ABSTRACT
A detailed experimental study has been carried out to evaluate the heat transfer performance of a solid/liquid phase-change thermal energy storage system. The phase-change material, 99% pure eicosane with a melting temperature of 36.5°C, was contained in a vertically oriented test cylinder that was cooled or heated at its outside boundary, resulting in radially inward freezing or melting, respectively. Detailed quantitative time-dependent temperature distributions and melt-front motion and shape data were obtained. In the freezing case study, a mathematical model was developed based on a one-dimensional analysis, which considered heat conduction as the only mode of heat transfer. In the melting case study, a heat transfer scale analysis was used to help interpret the data and development of heat transfer correlations. In the melting scale analysis, conduction heat transfer in the solid and natural convection heat transfer in liquid were considered. Comparison of experimental data with scale analysis predictions of the solid-liquid interface position and temperature distribution was performed. The analytical results agreed, in the worst case, within 10% of the experimental results in both melting and freezing cases. In the case of melting, scale analysis results agreed within 5% (after initial superheat disappeared in 50 minutes) with experimental results, and experimental results confirm the existence of four melting regions.
Nomenclature | ||
a,b | = | Constants |
cp | = | Specific heat of water, kJ/kgK |
Fo | = | Fourier number of solid eicosane, dimensionless |
H | = | Height of the tank, m |
g | = | Gravitational constant, m2/s |
h | = | Convection heat transfer coefficient, W/m2K |
h(subscript) | = | Height in a given regime, m |
k | = | Thermal conductivity, W/m2°C |
m | = | Mass, kg |
= | Mass flow rate, kg/s | |
Nu | = | Nusselt number, dimensionless |
Pr | = | Prandtl number |
q | = | Heat transfer rate, W |
Q | = | Heat transfer, kJ |
R | = | Relative uncertainty, dimensionless |
Ra | = | Rayleigh number, dimensionless |
r | = | Radius, m |
s | = | Thickness of the liquid PCM, m |
St | = | Stefan number, dimensionless |
t | = | Time, s |
T | = | Temperature, °C |
u | = | Velocity in radial direction, m/s |
w | = | Velocity in axial direction, m/s |
x, X | = | Uncertainty variables |
z | = | upper convection region height |
Greek symbols | ||
α | = | Thermal diffusivity, m2/s |
β | = | Coefficient of thermal expansion, 1/K |
βr | = | Radius of fusion, dimensionless |
δ | = | Thermal boundary layer thickness, m |
δx | = | Difference of x |
Δ | = | Change |
Δhfus | = | latent heat of fusion, kJ/kg |
θ | = | Time for the scale analysis, dimensionless |
μ | = | Absolute viscosity, Ns/m2 |
ν | = | kinematic viscosity, m2/s |
ρ | = | Density, kg/m3 |
τ | = | Time, dimensionless |
ψ | = | heat balance integral, m2°C/s |
Subscripts | ||
1, 2, 3 | = | System heat transfers |
I, II, III, IV | = | Melting regimes |
b | = | bulk |
comp | = | component |
conv | = | convection |
f | = | final |
f-s | = | sensible heat, subcooling liquid |
fus | = | fusion |
i | = | initial |
l, liq | = | liquid |
l-f | = | sensible heat, superheated liquid |
m | = | mean |
meter | = | measured value |
min | = | minimum |
sen | = | sensible |
s | = | solid |
TC | = | thermocouple |
tot | = | total |
w | = | wall |
Additional information
Notes on contributors
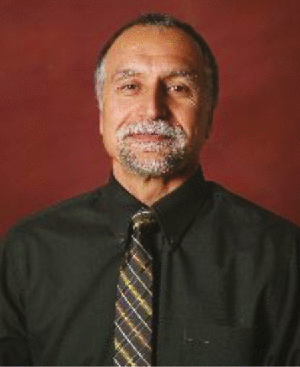
Ali Siahpush
Ali Siahpush is an Associate Professor at Southern Utah University. He received his Ph. D. in Mechanical Engineering from University of Idaho, Idaho Falls, Idaho. He has over 24 years of experience in nuclear industry, and over 10 years of higher education teaching experience. He has notability and recognition in the heat transfer, aerospace, and thermohydraulic fields. He also has experience in the fields of department of energy reliability in engineering design. He is the owner of five patents within the field of Systems for Delivering Liquefied Natural Gas to an Engine, and author of over thirty peer reviewed technical publications.
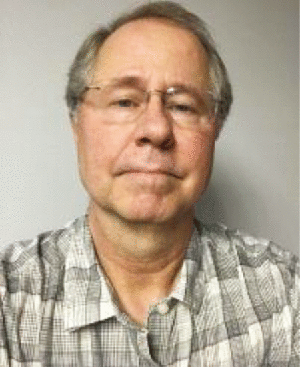
James O'Brien
James O'Brien is a Senior Research Engineer in the Fusion, Hydrogen, and Measurement Sciences Department at the Idaho National Laboratory. He received his Ph.D. in Mechanical Engineering from the University of Minnesota in 1981 with a specialty in Heat Transfer. He served as a member of the ME faculty at The Pennsylvania State University from 1981 – 1985 and as a research engineer at NASA Lewis (now Glenn) Research Center from 1985 – 1990. He joined the Idaho National Laboratory (INL) in 1990. While working at INL, he has performed research on boiling heat transfer, heat transfer enhancement, reactor thermal hydraulics, severe accidents, high-temperature electrolysis for nuclear hydrogen production, energy conversion, and other energy-related research topics. He is currently working to develop a new multi-loop, multi-fluid advanced test facility designed to examine thermal hydraulic and materials issues associated with advanced nuclear reactor technologies. He is the author or co-author of 5 book chapters, 40 journal articles and more than 130 conference papers on a variety of topics in thermal sciences. He has also been awarded 10 patents. He has received numerous awards, and is an active member of the American Society of Mechanical Engineers (ASME). He has also served as a technical consultant for IAEA on non-electric applications of nuclear energy.
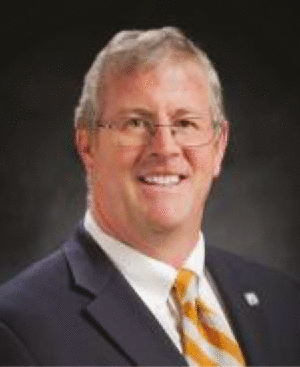
John Crepeau
John Crepeau received his Bachelor degree in mechanical engineering from the University of California, Berkeley, and his Master and Doctoral degrees, also in mechanical engineering from the University of Utah. After completing an NSF-NATO Postdoctoral Research Fellowship at Humboldt University in Berlin, Germany, he was appointed an assistant professor at the University of Idaho, where he is currently a full professor.
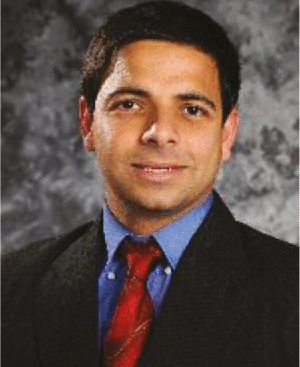
Piyush Sabharwall
Piyush Sabharwall is a research staff scientist working in the Nuclear Science and Technology division at Idaho National Laboratory. He has a premier role in the development of very high temperature nuclear reactor technologies that are integral to the Department of Energy strategic plans for the sustained advances in nuclear energy. He has expertise in heat transfer, fluid mechanics, thermal design, thermodynamics, system modeling and nuclear safety analyses. He has extensive experience in the design and construction of large-scale experimental systems for nuclear and thermal-hydraulic research, he is currently developing a new high-temperature multi-fluid, multi-loop test facility (known as the Advanced Reactor Technology Integral System Test [ARTIST] facility to enable development of gas cooled, molten salt cooled and water cooled reactors along with development and application of heat utilization using innovative techniques in nuclear hybrid energy systems. He has published over 100 publications including journal articles, conference proceedings, and technical reports. He has been a significant catalyst for international and national research partnerships in the field of nuclear science and engineering. He has been an active member of the ASME Heat Transfer Division (particularly the K-13 and K-9 committees) and the ANS Thermal Hydraulic Division. In 2011 he received the New Faces of Engineering ASME National Award and was also the recipient of the ANS 2013 Young Member Excellence Award.