Figures & data
Figure 1. Ultrasonic beam orientations to detect axial and circumferential oriented flaws. (a) Transducer configuration for wall loss and axial crack. (b) Transducer configuration for circumferential crack.
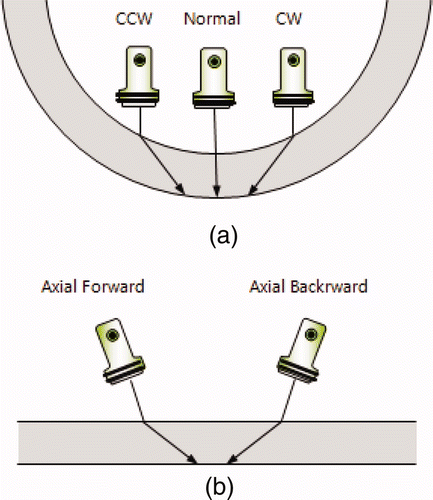
Figure 2. The modeling result of normal beam sound field focused at middle of tube thickness. (a) C-scan image. (b) B-scan image.
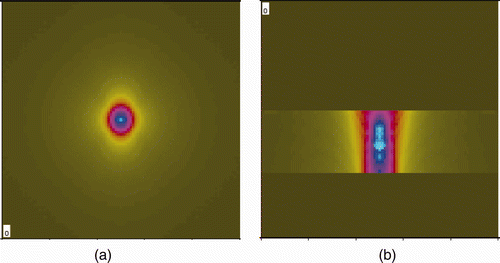
Figure 3. The modeling result of CCW and CW beam sound field focused at middle of tube thickness. (a) C-scan image. (b) B-scan image.
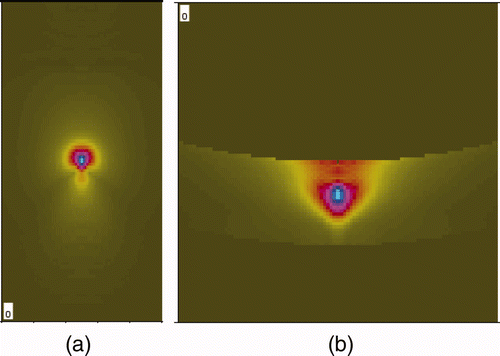
Figure 4. The modeling result of backward and forward beam sound field focused at middle of thickness. (a) C-scan image. (b) B-scan image.
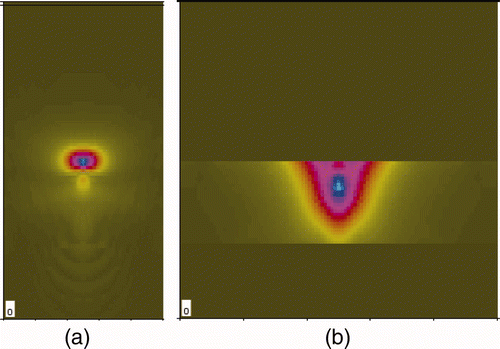
Figure 5. Ultrasonic transducer for steam generator tube inspection designed based on the modeling result. (a) Modeling result. (b) Manufactured multi-array ultrasonic assembly.
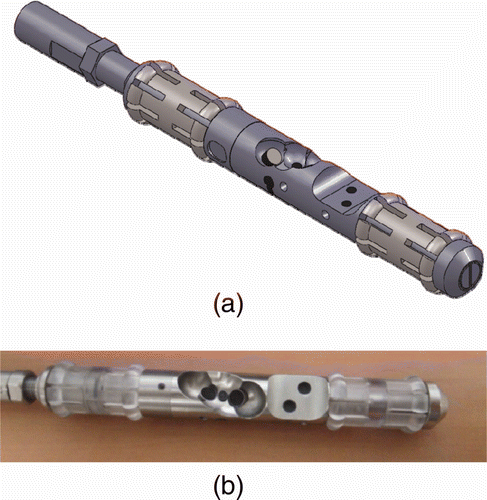
Table 1. Ultrasonic characteristic measurement of each element (at 6 dB).
Table 2. Dimensional specification of steam generator tube specimen.
Figure 6. Test tube drawing for the steam generator ultrasonic testing experiment with artificial flaws (unit : mm).
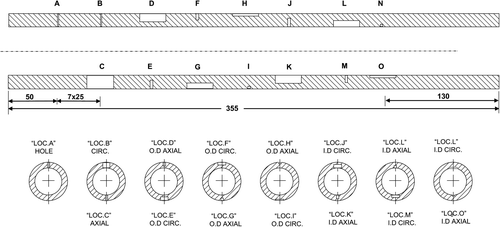