Figures & data
Figure 1. Schematic illustrations of sub-response matrices. (a) Transmission probability. (b) Neighbor-induced production probability. (c) Self-induced production probability. (d) Escape probability.
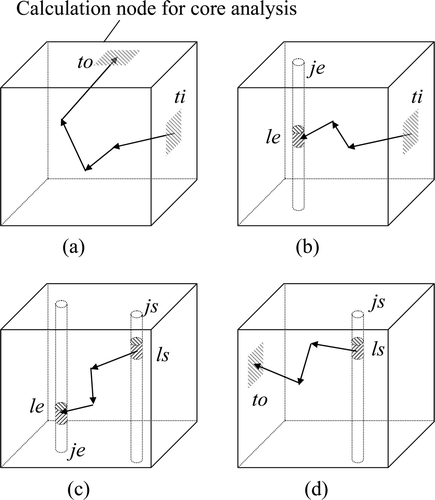
Table 1. Core characteristics and fuel assembly specifications of BASALA experiments.
Figure 3. Configuration of reference core for core 1. The percentages are wt % of Pu total content and the numbers are the numbers of each type of rod.
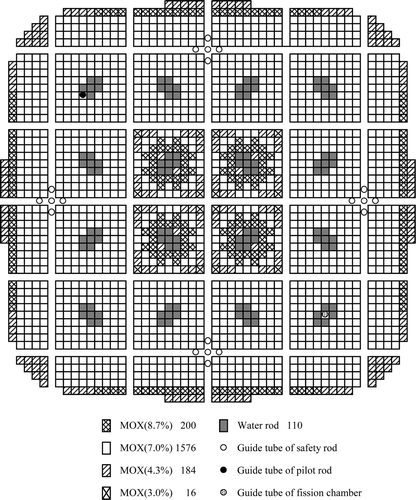
Figure 4. Configuration of reference core for core 2. The percentages are wt % of Pu total content and the numbers are the numbers of each type of rod.
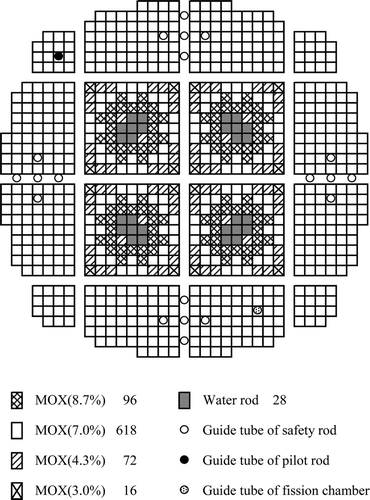
Figure 5. Configuration of 8Gd core for core 1. The percentages are wt % of Pu total content and the numbers are the numbers of each type of rod.
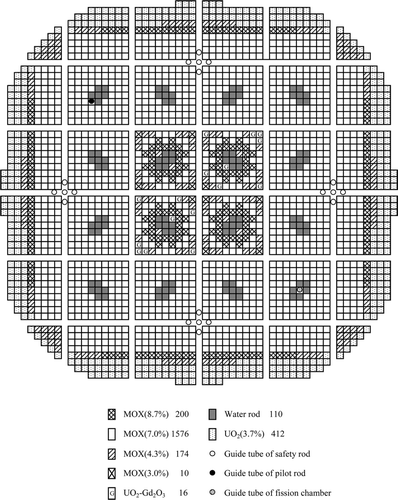
Figure 6. Configuration of 16Gd core for core 1. The percentages are wt % of Pu total content and the numbers are the numbers of each type of rod.
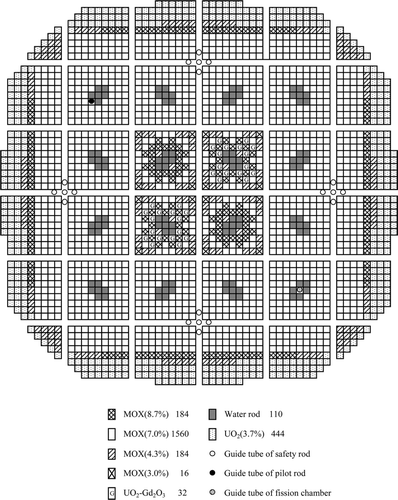
Figure 7. Configuration of 8Gd core for core 2. The percentages are wt % of Pu total content and the numbers are the numbers of each type of rod.
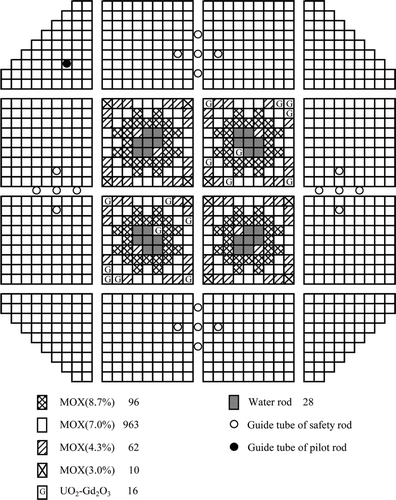
Figure 8. Configuration of 16Gd core for core 2. The percentages are wt % of Pu total content and the numbers are the numbers of each type of rod.
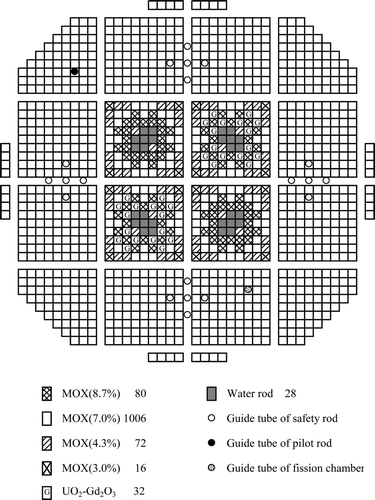
Figure 9. Configuration of 2D void core for core 1. The percentages are wt % of Pu total content and the numbers are the numbers of each type of rod.
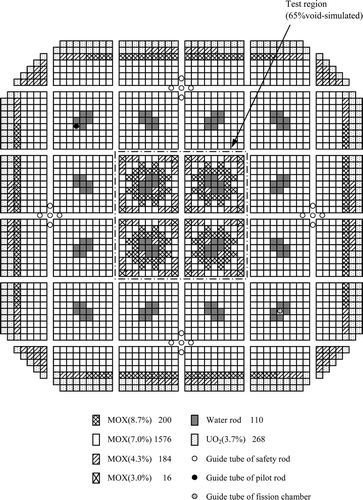
Figure 10. Configuration of water rod core for core 1. The percentages are wt % of Pu total content and the numbers are the numbers of each type of rod.
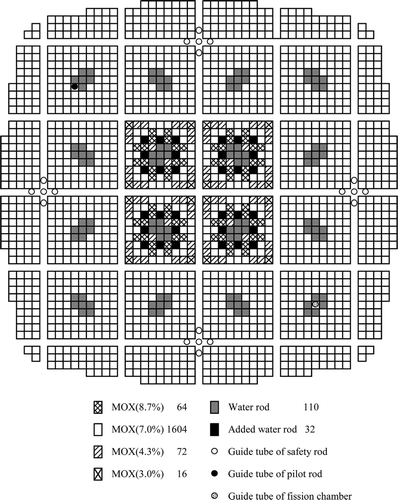
Figure 11. Configuration of control blade inserted core for core 2. The percentages are wt % of Pu total content and the numbers are the numbers of each type of rod.
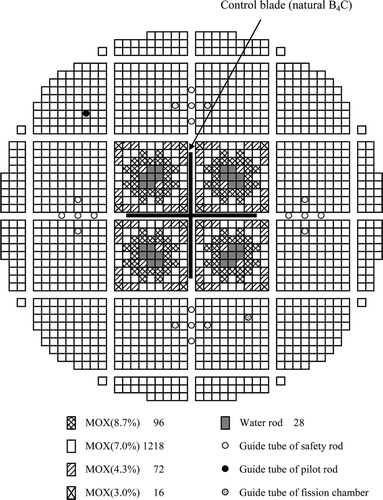
Figure 12. Illustrations of sub-surfaces and angular segments. (a) Number of sub-surfaces and angular segments : 4 × 4 and 4. (b) Number of sub-surfaces and angular segments : 4 × 4 and 16.
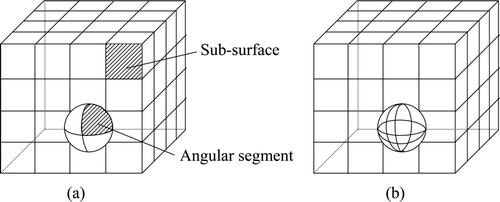
Table 2. Energy group structure for sub-response matrices.
Table 3. Critical k-effective values for reference cores.
Table 4. Root mean square and maximum differences of fuel rod fission rate distribution between calculation and measurement in diagonal direction for reference cores (unit:%).
Table 5. Root mean square and maximum differences of fuel rod fission rate distribution between calculation and measurement in test assembly for reference cores (unit:%).
Table 6. Critical k-effective values.
Table 7. Root mean square and maximum differences of fuel rod fission rate distribution between calculation and measurement in diagonal direction (unit:%).
Figure 23. Fuel rod fission rate distribution of control blade inserted core for core 2 (diagonal direction).
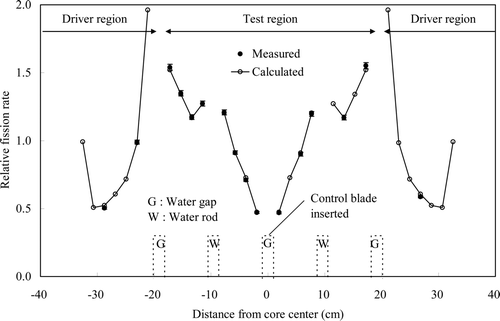
Table 8. Root mean square and maximum differences of fuel rod fission rate distribution between calculation and measurement in test assembly (unit: %).
Figure 30. Fuel rod fission rate distribution of control blade inserted core for core 2 (test assembly)
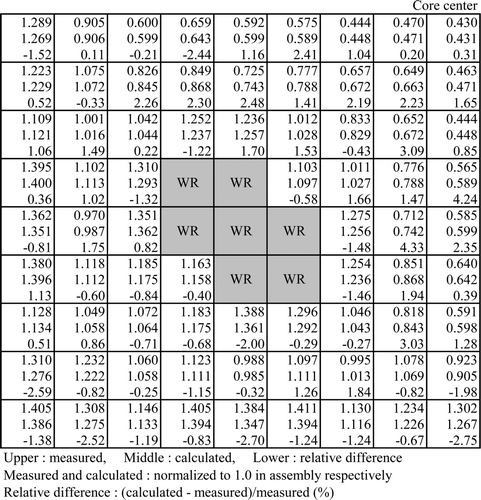