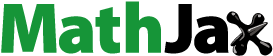
Abstract
Waste heat recovery is significant for improving energy utilization, reducing carbon emissions, and neutrality. The gravity heat pipe (GHP) has excellent thermal performance due to the cyclic phase transformation of the working fluid. As an important thermal management device for waste heat recovery, the heat transport capacity of GHP improves, the efficiency and performance of the waste heat recovery increase, and more wasted heat can be stored more quickly. Nano-diamond has the highest thermal conductivity and can be dispersed in water to form a diamond nanofluid, enhancing the thermal performance of GHP. In contrast, the study on the heat transfer behavior of the diamond nanofluid in GHP is insufficient. Besides, the influences of filling ratio (FR), mass fraction (MF), and heat flux on thermal performance are in demand for further study. In this article, the heat transfer behavior is investigated by studying the flow patterns of diamond nanofluids. The influences of filling ratio and mass fraction on flow patterns are analyzed. An orthogonal experiment is conducted; the heat flux has the most significant effect on the thermal performance, followed by the filling ratio and mass fraction. The thermal performance is the best when the optimal parameters (FR = 20%, MF = 1 w.t.%) are selected under a heat flux of 20 × 104 W/m2. The equivalent heat transfer coefficient reaches 3485 W/(m2·°C). This article can achieve a deeper understanding of the diamond nanofluid heat transfer mechanism in GHP and enhance the thermal performance of GHP for better waste heat recovery.
1. Introduction
Heat or thermal energy is a form of energy that meets the demand for energy transformation of various types as a primary energy source to meet the requirements of industries. Due to inefficient utilization, there is 20% - 50% heat loss [Citation1,Citation2]. This part of the energy, called waste heat, is transferred to the surrounding environment, increasing industrial production costs and causing the greenhouse effect [Citation3]. Promising studies have shown that waste heat can be collected and stored to provide energy to any process driven by thermal energy, mechanical energy and electricity [Citation4–6]. The waste heat recovery can reduce energy consumption and increase energy utilization, aiming to reduce carbon emissions and continue to achieve China’s “2030 carbon peak and 2060 carbon neutrality” goal [Citation1,Citation7].
The process of waste heat recovery requires various effective tools which can transfer waste heat efficiently and store the energy in a steady stage. The gravity heat pipe (GHP) is a passive thermal management element with high heat transfer performance, which can be used to transfer heat to storage [Citation8]. GHP has three parts: evaporator, condenser, and adiabatic section [Citation9]. GHP mainly conducts heat transfer by cyclic phase change of the inside working fluids under thermal driving force. The liquid working fluid at the evaporator absorbs heat and turns into vapor, and moves to the condenser driven by the pressure difference. The vapor dissipates heat to the environment and condenses into liquid and then flows back to the evaporator driven by gravity (see ). The cyclic phase change of the working fluid makes the GHP have a good heat transfer capacity [Citation10,Citation11]. And the movement of working fluid has different patterns, eg, bubble flow, slug flow, and churn flow, and achieves varied heat transport capacity [Citation12]. Therefore, it is important to study the flow pattern in the GHP to reveal its heat transfer behavior and the effect on the heat transport capacity.
The GHP as an efficient way to recover waste heat attracted much attention [Citation13–16]. Meanwhile, the approaches to improve its thermal performance have become important research hotspots. If the GHP has a higher heat transport capacity, the waste heat recovery will have better efficiency and performance. Therefore, it is beneficial to improve the thermal performance of GHP.
Working fluid in the GHP is one of the most important parameters affecting thermal performance [Citation17]. Various techniques concerning working fluids have been developed to improve thermal efficiency [Citation12,Citation16,Citation18,Citation19], and nanofluids have come into the research’s sight [Citation20–23]. Nanofluids are prepared by dispersing nanoparticles into pure fluids. The appropriate addition of nanoparticles is an effective way to improve the thermal performance of based fluids [Citation24]. Diamond is one of the natural matters with the highest thermal conductivity; its thermal conductivity can reach up to 2000 W/m·°C [Citation25]. The nano-diamond can be dispersed in deionized water, the most common working fluid for GHP, to form a diamond nanofluid. Based on the thermal function of the nano-diamond, the nanofluid’s thermal conductivity can be significantly improved by the nano-diamond. On the other hand, the interactions of nano-diamond particles and base fluid can increase the turbulent flow and enhance the heat transfer efficiency. In addition, the nano-diamond in the base fluid can increase the boiling nucleus and promote nucleate boiling; in this case, the nano-diamond can enhance the inside energy transfer of the nanofluid. As a result, diamond nanofluid shows great potential for applications to improve the heat transport capacity of GHPs [Citation26].
The mass fraction of the nanofluid and the filling ratio are the key parameters affecting the heat transport capacity of GHP [Citation10,Citation27]. The heat transport capacity of the GHPs filled with the same nanofluid is linked to the different mass fractions. Increasing the nanofluid mass fractions improved GHPs’ heat transport capacity due to the nanoparticle energy exchange rate. When the mass fraction of nanofluid exceeds a threshold, severe boiling may occur during the heat transfer process due to the excessive nucleate boiling caused by nanoparticles, which can make heat transfer capacity worse [Citation28,Citation29]. The GHP filled with nanofluid can operate with the filling ratio (FR) varying from 20% to 80%. While some optimal filling ratio exists, the optimal filling ratio changes according to the kind of nanofluid, mass fraction, or geometry of the GHP. Few robust models predict the optimal filling ratio for a given GHP [Citation10]. Given all that, the investigation of the diamond nanofluid on the heat transport capacity of GHP is still insufficient. In particular, the impact of the diamond nanofluid on the changes of flow patterns and inside heat transfer behavior, as well as the effects of filling ratio and mass fraction on the diamond nanofluid GHP, still needs a deep understanding.
In this article, the nano-diamond is proposed to form the diamond nanofluid, which is supposed to improve the heat transport capacity of the GHP for energy recovery. Section 2 describes the materials and methods involved in the article. In Section 3, the heat transfer behavior of the GHP filled with diamond nanofluid as the working fluid is investigated by observation of the flow patterns. The influences of the filling ratio and mass fraction of diamond nanofluid on flow patterns are studied. In Section 4, an orthogonal experiment is designed and conducted to study the influence degree of filling ratio, mass fraction, and heat flux on the heat transport capacity of GHP. The optimal parameters can also be selected. Finally, the main conclusions are drawn in Section 5.
2. Material and methods
2.1. Diamond nanofluid
Diamond nanofluids are applied in the experiment as the working fluid. The average diameter of the nano-diamond is 50 nm. The nano-diamonds are dispersed in deionized water (DI water) to prepare the diamond nanofluids with different mass fractions. To investigate the effect of the mass fraction on the flow patterns inside GHP, four mass fractions, 0.1, 0.5, 1, 2 w.t.%, are involved in this article. In addition, DI water (can be seen as 0 w.t.% diamond nanofluid) is used as a comparison. Some key thermophysical properties of the diamond nanofluid are listed in .
Table 1. Key thermophysical properties of diamond nanofluids.
The diamond nanofluid is ultrasonically vibrated for 10 min to disperse the nano-diamond uniformly in DI water before filling it to GHPs. The nano-diamond distribution observed by TEM is shown in .
2.2. Experimental setup
The experimental setup consists of a GHP, cooling device, high-speed camera, DC power supply, and data acquisition system (see ). The GHP is made of glass for flow pattern visualization. The glass GHP is 76 mm long, and the inner and outer diameters are 15 mm and 17 mm, respectively. The evaporator of GHP, which is the position of the bottom surface, is placed with a ceramic heating plate connected to the DC power supply. In this case, the GHP is bottom-heated. In the condenser, the GHP is cooled by 0.4 MPa and 0 °C cold air jet generated by a vortex tube. The GHP is placed vertically, promoting the diamond nanofluids condensed at the condenser to flow back to the evaporator driven by gravity.
A data acquisition system includes thermocouples (TCs), PC, and NI DAQ. Two Omega K-type thermocouples are installed on the condenser and evaporator to measure the temperature at those locations. A NI-USB6366 card (at 100 Hz DAQ frequency) acquires data that is processed and analyzed by LabView and DIAdem software. The detailed experimental conditions are listed in .
Table 2. Experimental conditions.
In addition, the environment temperature is kept constant at 20 ± 1°C by the HVAC system. The flow pattern has been recorded by SONY AX700 high-speed camera under the super slow-motion mode. Image acquisition has been done at 1000 fps in the visualization experiments.
2.3. Data processing
The equivalent heat transfer coefficient is used as an important index to characterize the heat transport capacity of GHP. It is defined in EquationEq. (1)(1)
(1)
(1)
(1)
where heff is the equivalent heat transfer coefficient, q” is heat flux, Te and Tc are the average measured temperatures at the evaporator and condenser, respectively. The higher equivalent heat transfer coefficient means better heat transport capacity of GHP.
3. Results and discussion
3.1. Flow pattern of diamond nanofluid
The GHP has different flow patterns under various conditions, which can accordingly reflect the change in the heat transfer capacity of GHP. Through the visualization, typical flow patterns are found in GHP. With increased heat flux, the diamond nanofluid experiences six flow patterns, ie, convective heat transfer, intermittent boiling, bubble flow, slug flow, and churn flow.
When the GHP works under low heat flux, the diamond nanofluid is in the convective heat transfer stage (see ). As the heat flux and temperature increase, the diamond nanofluid at the evaporator begins to generate bubbles. Meanwhile, the high overheat makes the bubbles expanse rapidly and rupture, and causes intermittent boiling. Part of the diamond nanofluid ejects upward and then fills back to the evaporator under the action of gravity, causing violent fluctuations in the liquid pool. The working fluid changes in the motion of intermittent boiling-ejection-backflow, which forms an intermittent boiling cycle (see ).
With the increment of heat flux, the flow pattern of diamond nanofluid will develop into bubble flow (see ). Accordingly, the equivalent heat transfer coefficient increases. And the number of bubbles in the liquid pool and the generation frequency of bubbles increase gradually. Then small bubbles are driven to merge into large bubbles by the elevated temperature, and the large bubbles take the shape of a bullet. This is the characteristic of a slug flow (see ); the equivalent heat transfer coefficient increases with the flow speed and generation frequency of vapor slugs.
As the slug flow grows with the increasing heat flux, the vapor slugs turn into a complex combination of large vapor slugs and bubbles. The flow pattern becomes a churn flow (see ); the generation speeds of the bubbles are accelerated, and the vapor slugs are deformed. The phase change of diamond nanofluid occurs violently. The liquid, vapor slugs, and bubbles show a turbulent and chaotic state. The heat exchange between the evaporator and condenser is enhanced, causing the improvement of heat transport capacity.
3.2. Effect of filling ratio on flow patterns
When GHP is filled with DI water without nano-diamond, the flow patterns evolve from slug flow to bubble flow along with the increase of filling ratio (see ). In terms of diamond nanofluids with varied filling ratios, the flow pattern changes sophisticatedly.
Figure 6. Flow pattern of the GHPs filled with: (a) DI water, (b) 0.5 w.t.%, (c) 1 w.t.%, and (d) 2 w.t.% diamond nanofluids.
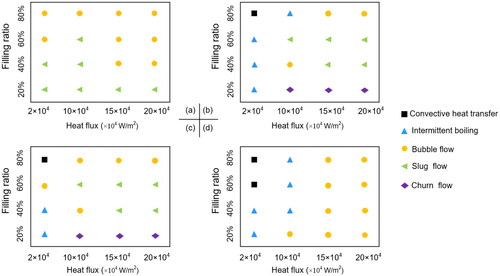
At the filling ratio of 20%, with the increase of heat load, the flow pattern of diamond nanofluid mainly evolves from intermittent boiling to churn flow when the mass fraction is 0.5 w.t.% and 1 w.t.% (see ). The results indicate that due to the low filling ratio of the GHP, the distance from the liquid pool where the bubbles generate and rise to the gas-liquid interface is short, and the continuous phase change accelerates the vapor flow rate. Meanwhile, the high overheat promotes large bubbles growing at the bottom of GHP. It is easy for bubbles to aggregate and deform each other, which leads to generating a churn flow. A circular liquid film with the same diameter as the inner wall is formed (see ). The circular liquid film moves upward by the rising vapor pressure and flows back driven by gravity, which promotes heat transfer in GHP. In this stage, the heat transport capacity of GHP rises.
At the filling ratios of 40% and 60%, the flow pattern turns from intermittent boiling to slug flow as the heat flux increases. Under the low heat flux (< 1 × 105 W/m2) and mass fraction of 0.5 w.t.% and 1 w.t.%, intermittent boiling is the dominant flow (see ). At the filling ratio of 60%, the bubbles generate near the condenser, and heat exchange is stronger. Therefore, its thermal performance is better than that of 40%. At the filling ratio of 80%, bubble flow is dominant under a mass fraction of 0.5 w.t.% and 1 w.t.% (see ). While bubbles are only observed at the gas-liquid interface under the mass fraction of 1 w.t.%, and the heat transfer capacity decreases due to the insufficient heat exchange between the evaporator and condenser (see ).
The flow pattern of GHP with 2 w.t.% diamond nanofluid varies from convective heat transfer to bubble flow at the filling ratio of 20%, and from convective heat transfer to intermittent boiling to bubble flow at the filling ratio of 60% and 80% (see ). As the filling ratio increases, the generation rate of the bubbles decreases; consequently, the thermal performance reduces.
In general, at a high filling ratio, the flow pattern of GHP changes from convective heat transfer to intermittent boiling and then to bubble flow. And it is difficult to form a slug flow. On the contrary, at a low filling ratio, all flow patterns can occur under related mass fraction and heat flux.
3.3. Effect of mass fraction of diamond nanofluid on flow patterns
Experimental results of DI water (0 w.t.%), 0.5 w.t.%, 1 w.t.%, and 2 w.t.% of diamond nanofluid at the filling ratio of 60% are selected to investigate the effect of the mass fraction on flow patterns. Compared with the flow pattern of the GHP filled with DI water, the addition of nano-diamonds improves the thermal performance of the based fluid and promotes the flow pattern to develop. The flow pattern of GHP with DI water is mainly the bubble flow (see ).
The flow pattern of the GHP with a mass fraction of 0.5 w.t.% is intermittent boiling at a low heat flux (< 1 × 105 W/m2). As the heat flux increases, the flow pattern changes to slug flow. Nevertheless, slug flow is dominant under the mass fraction of 1 w.t.%, developed more fully than the GHP with a mass fraction of 0.5 w.t.% (see ). The higher generation position of the vapor slug and larger vapor flow rate in the GHP significantly enhances the heat transfer capacity.
When the mass fraction of diamond nanofluid reaches 2 w.t.%, the flow pattern changes from intermittent boiling to bubble flow, and the corresponding thermal performance deteriorates under such condition (see ). Comparing the effect of different mass fractions on the flow pattern, it is found that the addition of nano-diamond makes the base fluid easier to have nucleate boiling.
In general, with the increase of mass fraction, the heat transport capacity improves first and then decreases. In the low mass fraction condition, the diamond nanofluid’s flow pattern is dominated by slug flow. As the mass fraction increases, the diamond nanofluid’s flow pattern gradually changes into a bubble flow due to competing heat transfer mechanisms inside the nanofluid, namely the heat transfer enhancement effect and the bubble growth retardation effect [Citation30].
From the perspective of enhanced heat transfer by nano-diamond, the nanoparticles have an important influence on the nucleation and growth of bubbles in the working fluids [Citation26]. Compared with DI water, it is easier to nucleate and enhance the energy transfer inside the diamond nanofluids, which is the result of the leading effect of the heat transfer enhancement effect of nano-diamond. At the same time, the deposition of nano-diamond on the surface is more conducive to the wetting characteristics of the liquid on the heating surface, reducing the contact angle between the fluid and the heating surface [Citation30,Citation31], which is conducive to the evaporation of the liquid, forming a slug flow or a churn flow.
As the mass fraction increases, the enhanced heat transfer effect of nano-diamond increases. However, when reaching a certain mass fraction (1–2 w.t.% in this case), the high mass fraction of nano-diamond will increase the viscosity (), in turn, inhibit the transfer of energy in the diamond nanofluid. At the same time, the bubble growth retardation effect starts to play a leading role. Due to the small size effect, the nano-diamond fills the cavities on the heating surface, which reduces the surface roughness and makes the nucleation and boiling of nanofluids more difficult. In addition, because of the deposition of nano-diamond, part of the vapor in the cavity on the heating surface is driven away, which inhibits the growth of bubbles and reduces the growth rate [Citation26,Citation30,Citation31]. The interior of the diamond nanofluid is mainly composed of irregular small bubbles, and the flow pattern is bubble flow. Therefore, the boiling of diamond nanofluids with high mass fraction will deteriorate, and thermal performance will decrease.
4. Orthogonal experiment design
4.1. Experiment plan
Based on the observation of flow patterns in diamond nanofluid gravity heat pipe, different operating parameters (eg, filling ratio, mass fraction of diamond nanofluid, or heat flux) result in different flow patterns, which are related to varied heat transfer capacity. An orthogonal experiment design is conducted to evaluate the influence degree of each factor (ie, filling ratio, mass fraction of diamond nanofluid, and heat flux) on the heat transport capacity of GHP. The software SPSS (Statistical Product and Service Solutions) designs the orthogonal experiment and analyzes the experimental data. According to the factors and levels in , the orthogonal experimental design is arranged as presented in . This article uses an L18 (43) orthogonal table to experiment. The factors, filling ratio, mass fraction of diamond nanofluid, and heat flux, are marked as A, B, and C, respectively.
Table 3. Three factors and the corresponding level values.
Table 4. An L18 (43) orthogonal experimental table.
4.2. Range analysis of experimental data
The influence degree of three factors in the experiment on the heat transfer capacity of GHP is estimated by range analysis which is a method to analyze the results. The experiment results and the range analysis are listed in . An indicator, marked as R, evaluates the influence of the level of each factor on the experiment results. The larger the R-value, the greater the effect of the level change in this factor on the experimental index (equivalent heat transfer coefficient in this case) [Citation32]. In this experiment, the increasing R-value indicates that a change in the value of the factor within the experimental range will lead to a larger change in the value of the experiment index [Citation33]. R can be calculated by EquationEq. (2)(2)
(2) ,
(2)
(2)
where R denotes the range value of each factor; Ki indicates the sum of the corresponding experiment results of a factor at all levels i (i = 1, 2, 3, or 4). The larger the R-value of a factor, the greater variation the performance indices have in value within the experiment range. And the factor with the largest R-value is the most influential one on the experiment results [Citation32,Citation33].
Table 5. Experiment results and range analysis.
The range analysis results figure that the order of influence degree for equivalent heat transfer coefficient is Heat flux (C) > Filling ratio (A) > Mass fraction of diamond nanofluid (B), correspondingly (see ). To sum up, the impact of the heat flux on the thermal performance of the gravity heat pipe is the most significant, followed by the filling ratio and mass fraction of the diamond nanofluid. Value ki can be calculated by EquationEq. (3)(3)
(3) ,
(3)
(3)
where s indicates the number of times which each level of each factor occurs (s = 4 in this case); ki indicates the mathematical average value of the corresponding indexes of a factor at each level i (i = 1, 2, 3, or 4). The trend reflects the relationship between factors and indicators. In the trend, the X-axis is the levels of the factor in order of size, and the mean value of the experiment index, ki, is on the Y-axis (see ) [Citation32–34].
Figure 7. Various trends in the mean values of equivalent heat transfer coefficient under different factor levels.
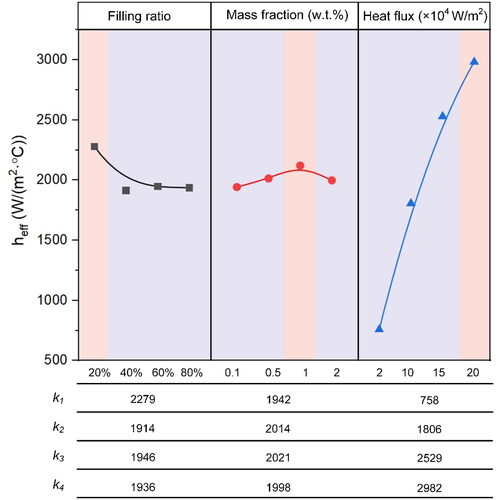
The equivalent heat transfer coefficient rapidly increases from 758 W/(m2·°C) to 2982 W/(m2·°C) as heat flux increases from 2 × 104 W/m2 to 20 × 104 W/m2 (see ). The trend presents a positive correlation between the equivalent heat transfer coefficient and the heat flux. By contrast, the equivalent heat transfer coefficient shows a decreasing trend with the increase in the filling ratio. The equivalent heat transfer coefficient drops rapidly when the filling ratio increases from 20% to 40%. When the filling ratio further increases to 80%, the equivalent heat transfer coefficient decreases slowly. The curve reaches the lowest point, meaning the GHP at the filling ratio of 40% has the worst heat transfer capacity (see ). The mass fraction of diamond nanofluid has the smallest influence on the equivalent heat transfer coefficient, reflecting the heat transfer capacity of the GHP. However, it shows a different trend from the other factors. With the mass fraction of diamond nanofluid increasing from 0.1 w.t.% to 1 w.t.%, the equivalent heat transfer coefficient increases by 4%. And the GHP has the beat heat transfer capacity in this condition of 1 w.t.% mass fraction. While the heat transfer capacity of the GHP deteriorates as the mass fraction of diamond nanofluid increases up to 2 w.t.%. The equivalent heat transfer coefficient decreases from 2021 W/(m2·°C) to 1998 W/(m2·°C) (see ). The result is similar to the characteristics flow pattern according to visualization.
According to the experiment analysis, the experiment parameters that correspond to the best heat transfer capacity are the filling ratio of 20%, the mass fraction of 1 w.t.% diamond nanofluid, and the heat flux of 20 × 104 W/m2. These are the preferred experimental parameters. When the filling ratio is 20%, the GHP filled with the mass fraction of 1 w.t.% diamond nanofluid has the best heat transfer capacity in the condition of the 20 × 104 W/m2 heat flux. The equivalent heat transfer coefficient is 3485 W/(m2·°C).
5. Conclusion
In this article, the diamond nanofluid, which disperses nano-diamond into deionized water, is used as the working fluid of a gravity heat pipe to enhance heat transfer for waste heat recovery. The diamond nanofluid’s heat transfer behavior is studied by observing the flow patterns. The orthogonal experiment and range analysis investigate the influence of filling ratio, mass fraction of diamond nanofluid, and heat flux on the heat transfer capacity. The main conclusions can be drawn as follows.
With the filling ratio of the GHP increases, the flow pattern of the 0.5 w.t.% mass fraction of the diamond nanofluid changes from churn flow to slug flow and then to bubble flow, as well as the 1% mass fraction of the diamond nanofluid. And the flow pattern of the 2 w.t.% mass fraction of the diamond nanofluid is mainly bubble flow. When the filling ratio rises, the heat transfer capacity decreases, caused by the low generation rate of the bubbles and the vapor flow rate. It will be difficult for the GHP with diamond nanofluid at a high filling ratio to generate slug flow, and the heat transport capacity decreases.
Under the condition of 0.5 w.t.% and 1 w.t.% mass fraction, the flow pattern of diamond nanofluid is dominated by slug flow. With the 2 w.t.% mass fraction, the flow pattern of diamond nanofluid changes to bubble flow. The heat transfer capacity increases when the mass fraction of the diamond nanofluid increases from 0.5 w.t.% to 1 w.t.%, then decreases when the mass fraction reaches 2 w.t.%. It is found that the addition of nanoparticles can make based fluid easier to nucleate and enhance the energy transfer inside the diamond nanofluids, which is caused by the leading effect of the nano-diamond heat transfer enhancement effect. The enhanced heat transfer effect of nanoparticles increases with the mass fraction. When reaching 2 w.t.% mass fraction, the nano-diamond nanoparticles will inhibit energy transfer in the diamond nanofluid for the excessively high fluid viscosity.
While the equivalent heat transfer coefficient shows a positive relationship with the heat flux and a negative relationship with the filling ratio. As the heat flux increases from 2 × 104 W/m2 to 20 × 104 W/m2, the equivalent heat transfer coefficient rapidly increases from 758 W/(m2·°C) to 2982 W/(m2·°C). And when the filling ratio increases from 20% to 80%, the equivalent heat transfer coefficient drops by 14%–16%. The thermal performance of the GHP is enhanced as the mass fraction of diamond nanofluid is lower than 1 w.t.%. The thermal performance of the GHP deteriorates when the mass fraction of diamond nanofluid increases up to 2 w.t.%. When the filling ratio is 20%, the GHP filled with the mass fraction of 1 w.t.% diamond nanofluid has the best heat transfer capacity in the condition of the 20 × 104 W/m2 heat flux. The equivalent heat transfer coefficient is 3485 W/(m2·°C).
Additional information
Funding
References
- Olabi AG, Elsaid K, Rabaia MKH, et al. Waste heat-driven desalination systems: perspective. Energy. 2020;209:118373.
- Mahmoudi A, Fazli M, Morad MR. A recent review of waste heat recovery by organic rankine cycle. Appl Therm Eng. 2018;143:660–675.
- Olabi AG, Abdelkareem MA. Renewable energy and climate change. Renew Sustain Energy Rev. 2022;158:112111.
- Jouhara H, Sayegh MA. Energy efficient thermal systems and processes. Therm Sci Eng Prog. 2018;7:e1–2–e2.
- Olabi AG, Obaideen K, Elsaid K, et al. Assessment of the pre-combustion carbon capture contribution into sustainable development goals SDGs using novel indicators. Renew Sustain Energy Rev. 2022;153:111710.
- Tabbi W, Olabi AG, Imran M, et al. Recovery of waste heat from proton exchange membrane fuel cells – a review. Int J Hydrogen Energy. 2022. https://doi.org/10.1016/j.ijhydene.2022.08.069
- Yang P, Peng S, Benani N, et al. An integrated evaluation on china’s provincial carbon peak and carbon neutrality. J Clean Prod. 2022;377:134497.
- Reay D, Harvey A. The role of heat pipes in intensified unit operations. Appl Therm Eng. 2013;57(1–2):147–153.
- Hassan MI, Alzarooni IA, Shatilla Y. The effect of water-based nanofluid incorporating Al2O3 nanoparticles on heat pipe performance. Energy Procedia. 2015;75:3201–3206.
- Zhang T, Cai J, Wang L, et al. Comparative and sensitive analysis on the filling, operating and performance patterns between the solar gravity heat pipe and the traditional gravity heat pipe. Energy. 2022;238:121950.
- Amir F. Heat pipes: review, opportunities and challenges. Front Heat Pipes. 2014;5(1):1–48.
- Kim JS, Kim Y, Shin DH, et al. Heat transfer and flow visualization of a two-phase closed thermosiphon using water, acetone, and HFE7100. Appl Therm Eng. 2021;187:116571.
- Abdelkareem MA, Maghrabie HM, Sayed ET, et al. Heat pipe-based waste heat recovery systems: background and applications. Therm Sci Eng Prog. 2022;29:101221.
- Ma H, Du N, Zhang Z, et al. Assessment of the optimum operation conditions on a heat pipe heat exchanger for waste heat recovery in steel industry. Renew Sustain Energy Rev. 2017;79:50–60.
- Jouhara H, Bertrand D, Axcell B, et al. Investigation on a full-scale heat pipe heat exchanger in the ceramics industry for waste heat recovery. Energy. 2021;223:120037.
- Ramkumar P, Sivasubramanian M, Raveendiran P, et al. An experimental inquisition of waste heat recovery in electronic component system using concentric tube heat pipe heat exchanger with different working fluids under gravity assistance. Microprocess Microsyst. 2021;83:104033.
- Chen J, Huang W, Cen J, et al. Heat extraction from hot dry rock by super-long gravity heat pipe: selection of working fluid. Energy. 2022;255:124531.
- Gedik E, Yilmaz M, Kurt H. Experimental investigation on the thermal performance of heat recovery system with gravity assisted heat pipe charged with R134a and R410A. Appl Therm Eng. 2016;99:334–342.
- Savino R, Abe Y, Fortezza R. Comparative study of heat pipes with different working fluids under normal gravity and microgravity conditions. Acta Astronaut. 2008;63(1–4):24–34.
- Nazari MA, Ahmadi MH, Sadeghzadeh M, et al. A review on application of nanofluid in various types of heat pipes. J Cent South Univ. 2019;26(5):1021–1041.
- Yilmaz Aydin D, Gürü M, Sözen A, et al. Investigation of the effects of base fluid type of the nanofluid on heat pipe performance. Proc Inst Mech Eng Part A J Power Energy. 2021;235(1):124–138.
- Borode AO, Ahmed NA, Olubambi PA. A review of heat transfer application of carbon-based nanofluid in heat exchangers. Nano-Struc Nano-Obj. 2019;20:100394.
- Khanlari A, Yılmaz Aydın D, Sözen A, et al. Investigation of the influences of kaolin-deionized water nanofluid on the thermal behavior of concentric type heat exchanger. Heat Mass Transfer. 2020;56(5):1453–1462.
- Alawi OA, Sidik NAC, Mohammed HA, et al. Fluid flow and heat transfer characteristics of nanofluids in heat pipes: a review. Int Commun Heat Mass Transf. 2014;56:50–62.
- Sang L. Diamond as the heat spreader for the thermal dissipation of GaN-based electronic devices. Funct Diam. 2021;1(1):174–188.
- Alshayji A, Asadi A, Alarifi IM. On the heat transfer effectiveness and pumping power assessment of a diamond-water nanofluid based on thermophysical properties: an experimental study. Powder Technol. 2020;373:397–410.
- Aydın DY, Aydin E, Gürü M. The effects of particle mass fraction and static magnetic field on the thermal performance of NiFe2O4 nanofluid in a heat pipe. Int J Therm Sci. 2023;183:107875.
- Sundar LS, Shaik F. Heat transfer and exergy efficiency analysis of 60% water and 40% ethylene glycol mixture diamond nanofluids flow through a shell and helical coil heat exchanger. Int J Therm Sci. 2023;184:107901.
- Chen J, Cen J, Huang W, et al. Multiphase flow and heat transfer characteristics of an extra-long gravity-assisted heat pipe: an experimental study. Int J Heat Mass Transf. 2021;164:120564.
- Xuan Y, Li Q, Tie P. The effect of surfactants on heat transfer feature of nanofluids. Exp Therm Fluid Sci. 2013;46:259–262.
- Ma H, He B, Su L, et al. Heat transfer enhancement of nanofluid flow at the entry region of microtubes. Int J Therm Sci. 2023;184:107944.
- Liao M, Jin R, Ren H, et al. Orthogonal experimental design for the optimization of four additives in a model liquid infant formula to improve its thermal stability. LWT-Food Sci Technol. 2022;163:113495.
- Kang P, Zhao Q, Guo S, et al. Optimisation of the spark plasma sintering process for high volume fraction SiCp/Al composites by orthogonal experimental design. Ceram Int. 2021;47(3):3816–3825.
- Li J, Yang F, Zhang H, et al. Comparative analysis of different valve timing control methods for single-piston free piston expander-linear generator via an orthogonal experimental design. Energy. 2020;195:116966.