Figures & data
Figure 3. Confirmation of temperature rise due to laser welding: (a) measurement point locations; (b) temperature change due to laser welding.
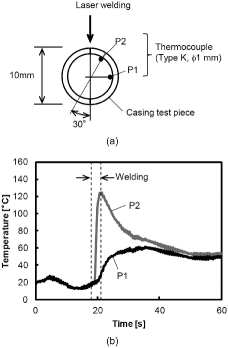
Figure 5. Instrument configuration: (a) connection with the instrument; (b) configuration for observing the pulse reflected from the casing surface; (c), (d) configuration for observing the pulse reflected from the liquid film surface.
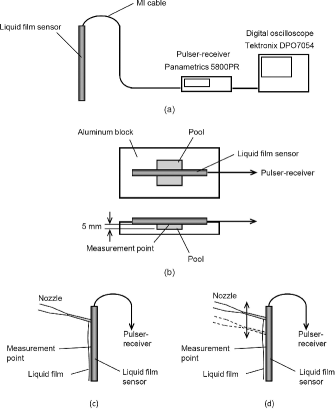
Figure 6. Waveforms obtained on an oscilloscope: (a) for the fixed nozzle position; (b) for the moving nozzle position.
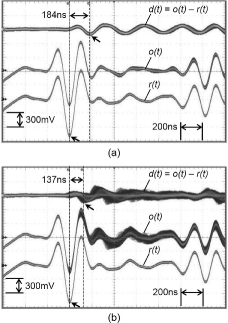
Figure 7. Time series liquid film thickness: (a) for the fixed nozzle position; (b) for the moving nozzle position.
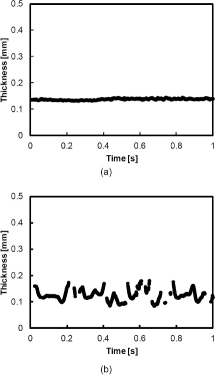
Table 1. Material properties at room temperature (20 °C).
Table 2. Material properties at 286 °C.