Abstract
The formation of the icosahedral phase (I-phase) as a secondary solidification phase in Mg–Zn–Y and Mg–Zn–Al base systems provides useful advantages in designing high performance wrought magnesium alloys. The strengthening in two-phase composites (I-phase + α-Mg) can be explained by dispersion hardening due to the presence of I-phase particles and by the strong bonding property at the I-phase/matrix interface. The presence of an additional secondary solidification phase can further enhance formability and mechanical properties. In Mg–Zn–Y alloys, the co-presence of I and Ca2Mg6Zn3 phases by addition of Ca can significantly enhance formability, while in Mg–Zn–Al alloys, the co-presence of the I-phase and Mg2Sn phase leads to the enhancement of mechanical properties. Dynamic and static recrystallization are significantly accelerated by addition of Ca in Mg–Zn–Y alloy, resulting in much smaller grain size and more random texture. The high strength of Mg–Zn–Al–Sn alloys is attributed to the presence of finely distributed Mg2Sn and I-phase particles embedded in the α-Mg matrix.
Introduction
Magnesium alloys are considered as one of the potential candidates for light-weight alloys in various vehicle industries such as the automobile and aerospace industries [Citation1]. For this purpose, development of magnesium alloys with proper combination of properties including strength, ductility, formability and corrosion resistance is strongly required. Therefore, there has been a great amount of research to enhance the properties of the conventional magnesium alloys such as Mg–Al and Mg–Zn based alloys. Prime concern has been given for better combination of strength and ductility through grain size refinement [Citation2–Citation5], proper selection of the second phase embedded in the α-Mg matrix [Citation6–Citation12] and enhanced age hardening effect [Citation13–Citation16]. Another point to be considered for magnesium alloys is high temperature properties. In this respect, some magnesium alloys containing rare earth (RE) elements have been developed for elevated temperature applications [Citation17–Citation21]. However, most magnesium alloys generally exhibit moderate strength with limited ductility at ambient temperature owing to the hexagonal-close-packed (hcp) structure of magnesium. Thus, most magnesium alloy components developed so far have been produced by casting methods such as sand-mold and die casting methods [Citation22, Citation23]. On the other hand, to catch up with recent demand from the rapidly growing vehicle industries, wrought magnesium alloys fabricated by rolling or extrusion have been studied intensively, aiming for better combination of mechanical properties (strength and ductility) and formability [Citation24–Citation26]. The typical wrought magnesium alloys are normally based on the solid-solution type microstructure without secondary solidification phases, i.e. they contain only a small amount of alloying elements in order to derive the ductility benefit from pure magnesium.
While most of the wrought magnesium alloys developed so far have been based on solid-solution type microstructure, recently secondary solidification phase reinforced magnesium alloys have received increasing attention. The secondary solidification phase particles embedded in the α-Mg matrix can play a role in enhancing the mechanical properties and formability by inducing dispersion particle strengthening and basal texture weakening. From this point of view, quasicrystals may be a good candidate for reinforcing phases in magnesium alloys, since they exhibit high hardness and low interfacial energy [Citation27]. Since it has been shown that thermodynamically stable icosahedral phase (I-phase) forms in Al–Cu–Fe and Mg–Zn–Y alloy systems [Citation28–Citation30], it is basically possible to synthesize in situ composite which consists of I-phase particles embedded in the solid-solution matrix through a simple casting process, on condition that the composition is properly selected in the two-phase region of I-phase + Al or Mg rich solid solution. However, in the case of the Al–Cu–Fe alloy system, there is no (I-phase + solid solution) two-phase region, since the composition range for formation of quasicrystals is wholly surrounded by various (quasicrystal + intermetallic phase) two-phase regions [Citation31]. In the case of Mg–Zn–Y, a thermodynamically stable I-phase with composition of ∼Mg42Zn50Y8 (in at%) has been reported to form by a peritectic reaction between previously formed (Zn, Mg)5Y and residual Mg-enriched liquid phase, during solidification from the alloy melt [Citation32–Citation34]. Following the report showing that I-phase is present in Mg–Zn–Y alloy in the form of a primary or eutectic solidification phase [Citation35, Citation36], Tsai et al have shown that a two-phase region of (I-phase + α-Mg) is present in the Mg-rich corner of the Mg–Zn–Y phase diagram [Citation37].
On the other hand, in the Mg–Zn–Al system, it has been known that metastable I-phase forms based on the composition of the Frank−Kasper phase (Al, Zn)49Mg32 [Citation38, Citation39]. However, it has been suggested that thermally stable I-phase with a composition near ∼Mg44Zn41Al15 forms in the Mg–Zn–Al system [Citation40]. Indeed, the Mg44Zn41Al15 I-phase is thermally stable up to 653 K, and in the higher temperature region it decomposes into liquid and the remaining phase as a result of a peritectic reaction [Citation41]. Therefore, the I-phase in the Mg–Zn–Al system can be a candidate for formation of in situ composite microstructure which consists of I-phase and solid-solution matrix. In the present paper, formation of composite microstructure (I-phase + solid-solution matrix), and resulting mechanical properties in Mg–Zn–Y and Mg–Zn–Al base alloy systems have been reviewed.
Mg–Zn–Y base alloy
The existence of the two-phase region (I-phase + α-Mg) in the Mg-rich corner of the Mg–Zn–Y system indicates that small additions of Y in the binary Mg–Zn system can change the alloy microstructure significantly [Citation42]. A detailed study on the formation of the I-phase has shown that a eutectic structure in the form of an alternating lamellar of I-phase and α-Mg forms in the Mg–Zn–Y system [Citation8]. Therefore, as-cast Mg-rich Mg–Zn–Y alloys in the compositional range up to the pseudoeutectic composition consist of the thermally stable I-phase formed as a secondary solidification phase in the α-Mg matrix during solidification, indicating that I-phase reinforced magnesium alloys can be fabricated just by solidification from the alloy melt. During solidification, α-Mg phase nucleates first and grows into a dendritic morphology. At the later stage of solidification the remaining liquid in the interdendritic region solidifies into a eutectic structure consisting of I-phase and α-Mg. As the composition moves closer to the α-Mg single phase region, the volume fraction of the I-phase decreases, still retaining a two-phase structure of I-phase and α-Mg in the interdendritic region. Furthermore, the disadvantage of the low eutectic temperature of the Mg–Zn binary alloy (∼340 °C) can be surmounted in the Mg–Zn–Y alloy since the addition of a small amount of yttrium raises the eutectic temperature significantly up to ∼450 °C. Figures (a)–(c) show the optical microstructures of the as-cast Mg–1.14Zn–0.17Y, Mg–1.53Zn–0.23Y, and Mg–3.17Zn–0.47Y alloy (at%). The fraction of the interdendritic eutectic increases with increasing zinc and yttrium contents. The volume fraction of the interdendritic eutectic region measured using an image analyzer is 1.2, 2.3 and 3.7% in Mg–1.14Zn–0.17Y, Mg–1.53Zn–0.23Y, and Mg–3.17Zn–0.47Y alloys, respectively [Citation43].
Figure 1 Optical microstructures obtained from as-cast: (a) Mg−1.14Zn−0.17Y; (b) Mg−1.53Zn−0.23Y; and (c) Mg−3.17Zn−0.47Y alloy [Citation43]. © IOP Publishing. Reproduced by permission of IOP Publishing. All rights reserved.
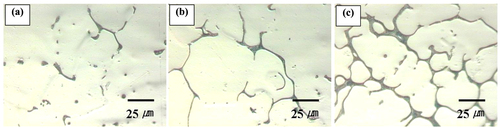
In addition to the eutectic structure of I-phase and α-Mg, fine polygon-shaped I-particles (20–30 nm) are distributed in the α-Mg matrix in the as-cast alloy, as shown in figure (a) [Citation43]. The alignment of I-phase particles implies that they form when the alloy is in the liquid state and moves in a line ahead of the advancing solid–liquid interface, finally entrapped in the α-Mg grain when the pulling force by interfacial energy is exceeded by gravitational force by accumulated I-phase particles. The morphologies of the I-phase particles and schematic drawings of a pentagonal dodecahedron, which is projected along its five-fold, three-fold and two-fold symmetry axes, are shown in figures (b)–(d). The polygonal shapes again confirm that the I-phase particles form directly in the liquid melt.
Figure 2 (a) TEM micrograph of icosahedral nanoparticles in the α-Mg matrix of as-cast Mg–8.3Zn–0.7Y alloy; (b)–(d) the projected morphologies of the I-particles and corresponding schematic drawings of a pentagonal dodecahedron, which is projected along its five-, three- and two-fold symmetry axes, respectively [Citation43]. © IOP Publishing. Reproduced by permission of IOP Publishing. All rights reserved.
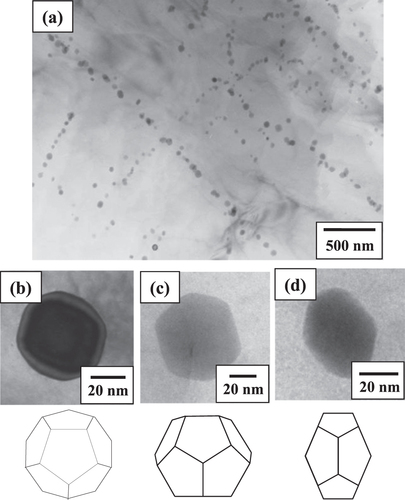
The as-cast eutectic structure in the dendritic region was destroyed during the hot rolling process, providing the distribution of I-phase particles (0.3–2.0 μm in size) shown in figures (a) and (b). The existence of an I-phase in the deformed specimen clearly indicates that the I-phase thermally equilibrates with the α-Mg phase. A relatively fine grain size can be obtained due to the dynamic recrystallization process during thermo-mechanical processing. The cracked I-particles effectively act as dynamic recrystallization sources during hot rolling, helping to refine the grains of the α-Mg matrix. Transmission electron microscopy (TEM) observation revealed that the size of the pre-existing I-particles does not change significantly (∼100 nm) even after experiencing long exposure at high temperature (figure (b)) [Citation43]. Typical values of yield strength (YS, MPa), ultimate tensile strength (UTS, MPa) and elongation (%) obtained from rolled Mg–Zn–Y alloys are summarized in table [Citation44]. The mechanical properties in table indicate that a very good combination of strength and elongation is obtained in the quasicrystal-strengthened Mg–Zn–Y alloys when compared with those of the other conventional wrought magnesium alloys. The high strength is mainly due to the I-phase particle dispersion strengthening effect. While it is unusual that relatively high ductility is obtained in spite of the presence of the large number of secondary solidification I-phase particles. Generally, the ductility for the alloy containing a large number of intermetallic particles is low, since formation of dislocations is required to overcome the geometrical constraint during deformation, particularly in the region surrounding the hard particles [Citation42]. Such an accumulation of dislocations eventually leads to occurrence of decohesion or cracks at the particle/matrix boundary [Citation45]. For example, the interface between the intermetallic particle and the matrix in AZ91 alloy containing the intermetallic particles of Mg17Al12 is relatively weak, providing the opening site of a microcrack during deformation [Citation46]. However, in the case of Mg–Zn–Y alloy, no microcracks at the I-phase/α-Mg interface are observed, although many I-phase particles are closely spaced in some regions as shown in figure (b). Thus, the improvement of mechanical properties by I-phase particles in the Mg–Zn–Y alloy is different from the conventional wrought Mg–Al–Zn alloys. The quasi-periodic lattice structure of the I-phase provides the stable I-phase particle/matrix interface [Citation27], resulting in low lattice mismatching strain in the α-Mg/I-phase particle interface. As shown in table [Citation44], YS and UTS increase with increasing volume fraction of I-phase, indicating that the alloys with a range of a combination of strength and ductility can be designed by changing the fraction of I-phase, i.e. by changing the total solute content of Zn and Y. The strengthening behavior with increasing volume fraction of I-phase can be explained by the effect of dispersion hardening due to the presence of finely dispersed I-phase particles [Citation7].
Figure 3 (a) Optical micrograph obtained from as-rolled Mg–1.53Zn–0.23Y alloy, and (b) bright-field TEM images showing destroyed icosahedral particles (0.3 ∼ 2 μm) and pre-existing icosahedral particles (∼100 nm) [Citation43]. © IOP Publishing. Reproduced by permission of IOP Publishing. All rights reserved.
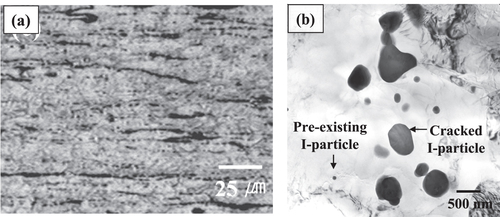
Table 1. Yield strength (YS, MPa), ultimate tensile strength (UTS, MPa) and elongation (%) of the rolled Mg–Zn–Y alloy sheets with different volume fraction of icosahedral phase [Citation44].
Enhancement of formability has been an important issue in developing wrought magnesium alloy, since strong basal texture develops during deformation, resulting in large anisotropy and difficulty in the secondary forming process. In this context, texture modification or weakening basal texture is known to be an effective way to improve its formability [Citation47–Citation49]. Studies have been performed in two ways: by processing condition control and by alloy chemistry control. In the former case, various processing techniques, such as severe plastic deformation (SPD), differential speed rolling and cross rolling techniques have been applied to achieve grain size refinement and basal texture relaxation [Citation2, Citation50–Citation53]. In the latter case, the addition of RE elements to Mg alloy promotes weak basal texture evolution, leading to enhanced ductility and reduced anisotropy [Citation54, Citation55].
Recent studies show that Mg−Zn−RE alloy (RE: rare earth element; Y, Gd) is one of the most promising candidates providing a combination of enhanced mechanical properties and formability [Citation26, Citation56–Citation60]. It has been shown that the more random texture can be obtained in RE-containing Mg alloys strengthened with secondary particles [Citation11, Citation61–Citation64]. However, the detailed mechanism of the weakening or changing of basal texture is not clarified, even though a few models are proposed to explain the phenomenon: (1) the more randomized texture in Y- and RE-containing Mg alloy is associated with particle stimulated nucleation (PSN) of recrystallization [Citation64, Citation65]; and (2) the lower overall texture strength in wrought Mg–Zn–RE alloys is attributed to the solute content in the solid-solution matrix, for example, Zn content in the α-Mg matrix [Citation10]. It has been shown further that more random texture is possible even in solid-solution type binary Mg alloy containing a lower content of Y, indicating that formation of the texture is affected by the nature of α-Mg solid-solution matrix [Citation66].
On the other hand, in Mg–Zn–Ca system, Clark [Citation67, Citation68] reported formation of two ternary compounds: Ca2Mg6Zn3 and Ca2Mg5Zn13, and Zhang et al [Citation69] reported that the Ca2Mg6Zn3 phase has a homogeneity composition range, Ca3MgxZn15 − x (4.6 ≰ x ≰ 12). Based on previous reports on the existence of the orientation relationship between Ca2Mg6Zn3 and α-Mg [Citation70, Citation71], implying a structural connectivity between two phases, the co-presence of two secondary solidification phases, i.e. Ca2Mg6Zn3 and I phases may play a role in modifying the texture evolution in Ca added Mg–Zn–Y alloy. Figure compares the electron back-scattered diffraction (EBSD) basal pole figures obtained from the normal direction of the rolled Mg–5Zn–0.8Y and Mg–5Zn–0.8Y–0.3Ca (hereafter wt%, unless stated otherwise) alloy sheets after annealing at 350 °C for 30 min, indicating that the strong basal texture is significantly weakened with the addition of Ca. According to the gray-tone scale shown in figures (a) and (b), maximum basal pole intensity in the Mg–5Zn–0.8Y alloy is ∼14, which was much higher than ∼7 in the Mg–5Zn–0.8Y–0.3Ca alloy [Citation72]. In addition, the inverse pole figure (IPF) maps obtained from the same region in the as-rolled sheet sample and the sheet sample after annealing at 350 °C for 5 min are compared in figure . In as-rolled Mg–5Zn–0.8Y alloy, many tensile twins are present, and after annealing treatment, the microstructure remained almost the same. On the contrary, in as-rolled Mg–5Zn–0.8Y–0.3Ca alloy, twins are hardly observed, indicating that the dynamic recrystallization occurs extensively during the rolling process. Moreover, after annealing treatment, many new grains were formed by recrystallization, weakening the basal texture. Therefore, addition of Ca in Mg–5Zn–0.8Y alloy alleviates the strong basal texture remarkably and rapidly by accelerated recrystallization during rolling and annealing treatment. Moreover, instead of the PSN effect for recrystallization, the change of the matrix composition by addition of Ca in Mg–Zn–Y alloy plays a dominant role in accelerating dynamic and static recrystallization and weakening the basal texture. The presence of a small amount of Ca in the solid-solution matrix may change the c/a ratio or the stacking fault energy, resulting in a change in the nature of the recrystallization mechanism, or segregation of Ca at defects including grain boundaries may accelerate the recrystallization kinetics.
Figure 4 EBSD basal pole figures obtained from the normal direction of the rolled: (a) Mg–5Zn–0.8Y; and (b) Mg–5Zn–0.8Y–0.3Ca alloy sheets after annealing at 350 °C for 30 min [Citation72]. Reproduced by permission of The Japan Institute of Metals and Materials.
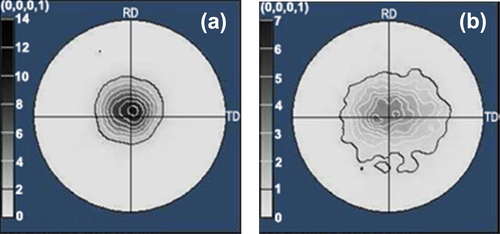
Figure 5 IPF maps obtained from the same region in: (a) and (c) as-rolled Mg–5Zn–0.8Y and Mg–5Zn–0.8Y–0.3Ca alloy sheet (after third rolling step, i.e. after rolling down to 7 mm from 10 mm thickness s; (b) and (d) Mg–5Zn–0.8Y and Mg–5Zn–0.8Y–0.3Ca alloy sheets after annealing at 350 °C for 5 min [Citation72]. Reproduced by permission of The Japan Institute of Metals and Materials.
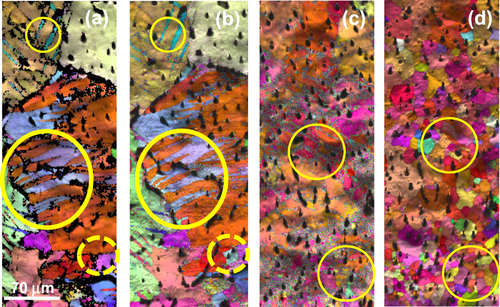
Mg–Zn–Al base alloy
Somekawa et al have reported a good balance of high strength and ductility in extruded Mg–7.6%Zn–3.9%Al alloy where I- or approximant phases are present as secondary solidification phases [Citation11]. In such a case, the I-phase is based on the τ phase, Mg32(Al,Zn)49, and transforms into the stable φ phase, Al2Mg5Zn2, after heat treatment at 598 K [Citation44]. It can be noticed that the co-presence of I-phase (or I- related phase) and another crystalline phase by proper selection of the secondary solidification phase may lead to enhancement of property combinations in wrought magnesium alloys [Citation73]. Here, Mg−Sn based alloy may be one of the candidates, since the Mg–Sn based alloy system receives attention as a possible candidate for high-strength wrought magnesium alloys with enhanced heat resistance [Citation74–Citation76]. However, since the ductility of the binary Mg–Sn alloy is too limited for the conventional wrought process to be applied for Mg–Sn alloy, most of the research on Mg–Sn based alloy has been focused on the development of casting alloys with an emphasis on the enhancement of age hardening characteristics [Citation75, Citation77–Citation79]. Previous study showed that the ductility required for the wrought process of Mg–Sn alloy can be provided by proper selection of alloying elements. Addition of Zn provides the ductility required for the wrought process for Mg–Sn alloy [Citation80] as well as to enhance the age hardening response by homogeneous distribution of the refined Mg2Sn precipitates [Citation81, Citation82]. It has been reported that superior creep characteristics can be obtained in extruded Mg–2.2Sn–1.0Zn–0.1Mn alloy (in at%) due to enhanced tendency to form Mg2Sn and MgZn2 precipitates [Citation83]. High room-temperature tensile strength (YS: 308 MPa) can be obtained in extruded Mg–2.2Sn–0.5Zn–1.0Al (in at%) alloy due to the strengthening effect by the presence of Mg2Sn precipitates and by the solid-solution hardening effect of aluminum [Citation76]. Further, the effect of Al and Mn addition on the aging behavior of Mg–Sn–Zn alloy has been examined [Citation84]. As mentioned above, the high strength of previously reported Mg−Sn based wrought alloys is attributed to the presence of precipitates formed during the forming process or artificial aging treatment. Further, it has been shown that addition of proper amount of zinc and aluminum in binary Mg–Sn alloy leads to the formation of I-phase and Mg2Sn during solidification in the interdendritic region. For example, as-cast Mg–7Sn–2Zn, Mg–7Sn–5Zn, and Mg–7Sn–5Zn–2Al alloys exhibited a solidification microstructure which consisted of primary α-Mg and interdendritic secondary solidification phase of which the fraction increased with increasing the solute content [Citation73]. Figures (a) and (b) show typical optical and scanning electron microscopy (SEM) images obtained from the as-cast Mg–7Sn–5Zn–2Al alloy. Two different types of secondary solidification phases, i.e. darker and lighter contrast phases, are present in the interdendritic region. The TEM images shown in figures (c) and (d) indicate that two different phases, Mg2Sn and MgZn2 are present in the interdendritic region of the as-cast Mg–7Sn–5Zn alloy. The morphology of Mg2Sn was blocky type, while that of MgZn2 was interconnected type. Interestingly, with the addition of aluminum in Mg–7Sn–5Zn alloy, the I-phase appeared in the interdendritic region instead of the MgZn2 phase. In this particular case, the total volume fraction of the secondary phase is ∼8.1%, and those for the Mg2Sn and I-phases are ∼4.0 and ∼4.1%, respectively. As mentioned above, in the Mg–Zn–Al system, metastable I-phase has been known to form based on the composition of the Frank−Kasper phase (Al,Zn)49Mg32 [Citation38, Citation39]. However, it has been reported that thermally stable I-phase forms in the Mg–Zn–Al system with composition near Mg44Zn41Al15 (in at%) [Citation40]. The composition of the I-phase is Mg47.2Zn36.9Al15.9 (in at%), which is very close to the previously reported composition range for the thermally stable Mg–Zn–Al I-phase [Citation72]. During homogenizing treatment, the I-phase in Mg–7Sn–5Zn–2Al alloy dissolves into the α-Mg matrix, while the Mg2Sn phase remains in the interdendritic region, since the eutectic temperature of α-Mg—Mg2Sn is relatively high. As in the case of Mg–Zn–Y alloy mentioned above, fragmentation of the Mg2Sn phase particles occurs during the rolling process, and the resulting particles are aligned along the rolling direction. Interestingly, 0.1 ∼ 0.5 μm size I-phase precipitates during rolling process in the case of Mg–7Sn–5Zn–2Al alloy [Citation73]. Here, no specific orientation relationship is present between the I-phase precipitate and the α-Mg matrix.
Figure 6 (a) Optical and (b) SEM images obtained from as-cast Mg–7Sn–5Zn–2Al alloy; (c) and (d) bright-field TEM images obtained from as-cast Mg–7Sn–5Zn and Mg–7Sn–5Zn–2Al alloys [Citation73]. Reproduced by permission of Elsevier.
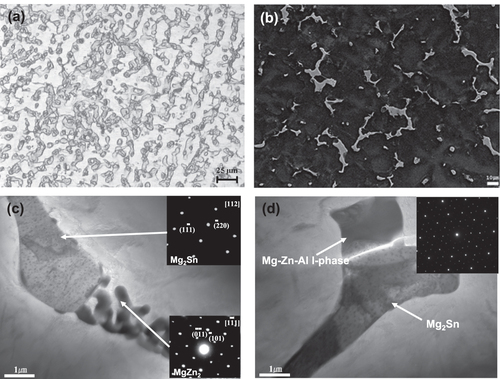
In the case of Mg–Zn–Y alloy mentioned above, the co-presence of I- and Ca2Mg6Zn3 phases by addition of Ca can induce a significant enhancement of formability. Similarly, in the case of Mg–Zn–Al alloy, the co-presence of the I-phase and Mg2Sn phase leads to the enhancement of mechanical properties. Typical mechanical properties obtained from Mg–7Sn–2Zn, Mg–7Sn–5Zn, and Mg–7Sn–5Zn–2Al rolled sheets are compared in figure [Citation73]. Mg–7Sn–5Zn–2Al alloy exhibits the highest strength (YS: 318 MPa, UTS: 373 MPa) with a reasonably large plastic strain of 8% in the as-rolled state. Mg–7Sn–5Zn alloy exhibits the second highest strength, and Mg–7Sn–2Zn alloy exhibits the lowest strength, but with slightly improved plastic strain. After annealing treatment, Mg–7Sn–5Zn–2Al alloy again exhibits the highest strength (YS: 202 MPa, UTS: 321 MPa) with a large plastic strain of 21%, indicating that a larger degree of strengthening effect comes from the presence of Mg2Sn and Mg2Zn phases, as can be seen in the mechanical properties of the Mg–7Sn–5Zn alloy; however, more significant strength increase effect in the Mg–7Sn–5Zn–2Al alloy comes from the replacement of the MgZn2 phase with the I-phase. A recent report on the mechanical property enhancement in extruded Mg–7.6Zn–3.9Al alloy [Citation36] is based on the presence of I- or approximant phases as secondary solidification phases. However, the I-phase in Mg–7.6Zn–3.9Al alloy is based on the τ phase, Mg32(Al,Zn)49, and transforms into stable the φ phase, Al2Mg5Zn2, after heat treatment. On the other hand, the report on the mechanical property enhancement in rolled Mg–7Sn–5Zn–2Al alloy [Citation73] is based on the presence of I- and Mg2Sn phases as secondary solidification phases. In such a case, the strengthening effect is provided by the I-phase which precipitates during the rolling process and the Mg2Sn phase which is present before the rolling process.
Figure 7 Tensile stress–strain curves obtained from Mg–7Sn–2Zn, Mg–7Sn–5Zn, and Mg–7Sn–5Zn–2Al rolled sheets: (a) as-rolled state, (b) after annealing at 350 °C for 30 min [Citation73]. Reproduced by permission of Elsevier.
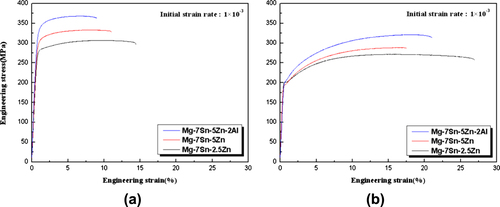
Role of quasicrystals in the enhancement of mechanical properties
When examining the mechanical properties of the particle strengthened composites, the nature of the interface between the particle and matrix is one of the most important factors determining the load carrying capacity of the embedded particles in the matrix. When the alloys are strengthened by second phase particles, the cracks or cavities at the matrix/particle interface emerge and grow during the deformation. Thus, forming processes such as the rolling process can leave weakly bonded interfaces or broken particles, and they do not generally self-sinter fully even after an exposure at high temperature.
However, no cavities have been detected in deformed quasicrystal-reinforced Mg–Zn–Y and Mg–Zn–Al base alloys. The strong bonding characteristics between the I-phase particle and the α-Mg matrix can be elucidated by high resolution electron microscopy [Citation6, Citation73]. After severe deformation such as rolling, the α-Mg matrix around the I-phase particle (∼20 nm thickness) preserves the orientation relationship between the I-phase and the surrounding thin layer of α-Mg, which can be expressed as [I2]//[0001]Mg and (2f), (5f)//{10-10}Mg. The α-Mg matrix away from the thin thickness region around the I-phase particle exhibits a different orientation due to SPD during rolling. Although it is generally understood that the incoherent interface in many composite alloys can exhibit some load carrying capacity, the rigid interface between the I-phase and surrounding hcp matrix can provide an enhanced strengthening effect.
Since the I-phase exhibits a more isotropic character than the crystalline phase due to its highly symmetric structure, reasonably stable bonding with low strain energy in the matrix adjacent to the I-phase particle can be provided. In general, the matrix adjacent to the microscale intermetallic particle is highly stressed due to the mismatched lattice constants between the matrix and the particle. However, due to the quasiperiodic lattice structure of the I-phase, the mismatch strain may be compensated by the I-phase particle, decreasing the stress concentration in the matrix near the I-phase particle [Citation73].
Summary
Two-phase composites (I-phase and α-Mg) can be obtained by proper selection of alloy compositions in Mg–Zn–Y and Mg–Zn–Al base alloy systems. In the case of Mg–Zn–Y alloy, with increasing Mg content, the primary solidification phase changes from I-phase to α-Mg phase, and a single eutectic structure of I-phase and α-Mg can be obtained at a composition of Mg–23.5Zn–3.5Y. The alloys with a range of combination of strength and ductility can be designed by changing the fraction of the I-phase, i.e. by changing the total solute content of Zn and Y. The strengthening behavior with increasing of the volume fraction of I-phase can be explained by the effect of dispersion hardening due to the presence of finely dispersed I-phase particles. No debonding or microscale defect at the particle/matrix interface is observed after the forming process. Such a phenomenon can be attributed to the stable interface between the matrix and I-phase.
In the case of Mg–Zn–Y alloy, the co-presence of I- and Ca2Mg6Zn3 phases by addition of Ca can induce a significant enhancement of formability. Similarly, in the case of Mg–Zn–Al alloy, the co-presence of the I-phase and Mg2Sn phase leads to an enhancement of mechanical properties. Dynamic and static recrystallization are significantly accelerated by addition of Ca in Mg–Zn–Y alloy, resulting in much smaller grain size and more random texture. Existence of Ca in the α-Mg solid-solution matrix may play a role in acceleration of recrystallization and weakening of basal texture. The secondary solidification phase can be selected as Mg2Sn and MgZn2 or Mg2Sn and I-phase depending on the alloy composition in Sn-added Mg–Zn–Al alloy. The high strength is attributed to the presence of finely distributed Mg2Sn and I-phase particles embedded in the α-Mg matrix. Such a good combination of mechanical properties opens up interesting perspectives for the application of such quasicrystal-reinforced magnesium alloys as light-weight components.
Acknowledgement
This study was supported by the World Premier Materials (WPM) project funded by the Korea Ministry of Knowledge and Economy, and the Global Research Laboratory Program of the Korea Ministry of Education, Science and Technology.
References
- BealsR STissingtonCZhangXKainerKPetrilloJVerbruggeM 2007 JOM 59 39 10.1007/s11837-007-0102-8
- KoikeJKobayashiTMukaiTWatanabeHSuzukiMMaruyamaKHigashiK 2003 Acta Mater. 51 2055 10.1016/S1359-6454(03)00005-3
- YangQGhoshA K 2006 Acta Mater. 54 5159 10.1016/j.actamat.2006.06.043
- Oh-ishiKMendisC LHommaTKamadoSOhkuboTHonoK 2009 Acta Mater. 57 5593 10.1016/j.actamat.2009.07.057
- TongL BZhengM YHuX SWuKXuS WKamadoSKojimaY 2010 Mater. Sci. Eng. A 527 4250 10.1016/j.msea.2010.03.062
- BaeD HKimS HKimD HKimW T 2002 Acta Mater. 50 2343 10.1016/S1359-6454(02)00067-8
- BaeD HLeeM HKimK TKimW TKimD H 2002 J. Alloys Compd. 342 445 10.1016/S0925-8388(02)00273-6
- OkJ BKimI JYiSKimW TKimD H 2003 Phil. Mag. 11 2359 10.1080/0141861031000113325
- SinghANakamuraMWatanabeMKatoATsaiA P 2003 Scr. Mater. 49 417 10.1016/S1359-6462(03)00305-1
- BohlenJNürnbergM RSennJ WLetzigDAgnewS R 2007 Acta Mater. 55 2101 10.1016/j.actamat.2006.11.013
- SomekawaHOsawaYSinghAMukaiT 2009 Scr. Mater. 61 705 10.1016/j.scriptamat.2009.06.008
- NamS WKimW TKimD HKimT S 2013 Met. Mater. Int. 19 205 10.1007/s12540-013-2010-5
- KimI JKimD HKimD H 2003 Mater. Sci. Eng. A 359 313 10.1016/S0921-5093(03)00352-6
- MendisC LOh-ishiKHonoK 2007 Scr. Mater. 57 485 10.1016/j.scriptamat.2007.05.031
- MendisC LOh-ishiKKawamuraYHonmaTKamadoSHonoK 2009 Acta Mater. 57 749 10.1016/j.actamat.2008.10.033
- LeeB DKimE JBaekU H 2013 Met. Mater. Int. 19 135 10.1007/s12540-013-2001-6
- BettlesC JGibsonM AZhuS M 2009 Mater. Sci. Eng. A 505 6 10.1016/j.msea.2008.11.004
- MuY LWangQ DHuM LJanikbVYinaD D 2013 Scr. Mater. 68 885 10.1016/j.scriptamat.2013.02.031
- ZafariAGhasemiH MMahmudiR 2013 Wear 303 98 10.1016/j.wear.2013.02.016
- Ajith KumarK KPillaiU T SPaiB CChakrabortyM 2013 Met. Mater. Int. 19 1167 10.1007/s12540-013-6001-3
- KimW JHongS ILeeK H 2010 Met. Mater. Int. 16 171 10.1007/s12540-010-0403-2
- PolmearI J 1996 Mater. Trans. JIM 37 12 10.2320/matertrans1989.37.12
- GuanR GZhaoZ YLiau CCuiTLeeC S 2013 Met. Mater. Int. 19 33 10.1007/s12540-013-1006-5
- ParkJ HKimH LJungJ EChangY W 2013 Met. Mater. Int. 19 389 10.1007/s12540-013-3003-0
- ScottJMilesMFullwoodDAdamsBKhosravaniAMishraR K 2013 Metall. Trans. A 44 512 10.1007/s11661-012-1405-0
- WuDChenaR SHanE H 2011 J. Alloys Compd. 509 2856 10.1016/j.jallcom.2010.11.141
- DuboisJ MPlaindouxPBelin-FerreETamuraNSordeletD J 1997 Proc. 6th International Conference on Quasicrystals FujiwaraXTakeuchiX
- TsaiA PInoueAMasumotoT 1987 Jpn J. Appl. Phys. 26 L1505 10.1143/JJAP.26.L1505
- OhashiWSpaepenF 1987 Nature 330 555 10.1038/330555a0
- LuoZ PSuiH XZhangS Q 1996 Metall. Mater. Trans. 27A 1779 10.1007/BF02651927
- GayleF WShapiroA JBiancanielloF SBoettingerW T 1992 Metall. Trans. A 23A 2409 10.1007/BF02658044
- TsaiA PNiikuraAInoueAMasumotoTNishitaYTsudaKTanakaM 1994 Phil. Mag. Lett. 70 169 10.1080/09500839408240971
- SatoT JAbeETsaiA P 1998 Phil. Mag. Lett. 77 213 10.1080/095008398178534
- TsaiA PNiikuraAInoueAMasumotoT 1997 J. Mater. Res. 12 1468 10.1557/JMR.1997.0202
- LangsdoftARitterFAssmusW 1997 Phil. Mag. Lett. 75 381 10.1080/095008397179453
- LuoZ PZhangS QTangY LZhaoD S 1993 Scr. Mater. 28 1513 10.1016/0956-716X(93)90584-F
- TsaiA PMurakamiYNiikuraA 2000 Phil. Mag. A 80 1043 10.1080/01418610008212098
- RamachandraraoPSastryG V S 1985 Pramana 25 L255 10.1007/BF02847665
- YamaneHKimuraKShibuyaTTakeuchiS 1987 Mater. Sci. Forum 22 539 10.4028/www.scientific.net/MSF.22-24
- TakeuchiTMurasakiSMatsumuroAMizutaniU 1993 J. Non-Cryst. Solids 156–158 914 10.1016/0022-3093(93)90095-F
- TakeuchiTMizutaniU 1995 Phys. Rev. B 52 9300 10.1103/PhysRevB.52.9300
- ChangH JKimW TKimD H 2011 Isr. J. Chem. 51 1176 10.1002/ijch.v51.11/12
- ChangH JLeeJ YKimD H 2008 J. Phys.: Condens. Matter 20 314001 10.1088/0953-8984/20/31/314001
- LeeJ YKimD HLimH KKimD H 2005 Mater. Lett. 59 3801 10.1016/j.matlet.2005.06.052
- CourtneyT H 1990 Mech. Behav. Mater. New York McGraw-Hill
- AlizadehRMahmudiR 2011 J. Alloys Compd. 509 9195 10.1016/j.jallcom.2011.06.109
- YukutakeEKanekoJSugamataM 2003 Trans. JIM 44 452 10.2320/matertrans.44.452
- ShinB SKangHBaeD H 2012 Met. Mater. Int. 18 23 10.1007/s12540-012-0003-4
- SrinivasaraoBdel ValleJ ARuanoO APerez-PradoM T 2012 Kov. Mater. 50 1
- ChinoYMabuchiMKishiharaRHosokawaHYamadaYWenCShimojimaKIwasakiH 2002 Mater. Trans. 43 2554 10.2320/matertrans.43.2554
- WatanabeHMukaiTIshikawaK 2004 J. Mater. Sci. 39 1477 10.1023/B:JMSC.0000013922.16079.d3
- KimS HYouB SYimC DSeoY M 2005 Mater. Lett. 59 3876 10.1016/j.matlet.2005.07.024
- LimH KLeeJ YKimD , HKimW TLeeJ SKimD H 2009 Mater. Sci. Eng. A 506 63 10.1016/j.msea.2008.12.037
- Al-SammanTLiX 2011 Mater. Sci. Eng. A 528 3809 10.1016/j.msea.2011.01.080
- NguyenD TKimandY SJungD W 2012 Met. Mater. Int. 18 583 10.1007/s12540-012-4025-8
- YamashitaAHoritaZLangdonT G 2001 Mater. Sci. Eng. A 300 142 10.1016/S0921-5093(00)01660-9
- KimK HLeeJ GBaeG TBaeJ HKimN J 2008 Mater. Trans. 49 980 10.2320/matertrans.MC200752
- LiQWangQWangYZengXDingW 2007 J. Alloys Compd. 427 115 10.1016/j.jallcom.2006.02.054
- XieG MMaZ YGengLChenR S 2007 Mater. Sci. Eng. A 471 63 10.1016/j.msea.2007.03.041
- XuD KTangW NLiuLXuY BHanE H 2008 J. Alloys Compd. 461 248 10.1016/j.jallcom.2007.07.096
- TangaW NChenaR SZhoubJHanE H 2009 Mater. Sci. Eng. A 499 404 10.1016/j.msea.2008.09.048
- LeeJ YLimH KKimD HKimW TKimD H 2008 Mater. Sci. Eng. A 491 239 10.1016/j.msea.2008.02.010
- YanHChenR SHanE H 2010 Mater. Sci. Eng. A 527 3317 10.1016/j.msea.2010.02.038
- BallE APrangnellP B 1994 Scr. Mater. 31 111 10.1016/0956-716X(94)90159-7
- LorimerG WMackenzieL W FHumphreysF JWilksT 2005 Mater. Sci. Forum 488–489 99 10.4028/www.scientific.net/MSF.488-489
- AgnewS RSennJ WHortonJ A 2006 JOM 58 62 10.1007/s11837-006-0026-8
- ClarkJ B 1961 Trans. AIME 221 644
- ClarkJ B 1961 JCPDS Card 12 0266 12–0266
- ZhangY NKevorkovDLiJEssadiqiEMedrajM 2010 Intermetallics 18 2404 10.1016/j.intermet.2010.08.033
- JardimP MSolorzanoGSandeJ B V 2002 Microsc. Microanal. 8 487 10.1017/S1431927602010413
- Oh-ishiKWatanabeRMendisC LHonoK 2009 Mater. Sci. Eng. A 526 177 10.1016/j.msea.2009.07.027
- Kyeong1J SKimJ KLeeM JParkY BKimW TKimD H 2012 Mater. Trans. 53 991 10.2320/matertrans.M2011401
- KimY KSohnS WKimD HKimW TKimD H 2013 J. Alloys Compd. 549 46 10.1016/j.jallcom.2012.09.050
- Nayeb-HashemiA AClarkJ B 1988 Phase Diagrams of Binary Magnesium Alloys Materials Park, OH ASM International
- KangD HParkS SKimN J 2005 Mater. Sci. Eng. A 413–414 555 10.1016/j.msea.2005.09.022
- SasakiT TYamamotoKHonmaTKamadoSHonoK 2008 Scr. Mater. 59 1111 10.1016/j.scriptamat.2008.07.042
- Van der PlankenK 1969 J. Mater. Sci. Lett. 4 927 10.1007/BF00549785
- DergeGKommelA RMehlR F 1937 Trans. AIME 124 367
- HenesSGeroldV 1962 Z. Met.kd. 53 743
- Pekgüleryü ZM ÖAvedesianM M 1992 Jpn J. JILM 42 679 10.2464/jilm.42.679
- MendisC LBettlesC JGibsonM AHutchinsonC R 2006 Mater. Sci. Eng. A 435–436 163 10.1016/j.msea.2006.07.090
- SonH TLeeJ BJeongH GKonnoT J 2011 Mater. Lett. 65 1966 10.1016/j.matlet.2011.03.083
- SasakiT TOh-ishiKOhkuboTHonoK 2006 Scr. Mater. 55 251 10.1016/j.scriptamat.2006.04.005
- ChengW LParkS STangW NYouB SKooB H 2010 Trans. Nonferr. Met. Soc. China 20 2246 10.1016/S1003-6326(10)60636-X