Figures & data
Figure 1. Tyre-road schematics in the Oxz and Oyz planes (left and right-hand side figures, respectively). The geometric parameters are drawn in black, the kinematic quantities in green, the generalised forces in blue and the elastic displacements in red. The dimension and the deformation of the bristles have been exaggerated to facilitate the visualisation.
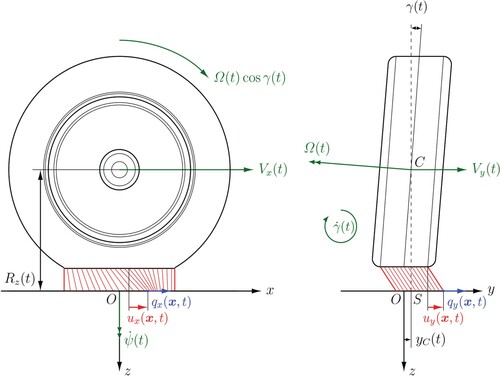
Figure 2. Subdomains ,
and
of the contact patch
(represented by the rectangles) for different values of the camber angle
, 30, 50 and
, respectively. The larger green area corresponds to the domain
, whilst the red and blue one to
and
. The arrows represent the velocity field
and are always tangent to the trajectories of the bristles, which coincide with the characteristics lines given by (Equation41a
(41a)
(41a) ). The length and the width of the contact patch are l = 0.1 and w = 0.07 (m). (a) Domains
,
and
for a camber angle of
. (b) Domains
,
and
for a camber angle of
. (c) Domains
,
and
for a camber angle of
. (d) Domains
,
and
for a camber angle of
.
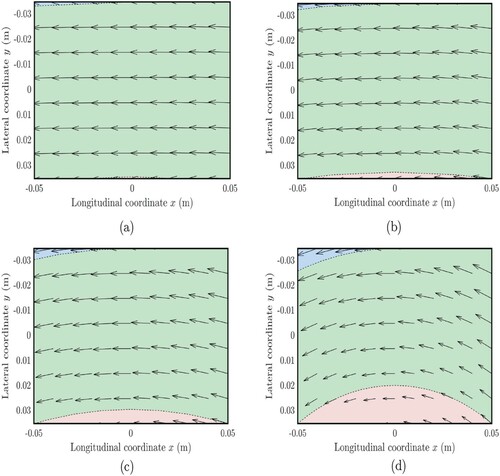
Figure 3. Steady-state and transient domains for each region of for a constant value of the camber angle
and different travelled distances
, 1/8, 1/4 and 1/2. The green, red and blue solid lines represent the interface between the steady-state and transient solution in the domains
,
and
, respectively. More specifically, the steady-state regions correspond to the right portion of the green and red areas for
and
, and to the upper part of the blue domain for
. It can be noted that steady-state conditions are reached in the region
relatively faster (the transient extinguishes in the blue area already for
). The length and the width of the contact patch are l = 0.1 and w = 0.07 (m). (a) Steady-state and transient domains for each region of
for
. (b) Steady-state and transient domains for each region of
for
. (c) Steady-state and transient domains for each region of
for
. (d) Steady-state and transient domains for each region of
for
.
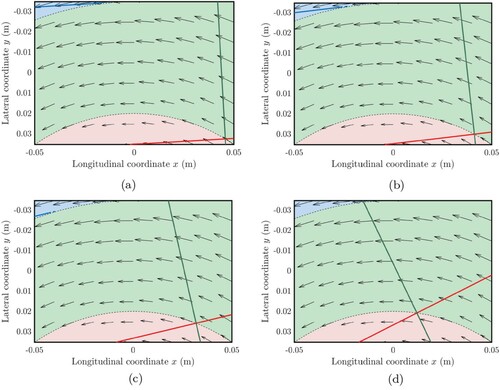
Figure 4. Steady-state and transient domains for each region of for a constant value of the camber angle
and different travelled distances
and 1/2. The functions
and
correspond to the green, red and blue curve, respectively, and represent the interface between the steady-state and blacktransient blacksolution in the domains
,
and
. It can be seen that they rotate tangentially to the circumferences
,
and
. (a) Steady-state and transient subdomains of the contact patch
corresponding to a normalised travelled distance of
. (b) Steady-state and transient subdomains of the contact patch
corresponding to a normalised travelled distance of
.
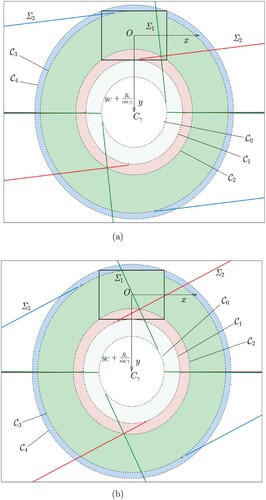
Figure 5. Transient trend of the total shear stress (
,
) predicted by the different models for two values of the normalised travelled distance
(left-hand side subplot) and
(right-hand side subplot). The figures refer to the following values of the kinematic parameters:
,
,
. (a) Total shear stress
predicted using the 1DCM. The left and right-hand side subplots refer to a value of the normalised travelled distance of
and 2, respectively. (b) Total shear stress
predicted using the 2DM. The left and right-hand side subplots refer to a value of the normalised travelled distance of
and 2, respectively. (c) Total shear stress
predicted using the 2DCM. The left and right-hand side subplots refer to a value of the normalised travelled distance of
and 2 respectively.
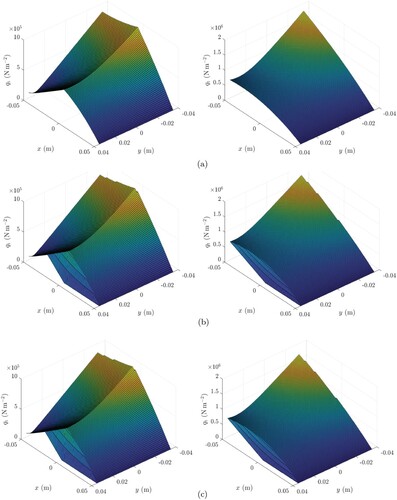
Figure 6. Tyre characteristics versus the longitudinal slip for different discrete values of the lateral slip
and steering ratio
. (a) Longitudinal and lateral tyre characteristics versus the longitudinal slip
for different values of the lateral slip
and steering ratio
. (b) Longitudinal and lateral tyre characteristics versus the longitudinal slip
for different values of the lateral slip
and steering ratio
.
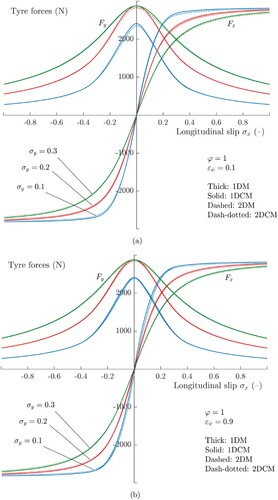
Figure 7. Self-aligning moment versus the longitudinal slip for different discrete values of the lateral slip
and steering ratio
. It can be noted that, for small values of the steering ratio, the 2DM and 2DCM both succeed in estimating the true trend of the self-aligning moment, where the other theories fail; conversely, for larger values of
, the trend is better predicted by the 1DCM and 2DCM. (a) Self-aligning moment versus the longitudinal slip
for different values of the lateral slip
and steering ratio
. (b) Self-aligning moment versus the longitudinal slip
for different values of the lateral slip
and steering ratio
.
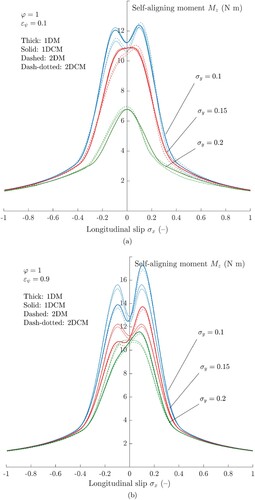
Figure 8. Friction ellipses for different discrete values of the lateral slip and steering ratio
. It can be noted that, for small values of the steering ratio, the 2DM and 2DCM both succeed in estimating the true trend of the self-aligning moment, where the other theories fail; conversely, for larger values of
, the trend is better predicted by the 1DCM and 2DCM. (a) Friction ellipse for different values of the lateral slip
and steering ratio
. (b) Friction ellipse for different values of the lateral slip
and steering ratio
.
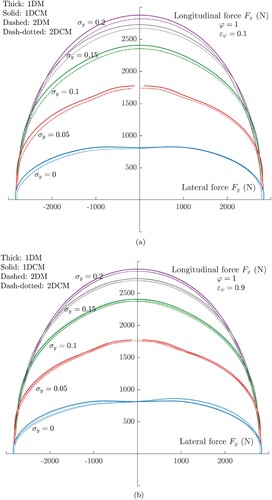
Figure 9. diagram for different discrete values of the lateral slip
and steering ratio
. It can be noted that, for small values of the steering ratio, the 2DM and 2DCM both succeed in estimating the true trend of the self-aligning moment, where the other theories fail; conversely, for larger values of
, the trend is better predicted by the 1DCM and 2DCM. (a)
diagram for different values of the lateral slip
and steering ratio
. (b)
diagram for different values of the lateral slip
and steering ratio
.
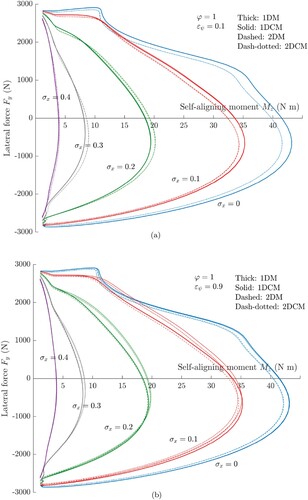
Figure 10. Tyre forces and friction ellipse for an heavily cambered tyre (). When the tyre experiences high level of cambering, the results predicted by the two-dimensional theories exhibit appreciable differences with the ones found by means of the 1DM and 1DCM. (a) Longitudinal and lateral tyre characteristics versus the longitudinal slip
for different values of the lateral slip
and steering ratio
and 0.9, respectively. The tyre rolling radius and the lateral coordinate of the wheel hub centre modelled as a function of the camber angle γ. (b) Friction ellipse for different values of the lateral slip
and steering ratio
. The tyre rolling radius and the lateral coordinate of the wheel hub centre modelled as a function of the camber angle γ.
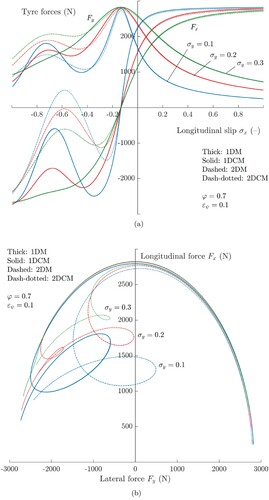
Table