Abstract
Hot rolled strips having a minimum yield stress of 700 MPa have been produced in full scale processing. Alloy additions (1·5%Mn, 1%Cr and 0·3%Mo) together with rapid cooling on the run-out table produce fully bainitic microstructures which confer strength and toughness. Microalloying with 0·08%V has been shown to be essential for achieving stable strength levels that are independent of the coiling temperature since the necessary low coiling temperatures are difficult to reproduce accurately under steelworks conditions. The products have excellent bendability and HAZ toughness. Typical microstructures and textures of the hot rolled strips are also presented.
Introduction
Hot rolled strip steels with thicknesses 3–15 mm are important commercial products with applications in many different areas such as vehicles, mobile cranes and buildings. Efforts have been made over many years to raise the strength level in these products to reduce weight and save money in their application. The simplest C–Mn variants have yield stresses in the region of 350 MPa but this can be increased to around 450 MPa by employing controlled accelerated cooling to refine the ferrite grain size.Citation1 Microalloying has proved to be an effective means of improving the strength further.Citation2,Citation3 Small additions (<0·1%) of Nb, Ti, and V, individually or in combination, raise the strength for two reasons. They help to restrict recrystallisation and grain growth during hot rolling so that the final austenite grain structures are refined which creates prolific nucleation of ferrite during cooling leading to extra refinement of the final grain structure. At the same time, precipitation of microalloy carbides and nitrides takes place since these phases are much less soluble in ferrite than in austenite, which provides for further strengthening by the finely dispersed particles. By these means, it is possible to achieve yield stress levels of at least 600 MPa in ferrite–pearlite steels but further increases in strength are problematic so alternative strategies are being sought by many steel producers.
The natural approach towards reaching higher strength is to make use of acicular transformation products, bainite or martensite, instead of precipitation strengthened polygonal ferrite. Much higher strength is easily reached in martensitic steels by adjusting the carbon content but this is to the detriment of other equally important properties. Ductility, toughness and weldability are all reduced as the strength level rises and the practical necessity is for a steel chemistry and process route that can provide an optimal balance in strength together with other properties, in particular with acceptable bendability and weldability. The present work was based on recent laboratory scale experiments that were designed to identify the most suitable conditions of steel chemistry and processing.Citation4 The principal aims and findings were that:
(i) | the carbon content should be maintained at a sufficiently low level that toughness in the base metal and also in weld HAZ structures should not be a problem. A target of <0·05% C was adopted | ||||
(ii) | alloying with elements to enhance hardenability was reviewed to predict the necessary contents for bainite formation on the run-out table after hot rolling. The initial aim was for through hardening of 8 mm plate with a cooling rate of 30 K s−1 which could be achieved with additions of 1·5%Mn, 1%Cr and 0·25%Mo | ||||
(iii) | microalloying with V and N proved to be essential to prevent loss of strength by tempering (recovery) of the steel after coiling. Measurement and control of coiling temperatures below about 500°C presents major difficulties in a steelworks environment so the virtue of V–N microalloying is to make the material relatively insensitive to the actual coiling temperature. It is, of course, necessary that this temperature is sufficiently low that the resulting microstructures are nearly fully bainitic. Dilatometer studies indicated that the coiling temperature should not be higher than about 450°C. |
Some selected results from the previous study are shown in . Two steels having similar chemistries apart from microalloying with 0·08%V were cooled in different ways following hot deformation in the austenite range. After direct cooling to room temperature their yield stresses were virtually identical. However, when the specimens were given simulated coiling treatments (at 400 or 500°C) or when the direct cooled specimens were reheated to 600°C, significant loss in strength was observed in the steel without vanadium due to recovery of the dislocation substructure. The V microalloyed steel was almost unaffected because precipitation or segregation of VN inhibited recovery so that strength was retained. Because of the small scale laboratory melts used in the previous work it was only possible to evaluate the products on the basis of their yield stresses from compression tests and their microstructures. Nevertheless, the results looked so promising that it was decided to pursue this line of development with full scale products where other important properties could also be determined.
Investigations
A number of full scale casts of steel have been made at SSAB Luleå and the slabs have been hot rolled on the strip mill at SSAB Borlänge. Most of the results presented here were obtained using a cast with the chemical analysis shown in . The composition corresponded very closely with the target analysis which was based on the laboratory melt A5 of the previous investigation.Citation4 Note that the nitrogen content is intentionally high since vanadium has a strong tendency for nitride formation and nitrogen is regarded as a valuable microalloying element in these steels.Citation5
Table 1. Chemical composition of steel used principally in present investigation in wt-%
The slabs were hot rolled with effective cooling on the run-out table and coiled at various temperatures. All present results refer to strips rolled to 8 mm thickness.
Extensive mechanical testing was undertaken using tensile specimens and Charpy specimens along both the rolling and transverse directions of the strip. In some cases the specimens were sampled from the full width of the strips. Bendability was assessed on specimens with the bend axis aligned along both the rolling and transverse directions. Experiments were also carried out to assess the toughness in weld heat affected zones (HAZ). Samples were heated in a programmable weld simulator to a peak temperature of 1350°C and held for 3 s before cooling at different rates to room temperature. The cooling rate which in practice depends on the heat input during welding is defined in terms of the time to cool through the transformation range from 800 to 500°C. This parameter Δt8/5 was varied in the range from 3 to 35 s.
Microstructures were characterised using optical and scanning electron microscopy. The most informative method for these acicular bainitic structures is using electron backscattering diffraction (EBSD). This was done with a Jeol 700 FEGSEM instrument in combination with HKL software. Quantitative data relating to the interspacing of low angle lath boundaries and high angle packet boundaries was obtained by these means. An estimate of the prior austenite grain (PAG) sizes could also be obtained from the EBSD maps by identifying grain boundaries having misorientations within the intermediate range 15–50°. Lath and packet boundaries of bainite have either small or large misorientations so these are filtered out when selecting the intermediate range. Some true austenite grain boundaries are also lost in this process with the result that the true austenite grain sizes should be uniformly about 30% larger than the measured ones. The EBSD data from large maps were also used to deduce the texture of the bainite using pole figures.
Mechanical properties
Tensile test results are summarised in for five different strip conditions. The yield stress values comfortably exceed the target of 700 MPa excepting for the material that was coiled at the highest temperature of 530°C. Tensile strength values mostly exceed 800 MPa and total elongation values are in the range 11–14% for the bands having adequate strength levels. The strength levels are similar in the rolling and transverse directions within the reproducibility of the results while the ductility is slightly less in transverse direction tests as is commonly the case in hot rolled steels. Although the total elongation values are >11%, the uniform elongations lie typically in the range 2–4%. There is a significant necking strain associated with a large reduction of area at fracture in these materials. Strength and ductility values were very uniform across the width of the strip. Only samples that were very close to the edges (<30 mm) showed any inferior properties.
Table 2. Summary of tensile test properties including 0·2% proof stress (Rp02), tensile strength (Rm), total elongation (A5) and uniform elongation (Ag)
Other mechanical properties and results from quantitative metallography are summarised in . Toughness values are acceptable down to the lower test temperature of −60°C. Note that these have been normalized to nominal fracture areas of 1 cm2 since the samples are 8 mm thick and so the specimens are subsize. The Charpy energies are lower in transverse than longitudinal tests, that is to say when the fracture plane contains the rolling direction. There is also a tendency for lower Charpy energies in plates that were coiled at the higher temperatures despite the fact that these plates showed somewhat lower strength. The usual inverse relationship between strength and toughness appears not to apply in these steels.
Table 3. Summary of Charpy energies and grain sizes for various strip coiling conditions
The effect of coiling temperature on strength and Charpy toughness is shown in . As seen in this figure, the strength is only slightly affected by coiling temperature up to about 450°C which is a benefit for ensuring that this property is stable with regard to unavoidable fluctuations in the process parameter. Previous work indicated that the presence of vanadium and nitrogen atoms in the steel pin dislocations and so retard recovery of the bainitic substructure that contributes much of the strength. Such behaviour is clearly borne out in the present results. At higher temperatures and, in particular above 500°C, the yield stress and tensile strength fall significantly as thermally activated recovery processes accelerate.
It is interesting that Charpy energies follow a similar trend to the tensile test results. All the specimens failed with extensive ductile fracture so it may be supposed that the plastic work varies proportionally with the flow stress. This is also in conformance with the fact that the total elongation values were virtually independent of the coiling temperature and strength level. No significant change in the failure process is seen.
Another property of technological importance for these hot strip products is their capability to be bent. More extensive plate forming is seldom applied but bendability is a crucial requirement. Usually, bendability is expressed as the ratio of the critical bend radius R to the plate thickness t. The criterion used to define the critical radius is the first observation of a crack on the exterior, convex surface. The requirement is that R/t should be less than 2·5. Bends are carried out on strips cut along the rolling L and transverse T directions of the plate. Commonly, the bendability is worse for transverse tests, being affected by inclusion stringers and surface defects. Results are summarised in for three plates having a range of yield stresses after coiling at different temperatures.
Table 4. Results of bendability on three plates*
It can be seen from that all the plates satisfy the pass criterion with a substantial margin. The present materials have excellent bendability, probably because the microstructures are very homogeneous with few coarse particles that lead to nucleation of voids in the outer fibres of the bends. Also, directionality of the bending results is quite marginal in most cases.
Weldability
So far, only limited welding tests have been carried out on these strips. However, evaluations have been made of the toughness in high temperature heat affected zones using simulated thermal cycles followed by Charpy testing. Four different cooling times, Δt8/5, were applied to see the effect of heat input levels. Fracture energy values are plotted as a function of the test temperature in . The transition in fracture energy extends over a wide range of temperature but in most cases the commonly used criterion of 40 J cm−2 occurs around −60°C which is considered to imply very good toughness. Only the fastest cooling condition with Δt8/5 of 3 seconds has a somewhat higher value of about −40°C but even this can be considered as fully satisfactory in most applications.
Microstructures and textures
Examinations were carried out on cross-sections of the hot strips perpendicular to their transverse directions. Careful comparisons were made of structures at different depths below the plate surfaces but no significant or systematic differences could be seen at these different locations so all the results presented here are taken from positions near to the centre line of the plates. Optical micrographs for three different coiling temperatures are shown in .
4. Optical micrographs for hot strips coiled at a 180°C, b 320°C and c 500°C: magnification markers are 10 μm; RD horizontal; ND vertical
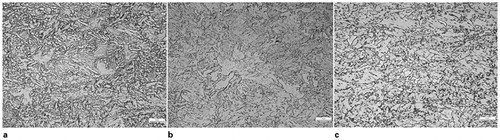
The microstructures are bainitic/acicular in all cases with no evidence of polygonal ferrite. There is possibly a tendency for the structures to be somewhat more acicular at the lower temperatures and rather more granular with larger carbide particles at higher temperatures. However, the microstructures are very homogeneous with little evidence of inheritance from the prior austenite and only slight elongation in the rolling plane. Since it is difficult to quantify such structures in optical microscopy, more detailed investigations were made using EBSD. These were also made at different depths in the plates but as they did not show significant differences only the central regions are reported here.
Representative EBSD maps for the same samples as in are shown in . Several sorts of quantitative data can be extracted from these maps as presented in . When choosing only grain boundaries with misorientations in the range from 15 to 50°, one selects only the boundaries that were present in the prior austenite and not in the bainite, so this permits estimates to be made of the prior austenite grain sizes. Mean intercept lengths in these cases are of the order of 8 μm but as some austenite boundaries are systematically omitted, a more correct result should be in the vicinity of 10 μm. It is noteworthy that the measured PAG sizes are larger along the rolling direction than along the plate normal direction but the difference is only about 20%. The fact that these prior austenite grains were small and fairly equiaxed, compared to many other hot rolled steels, implies that recrystallisation of the austenite must have continued to take place to a late stage during strip rolling and possibly even after the final hot rolling pass.
5. EBSD maps with IPF colouring with thin black lines for misorientations 2–20° and thick white lines for misorientations >20°: coiling temperatures were a 180°C, b 320°C and c 500°C; magnification marker is 50 μm
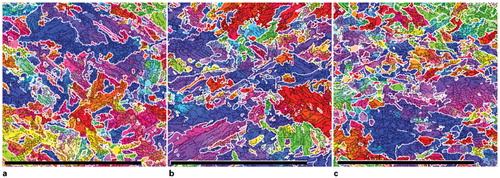
The ferrite grains are small and quite uniform in size. They become possibly less acicular and more globular in shape as the coiling temperature is raised. However, all the structures appear to be bainitic in character, judging from the grain boundary misorientation distributions (not shown) that are similar in all cases. Polygonal ferrite differs considerably in this respect. Considering high angle grain boundaries only (misorientations >20°) gives a ferrite grain size of just under 3 μm. When low angle grain boundaries are also includes (misorientations >2°) the average ferrite grain size is around 1 μm or slightly more. These values are rather independent of the processing conditions although it seems possible to discern a slight reduction in both as the coiling temperature decreases. Such an effect could contribute to the strength and toughness behaviour described above although the more prominent decreases above 500°C do not appear to be explicable only on this basis. In the previous investigationCitation4 it was concluded that much of the strengthening in these steels arises from the high densities of dislocations that are generated during phase transformation. These are difficult to measure experimentally but a reasonable interpretation of the present results is that significant recovery can occur after coiling at temperatures above about 500°C, reducing the density of dislocations. At lower temperatures, recovery is markedly inhibited by the presence of vanadium and nitrogen atoms but this retardation is not sufficiently effective above 500°C.
Textures of the same three hot strips are shown in the form of φ2 = 45° sections of the orientation distribution functions (ODFs) derived from EBSD maps are shown in . These are fairly typical for hot rolled steelsCitation6 showing components such as {112}<110>, {001}<{110}, {112}<311> and {233}<311>. The textures are less strong than in many strip steel products which is consistent with the metallographic evidence showing that the austenite had recrystallised towards the end of hot rolling. The weak texture is also compatible with the mechanical test results which showed little difference in strength between the rolling and transverse directions.
General discussion
The present full scale steel production data are in good agreement with the previous limited results from laboratory scale trials regarding the yield stresses and microstructures of this steel (4). Adequate hardenability is achieved through the addition of 1·5%Mn, 1·0%Cr and 0·3%Mo to ensure that transformation to bainite is complete on cooling at 30 K s−1 which is approximately the rate that applies on the run-out table with 8 mm thick strip, down to a coiling temperature around 400°C. This was quite apparent from the microstructures of the present materials which were all free from polygonal ferrite. In addition, the structures are very uniform throughout the thickness of the plates. The EBSD examinations indicate strongly that recrystallisation of the austenite took place during hot deformation up to and perhaps after the final the final rolling pass, creating a uniform and fine grained condition prior to the rapid cooling.
The strength of the products depends somewhat on the coiling temperature but below ∼450°C the yield stress and tensile strength are virtually constant. At higher temperatures and in particular above 500°C there is a significant softening and the target yield stress of 700 MPa is not achieved. Nevertheless, when viewed in conjunction with the previous results (4), there is strong evidence that the presence of vanadium and nitrogen do increase the stability of the strengthening so that it is insensitive to coiling temperatures over a wide practical range.
Previous workCitation4 showed that the bainitic dislocation substructure contributes a major part of strength in this type of steel, and that the segregation or precipitation of V(C,N) at dislocations impedes the recovery of this substructure, so retaining the strength of the bainite effectively after coiling. Such behaviour is clearly borne out also in the present results. In this work, as well as in the previous, it was found that the strength falls significantly at 500°C and above. Coiling in this temperature regime implies that practically all the bainite is formed at or above 500°C. It was also foundCitation4 that the strength of the same bainite that lacked V microalloying decreases quite sharply already at 400°C and significantly more above 500°C. For the present steel, microalloyed with vanadium and nitrogen, this implies that when coiled at temperatures above 500°C the bainitic substructure may recover rather rapidly before the V(C,N) has time to precipitate, hence resulting in a reduction in strength. Further recovery and associated softening may also be possible in the pinned substructure after coiling at the higher temperatures. With the present results showing an invariance of the ferrite grain size with coiling temperature, or possibly a very modest increase, it therefore seems highly probable that early recovery of the bainite substructure during coiling is the primary cause of the decline of strength at temperatures above 500°C and that the variation of ferrite grain size affects this only marginally.
The uniform microstructure and the absence of any larger carbide particles or other hard phases ensures good ductility, in particular area reduction during necking and high toughness at temperatures down to at least −40°C as measured in the Charpy tests. Probably for the same reasons, the plates show excellent bendability for both rolling and transverse tests. In all cases the bendability tests far exceeded the requirements in current usage.
Only limited investigations have so far been carried out as regards weldability of this material. For example the optimum choice of consumables still needs to be clarified. However, the simulation tests suggest that the HAZ regions should satisfy all requirements in terms of toughness. Charpy energies at room temperature exceeded 150 J cm−2 under all conditions that were tested and the ductile–brittle transition temperatures were all below −40°C based on the 40 J cm−2 criterion. The intentionally low carbon content of <0·05% is considered to be an important factor regarding the HAZ toughness.
Conclusions
The present concept provides a way of producing hot rolled strip products with a minimum yield stress of 700 MPa having attractive formability, toughness and weldability.
A fully bainitic microstructure is achieved by optimised alloy contents of Mn, Cr and Mo in combination with rapid cooling after final hot rolling.
Microalloying with vanadium is an essential feature of the steel that ensures mechanical properties are stable and largely independent of the precise coiling temperature (below about 450°C), which is difficult to control accurately in the steelworks environment.
Acknowledgements
The authors are grateful to Vanitec for financing the work at SwereaKIMAB and to David Milbourn of Vanitec for his enthusiastic support during the project. They also thank numerous colleagues at SSAB-EMEA, in particular Leif Bader, and also colleagues at SwereaKIMAB for their practical assistance.
References
- Hutchinson W. B.: ‘Microstructure development during cooling of hot rolled steels’, Ironmak. Steelmak., 2001, 28, 145–151.
- Gladman T.: ‘The physical metallurgy of microalloyed steels’; 1997, London, Institute of Materials.
- Korchynsky M. (ed.): Microalloying ’95, Iron and Steel Society, Pittsburgh, PA, USA, 1995.
- Siwecki T., Eliasson J., Lagneborg R. and Hutchinson B.: ‘Vanadium microalloyed bainitic hot strip steels’, ISIJ Int., 2010, 50, 760–767.
- Lagneborg R., Siwecki T., Zajac S. and Hutchinson B.: ‘The role of vanadium in microalloyed steels’, Scand. J. Metall., 1999, 28, 186–241.
- Ray R. K. and Jonas J. J.: ‘Transformation textures in steels’, Int. Metall. Rev., 1990, 35, 1–36.