Figures & data
Figure 1. Contour plot for the distribution of using EquationEq. (11)
(11)
(11) .
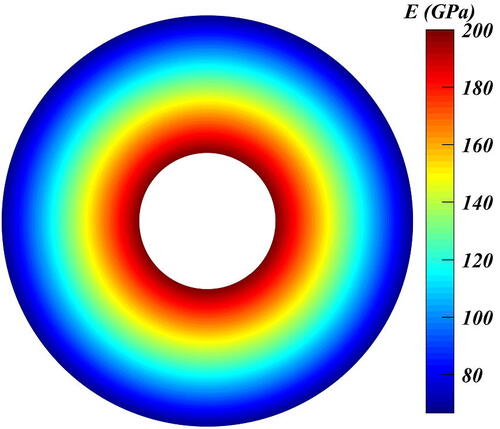
Figure 2. Dimensionless stresses distribution from the current study and Ref. [Citation37]. and
are plotted at
and
is plotted at
![Figure 2. Dimensionless stresses distribution from the current study and Ref. [Citation37]. σ¯r and σ¯θ are plotted at θ=0°, and τ¯rθ is plotted at θ=+45°.](/cms/asset/3faf6099-d441-469c-b190-de2a1bb2ca06/uths_a_2151960_f0002_b.jpg)
Figure 3. Contour plots for using EquationEq. (14)
(14)
(14) .

Figure 4. Dimensionless stress contours based on FEM solution for 1D-FGC. (a) Dimensionless radial stress, (b) dimensionless tangential stress, and (c) dimensionless shear stress.
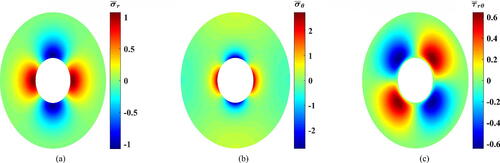
Figure 5. Dimensionless stress contours for (a) Dimensionless radial stress, (b) dimensionless tangential stress, and (c) dimensionless shear stress.
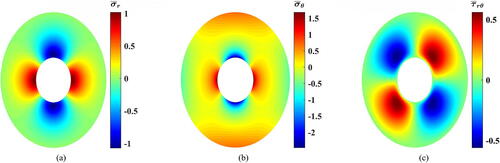
Figure 6. Dimensionless stress contours for (a) Dimensionless radial stress, (b) dimensionless tangential stress, and (c) dimensionless shear stress.
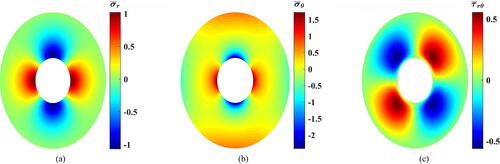
Figure 7. Dimensionless stress contours for (a) Dimensionless radial stress, (b) dimensionless tangential stress, and (c) dimensionless shear stress.
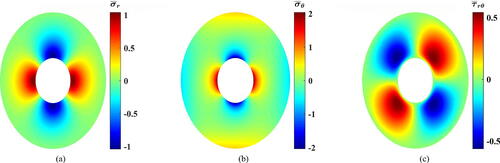
Figure 8. Dimensionless stress contours for (a) Dimensionless radial stress, (b) dimensionless tangential stress, and (c) dimensionless shear stress.
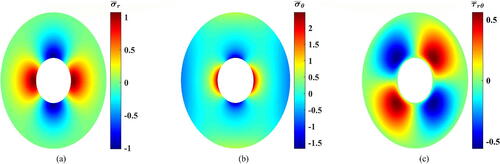
Figure 10. Resulting contours of the thermoelastic problem of 1D-FGC (). (a) Temperature, (b) dimensionless radial stress, (c) dimensionless tangential stress, (d) dimensionless axial stress, (e) dimensionless shear stress, and (f) dimensionless von Mises stress.
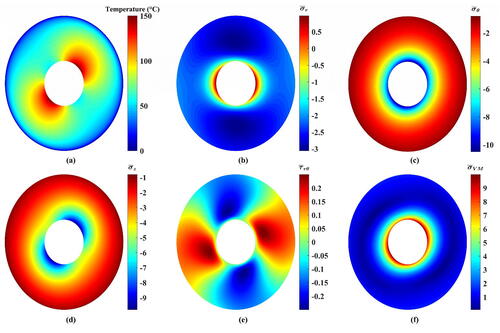
Figure 11. Resulting contours of the thermoelastic problem of 2D-FGC with (a) Temperature, (b) dimensionless radial stress, (c) dimensionless tangential stress, (d) dimensionless axial stress, (e) dimensionless shear stress, and (f) dimensionless von Mises stress.
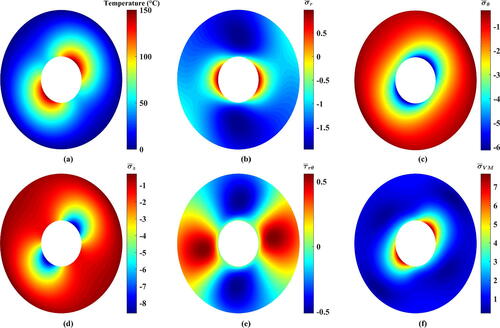
Figure 12. Resulting contours of the thermoelastic problem of 2D-FGC with (a) Temperature, (b) dimensionless radial stress, (c) dimensionless tangential stress, (d) dimensionless axial stress, (e) dimensionless shear stress, and (f) dimensionless von Mises stress.
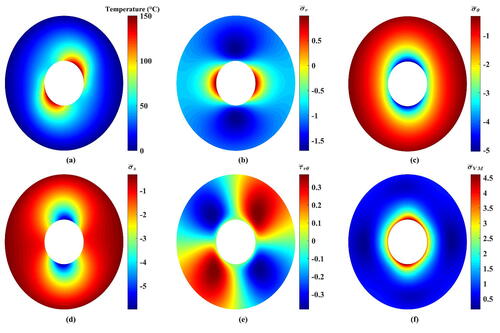
Figure 13. Resulting contours of the thermoelastic problem of 2D-FGC with (a) Temperature, (b) dimensionless radial stress, (c) dimensionless tangential stress, (d) dimensionless axial stress, (e) dimensionless shear stress, and (f) dimensionless von Mises stress.
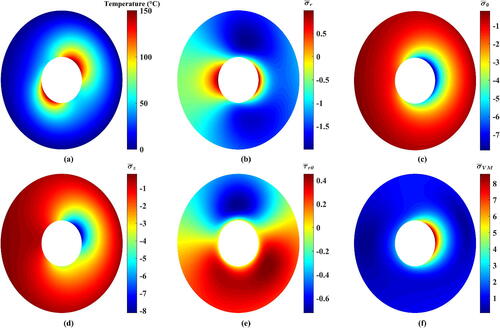
Figure 14. Resulting contours of the thermoelastic problem of 2D-FGC with (a) Temperature, (b) dimensionless radial stress, (c) dimensionless tangential stress, (d) dimensionless axial stress, (e) dimensionless shear stress, and (f) dimensionless von Mises stress.
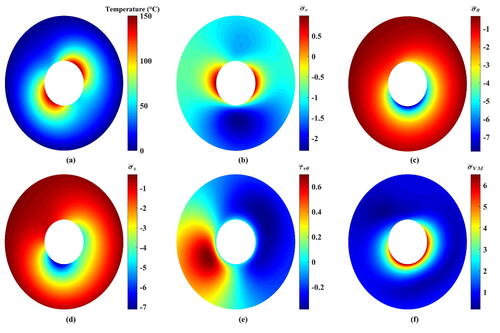
Figure 15. Variation’s percentage for each stress component for the thermoelastic problem of 2D-FGC with (a)
and (b)
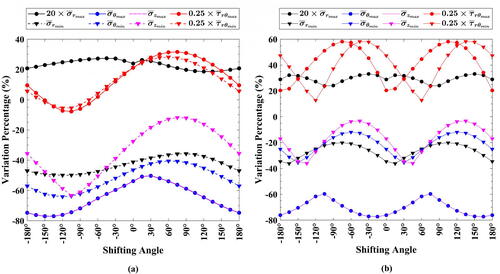
Table 1. The pertinent numerical values of some parameters used while investigating different values of of 2D-FGC under thermomechanical loading conditions.
Data availability
The raw/processed data required to reproduce these findings cannot be shared at this time as the data also forms part of an ongoing study.