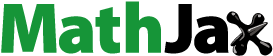
Abstract
In this paper, the primary synthesis and secondary treatment of Aluminium matrix composites (AMCs) has been reviewed. The renewed quest for component materials with high strength-to-weight ratio, unusual and superlative combination of properties for applications in automotive, aerospace, marine and warfare armoury manufacturing industries has increased the versatility potential of aluminium alloy-based composites. Several categories (synthetic and agro-based ceramics) of reinforcement materials for aluminium composite are discussed. The manufacturing/fabrication techniques which could be solid phase (powder metallurgy and rapid prototyping or 3 D printing method) or liquid phase (casting and pressure infiltration) methods are discussed in this review work. Secondary treatment such as heat treatment, forging and other thermomechanical treatments which improves the properties of as-synthesized composites are also discussed. A review synopsis of recent studies provides opportunity for concise but a more robust understanding of potential benefits and detrimental effects associated with the use of various primary synthesis routes and secondary treatment for manufacturing of ceramic reinforced AMCs. Despite the laudable research efforts that have been made towards development and enhancement of the properties of AMCs, this review work revealed that literature is very sparse on synergetic adoption of multi-synthesis route and multi-approach secondary treatment for producing AMCs. Sequel to the aforementioned unexplored research concept, some lacunae are identified and suggested for further elaborations and study.
1. Introduction
Rising demand for structural components with increased service duration, improved in-service performance, high strength to weight ratio and affordable cost implications has led to the synthesis of new materials such as composites. Composites are formed by combining at least two different chemical materials with different interphase separating the constituents in a three-dimensional form to obtain improved properties which are different from those of the parent materials (Chin, Koav, Chan, Yeow, & Pang, Citation2020; Gupta & Srivastava, Citation2018; Kale, Citation2015; Kumar & Rai, Citation2018; Obande, Mamalis, Ray, Yang, & O’Bradaigh, Citation2019; Varvani-Farahani, Citation2010). The increased use of these materials is a function of their mechanical properties which in turn have enormous influence on the vastness of their areas of applications (Aweda, Orhadahwe, & Ohijeagbon, Citation2018; Hussain, Khan, & Sarmah, Citation2020; Kahlani & Jafarzadeh, Citation2020; Kim et al., Citation2020; Orhadahwe, Adeleke, Aweda, Ikubanni, & Jamiu, Citation2020; Veličković, Garić, Stojanović, & Vencl, Citation2016).
Aluminium alloys are used massively in the production of metal matrix composites (MMCs) owing to their unique properties. These properties include high strength, low density, good wear response, fatigue resistance, good thermal conductivity, corrosion resistance, recyclability, relatively low cost of production, and ease to be shaped, rolled, drawn, extruded and welded (Gowrishankar, Manjunatha, & Sangmesh, Citation2019; Keshavamurthy, Sudhan, Gowda, & Krishna, Citation2016; Veličković et al., Citation2016). Metal matrix composites (MMCs) are materials produced by the reinforcement of metals with other metals, ceramic or compounds of organic materials. The reinforcement material is dispersed in the matrix of the base metal. The addition of reinforcement is aimed at improving the material’s integrity in terms of its mechanical and microstructural properties (Ramnath et al., Citation2014). Aluminium composites gain application in aviation and aerospace technology, automobile technology, armament industry, electrical and electronic engineering among others (Dobrzanski, Kremzer, & Adamiak, Citation2008). Specifically, they are used industrially in the manufacture of engine blocks, cylinder liners, connecting rods crankshafts, cardan shafts, propellers of helicopters, brake discs and drums of cars and trains (Veličković et al., Citation2016).
A special class of composites is nanocomposites. Nano composites are composites which have a minimum of one of the constituents existing as nanometre particles (1 nm or 10−9 m). Nanocomposites materials are reliable alternatives that can overcome the setbacks of micro-composites and monolithic. They have been viewed as the 21st century materials because they possess design uniqueness and a combinations of properties which are not found in conventional composites (Camargo, Satyanarayana, & Wypych, Citation2009; El-Labban, Abdelaziz, & Mahmoud, Citation2014). Nanocomposites can be categorized based on their constituent materials into three different groups; metal, ceramic and polymer nanocomposites. Examples of metal matrix nanocomposites include Fe-Cr/Al2O3, Ni/Al2O3, Co/Cr, Fe/MgO, and Al/CNT (Camargo et al., Citation2009). Metal matrix nanocomposites are materials that comprise ductile metal or alloy in which some nano-sized reinforcement materials are implanted so as to improve ductility, toughness, high strength and modulus. Metal matrix nanocomposites gain application in the synthesis of materials with high strength suitable for shear and compression processes and high service temperature environments. They are specifically useful in aeronautic and automotive industries as well as in the development of structural materials (Tjong, Wang, Geng, & Mai, Citation2004; Tjong, Wang, and Mai, Citation2005).
There are various reinforcement materials which are added in the form of particles, whiskers or fibres at varying quantities to the base aluminium metal to improve its properties. Such reinforcement materials include; silicon carbide, alumina (Al2O3), silicon nitride (Si3N4), titanium dioxide (TiO2), boron carbide (B4C), fibres, fly ash, zircon (Stojanovic et al., Citation2013). Silicon carbide is one of the widely used reinforcement materials as it improves the tensile strength, hardness, density and wear resistance of aluminium (Ramnath et al., Citation2014). Reinforcement using alumina improves the compressive strength and wear resistance of aluminium and its alloys while B4C reinforcement yields high elastic modulus and fracture toughness but with insignificant improvement in the wear resistance (Ipekoglu, Nekouyan, Albayrak, & Altintas, Citation2017; Khodabakhshi, Gerlich, & Worswick, Citation2018; Kishore Babu et al., Citation2017; Nanjan & Janakiram, Citation2019; Palanikumar, Rajkumar, & Pitchandi, Citation2019; Tiku, Navin, & Kurchania, Citation2020). The use of fibres as reinforcement materials improves the strength and other properties of the aluminium. The use of fly ash is gaining wide acceptance due to its low cost and availability. Fly ash is obtained as a by-product from the waste of thermal power plants. Its addition as reinforcement material enhances the electromagnetic shielding capacity of aluminium based composites (Ramnath et al., Citation2014).
Aluminium metal matrix nanocomposites can be fabricated using different methods which include powder metallurgy, stir casting, squeeze casting, co-spray deposition process, pressure infiltration, vacuum hot pressing, and 3 D printing (Babalola, Bolu, Inegbenebor, & Odunfa, Citation2014). This paper reviews the different types of aluminium composites, fabrication techniques and post fabrication treatment of aluminium composites, with special emphasis on nanocomposites and secondary treatment.
2. Category of reinforcement materials for aluminium composites
The Reinforcement Materials can further be divided into synthetic ceramic reinforcements, agro waste ceramic reinforcements, hybrid and other reinforcements (synthetic fibres, natural fibres, and so on).
2.1. Synthetic ceramic reinforcements
2.1.1. Silicon carbide
Research has shown that addition of a high amount of silicon carbide (SiC) to the base aluminium matrix helps in preventing the formation of aluminium carbide (Al4C3) which has detrimental impact on the mechanical properties (Manfredi et al., Citation2014). In a similar study, Ghosh and Saha (Citation2011) observed that the particle size of SiC is vital to the composite integrity, positing that specific wear rate of aluminium-based composites is reduced as the size of SiC particles increases. Also, the volume of SiC added to the matrix should be limited to 15% to inhibit excessive crack formation. This view was coroborated by Naveen and Ramesh (Citation2014) who discovered that increase in the amount of SiC in Al6061 alloy led to a reduction of the wear rate and increased friction coefficient. Veličković et al. (Citation2019) optimized the wear rate parameters of aluminium based nanocomposites. The reinforcement material comprised SiC nanoparticles which were added in varying proportion of 0.2, 0.3 and 0.5 wt%. The analyses of the findings depicted that the amount of SiC particles added ranked the second most influential parameter to be optimized so as to minimize the wear rate of A356 aluminium alloy.
2.1.2. Alumina
Aluminium oxide also known as alumina is one of the commonly used reinforcement materials in the fabrication of AMCs. It is specifically known for its strong ionic inter-atomic bonding which produces desirable properties. It is the strongest and stiffest ceramic oxide with excellent size and shape capabilities. It is also the most corrosion resistant material known. It is hard and possess good wear resistance. Compared to aluminium alloy, alumina possesses greater specific density value (Ekambaram & Murugan, Citation2015; Kok, Citation2005). Ekambaram and Murugan (Citation2015) produced AMCs with 4, 6 and 8% alumina through stir casting and observed that the composites had fewer casting defects when compared to the aluminium alloy.The composites also showed better wettability. Also, the influence of using Al2O3 as a ceramic reinforcement material on the mechanical properties of Al7072 alloy composites has been examined (Kumar & Venkatesh, Citation2018). The study revealed that breaking strength, compressive strength, hardness, ductility and lightness properties of the composites improved remarkably.
2.1.3. Boron carbide
The use of boron carbide (B4C) as reinforcement material in AMCs have been shown to exhibit remarkable tensile strength, wear resistance, high hardness, good structural rigidity and low density (Kumar & Rai, Citation2018; Kummari & Paramesh, Citation2019; Ravi, Balu, & Uday, Citation2016). For instance, Gomez, Busquets-Mataix, Amigo, and Salvador (Citation2009) studied the mechanical and tribological properties of B4C reinforced aluminium alloy composites and compared with that of monolithic alloy and SiC reinforced. Although there was a decrease in wear rate, B4C reinforced aluminium alloy composites at 10 wt.% B4C exhibited better hardness, strength and dynamic friction coefficient when compared with either unreinforced aluminium alloy or SiC reinforced composites. In the work of Gopal, Sreenivas, and Vasudeva (Citation2013), 6061Al matrix was reinforced with B4C particles of 3,74,46,31,05,250 μm sizes using liquid metallurgy technique. The tensile strength and hardness of the 6061 Al- B4C composites were found to increase with the increase in the particle size. The authors’ study enriched literature on the crucial role of particle size of ceramic reinforcement materials in properties modification of aluminium alloy composites. An investigation of the physico-mechanical properties of aluminium based composites reinforced with B4C has been carried out (Shirvanimoghaddam et al., Citation2016). The authors found that Al-B4C composites exhibited improvement in tensile strength and Vickers hardness properties in comparison with the monolithic aluminium alloy. It was however reported that a substantial decrease in tensile strength and Vickers hardness behaviours of the composites was observed at higher volume fraction of B4C particles. The authors attributed this observation as an aftermath effect of using B4C reinforcement particles in the composite beyond 15 vol.%, thus promoting particle agglomeration, which is then rejected from molten metal to form slag.
2.1.4. Fly ash
Fly ash is one of the by-products of coal combustion usually produced in millions of tonnes yearly and at relatively low costs. Incorporating fly ash as a reinforcement material in aluminium based composites can reduce the cost of production. Aside this, fly ash is known for its high electrical resistivity, low thermal conductivity and low density which are very useful properties to be considered when fabricating light weight insulator composites. Its addition to aluminium matrix has been found to improve the material integrity by reducing density, increasing hardness, stiffness, wear and abrasion resistance. In addition, the machinability, damping capacity and coefficient of friction of the composite will be improved thereby making it adaptable to the automotive industry (Awotunde et al., Citation2019; Kumar & Theerthan, Citation2008; Ramnath et al., Citation2014).
2.2. Agro-Waste-based ceramic reinforcements
The use of agro-waste in the production of engineering materials is gaining wide acceptance due to its low cost, availability and the enormous advantage of reducing the rate of environmental pollution (Alaneme, Eze, & Bodunrin, Citation2015; Joseph & Babaremu, Citation2019). The use of ash sourced from agro waste such as rice husk, groundnut shell, bamboo leaf, coconut shell, sugarcane bagasse, corn cob, palm kernel and periwinkle shell have been identified as suitable ceramic reinforcement materials for synthesizing AMCs (Alaneme, Bodunrin, & Awe, Citation2018; Joseph & Babaremu, Citation2019; Kulkarni, Siddeswarappa, & Kumar, Citation2019). The authors reported that the ash forms of the mentioned agro wastes are rich in silicon and magnesium and could be deployed as reinforcement materials in AMCs. Ebrahimi, Konaganti, Moradi, Doufas, and Hatzikiriakos (Citation2016) produced an Al1100 composite reinforced with Coconut Shell Ash (CSA) of size 60 µm by the method of compo-casting. It was discovered that the composite’s density was less than that of the Al alloy but the composite exhibited higher hardness compared to the Al alloy. This was attributed to the presence of SiO2 and MgO in the CSA reinforcement material. Lakshmi, Subbaiah, Sarojini, and Shabana (Citation2017) used sugarcane bagasse ash as the reinforcement particle for Al6061. The study revealed that there was an increase in mechanical and wear resistance. The fabricated AMCs also experienced better corrosion wear resistance for 0-1.5 wt% sugarcane bagasse ash addition. The addition of more SCBA produced a decrease in the ability of the composite to withstand corrosion. Mangalore et al. (Citation2019) carried a study on tribological behaviour of CSA reinforced Al 7079 matrix composites. Results obtained showed remarkable reduction in wear rate as well as improvement in hardness and tensile strength properties. Other forms of agro wastes for AMCs have also been documented (Arora & Sharma, Citation2018; Donald et al., Citation2018; Krushna, Shekhar, & Kumar, Citation2019; Rozhbiany & Jalal, Citation2019; Yekinni et al., Citation2019).
2.3. Hybrid and other reinforcement materials
El-Labban et al. (Citation2014) produced aluminium alloy-based nanocomposite by the addition of Al-Ti5-B1 master alloy to the matrix melt using mechanical stirring and squeeze casting. The percentage of the reinforcement material was varied from 1-3% and the as-produced composite was characterized using Scanning Electron Microscope (SEM), EnergyDispersive X-ray (EDX) and X-ray Diffraction (XRD) analyzers and Vicker microhardness test. The results showed that the addition of the master alloy led to a remarkable reduction in the matrix grain size. There was also an increase in hardness as the percentage of Al-Ti5-B1 increased from 1-3%. There are so many other reinforcement materials found in literature such as barium carbide, hematite, multiwalled carbon nanotubes among others (Hussain, Khan, Chanda, & Jangid, Citation2017; Ikubanni et al., Citation2020; Ipekoglu et al., Citation2017; Saravanakumar et al., Citation2014; Ozer, Citation2016). Some researchers combined two or more reinforcement materials to form hybrid reinforced aluminium composite. Alaneme et al. (Citation2015) combined groundnut shell ash and silicon carbide as reinforcements of Al-Mg-Si alloy and investigated the corrosion resistant property of the composite in 3.5% NaCl and 0.3 M H2SO4. The result revealed that as the proportion of groundnut shell ash increased, the corrosion property of the composite increased.
In the work of Canute and Majumder (Citation2018), hybrid Al/B4C/Fly ash composites were synthesized using stir casting technique. The authors examined mechanical and tribological properties of the produced composites. The results obtained revealed a superior mechanical property (hardness, tensile and compressive strengths) and resistance to wear when compared with the monolithic aluminium alloy and mono-ceramic reinforced type composites. Interestingly, the inclusion of strontium master alloy in the composites was able to refine its grain structure. Furthermore, the inclusion of potassium flurotitanate (K2TiF6) enhances bonding characteristics of the major ceramic reinforcements (boron carbide and fly ash particles) with aluminium alloy matrix was improved. The use of magnesium powder and K2TiF6 have also been reported to promote wettability and bonding characteristics in AMCs (Canute & Majumder, Citation2018; Dhinakaran & Moorthy, Citation2014). Fabrication of hybrid AMCs with varying compositions of silicon carbide and boron carbide was carried out by Reddy, Kesavan, and Vijaya Ramnath (Citation2018). The study revealed that the hybrid 6061 Al-SiC-B4C composites have better mechanical properties when compared with either unreinforced 6061 Al or a mono-ceramic particle reinforced composite. The author reported that 6061 Al-2% SiC-2% B4C has higher tensile, flexural strengths and hardness compared to the unreinforced 6061 Al. The general improvement in mechanical strength was adduced to the formation of high fraction of carbides in the composites. Mohanavel, Rajan, Suresh Kumar, Vijayan, and Vijayanand (Citation2018) characterised AA6351 matrix composites reinforced with graphite particulates via liquid metallurgy method. The mass fraction of reinforcement was varied from 0 to 12%. The study showed that the mechanical properties of the composite experienced a substantial decrease as the volume fraction of graphite particle increases. This was attributed to poor interfacial bonding that existed between the constituents of the composites. It was asserted that the brittle nature of the reinforcement particles such as graphite could have detrimental impact on the mechanical characteristics of AMCs strengthened by the inclusion of graphite particles.
Furthermore, Pugalenthi, Jayaraman, and Subburam (Citation2019) examined the microstructural and mechanical behaviours of aluminium hybrid composite consisting of SiC and Al2O3. The outcome of the study revealed that increasing the percentage weight of the reinforcement materials led to higher hardness, tensile and yield strengths of the composite. Palanikumar et al. (Citation2019) combined B4C (primary reinforcement) and Mica (secondary reinforcement) particles and reported an increase in wear strength of the hybrid when compared with the composite produced by only the primary reinforcement. The use of titanium diboride for grain refinement (Xi et al., Citation2020) as well as carbides, nitrides, compounds of oxides, organic, inorganic, and industrial waste sourced form of reinforcement particles at micrometres and nanometres sizes for remarkable improvement in properties of AMCs have also been documented (Chen et al., Citation2020; Ma et al., Citation2016; Tiku et al., Citation2020). Several other studies have also reported the use of hybrid and other forms of reinforcement particles in the synthesis of AMCs (Arora & Sharma, Citation2018; Gowrishankar et al., Citation2019; Krushna et al., Citation2019; Nanjan & Janakiram, Citation2019; Patel, Kumar, Sahu, & Singh, Citation2020; Radhika, Subramanian, Venkat Prasat, & Anandavel, Citation2012; Rozhbiany & Jalal, Citation2019).
3. Fabrication techniques
From literature, composites can be manufactured by solid or liquid phase methods. Solid phase fabrication includes powder metallurgy, diffusion bonding and direct metal layer sintering (Rapid Prototyping or 3 D method). Liquid phase methods include; squeeze casting, stir casting, pressure infiltration, spray deposition and in-situ reaction synthesis (Goyal & Marwaha, Citation2016).
3.1. Powder metallurgy
The use of solid-state processes (powder metallurgy and extrusion) for producing aluminium matrix composites has been studied by several researchers (Chen et al., Citation2020; Gomez et al., Citation2009; Wąsik, Leszczyńska-Madej, Madej, & Goły, Citation2020). Powder metallurgy process involves the mixing, degassing and sintering of metal alloy and the reinforcements (Awotunde et al., Citation2019; Muni et al., Citation2019; Goyal & Marwaha, Citation2016; Hussain et al., Citation2017; Liu, Zhang, Gou, & Ding, Citation2017). The use of powder metallurgy as a fabrication process in the production of aluminium composite enhances easy control of material properties. For instance, the use of extrusion process makes fabrication of products with various geometries (such as solid and hollow profiles) seamless, which is an evidence of properties variation along their axis owing to the different degree of deformation during extrusion (Dobrzanski et al., Citation2008). With powder metallurgy, it is possible to manufacture near net shape even for small elements. This method was used by Dobrzanski et al. (Citation2008) in the fabrication of EN AW-AlCu4Mg1(A) and Al2O3 particles composite. Consolidation was done by wet mixing the powders into slurry using methanol in a ball mill so as to derive uniform deformation of reinforcement particles in the metal matrix. The powders were air dried and subjected to cold state compaction in a die which unidirectional pressure was set at 350 kN. The compacted powders were heated to 500 and then extruded with a pressure of 500 kN. Product characterization was by metallographic examination using a LEICA MEF4A light microscope. The specimen was viewed along the longitudinal direction through which it was extruded. The metallographic examination depicted even dispersal of reinforcement particles in the matrix of the metal. It was also pointed out that there was banding of the reinforcement particles parallel to the extrusion direction. However, agglomeration of reinforcement particles due to poor intermixing and small deformations as a result of extrusion was noticed. Similarly, Kallip et al. (Citation2017) synthesized aluminium nanocomposite using high energy cube milling and hot-pressing process. The base alloy was AlMg5 and nano-sized alumina particles were used as the reinforcement material with its volume varying from 1 to 4%. The reinforcement and the powdered based alloy were mixed using the high energy cube mill and the milled powders were then hot-pressed for compaction at 595 MPa. The synthesized composites were characterized by optical microscopy, SEM, Vickers microhardness test and Differential Thermal Analyses (DTA). The results of the study further validated the use of powder metallurgy for the production of near net shapes. The use of high energy cube milling proved to be more efficient than the conventional planetary ball milling process in that a greater impact force is generated when milling ball hits flat surfaces than when it hits round surfaces. The major drawback from the study was that compacting at high temperature could result in the formation of galvanic corrosion and this seemed to be unavoidable. Hatti, Murthy, and Somanakatti (Citation2019) fabricated aluminium/carbon nanotube composite using two different ball materials (tungsten and aluminium oxide) in a planetary ball milling process. The milled powder was compacted in a die and sintered in a microwave. It was observed that the alumina ball-milled samples exhibited higher hardness values. The study did not explain the reason for this variation. B4C particles were incorporated in Al6061 matrix by powder processing (Khan, Syed, Ud-Din, Akhtar, & Aune, Citation2019) via Spark Plasma Sintering (SPS). It was shown that hardness, compressive strength, ductility and relative density of the Al6061 based composites processed via SPS exhibited remarkable enhancement. This may result from the attainment of uniform distribution of B4C particles in Al6061. This fabrication technique provides dislocations peening leading to strengthening in the composite matrix.
3.2. Casting
Casting is a liquid state method of fabrication which involves the addition of a dispersed phase of the reinforcement material into the molten phase of the base metal and then the mixture is left to solidify. There are different casting techniques for producing nano-metal composites and include stir casting, squeeze casting, compocasting, centrifugal casting and friction casting (Ebhota & Jen, Citation2018). Stir casting has been reported as the most cost effective and simplest method of liquid state fabrication. The method involves the mechanical stirring of the mixture of the dispersed phase and molten phase to achieve homogeneity. The liquid composite is then cast using any suitable conventinal casting technique (Kumar & Theerthan, Citation2008). The content of the dispersed phase in stir casting is usually limited to a certain volume (in most cases, not more than 30%). The aim of stirring is to achieve homogenous distribution of the dispersed phase in the molten matrix but usually, this is not so due to formation of clusters by the dispersed particles and the difference in densities of the dispersed and molten phases (Kumar & Theerthan, Citation2008). This method of production was also adopted in the study carried out by Jims John Wessley, Srinivas, and Ali (Citation2019) as illustrated in . The apparatus consists of a motor (a) which turns a rotor (f). The melt (e) is placed in a crucible (d) in the furnace (c). The reinforcement (b) is introduced into the melt while the rotor spins at predefined speed to form a uniform mix of the materials. One of the drawbacks of stir casting is the improper wetting of reinforcement particles. It is on this basis that some researchers have either adopted squeeze casting technique as is in Etter et al. (Citation2004) or a combined process of stir and squeeze casting as in El-Labban et al. (Citation2014). Squeeze casting technique, entails the solidification of liquid-metal under pressure in a closed die (Ebhota & Jen, Citation2018). Squeeze casting enhances densification and mechanical properties of metal composites (Ipekoglu et al., Citation2017; Soundararajan, Ramesh, Sivasankaran, & Vignesh, Citation2017).
Figure 1. Schematic for the apparatus for stir casting; a- motor, b-reinforcement, c – furnace, d – crucible, e – melt, f – rotor (Singla, Rana, & Lata, Citation2017).
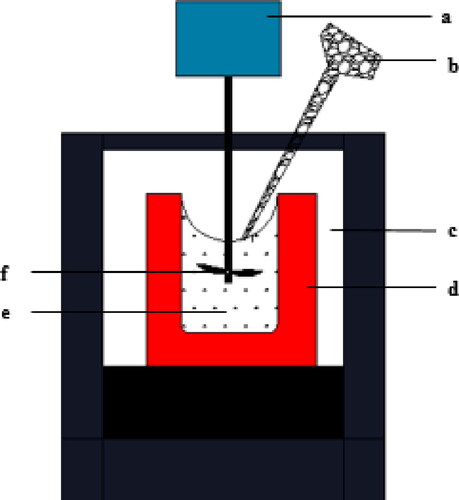
In attempt to ameliorate the problem of agglomeration often associated with conventional casting approach, Barekar et al. (Citation2009) adopted a melt conditioned high-pressure die casting (MC-HPDC) method. The authors observed a proper distribution of particles owing to high-shear dispersive mixing action of a twin-screw mechanism associated with this MC-HPDC technique. The aftermath effects of this uniform distribution of particles are strong interfacial bond, improved ultimate tensile strength and tensile elongation in comparison with composites synthesized via the traditional casting processes. Another casting technique with reported economic benefits is compocasting. Veličković et al. (Citation2019) deployed compocasting technique in the production of aluminium nanocomposites comprising A 356 aluminium based alloy and nanosized silicon carbide reinforcement particles.
3.3. 3D Printing (direct metal layer sintering)
3D printing which is also referred to as additive manufacturing (AM) or rapid prototyping is an emerging technology that has the potential to recalibrate the concept of manufacturing globally from the usual mass production in factories to a new order of mass customization of products (Manfredi et al., Citation2014). AM technology can be applied at any stage in a product life cycle. Manfredi et al. (Citation2014) used the method of Direct Metal Laser Sintering (DMLS) which is a rapid prototyping process in producing AMCs and posited that the alloys and composites fabricated by this technique provides ultra-fine microstructures due to very fast cooling which occurs after the laser induced melting. The resultant mechanical properties are also improved when compared to the conventional casting processes. As illustrated in , Ghosh and Saha (Citation2011) deployed DMLS in the production of SiC particulate reinforced aluminium based metal matrix composite. The process involved first preparing the powders to be sintered, in this case, the powders were Al (44 µm), Cu (44 µm), Mg (44 µm) and SiC (varying particle sizes). The powders were aligned in their different fractions and were deposited by an aluminium substrate in an argon gas chamber, where the gas was supplied constantly via the nozzle of a laser to fuse the particles together. The bed of the CNC machine was moved horizontally after the laser has fired a particular spot. After the consolidation of one layer, a new layer of powder was applied. The process was repeated until the entire cross section has been fabricated. Pertinent among the findings was that the fabricated composites had cracks which the authors attributed to thermal stress and contraction stress due to rapid solidification during laser sintering. However, Marchese et al. (Citation2018) highlighted the need to critically elucidate the consequence of combining different parameters involved in the process of densification of powders to inhibit crack formation on the produced composites. Xi et al. (Citation2020) attempted the use of selective laser melting for the development of titanium diboride (TiB2) reinforced AMCs. The study revealed emergence of fine equiaxed grains with narrow size distribution at high volume fraction of TiB2 particles thus, leading to significant improvement in the tensile strength, yield strength and microhardness properties of the developed AMCs. This study is a further testimony on the enormous properties’ enhancement benefits in the use of additive manufacturing routes, a 3 D printing based method for synthesis of AMCs.
Figure 2. Schematic of inert gas chamber for DMLS process; a: laser head, b:quartz window, c: laser chamber, d: laser beam, e: substrate, f: substrate holder, g: x-y table, i: base of chamber and h: entry of argon gas (Ghosh & Saha, Citation2011).
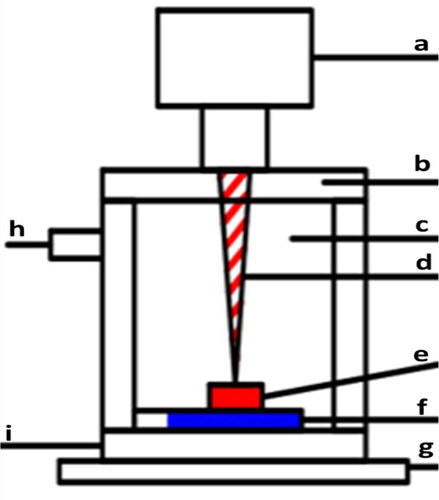
3.4. Pressure infiltration method
It is possible to manufacture a wide range of products from materials reinforced locally with near net shapes and good surface finish (Dobrzanski et al., Citation2008). The process however, consumes a lot of energy but can be adapted for mass scale production. The use of pressure infiltration process in the manufacture of metal matrix composite involves first preforming the reinforcement material using sintering. The quality of this preform may determine the quality and properties of the finished product. The major property to be considered during preforming is porosity. The pores allow the liquid metal to flow easily and can be improved by adding pore forming agent during sintering. After preforming, the preformed reinforcement material is then heated to about 800 °C and the liquid metal is introduced into the furnace containing the preform and then the whole setup is subjected to infiltration pressure of about 100 MPa for about 120 s using a hydraulic press (Dobrzanski et al., Citation2008). It can be asserted therefore, that the process of pressure infiltration combines powder metallurgy and casting. Etter et al. (Citation2004) also used this process in the production of graphite/aluminium composites. The process involved the infiltration o
f the aluminium alloys with varying silicon content into porous graphite preforms by gas pressure. The preforms were then heated with aluminium in an autoclave under a vacuum pressure of 30 Pa until 750 °C. The liquid metal was pressed into the preform by inert gas at about 8 MPa.
4. Secondary treatment
The essence of secondary treatment is to improve the properties of the as-synthesized composites (Goyal & Marwaha, Citation2016). Heat treatment has been reported to be combined alongside with other mechanical processing like forging and rolling. Keshavamurthy et al. (Citation2016) combined forging and heat treatment of Si3N4 reinforced Al6061 composite and reported a furtherance of the mechanical properties. This process is referred to as thermo-mechanical processing (Rofman, Mikhaylovskaya, Kotov, Prosviryakov, & Portnoy, Citation2019).
4.1. Heat treatment
It has been assured from research that heat treatment result in the improvement of the mechanical and microstructural characteristics of materials (Aweda et al., Citation2018; Orhadahwe, Adeleke, Aweda, et al., Citation2020; Soni & Pandey, Citation2014). Soni and Pandey (Citation2014) investigated the impact of heat treating on the mechanical and structural properties of Al-Si composite. The composites synthesized by stir casting were reheated to various temperatures; 135, 150, 175, 200 and 240 °C for 6 hours and then air cooled. The tensile strength, proof strength and fracture behaviours were observed. It was revealed that heat treatment produced good bonding of the interface connecting SiC particles and Al matrix thereby leading to improved mechanical properties. Ageing is a form of heat treatment that involves the transformation of the physical properties of metals over time due to environmental conditions. Usually the surface texture and colour of the metal changes due to the formation of hydroxide layer which then reacts with other elements in the environment and the metal surface attains a stable mineral composition which becomes resistant to any other alteration. Ageing can be natural (when it occurs at room temperature) or artificial (treatment at elevated temperatures to accelerate ageing). Chen and Lin (Citation2017) investigated the ageing behaviour of Al6061 composites reinforced with Y2O3 and TiC using metal consolidation and sintering. Ageing treatment was done by first subjecting the composites to solution treatment at 550 °C for 2 h and quenching in water to room temperature. Both natural aging at room temperature and artificial ageing at 160 °C in an oil bath were carried out. The study marked that the inclusion of reinforcement particles resulted in faster ageing and the aged composites exhibited higher hardness values as compared to those of the alloy. Natural ageing hardness value was only 5% better than those of artificially ageing.
4.2. Forging
Forging is the process whereby metals are shaped by the use of compressive forces. Such compressive forces are usually delivered with the use of a hammer or a die. Forging is classified based on the temperature within which it was done as cold, warm or hot forging (Narayan & Rajeshkannan, Citation2017). Warm forging and hot forging require heating the metal while the compressive forces are applied. Keshavamurthy et al. (Citation2016) subjected Al6061-10wt%Si3N4 composite manufactured by stir casting to forging at 500 °C. The samples were then heat treated. Metallographic examination using SEM showed that the Si3N4 powder aligned along the path of metal flow during forging. The microhardness results revealed that the hardness value of the forged composite was 7% higher than that of the as cast composite.
4.3. Other thermomechanical treatments
Thermomechanical processing includes hot rolling, multi-directional forging, cryorolling, equal angular channel pressing and high-pressure torsion among others. Lokesh, Ramachandra, and Mahendra (Citation2014) measured the impact of hot rolling on mechanical and tribological behaviours of Al4.5Cu based composite reinforced with fly ash. The observation of the characterised samples manifested a substantial enhancement in resistance to porosity, wear resistance, tensile strength and hardness as rolling reduction increases from 20 to 80%. The aforementioned improvement properties were adduced to even dispersion of fly ash particles and grain structure refinement as percentage rolling reduction increases. In Hanamantraygouda and Shivakumar (Citation2015), Al-SiC based composites subjected to hot forging at a temperature of 450 °C and aged at T6 conditions were examined. It was shown that the treated Al-SiC based composites exhibited improved tensile strength, compressive strength and hardness properties although with insignificant detrimental effect on ductility. It can be inferred from the author’s work that the use of hot forging yielded recrystallization and grain refinement. The influential effects of this grain refinement led to the general advancement of the mechanical properties of Al-SiC composites. The potential of forging and heat treatment for enhancing tribological characteristics of AMCs was investigated by Keshavamurthy et al. (Citation2016). The study revealed significant enhancement in hardness, friction and wear properties of hot forged and heat-treated Al-SiC based composites. The improvement in properties was attributed to thorough allocation of reinforcement particles in the microstructure and this was in turn associated with the synergestic effect of dual treatment (hot forging and heat treatment).
Ozer (Citation2016) subjected Al-15Si-2.5Cu-0.5 Mg/(wt.%) B4C composites synthesized by hot pressing and hot extrusion. The author reported a reduction in the grain size of samples subjected to secondary treatment. Some researchers use thermomechanical processes as fabrication routes (Khodabakhshi et al., Citation2018) or as thermomechanical treatment for ameliorating detrimental defects inherent in as-synthesized composites (Hussain, Rao, Singh, & Jayaganthan, Citation2018; Jaseem et al., Citation2018; Joshi, Yogesha, Kumar, & Jayaganthan, Citation2016; Kishchik et al., Citation2018). There are some studies where thermomechanical treatment was deployed as secondary treatment for other composites. Zhang et al. (Liu et al., Citation2017) deployed multi-directional forging as secondary treatment of TiBw/TA15 composites produced through powder metallurgy. Similarly, Anjan and Kumar (Citation2018) subjected ZA27 reinforced by SiC composites which were produced through stir and squeeze casting routes to multidirectional forging. However, limited studies exist on the use of thermomechanical treatment processes (such as cryorolling, multidirectional processing and other SPD processes) as secondary treatment of AMCs. Among the existing limited studies on the use of thermomechanical treatment are the works of Zeng, Chao, Luo, Cai, and Song (Citation2018), Bembalge and Panigrahi (Citation2018), Hussain et al. (Citation2018), Bembalge and Panigrahi (Citation2019), Vandersluis et al. (Citation2020) and Wąsik et al. (Citation2020).
Zeng et al. (Citation2018) subjected ZrB2p/6061Al composites produced by casting to multidirectional forging and heat treatment and observed an improvement in the mechanical properties. The procedure for cryorolling is as contained in Bembalge and Panigrahi (Citation2018) and the impact on the microstructural and mechanical properties were discussed in Bembalge and Panigrahi (Citation2019). Cryorolling can be used to transform as cast billet into useable rod-forms while imparting the properties positively (Hussain et al., Citation2018). Wąsik et al. (Citation2020) examined the impact of solution treatment on sintered Al4Cu-SiC composites. The composites were subjected to solution treatment for 6 h first at 495 °C and later at 530 °C. Each of the composites subjected to the two different temperatures were thereafter aged at 180 °C for various ageing periods. It was discovered that increase in the solid-solution temperature leads to reduction in the time to reach peak hardness. The highest increment in microhardness by ageing treatment was recorded for Al4Cu-5SiC composite which was subjected to solution treatment at 530 °C for 12 h. The adopted solution treatment might have caused the emergence of Al2Cu strengthening phase and attainment of uniform distribution of particles in the composite’s matrix. In the work of Vandersluis et al. (Citation2020) where the synergetic use of hot isostatic pressing (HIP) treatment and heat treatment at 2 h and temperature of 500 °C for enhancing mechanical and conductivity properties of low-pressure die-cast 319 Al alloy can equally be extended to its composite’s form. The attainment of enhanced properties in the study was attributed to dissolution of Al2Cu and silicon spheroidization.in the matrix. Others treatments have also been reported (Krushna et al., Citation2019; Reddappa et al., Citation2020; Yuen, Lee, & Ralph, Citation1995; McWilliams, Sano, Yu, Gordon, & Yen, Citation2013). Summary of review of AMCs production routes and treatment from Literature is provided in .
Table 1. Summary of review of AMCs production routes and treatment from literature.
5. Synopsis of selected results and discussion from literature
Aluminium matrix composites have gained huge industrial use over the years. They have been deployed in the fabrication of diverse automotive components such as brakes, engine blocks, drive shafts, piston cylinders and snow stud wheels. This can be attributed to their enormous qualities which differ greatly from those of aluminium. Despite the fact that aluminium has light weight, it possesses low strength and low melting point which makes it unfit in areas of applications where high strength is needed (Bahrami, Soltani, Pech-Canul, & Gutiérrez, Citation2016; Kulkarni et al., Citation2019). Research has shown that AMCs possess high specific strength, yield strength and ultimate tensile strength. Other properties include; increased corrosion resistance, low wear rate, increased coefficient of friction, increased hardness, improved weldability, and high strength to volume ratio (Al-Fadhalah, Almazrouee, & Aloraier, Citation2014; Kulkarni et al., Citation2019). The addition of reinforcements to aluminium improves the properties of the base metal. The improvement in properties is a function of the fabrication route, type of reinforcement material, the size of reinforcement particles and percentage volume of reinforcement particles. Kallip et al (Citation2017) discovered that increase in the volume of Al2O3 particles in the matrix of AlMg5 alloy led to increased formation of finer grains and bimodal grain structure. Similarly, Hatti et al. (Citation2019) discovered that increase in the percentage volume of CNT in aluminium nanocomposites results in improved hardness value. The impact of reinforcement of aluminium alloy on the microstructural properties was reviewed by Ajide, Oluwole, Abu, and Petinrin (Citation2016). It was reported that improved casting setup reduces the rate of agglomerations and promotes even distribution of the reinforcement particles in the aluminium matrix thereby resulting in improved microstructure which also imparts the mechanical, corrosion and thermal properties of the AMCs. Lakshmi et al. (Citation2017) in a study on aluminium A6061 and sugarcane bagasse ash (SCBA) composite deployed optical microscopy to observe the microstructure of the samples It was observed that there was a reduction in the particle size of the AMCs due to uniform distribution SCBA in the 0.5 and 1.5% samples but agglomeration was seen in the 2.5 wt% SCBA sample due to the clustering of the SCBA particles. The increased addition of SCBA led to a decrease in the wear rate, % elongation but the tensile strength and hardness values increased. It can be depicted from the study that there is an optimum amount of reinforcement that can be added to aluminium based matrix alloy to impart the desired properties. Similarly, Harish, Srikanth, Babu, and Sastry (Citation2019) characterized the microstructure of Al6063 hybrid composite made by alloying with cotton shell ash and SiC. The surface plot of the microstructure obtained is shown in . The surface plot was deduced using ImageJ software to give a 3-D view of the result of microstructural analysis. The authors posited uniform mixing of the reinforcement in the base alloy matrix which is not clear from the surface plots as the claim was only visible at 3 wt% of reinforcement. This is further evident in the microstructural properties shown in as there was no clear pattern in the variation of particle size. Also, the authors did not investigate the individual impact of the cotton shell ash and the SiC particles on the overall integrity of the composite. This could have been adduced from a well-constructed experimentation via modelling of process parameters using suitable software.
Figure 3. (a) Microstructure Al6063 (b) Al6063 + 0.1%(CSA + SiC, (c) Al6063 + 2%(CSA + SiC) (d) Al6063 + 3%(CSA + SiC) (Harish et al., Citation2019).
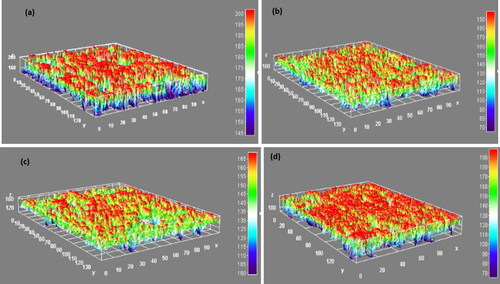
Table 2. Microstructural characteristics from image analysis (Harish et al., Citation2019).
The addition of reinforcement materials improves the mechanical integrity of aluminium. was adapted from the study of Pugalenthi et al. (Citation2019). It was observed that there was an increase ultimate strength (UTS) from 248 MPa in sample 1 to 325 MPa in Sample 4. Yield strength and hardness values increased with increase in the amount of reinforcement. Conversely, there was reduction in the percentage of elongation which is an indication of loss in ductility (Aweda et al., Citation2018). The improvement in strength is resulted from the reinforcement particles occupying the interstitial spacing between the aluminium atoms. Meanwhile, the loss in ductility is imparted by the ceramic particles which are brittle in nature. While strength is a desired property in AMCs, the need to retain ductility cannot be overemphasized, hence there is need to optimize the process of fabricating composites in terms of the mixing ratio. This is undoubtedly a lacuna for further research.
Figure 4. Mechanical properties of Al7075/SiC/Al2O3 composite (a) yield and ultimate strengths (b) %elongation (c) hardness; 1-Al7075 + 3%SiC + 2% Al2O3, 2 – Al7075 + 5%SiC + 2%Al2O3, 3-Al7075 + 7%SiC + 2%Al2O3, 4-Al7075 + 9%SiC + 2%Al2O3 (Pugalenthi et al., Citation2019).
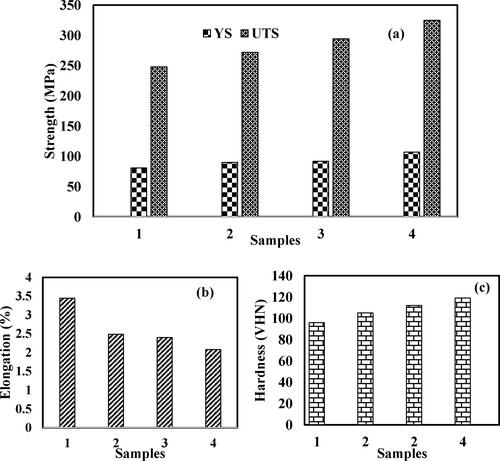
The impact of thermomechanical treatment has been investigated by many scholars (Bembalge & Panigrahi, Citation2019; Chidambaram, Balasivanandha Prabu, & Padmanabhan, Citation2019; Phanibhushana, Chandrappa, & Niranjan, Citation2018). shows a comparison of hardness and reinforcement for as-synthesized composite (0 Pass) and secondarily treated composite (1 Pass) in Phanibhushana et al. (Phanibhushana et al., Citation2018). Severe Plastic Deformation (SPD) was imposed on the as cast samples through Equal Channel Angular Pressing (ECAP). The results showed that there was a steady increase in the hardness values of the 0 Pass and 1 Pass samples from 1 − 3 wt% reinforcement. The 4 wt% 1 Pass sample witnessed a sharp rise in hardness while its corresponding 0 Pass sample witnessed a fall. This showed that at 3 wt.%, maximum reinforcement has been achieved for hardness. Generally, the SPD samples showed higher hardness values when compared to their as produced counterparts. This was attributed to higher strain hardening during the process of deformation which may have inhibited the growth of voids and cracks (Anjan & Kumar, Citation2018)
Figure 5. The Effect of reinforcement on hardness of hematite reinforced aluminium metal; 0 Pass: as produced composite; 1 Pass: secondary treatment by SPD process (Phanibhushana et al., Citation2018).
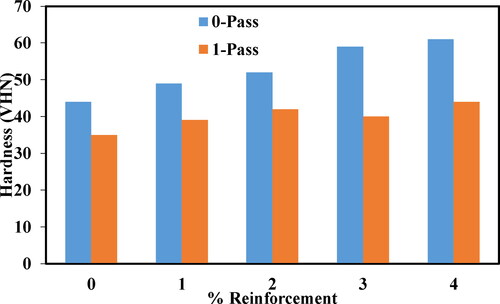
Veličković et al. (Citation2019) carried out optimization of the mixing ratios of A356/SiC nanocomposite using Taguchi method through compocasting route. The influence of amount of reinforcement on Signal-to-Noise (SN) showed that 0.2 wt.% of SiC is required to achieve the minimum SN in A356/SiC while a sliding speed of 0.25 m/s is needed to achieve the same. Also, a load of 100 MPa is needed to achieve minimum SN in the composite. The authors posited that the slopes of the graphs for the addition of SiC, sliding speed and normal load shows that all these factors have influence on SN. In another study conducted by Ravikumar, Amirthagadeswaran, and Senthil (Citation2014), Taguchi method was deployed to optimize the process parameters of AC2A-Ni composite coated with SiCp produced through squeeze casting route. The results of the analytic study proved that 10% reinforcement, a pouring temperature of 725 °C and a pressure of 100 MPa were among the optimum parameters needed to produce defect free cast composites. Despite these efforts, research on optimization of process parameters for the various routes of fabrication and various reinforcing agents are scarce; hence, the need for more study in this regard.
6. Concluding remarks and suggestions for future research
This review has established that laudable efforts have been made by researchers on primary synthesis of Aluminium Matrix Composites (AMCs). The use of several synthetic ceramics (Al2O3, Al3Ni, B4C, Beryl, fly ash, fibres, graphite, K2TiF6, mica, MgAl2O4, MoS2, MWCNTs, SiC, Si3N4,TiB2, Ti5-B1, TiC, TiO2, Y2O3, ZrB2p and quasicrystals) and ash from agro wastes (rice husk, groundnut shell, bamboo leaf, coconut shell, sugarcane bagasse, corn cob, palm kernel and periwinkle shell) as reinforcements as well as their hybrid forms for production of AMCs from various routes have been substantially reported. The review provides opportunity to understand potential benefits and detrimental effects associated with the use of various primary synthesis routes, ceramic reinforcements (synthetic ceramic, industrial waste, agro-waste ash and their hybrid forms) and secondary treatment for manufacturing of AMCs. Although several researchers have explored secondary treatment as a means for improving properties of developed AMCs, there is need for more studies that will focus on the synergetic use of heat treatment and selected thermomechanical treatment techniques as secondary treatment for AMCs. Furthermore, there is need to investigate the impact of combining multi-synthesis routes (powder metallurgy, casting, pressure infiltration, rapid prototyping and so on) and multi-approach secondary treatment on the mechanical, tribological and microstructural properties of as produced AMCs. Sequel to the combination of multi-synthesis route and multi-approach secondary treatment as pointed out in the aforementioned, some specific research lacunae have been identified in the pursuit of ameliorating the drawbacks inherent in the conventional production routes and treatment methods. Therefore, the following specific suggestions are made in the cause of future research endeavours:
Modelling properties of AMCs based on ceramic reinforcement type, particle size of reinforcement, fabrication temperatures and pressure of synthesized composites.
Investigative studies of aluminium matrix composite synthesized by several routes in order to ascertain the most appropriate one (s) for specific desired properties and applications.
Thermomechanical and tribological characterizations of as-synthesized AMCs subjected to secondary treatment by deploying thermomechanical processes such as cryorolling, cryoforging, hot forging, hot rolling and other evolving SPD treatments.
Examining the microstructures, mechanical and tribological properties of AMCs manufactured via multi-synthesis route.
Investigation on synergetic impact of multi-synthesis route and multi-approach secondary treatment on the mechanical, tribological and microstructural properties of AMCs.
Disclosure statement
No potential conflict of interest was reported by the author(s).
References
- Ajide, O. O., Oluwole, O. O., Abu, R., & Petinrin, M. O. (2016). Microstructural characteristics of aluminum based composites developed by liquid metallurgy route: An overview. Int J Eng Technol, 6, 405–415.
- Alaneme, K. K., Bodunrin, M. O., & Awe, A. A. (2018). Microstructure, mechanical and fracture properties of groundnut shell ash and silicon carbide dispersion strengthened aluminium matrix composites. Journal of King Saud University – Engineering Sciences, 30(1), 96–103. doi:10.1016/j.jksues.2016.01.001
- Alaneme, K. K., Eze, H. I., & Bodunrin, M. O. (2015). Corrosion behaviour of groundnut shell ash and silicon carbide hybrid reinforced Al–Mg–Si alloy matrix composites in 3.5% NaCl and 0.3M H2SO4 solutions. The Leonardo Electronic Journal of Practices and Technologies, 14, 141–158.
- Al-Fadhalah, K. J., Almazrouee, A. I., & Aloraier, A. S. (2014). Microstructure and mechanical properties of multi-pass friction stir processed Aluminum Alloy 6063. Materials and Design, 53, 550–560. doi:10.1016/j.matdes.2013.07.062
- Anjan, B. N., & Kumar, P. G. V. (2018). Microstructure and mechanical properties of ZA27 based SiC reinforced composite processed by multi directional forging. Materials Research Express, 1–19. doi:10.1088/2053-1591/aadb02.
- Arora, G., & Sharma, S. (2018). A comparative study of AA6351 mono-composites reinforced with synthetic and agro waste reinforcement. International Journal of Precision Engineering and Manufacturing, 19(4), 631–638. doi:10.1007/s12541-018-0076-1
- Aweda, J. O., Orhadahwe, T. A., & Ohijeagbon, I. O. (2018). Rapid cyclic heating of mild steel and its effects on microstructure and mechanical properties. IOP Conference Series: Materials Science and Engineering, 413, 012016. doi:10.1088/1757-899X/413/1/012016
- Awotunde, M. A., Adegbenjo, A. O., Obadele, B. A., Okoro, M., Shongwe, B. M., & Olubambi, P. A. (2019). Influence of sintering methods on the mechanical properties of aluminium nanocomposites reinforced with carbonaceous compounds: A review. Journal of Materials Research and Technology, 8(2), 2432–2449. doi:10.1016/j.jmrt.2019.01.026
- Babalola, P. O., Bolu, C. A., Inegbenebor, A. O., & Odunfa, K. M. (2014). Development of Aluminium Matrix Composites: A review. Online International Journal of Engineering Technology Research, 2, 1–11.
- Bahrami, A., Soltani, N., Pech-Canul, M. I., & Gutiérrez, C. A. (2016). Development of metal-matrix composites from industrial/agricultural waste materials and their derivatives. Critical Reviews in Environmental Science and Technology, 46(2), 143–207. doi:10.1080/10643389.2015.1077067
- Barekar, N., Tzamtzis, S., Dhindaw, B. K., Patel, J., Hari Babu, N., & Fan, Z. (2009). Processing of aluminium-graphite particulate metal matrix composites by advanced shear technology. Journal of Materials Engineering and Performance, 18(9), 1230–1240. doi:10.1007/s11665-009-9362-5
- Bembalge, O. B., & Panigrahi, S. K. (2018). Development and strengthening mechanisms of bulk ultrafine grained AA6063/SiC composite sheets with varying reinforcement size ranging from nano to micro domain. Journal of Alloys and Compounds., 766, 355–372. doi:10.1016/j.jallcom.2018.06.306
- Bembalge, O. B., & Panigrahi, S. K. (2019). Aging behavior of ultrafine-grained AA6063/SiC composites with varying reinforcement sizes. Materials Science and Engineering: A, 768, 138482. doi:10.1016/j.msea.2019.138482
- Bhoi, N. K., Singh, H., & Pratap, S. (2019). Review: Developments in the aluminium metal matrix composites reinforced by micro/nano particles – a review. Journal of Composite Materials, 0, 1–21. 10.1177/0021998319865307.
- Camargo, P. H. C., Satyanarayana, K. G., & Wypych, F. (2009). Nanocomposites: Synthesis, structure, properties and new application opportunities. Materials Research, 12(1), 1–39. doi:10.1590/S1516-14392009000100002
- Canute, X., & Majumder, M. C. (2018). Mechanical and tribological behaviour of stir cast aluminium/boron carbide/fly ash composites. J Eng Sci Technol, 13, 755–777.
- Chen, G., Chang, H., Sun, J., Wang, B., Yang, L., & Zhang, J. (2020). Microstructures and properties of graphite nanoflake/6061Al matrix composites fabricated via spark plasma sintering. Journal of Materials Engineering and Performance, 29, 1235–1244. doi:10.1007/s11665-020-04676-2
- Chen, C. L., & Lin, C. H. (2017). A study on the aging behavior of al6061 composites reinforced with Y2O3 and TiC. Metals (Metals), 7(1),1–8. doi:10.3390/met7010011
- Chidambaram, A., Balasivanandha Prabu, S., & Padmanabhan, K. A. (2019). Microstructure and mechanical properties of AA6061–5wt. %TiB2 in-situ metal matrix composite subjected to equal channel angular pressing. Materials Science and Engineering: A, 759, 762–769. doi:10.1016/j.msea.2019.05.068
- Chin, W. H. A., Koav, S. C., Chan, M. Y., Yeow, T. K., & Pang, M. M. (2020). Preparation and characterization of composites made from chrysanthemum waste using resin. AIP Conf Proc, 2233(1). doi:10.1063/5.0001338
- Dhinakaran, S., & Moorthy, T. V. (2014). Effect of weight percentage on mechanical properties of boron carbid particulate reinforced aluminium matrix composites. Applied Mechanics and Materials, 612, 151–155. doi:10.4028/www.scientific.net/AMM.612.151
- Dobrzanski, A. W.-F., Kremzer, L. A., & Adamiak, M. (2008). M. Manufacturing of aluminium matrix composite materials reinforced by Al2O3 particles. Journal of Achievements in Materials and Manufacturing Engineering, 27, 99–102.
- Donald, A. O., Hassan, M. A., Hamza, S., Garba, E., Dangtim, D. K., & Mamad, M. (2018). Development and characterisation of aluminum composites reinforced with carbonized coconut shell and silicon carbide particle for automobile piston application. Global Scientific Journals, 6, 390–398.
- Ebhota, W. S., & Jen, T.-C. (2018). Casting and applications of functionally graded metal matrix composites. Advanced Casting Technologies, 60–86. doi:10.5772/intechopen.71225.
- Ebrahimi, M., Konaganti, V. K., Moradi, S., Doufas, A. K., & Hatzikiriakos, S. G. (2016). Slip of polymer melts over micro/nano-patterned metallic surfaces. Soft Matter, 12(48), 9759–9768. doi:10.1039/c6sm02235a
- Ekambaram, S., & Murugan, N. (2015). Synthesis and characterization of aluminium alloy AA6061-Aluminal metal matrix composite. International Journal of Current Engineering and Technology, 5, 3211–3216.
- El-Labban, H. F., Abdelaziz, M., & Mahmoud, E. R. I. (2014). Coating of 6028 aluminum alloy using aluminum piston alloy and Al–Si alloy-based nanocomposites produced by the addition of Al-Ti5-B1 to the matrix melt. Metallurgical and Materials Transactions B, 45(5), 1608–1614. doi:10.1007/s11663-014-0081-4
- Etter, T., Kuebler, J., Frey, T., Schulz, P., Löffler, J. F., & Uggowitzer, P. J. (2004). Strength and fracture toughness of interpenetrating graphite/aluminium composites produced by the indirect squeeze casting process. Materials Science and Engineering: A, 386(1-2), 61–67. doi:10.1016/j.msea.2004.06.066
- Ghosh, S. K., & Saha, P. (2011). Crack and wear behavior of SiC particulate reinforced aluminium based metal matrix composite fabricated by direct metal laser sintering process. Materials and Design, 32(1), 139–145. doi:10.1016/j.matdes.2010.06.020
- Gomez, L., Busquets-Mataix, D., Amigo, V., & Salvador, M. D. (2009). Analysis of boron carbide aluminium matrix composites. Journal of Composite Materials., 43(9), 987–995. doi:10.1177/0021998308097731
- Gopal, K. U. B., Sreenivas, R. K. V., & Vasudeva, B. (2013). Effect of boron carbide reinforcement on aluminium matrix composites. International Journal of Metallurgy and Materials Science Engineering, 3, 41–48.
- Gowrishankar, T. P., Manjunatha, L. H., & Sangmesh, B. (2019). Mechanical and wear behaviour of Al6061 reinforced with graphite and TiC hybrid MMCs. Material Research Innovations, 24 doi:10.1080/14328917.2019.1628497.
- Goyal, K., & Marwaha, K. (2016). Processing and properties of aluminium matrix composites: A short review. European Journal of Advances in Engineering and Technology, 3, 54–59.
- Gupta, P. K., & Srivastava, R. K. (2018). Fabrication of ceramic reinforcement aluminium and its alloys metal matrix composite materials: A review. Materials Today: Proceedings, 5(9), 18761–18775. doi:10.1016/j.matpr.2018.06.223
- Hanamantraygouda, M. B., & Shivakumar, B. P. (2015). Effect of forging condition on mechanical properties of Al/SiC metal matrix composites. International Journal of Engineering Research and Technology, 4AD(5), 567–571.
- Harish, P., Srikanth, V. M., Babu, P. R., & Sastry, M. R. C. (2019). Characterization of mechanical and tribological properties of aluminium alloy based hybrid composites reinforced with cotton shell ash and silicon carbide. International Journal of Latest Engineering Science, 2, 1–15.
- Hatti, S. P., Murthy, K. N., & Somanakatti, A. B. (2019). Microstructure and hardness behaviour study of carbon nanotube in aluminium nanocomposites. Smart Innovation, Systems and Technologies, 169, 421–428.
- Hussain, M. Z., Khan, U., Chanda, A. K., & Jangid, R. (2017). Fabrication and hardness analysis of F-MWCNTs reinforced aluminium nanocomposite. Procedia Engineering, 173, 1611–1618. doi:10.1016/j.proeng.2016.12.262
- Hussain, M. Z., Khan, S., & Sarmah, P. (2020). Optimization of powder metallurgy processing parameters of Al2O3/Cu composite through Taguchi method with Grey relational analysis. Journal of King Saud University - Engineering Sciences, 32(4), 274–286. doi:10.1016/j.jksues.2019.01.003
- Hussain, M., Rao, P. N., Singh, D., & Jayaganthan, R. (2018). Precipitation hardening behaviour of Al-Mg-Si alloy processed by cryorolling and room temperature rolling. Materials Research Express., 5(4) 1–19. :
- Ikubanni, P. P., Oki, M., & Adeleke, A. A. A. (2020). review of ceramic/bio-based hybrid reinforced aluminium matrix composites. Cogent Engineering, 7, 1727167.
- Ipekoglu, M., Nekouyan, A., Albayrak, O., & Altintas, S. (2017). Mechanical characterization of B4C reinforced aluminum matrix composites produced by squeeze casting. Journal of Materials Research, 32(3), 599–605. doi:10.1557/jmr.2016.495
- Jims John Wessley, G., Srinivas, M. D. S., & Ali, M. D. (2019). Preparation and characterization of an aluminium 6061 alloy based metal matrix composite. International Journal of Engineering and Advanced Technology, 8, 113–116.
- Jaseem, I., Immanuel, R. J., Rao, P. N., Khan, F., Sahoo, B. N., & Panigrahi, S. K. (2018). Synergetic effect of cryorolling and postroll aging on simultaneous increase in wear resistance and mechanical properties of an Al–Cu alloy. Journal of Tribology., 140, 1–11. doi:10.1115/1.4040162.
- Joseph, O. O., & Babaremu, K. O. (2019). Agricultural waste as a reinforcement particulate for aluminum metal matrix composite (AMMCs): A review. Fibers, 7(4), 33. doi:10.3390/fib7040033
- Joshi, A., Yogesha, K. K., Kumar, N., & Jayaganthan, R. (2016). Influence of annealing on microstructural evolution, precipitation sequence, and fracture toughness of cryorolled Al–Cu–Si alloy. Metallography, Microstructure, and Analysis, 5(6), 540–556. doi:10.1007/s13632-016-0313-x
- Kahlani, B., & Jafarzadeh, H. (2020). Microstructure and mechanical properties of aluminium/copper composite rod fabricated by axisymmetric spiral extrusion. Transactions of the Indian Institute of Metals, 73(3), 515–520. doi:10.1007/s12666-020-01869-0
- Kale, V. C. (2015). Aluminium based metal matrix composites for aerospace application: A literature review. IOSR J Mech Civ Eng, 12, 2278–1684. doi:10.9790/1684-12653136.
- Kallip, K., Babu, N. K., AlOgab, K. A., Kollo, L., Maeder, X., Arroyo, Y., & Leparoux, M. (2017). Microstructure and mechanical properties of near net shaped aluminium/alumina nanocomposites fabricated by powder metallurgy. Journal of Alloys and Compounds, 714, 133–143. doi:10.1016/j.jallcom.2017.04.233
- Kar, C., & Surekha, B. (2020). Characterisation of aluminium metal matrix composites reinforced with titanium carbide and red mud. Material Research Innovations, 24, 1-10. doi:10.1080/14328917.2020.1735683.
- Keshavamurthy, R., Sudhan, J. M., Gowda, N., & Krishna, R. A. (2016). Effect of thermo-mechanical processing and heat treatment on the tribological characteristics of al based MMC’s. iop Conference Series: Materials Science and Engineering, 149, 012118. doi:10.1088/1757-899X/149/1/012118
- Khan, M., Syed, W. H., Ud-Din, R., Akhtar, S., & Aune, R. E. (2019). Spark plasma sintering of boron carbide reinforced aluminium alloy (Al6061) matrix composites. Proc. 16th Int. Bhurban Conf. Appl. Sci. Technol. Islam. Pakistan, 35–41.
- Khan, M., Zulfaqar, M., Ali, F., & Subhani, T. (2017). Hybrid aluminium matrix composites containing boron carbide and quasicrystals: Manufacturing and characterisation. Materials Science Technology., 33, 1–9 doi:10.1080/02670836.2017.1342017.
- Khodabakhshi, F., Gerlich, A. P., & Worswick, M. (2018). Fabrication and characterization of a high strength ultra-fine grained metal-matrix AA8006-B4C layered nanocomposite by a novel accumulative fold-forging (AFF) process. Materials and Design., 157, 211–226. doi:10.1016/j.matdes.2018.07.047
- Kim, J. T., Soprunyuk, V., Chawake, N., Zheng, Y. H., Spieckermann, F., & Hong, S. H. (2020). Outstanding strengthening behavior and dynnamic mechanical properties of in-situ-Al-Al3Ni composites by Cu addition. Compos Part B Eng, 189, 1–14.
- Kishchik, M. S., Mikhaylovskaya, A. V., Kotov, A. D., Mosleh, A. O., AbuShanab, W. S., & Portnoy, V. K. (2018). Effect of multidirectional forging on the grain structure and mechanical properties of the Al-Mg-Mn alloy. Materials, 11(11), 2166. doi:10.3390/ma11112166
- Kishore Babu, N., Kallip, K., Leparoux, M., AlOgab, K. A., Talari, M. K., & Alqahtani, N. M. (2017). High strength Ti-6Al-4V alloy fabricated by high-energy cube milling using calcium as process control agent (PCA) and spark plasma sintering. The International Journal of Advanced Manufacturing Technology, 93(1-4), 445–453. doi:10.1007/s00170-017-9994-9
- Kok, M. (2005). Production and mechanical Properties of Al2O3 particle-reinforced 2024 Aluminium alloy composites. Journal of Materials Processing Technology., 161(3), 381–387. doi:10.1016/j.jmatprotec.2004.07.068
- Krushna, M. G., Shekhar, P. S., & Kumar, S. A. (2019). Effect of hot forging on high temperature tribological properties of aluminium composite reinforced with agro and industrial waste. Int J Eng Adv Technol, 8, 1607–1612.
- Kulkarni, P. P., Siddeswarappa, B., & Kumar, K. S. H. (2019). A survey on effect of agro waste ash as reinforcement on aluminium base metal matrix composites. Open Journal of Composite Materials, 09(03), 312–326. doi:10.4236/ojcm.2019.93019
- Kumar, B. M., Parameshwaran, R., Deepandurai, K., & Senthil, S. M. (2020). Influence of milling parameters on surface roughness of Al-SiC-B4C. Transactions of the Indian Institute of Metals, 73(5), 1171–1183. doi:10.1007/s12666-020-01960-6
- Kumar, A., & Rai, R. N. (2018). Fabrication, microstructure and mechanical properties of boron carbide (B4Cp). IOP Conference Series: Materials Science and Engineering, 377, 012092. doi:10.1088/1757-899X/377/1/012092
- Kumar, S., & Theerthan, J. A. (2008). Production and characterization of aluminium-fly ash composite using stir casting method. Rourkela: National Institute of Technology.
- Kumar, V. M., & Venkatesh, C. V. (2018). Effect of ceramic reinforcement on mechanical properties of aluminium matrix composites produced by stir casting process. Materials Today: Proceedings, 5(1), 2466–2473. doi:10.1016/j.matpr.2017.11.027
- Kummari, N., & Paramesh, M. (2019). Mechanical characterization of aluminium reinforced with boron carbide metal matrix composites. American Institute of Physics Conference Proceedings 2200, 020002, 1-10.
- Lakshmi, V. V. K., Subbaiah, K. V., Sarojini, J. & Shabana, (2017). Study of mechanical properties and wear behaviour of sugarcane ash reinforced aluminium composite. International Journal of Mechanical Engineering & Technology, 8, 597–606.
- Liu, H., Zhang, J., Gou, J., & Ding, C. (2017). The preparation of Al/Fe composite powders by electroless plating. Materials Science and Technology, 33(10), 1180–1185. doi:10.1080/02670836.2016.1271933
- Lokesh, G. N., Ramachandra, M., & Mahendra, K. V. (2014). Effect of hot rolling on Al-4.5%Cu alloy reinforced fly ash metal matrix composite. International Journal of Composite Materials, 4, 21–29.
- Ma, X., Zhao, Y. F., Tian, W. J., Qian, Z., Chen, H. W., Wu, Y. Y., & Liu, X. F. (2016). A novel Al matrix composite reinforced by nano-AlNp network. Scientific Reports, 6, 34919. doi:10.1038/srep34919
- Manfredi, D., Calignano, F., Krishnan, M., Canali, Y., Ambrosio, E. P., & Biamino, S. (2014). Additive manufacturing of Al alloys and aluminium matrix composites (AMCs) Diego. Intech, 1, 1–35. 10.5772/57353.
- Mangalore, P., Vittal, C. S., Ulvekar, A., & Sanjay, J. (2019). Study of tribological properties of Al 70729 alloy reinforced with agro waste particles. AIP Conf Proc n.d, 020015, 1–5. doi:10.1063/1.5092898
- Marchese, G., Aversa, A., Lorusso, M., Manfredi, D., Calignano, F., Lombardi, M., … Pavese, M. (2018). Development and characterisation of aluminium matrix nanocomposites ALSi10Mg/MgAl2O4 by laser powder bed fusion. Metals (Metals), 8(3), 175. doi:10.3390/met8030175
- McWilliams, B., Sano, T., Yu, J., Gordon, A., & Yen, C. (2013). Influence of hot rolling on the deformation behavior of particle aluminium metal matrix composite. Materials Science and Engineering: A, 577, 54–63. doi:10.1016/j.msea.2013.03.039
- Mohanavel, V., Rajan, K., Suresh Kumar, S., Vijayan, G., & Vijayanand, M.S. (2018). Vijayanand M s. Study on mechanical properties of graphite particulates reinforced aluminium matrix composite fabricated by stir casting technique. Materials Today: Proceedings, 5(1), 2945–2950. doi:10.1016/j.matpr.2018.01.090
- Muni, R. N., Singh, J., Kumar, V., & Sharma, S. (2019). Influence of rice husk ash, Cu, Mg on the mechanical behaviour of aluminium matrix hybrid composites. Journal of Applied Engineering Research, 14, 1828–1834.
- Murthy, P. S. R., & Rao, Y. S. R. (2019). Evaluation of mechanical properties of aluminum alloy-alumima-boron carbide metal matrix composites. World Journal of Mechanical Engineering, 4, 027–034.
- Nanjan, S., & Janakiram, G. M. (2019). NCharacteristics of A6061/(Glass-Fibre + Al2O3 + SiC + B4C) reinforced hybrid composite prepared through stir casting. Advances in Materials Science and Engineering, 2019, 1–12. doi:10.1155/2019/6104049
- Narayan, S., & Rajeshkannan, A. (2017). Hardness, tensile and impact behavior of hot forged aluminium metal matrix composites. Journal of Materials Research and Technology, 6(3), 213–219. doi:10.1016/j.jmrt.2016.09.006
- Naveen, G. J., & Ramesh, C. S. (2014). Microstructure and Effect of Ni-P Coating of Sic Particles on. Tribological Behavior of Cast Al6061-Sic Composites, 3, 606–609.
- Obande, W., Mamalis, D., Ray, D., Yang, L., & O’Bradaigh, C. M. (2019). Mechanical and thermomechancial characterization of vacuum-infused thermoplastic and thermoset based composites. Materials and Design, 175, 1–13.
- Orhadahwe, T. A., Adeleke, A. A., Aweda, J. O., Ikubanni, P. P., & Jamiu, K. (2020). Microstructural image analyses of mild carbon steel subjected to a rapid cyclic treatment. Journal of Chemical Technology and Metallurgy, 55, 198–209.
- Ozer, A. (2016). The microstructures and mechanical properties of Al-15Si-2.5Cu-0.5Mg/(wt%)B4C composites produced through hot pressing technique and subjected to hot extrusion. Materials Chemistry and Physics, 183, 288–296. doi:10.1016/j.matchemphys.2016.08.029
- Palanikumar, K., Rajkumar, E., & Pitchandi, S. (2019). K. Influence of Primary B4C Particles and Secondary Mica Particles on the Wear Performance of Al6061/B4C/Mica Hybrid Composites. J Bio- Tribo-Corrosion, 5, 1–12. doi:10.1007/s40735-019-0267-z.
- Patel, M., Kumar, A., Sahu, S. K., & Singh, M. K. (2020). Mechanical behaviours of ceramic particulate reinforced aluminium metal matrix composites – a review. International Research Journal of Engineering & Technology, 7, 201–204.
- Phanibhushana, M. V., Chandrappa, C. N., & Niranjan, H. B. (2018). Experimental study of hematite reinforced aluminum metal matrix composites subjected to equal channel angular pressing. Materials Today: Proceedings, 5(5), 13282–13289. doi:10.1016/j.matpr.2018.02.320
- Pugalenthi, P., Jayaraman, M., & Subburam, V. (2019). Study of the microstructures and mechanical properties of aluminium hybrid composites With SiC and Al2O3. Materiali in Tehnologije, 53(1), 49–55. doi:10.17222/mit.2018.118
- Quintana, J. L. C., Medina, S. S., Hernandez, M., & Suarez, O. M. (2018). Study of thermomechanical properties of an Al-Zn-Based Based composite reinforced with dodecarboride particles. Advances in Materials Science and Engineering V, 1–8. doi:10.1155/2018/2975234.
- Radhika, N., Subramanian, R., Venkat Prasat, S., & Anandavel, B. (2012). Dry sliding wear behaviour of aluminium/alumina/graphite hybrid metal matrix composites. Industrial Lubrication and Tribology, 64(6), 359–366. doi:10.1108/00368791211262499
- Ramesh, C. S., Keshavamurthy, R., Pramod, S., & Koppad, P. G. (2011). Abrasive wear behavior of Ni-P coated Si3N4 reinforced Al6061 composites. Journal of Materials Processing Technology, 211(8), 1423–1431. doi:10.1016/j.jmatprotec.2011.03.015
- Ramnath, B. V., Elanchezhian, C., Annamalai, R. M., Aravind, S., Atreya, T. S. A., & Vignesh, V. (2014). Aluminium metal matrix composites - A review. Reviews on Advanced Materials Science, 38, 55–60.
- Ravi, B., Balu, N. K., & Uday, P. J. (2016). Fabrication and mechanical characterization of boron carbide reinforced aluminium matrix composites. Discovery, 52, 1389–1395.
- Ravikumar, A. R., Amirthagadeswaran, K. S., & Senthil, P. (2014). Parametric optimization of squeeze cast AC2A-Ni Coated SiC p composite using taguchi technique. Advances in Materials Science and Engineering., 2014, 1–10. doi:10.1155/2014/160519
- Reddappa, H. N., Suresh, K. R., Niranjan, H. B., & Satyanarayana, K. G. (2020). Effect of rolling on microstructure and wear behavior of hot rolled Al6061-Beryl composites. Advanced Material Research, 463 – 464, 444-448.
- Reddy, P. S., Kesavan, R., & Vijaya Ramnath, B. (2018). Investigation of mechanical properties of aluminium 6061-silicon carbide, boron carbide metal matrix composites. Silicon, 10(2), 495–502. doi:10.1007/s12633-016-9479-8
- Rofman, O. V., Mikhaylovskaya, A. V., Kotov, A. D., Prosviryakov, A. S., & Portnoy, V. K. (2019). Effect of thermomechanical treatment on properties of an extruded Al–3.0Cu–1.2Mg/SiCp composite. Materials Science and Engineering: A, 739, 235–243. doi:10.1016/j.msea.2018.10.053
- Rozhbiany, F. A. R., & Jalal, S. R. (2019). Influence of reinforcement and processing on aluminum matrix composites modified by stir casting route. Advanced Composites Letters, 28, 1–8.
- Saravanakumar, A., Sasikumar, P., & Sivasankaran, S. (2014). Effect of graphite particles in drilling of hybrid aluminium matrix composites. Procedia Engineering, 97, 495–504. doi:10.1016/j.proeng.2014.12.274
- Shirvanimoghaddam, K., Khayyam, H., Abdizadeh, H., Karbalaei Akbari, M., Pakseresht, A.H., Ghasali, E., & Naebe, M. (2016). Boron carbide reinforced aluminium matrix composite: Physical, mechanical characteriztion and mathematical modelling. Materials Science and Engineering: A, 658, 135–149. doi:10.1016/j.msea.2016.01.114
- Singla, M., Rana, R., & Lata, S. (2017). Microstructure and mechanical properties of aluminium based metal matrix composite – a review manufacturing microstructure and mechanical properties of aluminium based metal matrix composite – a review. International Journal of Advanced Product Industrial Engineering, 517, 3–6.
- Soni, S., & Pandey, A. (2014). Effect of heat treatment on mechanical and corrosion. International Journal of Advanced Mechanical Engineering, 4, 767–782.
- Soundararajan, R., Ramesh, A., Sivasankaran, S., & Vignesh, M. (2017). Modeling and analysis of mechanical properties of aluminium alloy (A413) reinforced with boron carbide (B4C) processed through squeeze casting process using artificial neural network model and statistical technique. Materials Today: Proceedings, 4(2), 2008–2030. doi:10.1016/j.matpr.2017.02.047
- Stojanovic, B., Babic, M., Mitrovic, S., Vencl, A., Miloradovic, N., & Pantic, M. (2013). Tribological characteristics of aluminium hybrid composites reinforced with silicon carbide and graphite: A review. Journal of the Balkan Tribological Association, 19, 83–89.
- Subramaniam, B., Natarajan, B., Kaliyaperumal, B., & Chelladurai, S. J. S. (2018). Investigation on mechanical properties of aluminium 7075-boron-coconut shell fly ash reinforced hybrid metal matrix composites. China Foundry, 15(6), 449–455. doi:10.1007/s41230-018-8105-3
- Thirumalai, T., Subramanian, R., Kumaran, S., Dharmalingam, S., & Ramakrishnan, S. S. (2014). Production and characterization of hybrid aluminum matrix composites reinforced with boron carbide (B4C) and graphite. Journal of Scientific and Industrial Research (India), 73, 667–670.
- Tiku, V., Navin, K., & Kurchania, R. (2020). Study of structural and mechanical properties of Al/Nano-Al2O3 metal matrix nanocomposite fabricated by powder metallurgy method. Transactions of the Indian Institute of Metals, 73(4), 1007–1013. doi:10.1007/s12666-020-01931-x
- Tjong, S. C., Wang, G. S., Geng, L., & Mai, Y. W. (2004). Cyclic deformation behavior of in situ aluminum-matrix composites of the system Al-Al3Ti-TiB2-Al2O3. Composites Science and Technology, 64(13-14), 1971–1980. doi:10.1016/j.compscitech.2004.02.006
- Tjong, S. C., Wang, G. S., & Mai, Y. W. (2005). High cycle fatigue response of in-situ Al-based composites containing TiB2 and Al2O3 submicron particles. Composites Science and Technology, 65(10), 1537–1546. doi:10.1016/j.compscitech.2005.01.012
- Vandersluis, E., Bois-Brochu, A., Ravindran, C., & Chiesa, F. (2020). Mechanical properties and properties of low-pressure die-cast 319 aluminum prepared with hot isostatic pressing, thermal treatment or chemical treatment. Journal of Materials Engineering and Performance, 1–11. doi:10.1007/s11665-020-04743-8.
- Varvani-Farahani, A. (2010). Composite materials: Characterization, fabrication and application - Research challenges and directions. Applied Composite Materials, 17(2), 63–67. doi:10.1007/s10443-009-9107-5
- Veličković, S., Garić, S., Stojanović, B., & Vencl, A. (2016). Tribological Properties of Aluminium Matrix Nanocomposites. Applied Engineering Letters, 1, 72–79.
- Veličković, S., Stojanović, B., Babić, M., Vencl, A., Bobić, I., & Bognár, G. V. (2019). Parametric optimization of the aluminium nanocomposites wear rate. Journal of the Brazilian Society of Mechanical Sciences and Engineering, 41, 1-10. doi:10.1007/s40430-018-1531-8.
- Vijayaraghavan, K., Arul Kumar, A., Amos Robert Jayachandran, J., & Subramani, N. (2016). Analysis on aluminium metal matrix composites with boron carbide and graphite. International Journal of Innovative Research in Science Engineering and Technology, 5, 46–51.
- Wąsik, A., Leszczyńska-Madej, B., Madej, M., & Goły, M. (2020). Effect of heat treatment on microstructure of Al4Cu-SiC composites consolidated by powder metallurgy technique. Journal of Materials Engineering and Performance, 29(3), 1841–1848. doi:10.1007/s11665-020-04685-1
- Wlodarcyzk-Fligier, A., Dobrzanski, L.A., Kremzer, M., & Adamiak, M. (2008). Manufacturing of aluminium matrix composite materials reinforced by Al2O3 particles. Journal of Achievements in Materials and Manufacturing Engineering, 27(1), 99.
- Xavier, L. F., & Suresh, P. (2016). Wear behavior of aluminium metal matrix composite prepared from industrial waste. Scientific World Journal., 2016, 1–8. doi:10.1155/2016/6538345
- Xi, L., Gu, D., Guo, S., Wang, R., Ding, K., & Prashanth, K. G. (2020). Grain refinement in laser manufactured Al-based composites with TiB2 ceramic. Journal of Materials Research and Technology., 9(3), 2611–2622. doi:10.1016/j.jmrt.2020.04.059
- Yadav, B. N., Muchhala, D., Singh, P., Gupta, G., Venkat, A. N. C., & Mondal, D. P. (2020). Compressive deformation behavior of Al–SiC–MWCNTs hybrid composite foam through factorial design of experiments. Transactions of the Indian Institute of Metals, 73(1), 223–234. doi:10.1007/s12666-019-01825-7
- Yekinni, A. A., Durowoju, M. O., Agunsoye, J. O., Mudashiru, L. O., Animashaun, L. A., & Sogunro, O. D. (2019). Automotive application of hybrid composites of aluminium alloy matrix: A review of rice husk as based reinforcements. International Journal of Composite Materials, 9, 44–52.
- Yuen, H. C., Lee, W. B., & Ralph, B. (1995). Hot-rolling bonding of aluminium matrix composites with different volume fractions of alumina. Journal of Materials Science, 30(4), 843–848. doi:10.1007/BF01178415
- Zeng, Y., Chao, Y., Luo, Z., Cai, Y., & Song, R. (2018). Effect of multidirectional forging and heat treatment on mechanical properties of in in situ ZrB2p/6061Al composites. High Temperature Materials and Processes, 37(7), 603–612. doi:10.1515/htmp-2016-0200