Figures & data
Figure 2. Schematic representation of a CFMA. The left picture shows a longitudinal cross-section and the right picture shows the shield electrode and the active electrodes.

Figure 3. Longitudinal cross-section (yz plane) of the modelled geometry. The computational domain is surrounded by 10 nearly perfectly matched layers (PML) and a perfect electric conductor (PEC) in all directions.
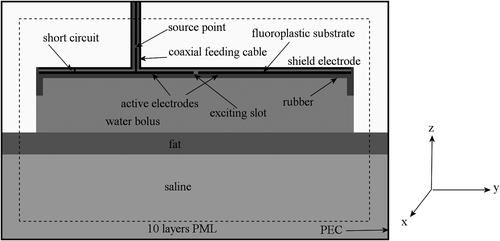
Table I. The dielectric properties used in the simulations.
Figure 4. Transversal and (partial) sagittal cross-section showing the position of the air layer between the metal plate and the rubber frame for the 1H applicator.
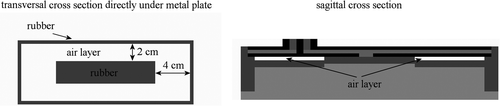
Figure 5. Transversal and (partial) sagittal cross-section showing the position of the air layer between the metal plate and the rubber frame for the 3H and 5H applicators. The pale grey region in the transversal cross-section is rubber in the simulation with an asymmetric air layer (5H, 2 cm bolus) and air in all other cases.
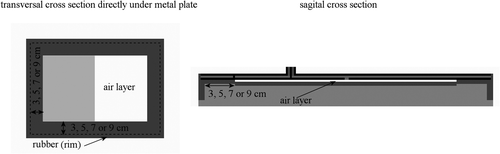
Table II. Overview of the simulated air layer configurations for the different types of CFMA applicators. The indication ‘air layer near edge’ refers to a situation as shown in , and the indication 'central air layer’ refers to the situation depicted in .
Figure 6. Contour plots of the measured (left) and simulated (right) SAR distribution generated by the 1H applicator with a bolus thickness of 1.5 cm. In the simulation, the 2 and 4 cm air layer at the edges of the long and short sides of the applicator was modelled, respectively.
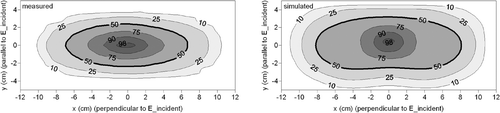
Figure 7. Transversal cross-sections of the modelled geometry directly under the metal plate, showing the air distributions in the simulations. The question marks at the centre represent the measurements, of which the air distribution is unknown.
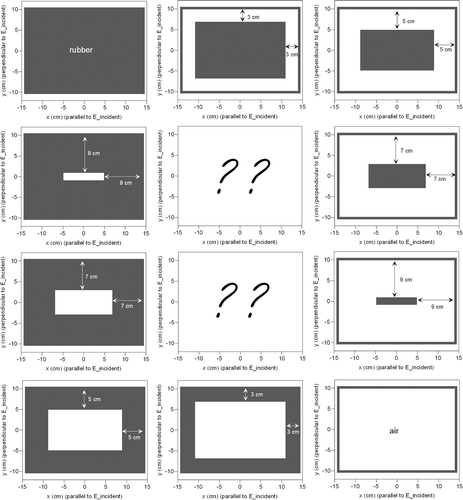
Figure 8. Simulated and measured iso-SAR contours for the 3H applicator with a bolus thickness of 1.7 cm.
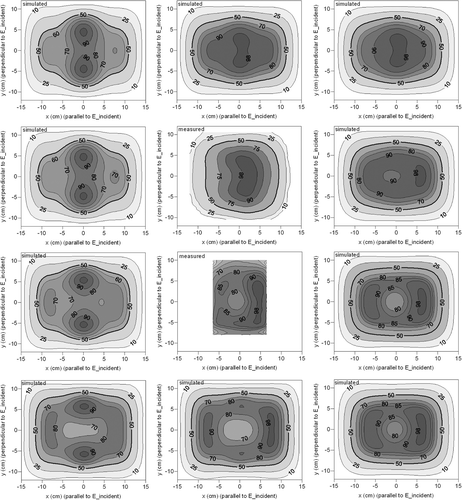
Figure 9. Simulated SAR profiles perpendicular (left) and parallel (right) to the incident E-field at the centre of the aperture of the 3H antenna. Simulations were performed with different extents of contact between the rubber and the metal plate.
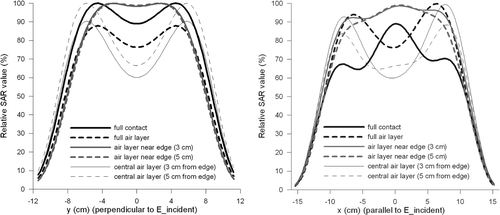
Table III. Simulated EHD values and the EFS sizes and area for the 3H applicator with a 1.7 cm water bolus and varying conditions of dielectric contact.
Figure 10. Simulated SAR contours for the 3H applicator with full contact (left), a central air layer of 1 mm (centre) and a central air layer of 2 mm (right).
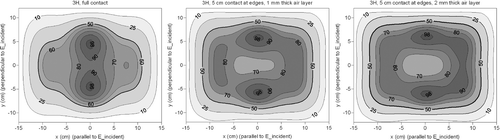
Figure 11. Simulated and measured iso-SAR contours for the 5H applicator with a bolus thickness of 1 cm.
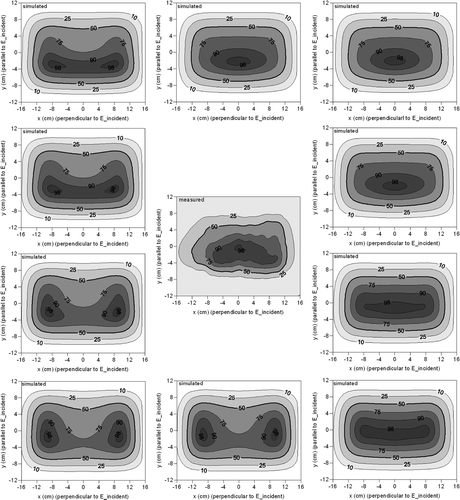
Table IV. Measured and simulated effective field sizes and effective heating depths of the three types of CFMA applicators in the rectangular phantom.
Figure 12. Simulated SAR profiles perpendicular (left) and parallel (right) to the incident E-field at the centre of the aperture of the 5H antenna. Simulations were performed with different extents of contact between the rubber and the metal plate.
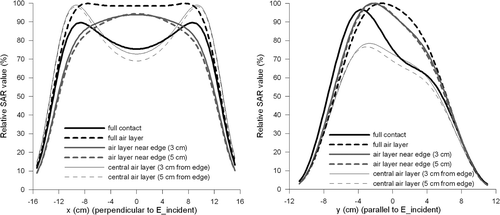
Figure 13. Contour plots of the measured (left) and simulated (right) SAR distribution generated by the 5H applicator with a bolus thickness of 2 cm. In the simulation, 3 cm contact was modelled at the edges.
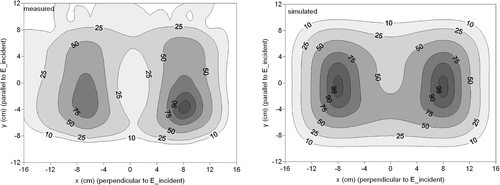
Figure 14. Left: Simulated SAR profile at y = 0 reproduced from and two measured SAR profiles resulting from the 5H applicator with a 2 cm water bolus. Measurement 1 was reproduced from . Measurement 2 shows a better quantitative correspondence with the simulation than measurement 1. For all three profiles, the maximum SAR value was normalised to 100%. Right: Profile of Measurement 2 and a simulated profile with an asymmetric air layer (see ).
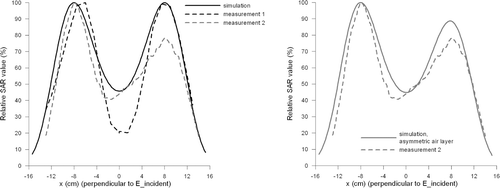
Table V. Simulated EHD values and the EFS sizes and area for the 5H applicator with a 1 cm water bolus and varying conditions of dielectric contact.