Abstract
Zirconium diboride (ZrB2) ceramic possesses a unique combination of nice mechanical performance, high melting point (> 3000 °C) and great high-temperature oxidation resistance (up to 1600 °C), which makes it a promising material system for ever-increasing ultra-high temperature (UHT) applications. However, ZrB2 suffers from poor mechanical performance at UHTs, which could strongly limit its applications at UHT. Here, we successfully demonstrate that texturing is an effective strategy to greatly enhance the flexural strength of monolithic ZrB2, reaching a high value of 810 ± 60 MPa at 1600 °C when loaded in c-axis direction. We thoroughly discuss the strengthening mechanism by in-depth microstructural observations and analysis. Our discovery has technological and scientific implications for other UHT ceramic systems, especially those using ZrB2 as a matrix.
Introduction
Zirconium diboride (ZrB2) is an ultra-high temperature ceramic (UHTC) with a melting temperatures in excess of 3000 °C [Citation1]. The high flexural strength (500–1000 MPa) and good oxidation resistance (∼ 1600 °C) make ZrB2-based UHTCs suitable for a variety of applications such as thermal protection systems for hypersonic aerospace vehicles, refractory linings or molten metal crucibles [Citation2–Citation4].
In realization of these applications in extreme environments, high temperature flexural strength, as an important aspect to evaluate the load-carrying capacity of materials at the service temperatures, has received increasing attention [Citation5–Citation11]. Kalish et al [Citation5] studied the flexural strength and the fracture mode of the fully densified ZrB1.89 with a grain size of 9 μm from room temperature to 1400 °C. Neuman et al [Citation11] measured the flexure strengths up to 2300 °C with atmosphere control of fully densified ZrB2 with a grain size of ∼19 μm produced by hot pressing. It was found that the high temperature strength of ZrB2 dropped down rapidly when test temperature was over 1000 °C.
It is well known that the degradation of flexural strength of ceramics at elevated temperature always relates to the softening of grain boundary or secondary phase. Efforts have been made to modify the volume and composition of the grain-boundary phase to overcome these problems. Since the addition of SiC as secondary phase has been proved to increase the room temperature bending strength from ∼500 MPa to >1 GPa [Citation12, Citation13], most of the recent works are focusing on the ZrB2–SiC composites. Bellosi et al [Citation6] indicated that the spark plasma sintering (SPS) technique favors retaining the strength of the ZrB2–10 vol% SiC ceramics at 1500 °C. Hu and Wang [Citation7] reported that ZrB2–SiC ceramics consisting of coarser grains were stronger at 1800 °C, because grain boundary sliding was suppressed by the large grains. Zou et al [Citation8, Citation10] found that the purity of the raw powders and the additives (WC and ZrC) could strongly affect the high temperature strength of ZrB2–SiC materials by controlling the grain boundary phases and the fracture mode. By adding 5% WC to remove the oxide impurities during densification, the average flexural strength tested at 1600 °C was as high as 675 MPa, which was 111.5% of its flexural strength at room temperature.
Previous studies suggest that the mechanical behavior of ZrB2 ceramics at elevated temperature is strongly affected by a series of parameters. Not only the grain size and the second phase, but also the sintering additives as well as the sintering method can change the high temperature performance of ZrB2-based materials. Besides, anisotropic mechanical behavior of textured ZrB2-based ceramics with a hexagonal crystal structure (AlB2-type, P6/mmm space group) is attractive to improve the mechanical properties depending on the crystal planes [Citation14–Citation17].
Textured ceramics with non-cubic crystal structure can be fabricated by applying a strong magnetic field during colloidal processing [Citation18, Citation19]. Why the feebly magnetic ceramics can be oriented in a strong magnetic field can be explained on the basis of their anisotropy. Anisotropy in the non-cubic unit cells of these materials introduces anisotropy in several properties like magnetic susceptibility. This anisotropic magnetic susceptibility will generate a torque given by (see [Citation20])
1
where Δχ(= |χa,b − χc|) is the anisotropy of the magnetic susceptibilities measured for the a, b-axis (χa,b) and c-axis (χc), V is the volume of the material, B is the applied magnetic field, is the angle between the easy magnetization axis in the crystal and the imposed magnetic field direction, and μ0 is the permeability in vacuum. The magnetic torque is the driving force for the magnetic alignment. It rotates the particles to an angle with the applied magnetic field to minimize the system energy. The fact that the values of magnetic susceptibilities of the ceramics are quite low (e.g. measured χc and χa,b for ZrB2 is 0.094 × 10−4 cm3 mol−1 and −0.671 × 10−4 cm3 mol−1, respectively [Citation21]) is taken care of by the application of a high magnetic field (∼ 12 T). Considering the average size of ZrB2 particles in suspension is ∼2 μm in diameter and fixing the angle equals to π/4 to maximize the value of sin 2, we have estimated the magnetic torque in the magnitude of ∼10−15N m in the applied high magnetic field (∼ 12 T). In colloidal processing, the particles are immersed in a liquid medium. Hence, a balance between the magnetic and the hydrodynamic torque is essential for the particle orientation. According to previous experiences, for optimizing the alignment results, two necessary conditions should be considered: the magnetic field is large enough to overcome the thermal motion and the viscosity of suspension should be low. For texturing ZrB2, the optimized suspension parameters for slip casting were determined as 20 vol% ZrB2 and 1.5 wt% polyethyleneimine (PEI) dispersant of powder in the ethanol or in water, which contributed to the low viscosity of suspension. It was confirmed that the c-axis of ZrB2 particles was parallel to the 12 T magnetic field direction [Citation14, Citation16].
In the present study, textured and non-textured ZrB2 ceramics with 5 vol% of B4C were prepared by slip casting with or without a strong magnetic field, followed by SPS. The introducing of B4C as additive can minimize grain coarsening and promote the densification by removing the surface oxides of ZrB2 powder [Citation22]. In addition, SPS owns its inherent advantages of faster densification, lower sintering temperature, and higher energy activity in comparison to the conventional hot pressing technique [Citation23, Citation24]. X-ray diffraction (XRD), scanning electron microscopy (SEM) and transmission electron microscopy (TEM) methods were used to characterize the texturization and microstructure of the sintered samples. The high-temperature flexural strength and fracture behavior were investigated up to 1650 °C and the fracture mechanism of the textured and non-textured ZrB2 ceramics was discussed.
Experimental procedures
Commercial ZrB2 (99%, 2 μm, Rare Metallic Co., Ltd, Japan) and B4C (99%, 2–5 μm, Japan New Metals Co., Ltd, Japan) powders were used as the starting materials. A stable ZrB2 slurry with a 20 vol% solid concentration was prepared by ball milling for 24 h in a plastic bottle with Si3N4 balls (diameter: 5 mm). Ethanol was used as the solvent, and PEI (MW = 10 000 g mol−1, Wako Pure Chemical Industries, Ltd, Tokyo, Japan) was used as the dispersant. The amount of PEI was fixed at 1.5 wt% based on the total weight of the powders. About 2.5 wt% Si3N4 impurity was imported during the ball milling of the raw powders. Slip casting was performed by using a glass tube (inner diameter: 30 mm; height: 15 mm) setting on a porous Al2O3 block in the 12 T magnetic field. The direction of the magnetic field was parallel to the slip casting direction. After consolidation, the drying was achieved in a vacuum oven at 110 °C, followed by cold isostatic pressing at 392 MPa. The green bodies were calcined at 700 °C for 30 min in vacuum to burn out the polymer dispersant before sintering. The sintering was conducted in an SPS furnace (100 kN SPS-1050, Syntex Inc., Japan) at a heating rate of 50 °C min−1 under a pressure of 50 MPa in vacuum. The sintering temperatures were 1700 and 1750 °C with a holding time of 5 min.
The analyses of phase and crystallographic orientation of the green and sintered bodies were conducted on each surface of the samples using XRD (Model RINT 2500, Rigaku Co., Tokyo, Japan, Cu Kα radiation, 40 kV, 300 mA). The degree of texture was evaluated on the basis of the Lotgering orientation factor f(00l) = (P − P0)/(1 − P0) [Citation25]. The values of P and P0 were calculated from the ratio ∑ I(00l) /∑ I (hkl) for the c-axis orientation, where ∑ I(00l) and ∑ I (hkl) were the sums of the peak intensities of the (00l) and (hkl) planes, respectively. P0 was evaluated from the standard JCPDS card (65–7806) of ZrB2. The data from the textured sample were used to calculate P.
Density values were calculated from Archimedes’ measurements using deionized water as the immersion medium. The Vickers hardness was measured by the indentation method using a load of 1 kg on a polished surface for 15 s using a micro-hardness tester (MVK-E, Akashi Co., Japan). The Young's modulus was evaluated by an ultrasonic setup (TDS 3034B, Tektronix Inc., USA). The fracture strength from room temperature to 1650 °C was measured by a mechanical strength testing system (Model 4505, Instron Corp., MA) in four-point loading (inner span 10 mm, outer span 20 mm and crosshead speed 0.5 mm min−1) on rectangular bars (2 mm × 2.5 mm × 25 mm) which were cut from the billet and machined finally with a 1000-grit diamond grinding wheel. The tensile surfaces were perpendicular to the SPS-direction and all of the tests were conducted in argon. The tests at high temperatures were performed after a dwell time of 20 min to ensure a homogeneous temperature during testing. The reported flexural strengths were the average of five specimens for room temperature and of three specimens for high temperatures.
The microstructure was observed by SEM (JSM-6500F, JEOL Ltd, Japan). The grain size of ZrB2 was measured and calculated using the Image-Pro Plus Version 6.0 software. About 100 grains were measured for each value. The chemical composition of the oxide scale was characterized by electron probe x-ray micro-analysis (JEOL JXA-8100F, Japan) with wavelength-dispersive spectroscopy and TEM (JEM-2100, JEOL Ltd, Japan) equipped with an energy dispersive spectroscopy system. After the flexural strength measurement at different temperatures, the tension surfaces of the sample bars were polished to <100 μm. The obtained thin foils were ion-milled (Ion Slicer, EM-09199IS, JEOL Ltd, Japan) and then observed by TEM.
Results
Microsructure and texturization
Figure shows the XRD patterns of the textured and non-textured ZrB2 ceramics sintered by SPS at 1750 °C. It is observed that the ZrB2 particles are well orientated in the strong magnetic field. On the top surface (TS, perpendicular to the magnetic direction), the main diffraction peaks are (00l) planes; on the side surface (SS, parallel to the magnetic direction), the main diffraction peaks belong to (110) and (10l) planes. The Lotgering orientation factor f(00l) used to evaluate the degree of the c-axis texture in the samples is 0.92 for the textured ZrB2 sample in the present study.
Figure 1 XRD patterns of (a) non-textured surface, (b) textured SS and (c) textured TS of ZrB2 samples after sintering.
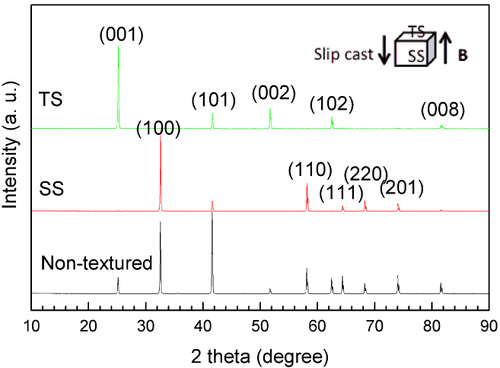
The measured densities, open porosities and ZrB2 grain sizes of the sintered samples are listed in table , and the morphology of starting ZrB2 powder and the microstructures of the polished surfaces are shown in figures and , respectively. There is no obvious morphology difference between the SS and the TS of textured ZrB2 ceramics sintered at 1750 °C (figures (a) and (b)). Most of the grains exhibit an equiaxial shape and the grain sizes for the two surfaces are 2.5 and 2.4 μm, respectively. The average ZrB2 particle size increased to 5.8 μm for the non-textured ZrB2 ceramics sintered at the same temperature (figure (c)). The grain morphology also changed from faceted to spherical, indicating an over-sintering at this temperature. Decreasing the sintering temperature to 1700 °C leads to the refinement of the microstructure (figure (d)).
Table 1 Sintering temperature, densities, open porosities and ZrB2 grain sizes of the sintered ZrB2 ceramics.
Figure 3 SEM images of polished surfaces for textured ZrB2 ceramics sintered at 1750 °C: (a) TS, (b) SS; and non-textured ZrB2 sintered at (c) 1750 °C and (d) 1700 °C.
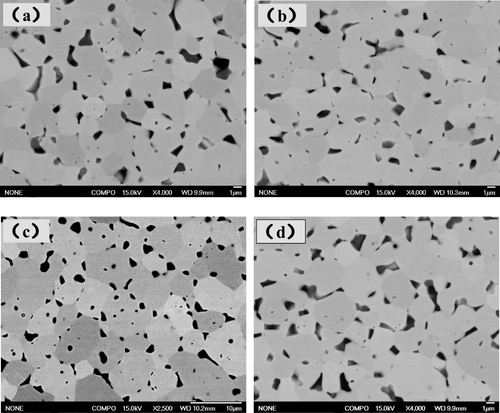
Compared to the theoretical value of 5.92 g cm−3, the lower densities may be attributed to the existence of secondary phases. Figure shows the images and compositional maps of the polished surface of non-textured ZrB2 sintered at 1750 °C for 5 min. Instead of B4C, the submicron secondary phase located homogenously at the triple points of the ZrB2 grains consists of plate-like BN grains and spherical SiC particles, with Si–O containing phase filling in the rest space of the pockets. The formation of BN and SiC could be derived from the reactions of B4C and Si3N4 introduced by milling balls with the oxide impurities from starting powders through the following reactions (Equation22 )–(Equation4
4 ).
2
3
4
Figure 4 SEM image (top left) and compositional maps of the polished surface of non-textured ZrB2 sintered at 1750 °C for 5 min.
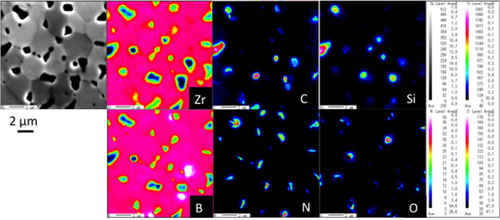
Figure shows typical TEM pictures of the ZrB2 ceramics studied in this work. High-resolution images (panels (a) and (b)) reveal that all the observed matched and mismatched ZrB2/ZrB2 grain boundaries are very clean. The secondary phase is constrained in isolated triple points without interconnect. A typical microstructure of these secondary phases is shown in figure (c). According to the detailed microstructure analysis of ZS material conducted by TEM, the phase between the BN flakes and the matrix grains is an amorphous Zr–Ca–Al–Y–Si–O phase (figure (d)), which may come from the impurities introduced by the milling balls of Si3N4, since CaO, Al2O3 and Y2O3 are usually added for the densification of Si3N4.
Vickers hardness and Young's modulus at room temperature
The mechanical properties of the textured and non-textured ZrB2 are summarized in table . The crystal structure of ZrB2 is composed of layers of B atoms in two-dimensional graphite-like rings or nets, which alternate with hexagonally close-packed Zr layers. Generally, the combination of bonds (Zr–Zr, B–B and Zr–B) influences the material properties and the anisotropy in properties. [Citation13] Although it is reported that the bonding in ZrB2 is isotropic, [Citation26] large difference in elastic modulus was observed between the c-axis and a, b-axis direction. The Young's modulus at room temperature is 463 ± 16 GPa for textured ZrB2 in c-axis direction, which is lower than 505 ± 10 GPa for the other directions and close to 463 ± 26 GPa for non-textured ZrB2. This characteristic behavior is observed in materials with layered structures, in which the bonding between (00l) planes is much weaker than in other directions in the crystal. Vickers hardness measurement reveals that c-plane has higher hardness than the a-plane, which is consistent with the results reported on the micro-hardness in the case of ZrB2 crystals [Citation27]. This can be attributed to the close-packed structure and the strong B–B covalent bonding in c-plane.
Table 2 Vickers hardness, Young's modulus and flexural strength at various conditions.
Flexural strength at room and elevated temperatures
The flexural strength and fracture behavior of the ZrB2 materials at both room and elevated temperatures significantly depend on the grain size. Flexural strength values of all the sintered materials are summarized in table and plotted in figure . For the data of non-textured ZrB2, smaller grain size is thought to be the main reason for the higher strength of the sample sintered at 1700 °C (ZB1700, 600 ± 97 MPa, 2.8 μm) than the one sintered at 1750 °C (ZB1750, 460 ± 59 MPa, 5.8 μm) at room temperature. The flexural strengths of ZB1750, ZB1700 at 1600 °C are 428 ± 61 and 748 ± 5 MPa, respectively. No obvious strength degradation of ZrB2 with coarse grains is detected with the test temperature increasing to 1600 °C, and 92.9% of its fracture strength measured at room temperature is maintained. Our values are comparable to the reported data for hot pressed ZrB2–SiC composites with a ZrB2 grain size of 6.1 μm [Citation9] and are much higher than those of ZrB2 ceramics with coarser ZrB2 grains of 19.4 μm [Citation11]. Furthermore, it is interesting to note that the strength of the fine ZB1700 (748 ± 5 MPa) at 1600 °C is 24.6% higher than that measured at room temperature.
Figure 6 Flexural strength of textured and non-textured ZrB2 ceramics at room and elevated temperatures.
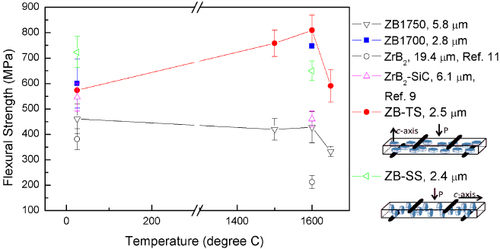
Textured ZrB2 ceramics with a grain size similar to that of ZB1700 revealed a similar behavior but larger improvement both at room and elevated temperature when the load surface is c-plane. The values of flexural strength at 1500 and 1600 °C for ZB-TS are 758 ± 52 and 810 ± 60 MPa, respectively, which are 132.2 and 141.1% of the strength measured with the same sample at room temperature (574 ± 31 MPa), respectively. These values are the highest reported ones for ZrB2-based materials at such high temperatures. However, while the highest room temperature strength of 723 ± 61 MPa was obtained from ZB-SS, for which the load is perpendicular to the c-axis direction during the testing, the strength at 1600 °C did not reveal such an increase but exhibited a drop to 650 ± 38 MPa.
Figure shows load–displacement curves of the flexural-strength tests of ZrB2 ceramics from room temperature to 1650 °C. No plastic deformation before fracture was observed in ZB1750, with a load/displacement plot remaining completely linear up to 1650 °C. The slope of the line, which can be used to calculate the Young's modulus of the materials, was almost constant until 1600 °C. Little plastic deformation prior to fracture with gradually reduced Young's modulus against time at 1600 °C was found in ZB-TS, while obvious plastic deformation occurred in ZB-SS at the same temperature. Such observations demonstrate that ZrB2 ceramics consisted of coarser grains have better creep resistance up to 1650 °C, as previously reported by Hu and Wang [Citation7] However, the low plastic deformation is not necessarily related to the high flexural strength. The sequence of the resistance in plastic deformation at high temperature is ZB1750 > ZB-TS > ZB-SS, while the sequence of high temperature strength is ZB-TS > ZB1700 > ZB-SS > ZB1750 at 1600 °C. Further increasing the test temperature to 1650 °C leads to dramatic strength degradation for both ZB1750 and ZB-TS, indicating a transition of fracture behavior at this temperature unrelated to the grain size.
Figure 7 Load–displacement curves of the flexural strength tests of ZrB2 ceramics from room temperature to 1650 °C.
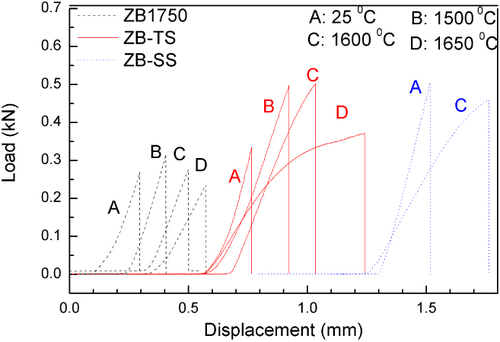
Examination of room-temperature fracture surface of both ZB1750 and ZB-1700 (figures (a) and (c)) revealed a fully transgranular mode of fracture, suggesting that the intergranular strength is higher than intracrystalline strength in the sintered samples, which could be attributed to the suppression of crack extension along the grain boundaries by the strong bonding at clean ZrB2/ZrB2 interfaces, as shown in figures (a) and (b). The fracture surfaces of the specimen exhibit a typical fracture of brittle materials (see insets of figures (a) and (c)), and a rough region can be observed starting from the tensile surface.
Figure 8 Tension side fracture surfaces of ZrB2 ceramics after flexural strength testing at room and high temperature. (a) ZB1750, room temperature (RT), (b) ZB1750, 1600 °C, (c) ZB1700, RT and (d) ZB1700, 1600 °C.
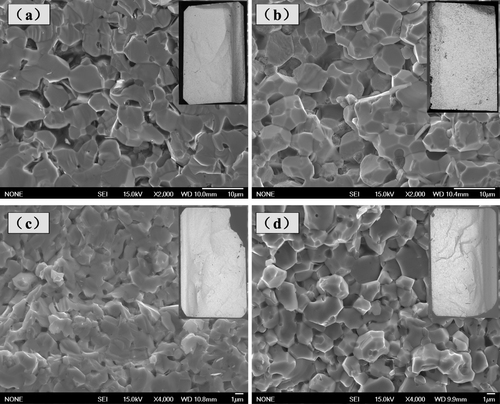
As the testing temperature increased to 1600 °C, the fracture mode of ZB1750 changed into completely intergranular with smooth fracture surface (figure (b)). No evidence of subcritical crack growth was found. In contrast, the corresponding fracture surfaces of ZB1700 demonstrated a transgranular/intergranular mode, in which the fracture surface is rather rough with several cracks radiating from the tension surface. According to Kalish et al [Citation5] and Zou et al [Citation8, Citation9] the decrease in percentage of intergranular fracture with increasing the test temperature is accompanied by an increase in flexural strength. Three reasons for the significant increasing in high temperature strength can be accounted to: (i) the crack healing on the tensile surfaces of bars during the high temperature test; (ii) the releasing of residual stresses from high-temperature forming as the forming temperature being re-approached.
According to the first reason, enhancement is only available when the testing temperature is lower than the softening temperature of grain boundary phase (normally <1400 °C for silicate glassy phases). As for the second, possible enhancement for all the samples with the same processing procedure should be observed, however, only parts of specimens in present work show such enhancement. Therefore, none of the reasons could explain the difference of fracture behavior between the room and elevated temperature up to 1650 °C in the present study independently, and none can explain the different behavior between the two directions of the textured ZrB2 ceramics.
High temperature fracture in ceramics frequently involves the nucleation, growth and coalescence of grain boundary located micro-cracks or cavities [Citation28]. The microstructure of the present study is an equiaxed grain structure with no grain boundary phase but seldom BN flakes and amorphous phase confined to the three-grain or four-grain junctions, as shown in figures and . In this case, cavities are presumed to nucleate primarily near grain triple points as a result of grain boundary sliding, then extend along grain boundaries and coalesce until sufficient contiguous boundaries have cavitated that a macro-crack develops which is capable of self-extending to failure [Citation29]. However, the grain boundary sliding is largely suppressed by the strongly bonded ZrB2/ZrB2 interface, indicating that the cavity initiation stage is the governing step in the fracture process. As can be seen in figure , cavities in the amorphous silica phase at the triple points were not generated until the testing temperature increased to 1600 °C (figure (e)). Once the cavities formed, the amorphous phase contained near the cavity tip will promote the coalescence by providing a rapid atom migration path, leading to the fracture behavior in an intergranular mode. As shown in figure (g), by increasing the testing temperature by only 50 °C, the isolated cavities became inter-connected. This enhanced crack growth at 1650 °C also explains the reason for the dramatic degradation of strength in all the tested samples at this temperature.
Figure 9 Bright-field TEM images show the successive growth of cavities at adjacent locations and the evolution of dislocations in tension surfaces of ZB1700 tested at different temperature. (a), (b) RT; (c), (d) 1500 °C; (e), (f) 1600 °C; (g), (h) 1650 °C. The white solid arrows indicate dislocations, the dashed arrows indicate sub-grain boundaries and the black solid arrows indicate the cavities formed at the triple points.
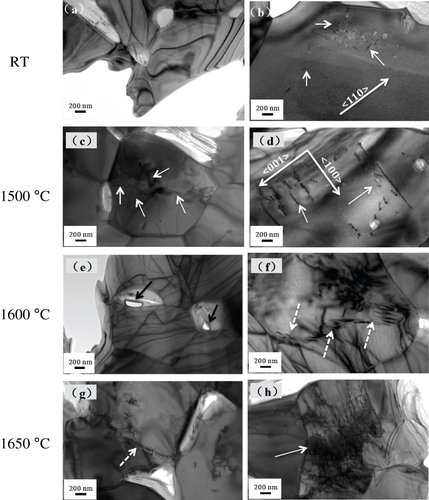
On the other side, while the testing temperature is under 1600 °C, no inter-connected cavities are located at the boundary and the high stresses generated by the external load cannot be relaxed by grain boundary sliding. As a result, the elastic stress will be accommodated by plastic deformation inside the ZrB2 grains. The dislocation formed during the plastic deformation may induce crack initiation and subsequently fracture in a transgranular mode at elevated temperature. According to the Griffith criterion, the fracture of brittle ceramics is governed by the propagation of a critical crack. When the stored elastic energy for crack extension is balanced by the surface free energy for creating two new surfaces, the large energy absorbing process during the plastic deformation will increase the required fracture strength for rupture. This consideration is supported by the dislocation evolution in ZB1700 as the testing temperature increased. While only small amount of dislocations can be found in the sample tested at room temperature (figure (b), the increase of dislocation density at 1500 °C (figure (d)) and the formation of sub-grain boundary at 1600 °C is accompanied by an increase of the flexural strength (dashed arrow in figure (g)). At 1600 °C, as shown in figure (h), the interconnection between the defects may increase the plastic deformation.
The plastic deformation inside the ZrB2 grains can also explain the anisotropic flexural strength for the textured ZrB2 ceramics. Direction of grains in ZB-TS is parallel to the tensile stress on the tensile surface, which is the longitudinal direction of specimen. This means that grains near tensile surface can bear the tensile stress with shear between grain and grain boundary. By studying the plastic deformation of ZrB2 single crystals, Haggerty and Lee [Citation29] found that slip occurred in a-direction on prismatic planes at room temperature and on the basal plane at high temperatures. Regions exhibiting parallel sets of long, straight dislocations (figure (d)) can be easily found in the sample that tested at 1500 °C. Trace analysis based on electron diffraction patterns shows that the dislocations lie parallel to a <100 > direction and the force load parallel to the alignment direction of texture could be released in ZB-TS. For the ZB-SS, the force was loaded on the surface perpendicular to the c-plane during the tests, and the tensile stress is borne by attractive stress between grains. Therefore, lower strength and higher fracture displacement of ZB-SS than ZB-TS at 1600 °C could be expected.
Conclusions
Highly textured ZrB2 and non-textured ZrB2 ceramics were successfully prepared by slip casting with or without a strong magnetic field, followed by SPS. The microstructure of the sintered samples consists of equiaxial ZrB2 grains with clean grain boundary, with BN flake grains and small amounts of glassy phase confined at the isolating triple points of the matrix grains. ZrB2 ceramics consisted of coarser grains do not have plastic deformation up to 1650 °C, however, the good resistance in plastic deformation is not necessarily related to the enhancement of the flexural strength. The superior high-temperature strength is related to the fine ZrB2 grain size, the suppression of crack extension along the grain boundaries by the strong bonding at clean ZrB2/ZrB2 interfaces, and the large energy absorbing process during the plastic deformation increases the required fracture strength for rupture. The anisotropic flexural strength for the textured ZrB2 ceramics is attributed to the direction of the grains and the different slip plane in ZrB2 single crystals at room and high temperatures.
Acknowledgments
Financial supports from the National Natural Science Foundation of China (no. 51272266) and the bilateral project of NSFC-JSPS (no. 51111140017) are gratefully acknowledged.
References
- UpadhyaKYangJ MHoffmanW P 1997 Am. Ceram. Soc. Bull. 76 51 56 51–6
- OpekaM MTalmyI GZaykoskiJ A 2004 J. Mater. Sci. 39 5887 5904 5887–904 10.1023/B:JMSC.0000041686.21788.77
- WuchinaEOpilaEOpekaMFahrenholtzWTalmyI 2007 Interface 30 6
- PaulAJayaseelanD DVenugopalSZapata-SolvasEBinnerJVaidhyanathanBHeatonABrownPLeeW E 2012 Am. Ceram. Soc. Bull. 91 22 28 22–8
- KalishDClougherEvKrederK 1969 J. Am. Ceram. Soc. 52 30 36 30–6 10.1111/j.1151-2916.1969.tb12655.x
- BellosiAMonteverdeF DScitiD 2006 Int. J. Appl. Ceram. Technol. 3 32 40 32–40 10.1111/j.1744-7402.2006.02060.x
- HuPWangZ 2010 J. Eur. Ceram. Soc. 30 1021 1026 1021–6 10.1016/j.jeurceramsoc.2009.09.029
- ZouJZhangG JHuC FNishimuraTSakkaYVleugelsJVan der BiestO 2012 J. Am. Ceram. Soc. 95 874 878 874–8
- ZouJZhangG JHuC FNishimuraTSakkaYTanakaHVleugelsJVan der BiestO 2012 J. Eur. Ceram. Soc. 32 2519 2527 2519–27 10.1016/j.jeurceramsoc.2012.01.035
- ZouJZhangG JZhangHHuangZ RVleugelsJVan der BiestO 2013 Ceram. Int. 39 871 876 871–6 10.1016/j.ceramint.2012.06.018
- NeumanE WHilmasG EFahrenholtzW G 2013 J. Am. Ceram. Soc. 96 47 50 47–50 10.1111/jace.12114
- ChamberlainA LFahrenholtzW GHilmasG EEllerbyD T 2004 J. Am. Ceram. Soc. 87 1170 1172 1170–2 10.1111/j.1551-2916.2004.01170.x
- FahrenholtzW GHilmasG ETalmyI GZaykoskiJ A 2007 J. Am. Ceram. Soc. 90 1347 1364 1347–64 10.1111/j.1551-2916.2007.01583.x
- NiD WZhangG JKanY MSakkaY 2009 Scr. Mater. 60 615 618 615–8 10.1016/j.scriptamat.2008.12.027
- LiuH TZouJNiD WWuW WKanY MZhangG J 2011 Scr. Mater. 65 37 40 37–40 10.1016/j.scriptamat.2011.03.016
- WuW WSakkaYSuzukiT SZhangG J 2013 Int. J. Appl. Ceram. Technol. doi: 10.1111/ijac.12061
- NiD WZhangG JKanY MSakkaY 2009 Scr. Mater. 60 913 916 913–6 10.1016/j.scriptamat.2009.02.013
- SakkaYSuzukiT S 2005 J. Ceram. Soc. Japan 113 26 36 26–36 10.2109/jcersj.113.26
- SakkaYSuzukiT SUchikoshiT 2008 J. Eur. Ceram. Soc. 28 935 942 935–42 10.1016/j.jeurceramsoc.2007.09.039
- SugiyamaTTahashiMSassaKAsaiS 2003 ISIJ Int. 43 855 861 855–61 10.2355/isijinternational.43.855
- GrechnevG EFedorchenkoA VLogoshaA VPanfilovA SSvechkarevI VFilippovV BLyashchenkoA BEvdokimovaA V 2009 J. Alloys Compounds 481 75 80 75–80 10.1016/j.jallcom.2009.03.123
- FahrenholtzW GHilmasG EZhangS CZhuS 2008 J. Am. Ceram. Soc. 91 1398 1404 1398–404 10.1111/j.1551-2916.2007.02169.x
- GrassoSSakkaYMaizzaG 2009 Sci. Technol. Adv. Mater. 10 053001 10.1088/1468-6996/10/5/053001
- WuW WXiaoW LEstiliMZhangG JSakkaY 2013 Scr. Mater. 68 889 892 889–92 10.1016/j.scriptamat.2013.02.022
- ZhuX WSakkaY 2008 Sci. Technol. Adv. Mater. 9 033001 10.1088/1468-6996/9/3/033001
- GilliesD CLewisD 1968 J. Less-Common Metals 16 162 163 162–3 10.1016/0022-5088(68)90073-8
- OtaniSKorsukovaM MMitsuhashiT 1998 J. Cryst. Growth 194 430 433 430–3 10.1016/S0022-0248(98)00691-5
- EvansA GRanaA 1980 Acta Metall. 28 129 141 129–41 10.1016/0001-6160(80)90062-0
- HaggertyJ SLeeD W 1971 J. Am. Ceram. Soc. 54 572 576 572–6 10.1111/j.1151-2916.1971.tb12210.x