Figures & data
Table 1. Nominal chemical composition of Co 158 and AISI 1045 steel (wt.%).
Table 2. Experimental parameters.
Figure 7. Electromagnetic, temperature, and gas flow fields at t = 210 s: J is the current density, Φ is the magnetic flux, T is the temperature, and v is the velocity of the sheilding gas.
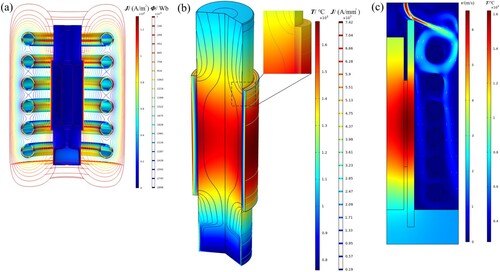