & AlQarni, M. M. (2019). MHD Prandtl fluid flow past an isothermal permeable sphere with slip effects. Case Studies in Thermal Engineering, 14, 100447. doi:10.1016/j.csite.2019.100447
- Animasaun, I. L., & Pop, I. (2017). Numerical exploration of a non-Newtonian Carreau fluid flow driven by catalytic surface reactions on an upper horizontal surface of a paraboloid of revolution, buoyancy and stretching at the free stream. Alexandria Engineering Journal, 56(4), 647–658. doi:10.1016/j.aej.2017.07.005
- Animasaun, I. L. (2015). Effects of thermophoresis, variable viscosity and thermal conductivity on free convective heat and mass transfer of non-Darcian MHD dissipative Casson fluid flow with suction and nth order of chemical reaction. Journal of the Nigerian Mathematical Society, 34 (1), 11–31. doi:10.1016/j.jnnms.2014.10.008
- Batchelor, G. K., & Shen, C. (1985). Thermophoretic deposition of particles in gas flowing over cold surfaces. Journal of Colloid and Interface Science, 107(1), 21–37. 10.1016/0021-9797. (85)90145-6 doi:10.1016/0021-9797(85)90145-6
- Choi, S. U. S. (2009). Nanofluids: From vision to reality through research. Journal of Heat Transfer, 131(3), 1–9. doi:10.1115/1.3056479
- Fagbade, A. I., Falodun, B. O., & Omowaye, A. J. (2018). MHD natural convection flow of viscoelastic fluid over an accelerating permeable surface with thermal radiation and heat source or sink: Spectral Homotopy Analysis Approach. Ain Shams Engineering Journal, 9(4), 1029–1041. doi:10.1016/j.asej.2016.04.021
- Gireesha, B. J., Ganesh Kumar, K., Ramesh, G. K., & Prasannakumara, B. C. (2018). Nonlinear convective heat and mass transfer of Oldroyd-B nanofluid over a stretching sheet in the presence of uniform heat source/sink. Results in Physics, 9, 1555–1563. doi:10.1016/j.rinp.2018.04.006
- Hayat, T., Waqas, M., Shehzad, S. A., & Alsaedi, A. (2016a). Mixed convection flow of a Burgers nanofluid in the presence of stratifications and heat generation/absorption. The European Physical Journal Plus, 131(8), 253. doi:10.1140/epjp/i2016-16253-9
- Hayat, T., Waqas, M., Shehzad, S. A., & Alsaedi, A. (2016b). On 2D stratified flow of an Oldroyd-B fluid with chemical reaction: An Application of non-Fourier heat flux theory. Journal of Molecular Liquids, 223, 566–571. doi:10.1016/j.molliq.2016.08.083
- Hayat, T., Zubair, M., Waqas, M., Alsaedi, A., & Ayub, M. (2017). On doubly stratified chemically reactive flow of Powell–Eyring liquid subject to non-Fourier heat flux theory. Results in Physics, 7, 99–106. doi:10.1016/j.rinp.2016.12.003
- Idowu, A. S., & Falodun, B. O. (2019). Soret–Dufour effects on MHD heat and mass transfer of Walter’s-B viscoelastic fluid over a semi-infinite vertical plate: Spectral relaxation analysis. Journal of Taibah University for Science, 13(1), 49–62. doi:10.1080/16583655.2018.1523527
- Khan, M. I., Waqas, M., Hayat, T., & Alsaedi, A. (2017). Soret and Dufour effects in stretching flow of Jeffrey fluid subject to Newtonian heat and mass conditions. Results in Physics, 7, 4183–4188. doi:10.1016/j.rinp.2017.10.011
- Latiff, N. A., Uddin, M. J., & Md. Ismail, M. I. (2016). Stefan blowing effect on bioconvective flow of nanofluid over a solid rotating stretchable disk. Propulsion and Power Research, 5(4), 267–278. doi:10.1016/j.jppr.2016.11.002
- Mahanthesh, B., Gireesha, B. J., & Gorla, R. S. R. (2016). Heat and mass transfer effects on the mixed convective flow of chemically reacting nanofluid past a moving/stationary vertical plate. Alexandria Engineering Journal, 55(1), 569–581. doi:10.1016/j.aej.2016.01.022
- Mondal, H., Mishra, S., Kundu, P. K., & Sibanda, P. (2020). Entropy generation of variable viscosity and thermal radiation on magneto nanofluid flow with dusty fluid. Journal of Applied and Computational Mechanics, 6(1), 171–182. doi:10.22055/JACM.2019.28273.1473
- Mondal, H., Pal, D., Chatterjee, S., & Sibanda, P. (2018). Thermophoresis and Soret-Dufour on MHD mixed convection mass transfer over an inclined plate with non-uniform heat source/sink and chemical reaction. Ain Shams Engineering Journal, 9(4), 2111–2121. doi:10.1016/j.asej.2016.10.015
- Naz, R., Noor, M., Hayat, T., Javed, M., & Alsaedi, A. (2020). Dynamism of magnetohydrodynamic cross nanofluid with particulars of entropy generation and gyrotactic motile microorganisms. International Communications in Heat and Mass Transfer, 110, 104431. doi:10.1016/j.icheatmasstransfer.2019.104431
- Omowaye, A. J., Fagbade, A. I., & Ajayi, A. O. (2015). Dufour and soret effects on steady MHD convective flow of a fluid in a porous medium with temperature dependent viscosity: Homotopy analysis approach. Journal of the Nigerian Mathematical Society, 34(3), 343–360. doi:10.1016/j.jnnms.2015.08.001
- Rafique, K., Anwar, M. I., Misiran, M., Khan, I., Alharbi, S. O., Thounthong, P., & Nisar, K. S. (2019). Numerical solution of Casson nanofluid flow over a non-linear inclined surface with Soret and Dufour effects by Keller-Box method. Frontier Physics, 7(139), 1-13. doi:10.3389/fphy.2019.00139
- Rajesh, V., Chamkha, A. J., & Mallesh, M. P. (2016). Transient MHD free convection flow and heat transfer of nanofluid past an impulsively started semi-infinite vertical plate. Journal of Applied Fluid Mechanics, 9(7), 2457–2467. doi:10.18869/acadpub.jafm.68.236.23443
- Ramana Reddy, J. V., Anantha Kumar, K., Sugunamma, V., & Sandeep, N. (2018). Effect of cross diffusion on MHD non-Newtonian fluids flow past a stretching sheet with non-uniform heat source/sink: A comparative study. Alexandria Engineering Journal, 57(3), 1829–1838. doi:10.1016/j.aej.2017.03.008
- Sibanda, P., Motsa, S. S., & Makukula, Z. G. (2012). A spectral-homotopy analysis method for heat transfer flow of a third grade fluid between parallel plates. International Journal of Numerical Methods for Heat & Fluid Flow, 22(1), 4–23. doi:10.1108/09615531211188766
- Talbot, L., Cheng, R. K., Schefer, R. W., & Willis, D. R. (1980). Thermophoresis of particles in a heated boundary layer. Journal of Fluid Mechanics, 101(4), 737–758. doi:10.1017/S0022112080001905
- Trefethen, L. N. (2000). Spectral Methods in MATLAB. Philadelphia: Society for Industrial and Applied Mathematics.
- Ullah, I., Shafie, S., Khan, I., & Hsiao, K. L. (2018). Brownian diffusion and thermophoresis mechanisms in Casson fluid over a moving wedge. Results in Physics, 9, 183–194. doi:10.1016/j.rinp.2018.02.021
- Ullah, N., Nadeem, S., Khan, A. U., Ul Haq, R., & Tlili, I. (2020). Influence of metallic nanoparticles in water driven along a wavy circular cylinder. Chinese Journal of Physics, 63(2020), 168–185. doi:10.1016/j.cjph.2019.11.012
- Waqas, M. (2020). A mathematical and computational framework for heat transfer analysis of ferromagnetic non-Newtonian liquid subjected to heterogeneous and homogeneous reactions. Journal of Magnetism and Magnetic Materials, 493(2020), 165646. doi:10.1016/j.jmmm.2019.165646
- Xu, H., & Liao, S. J. (2009). Laminar flow and heat transfer in the boundary-layer of non- Newtonian fluids over a stretching flat sheet. Computers & Mathematics with Applications, 57(9), 1425–1431. doi:10.1016/j.camwa.2009.01.029
- Zaigham Zia, Q. M., Ullah, I., Waqas, M., Alsaedi, A., & Hayat, T. (2018). Cross diffusion and exponential space dependent heat source impacts in radiated three-dimensional (3D) flow of Casson fluid by heated surface. Results in Physics, 8, 1275–1282. doi:10.1016/j.rinp.2018.01.001