Figures & data
Figure 3. Ultrasonic sound field modeling results at (a) 45° and (b) 80° refraction angles at a 0.4-mm pitch.
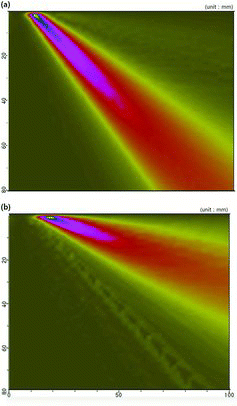
Table 1. Phased array probe and wedge specifications.
Figure 4. Phased array ultrasonic transducer and wedge for SG small bore piping socket weld inspection.
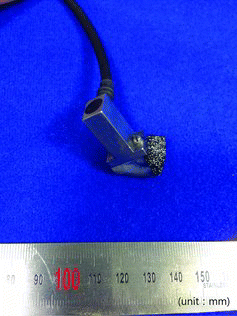
Figure 5. Manually operated ring-type encoded scanner for the small bore socket weld piping of steam generators.
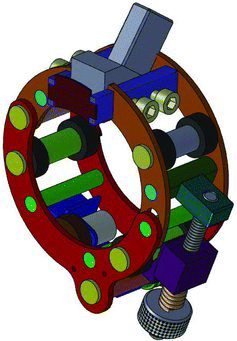
Table 2. Flaws introduced to specimens (unit: mm).
Table 3. Phased array system parameters for experimental.
Table 4. Flaw length sizing results of flawed specimens (unit: mm).