Figures & data
Table 1 Estimated design characteristics of important centrifuge generations.
Table 2 Design and performance characteristics of hypothetical centrifuges. Equation (Equation6) determines the theoretical maximum performance δUDirac. The overall efficiency and the resulting effective separative performance δURaetz can be determined with Eq. (Equation10) once the radii ratio is selected. The optimum feed rate F✶ and the corresponding separation factor α β depend on the selected countercurrent-to-feed ratio k.
Figure 3 Separative performance of a P1-type machine as a function of the feed rate for fixed internal circulation (top). Values for the countercurrent rates L have been chosen such that δ U is maximized for 10 mg/s (P1-100) and for 4 mg/s (P1-040). These design points are used for an analysis of cascade-performance below. The respective separation factors are also shown (bottom). Results based on the analytical model by Rätz using Eq. (Equation10).
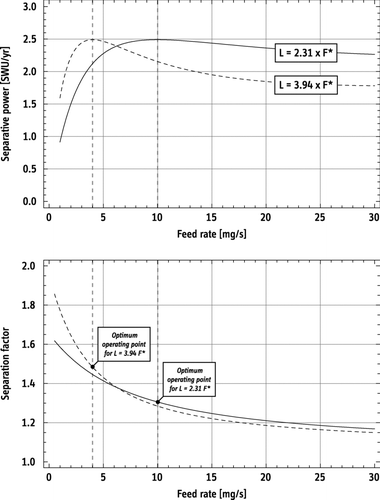
Figure 4 Enrichment level of product stream leaving a P1-type centrifuge (P1-100). At t = 0, the feed rate is gradually reduced from its reference value of 10 mg/s to 5 mg/s over a 30-min period. The separative performance drops slightly from its optimum value (2.5 SWU/yr) to about 2.3 SWU/yr, if the internal circulation is not adjusted. A new equilibrium is obtained within about one hour. In this simulation, the feed material is natural uranium, and the cut is 0.46.
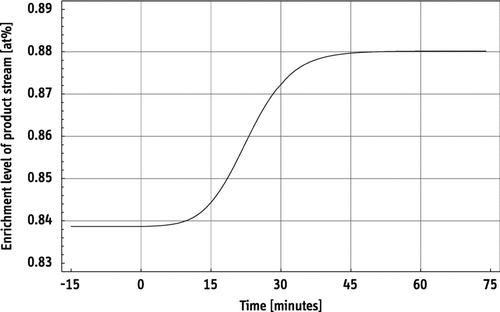
Table 3 Results of the simulations for the 164-machine cascade using P1-type centrifuges. The four different modes of operation are each characterized by a specific optimum machine feed rate F✶, which translates into corresponding external feed rates and product rates and ultimately determines the enrichment level of the product leaving the cascade. The separative performance for the cascade (SP-C) and for an average machine (SP-AM) are shown. Values for batch recycling assume 3.5% enriched feedstock, initially produced with P1-135, and are taken after 120 hours of operation.
Figure 6 Transient response of a 164-machine cascade using P1-type technology: Enrichment level of product in batch recycling mode, initiated at t = 0. Depending on the selected default feed rate, a new equilibrium is reached within 24–48 h.
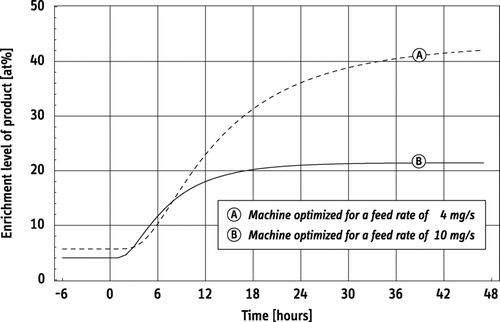
Figure 7 Enrichment level of the product recovered from a 164-machine cascade of the second batch recyling step. The machines in this cascade are operated at a reduced flow rate (P1-044); feedstock is 16.3% preenriched material from a first batch recycling step, in which machines are operated at the standard flow rate (P1-135). In this simulation, the target enrichment level of 90% is reached after about 3.5 days.
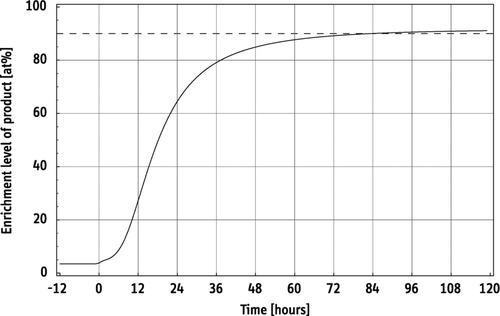
Figure 8 Illustration of the cascade arrangement as proposed for the Libyan enrichment project. Note the asymmetric upstream and downstream connections. Mass values are normalized to one kilogram of product (weapon-grade uranium at 90% enrichment), which is produced in about 4.1 days with this setup, if based on P1-type technology.
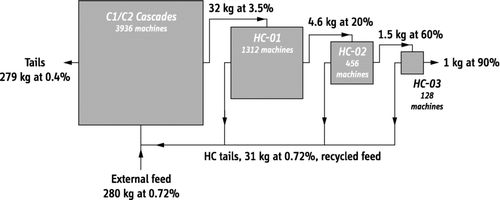