Figures & data
Figure 3. The hierarchical representation of the plant configuration including both the plant and human.
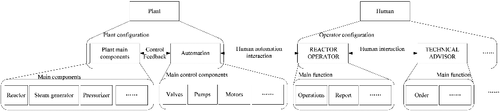
Figure 5. Configuration of passive safety system of AP1000 assumed in this study [Citation21,Citation22].
![Figure 5. Configuration of passive safety system of AP1000 assumed in this study [Citation21,Citation22].](/cms/asset/b6a0509a-0106-4000-9926-03052c039648/tnst_a_1417171_f0005_oc.jpg)
Table 1. Simulation results of the different scenarios
Figure 6. System pressure in case of SBLOCA (scenario 1 [Citation24] and scenario 2 [Citation23]).
![Figure 6. System pressure in case of SBLOCA (scenario 1 [Citation24] and scenario 2 [Citation23]).](/cms/asset/1a6a24fb-2964-43eb-9d5e-6ee5c411fd74/tnst_a_1417171_f0006_oc.jpg)
Figure 7. Activation sequence of safety system in case of SBLOCA (scenario 1) [Citation22]..
![Figure 7. Activation sequence of safety system in case of SBLOCA (scenario 1) [Citation22]..](/cms/asset/d4e110f1-1e4d-4e27-a369-2851070c2df6/tnst_a_1417171_f0007_oc.jpg)
Table 2. Sensor models for the different signals