Figures & data
Figure 1 Schematic of the casting process and sampling location in the Research Foundry at Technikon, LLC (McClellan, CA).
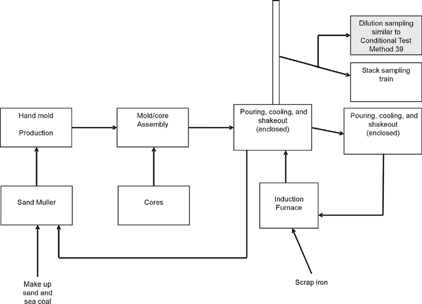
Figure 2 Schematic of the Desert Research Institute (DRI, Reno, NV) Source Dilution Sampling System.
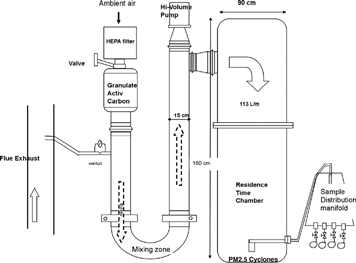
TABLE 1 Daily test conditions for comparisons of the dilution sampling method and U.S. Environmental Protection Agency (EPA) Modified Method 201A (Conditional Test Method 040)/202 sampling train from the Research Foundry at Technikon, LLC (McClellan, CA) from February 25–27, 2004
TABLE 2 PM2.5 mass concentrations determined by filter sampler and electronic low-pressure impactor (ELPI) with DRI source dilution sampling system (similar to U.S. Environmental Protection Agency [EPA] Conditional Test Method 039)
TABLE 3 Emission factors of PM2.5 chemical species from the foundry process (4-on irregular gear No-Bake® molds). No weighing factors for metal oxides and organic carbon are applied
Figure 3 Process variations of stack temperature (°C), carbon monoxide (CO) concentration (ppm), and total hydrocarbon concentration (THC) (ppm), measured in: (a) Run 3, (b) Run 4, (c) Run 5, and (d) Run 6. (Note that peak stack temperature [°C] in Runs 5 and 6 during shakeout period exceeds 300°C; in Runs 3 and 4 it is ∼ 200°C.)
![Figure 3 Process variations of stack temperature (°C), carbon monoxide (CO) concentration (ppm), and total hydrocarbon concentration (THC) (ppm), measured in: (a) Run 3, (b) Run 4, (c) Run 5, and (d) Run 6. (Note that peak stack temperature [°C] in Runs 5 and 6 during shakeout period exceeds 300°C; in Runs 3 and 4 it is ∼ 200°C.)](/cms/asset/b998935f-425c-4ed2-af7c-d902b74a3ead/uast_a_133460_o_f0003.jpg)
Figure 4 Process variations of PM2.5 concentration (4 μg/m3) and number concentrations (particles/cc) measured by ELPI for: (a) Run 3, (b) Run 4, (c) Run 5, and (d) Run 6. (Note that PM2.5 mass concentrations in Runs 5 and 6 are approximately twice those of Runs 3 and 4, whereas PM2.5 number concentrations are similar.)
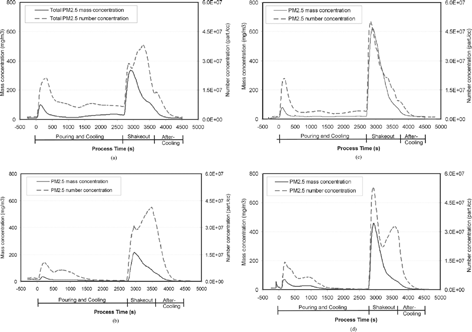