Figures & data
Table 1. Chemical composition of the examined steel.
Table 2. Specifications of the CF tests.
Table 3. Parameters for extraction experiments.
Table 4. Parameters for automated SEM/EDS measurements.
Figure 2. Carbide and inclusion distribution of the investigated material HS6-5-3C in a SEM image captured using a backscattered electron detector.
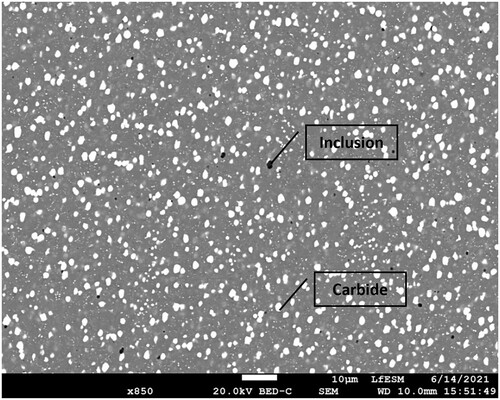
Figure 3. SEM-image in BSE-mode of a fracture-initiating inclusion on the fracture surface of a HCF specimen with corresponding EDS-elemental mappings.
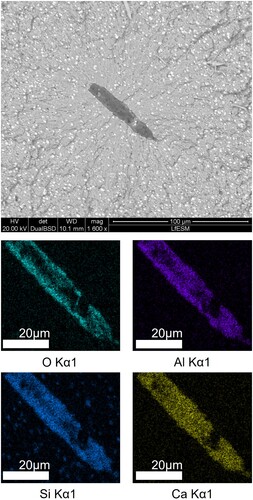
Figure 4. Relationship between the inclusion size and the load changes sustained by the samples in the HCF tests.
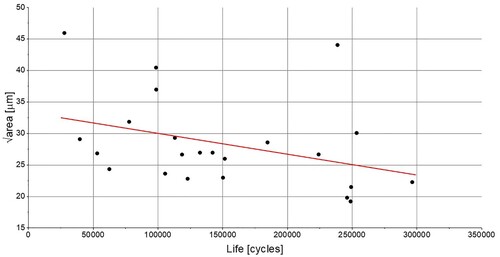
Figure 9. SEM-image in BSE-mode of oxide inclusions found on the filter after chemical extraction of specimen E3 (Duration: 7 days) with corresponding EDS-elemental mappings.
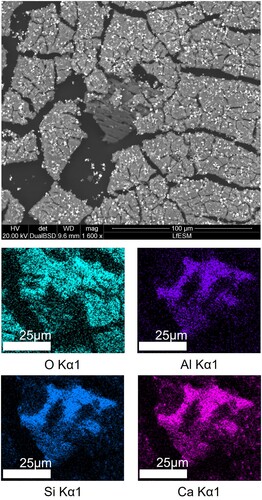
Figure 10. SEM-image in BSE-mode of oxide inclusions found on the filter after chemical extraction of specimen E1 (duration: 2 hours in 15-minute sequences) with corresponding EDS-elemental mappings.
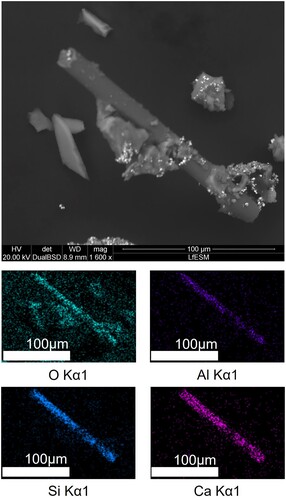
Figure 11. SEM/EDS elemental mapping of sulphide inclusions found on the filter after chemical extraction of specimen E1 (duration: 2 hours in 15-minute sequences).
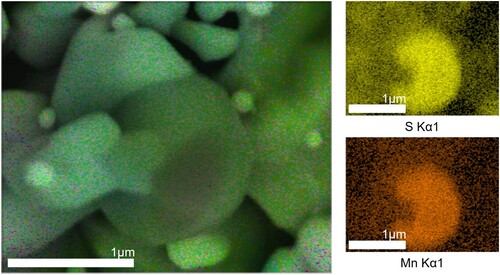
Figure 12. SEM-image in BSE-mode of oxide-sulphide inclusions found on specimen 7 with corresponding EDS-elemental mappings.
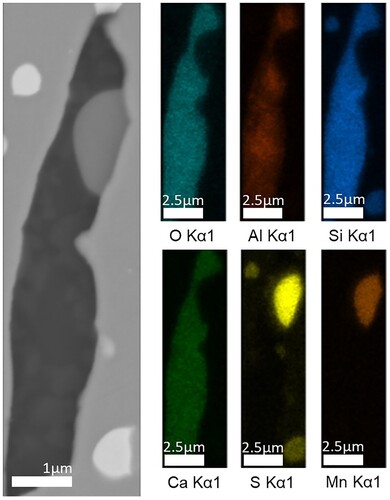
Figure 14. Comparison of inclusion composition between specimen 7 (a) and HCF samples (b) analysed with automated SEM/EDS.
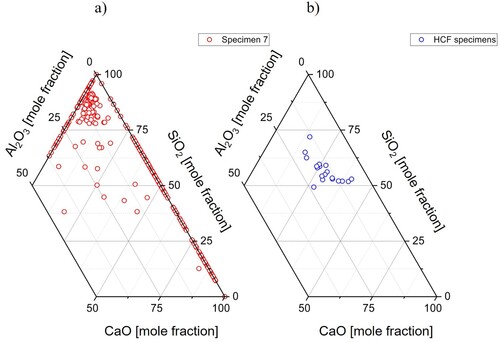
Table 5. Determined parameters of the investigated specimens.
Table 6. Calculated maximum inclusion sizes of the GPD method compared with the results for the Gumbel distribution.
Table 7. Method matrix with the findings from the performed analyses.