Figures & data
Figure 1. The proposed approach for detecting current tool conditions and predicting future conditions.
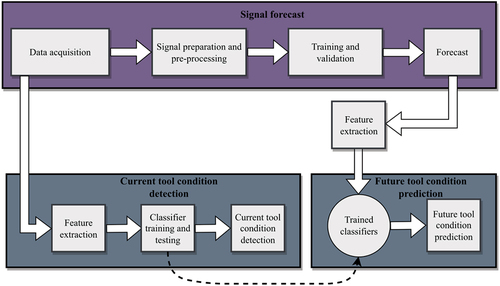
Table 1. The geometric features of the cutting tool, workpiece dimensions and cutting parameters.
Figure 4. Example bending moment signal from machining in (a) x-direction, (b) y-direction and (c) the resultant bending moment indicating the cutting tool engagement with the workpiece.
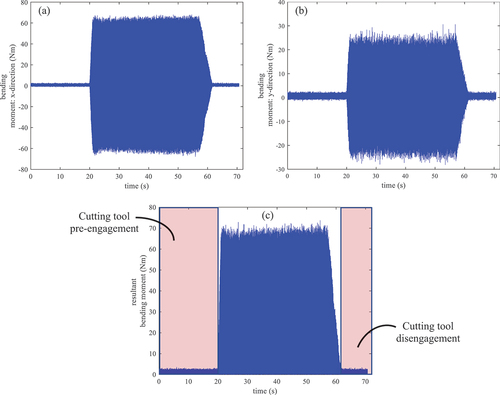
Figure 7. Illustration of the tool condition classification with the original and transformed signals.
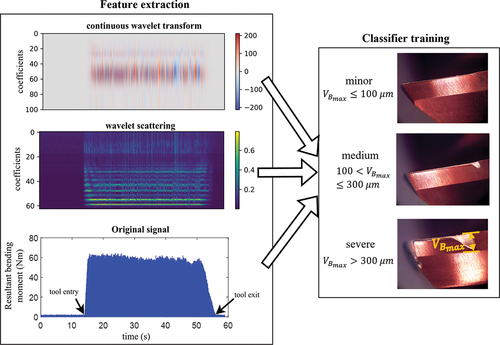
Table 2. List of statistical features extracted from signals.
Figure 8. Tool wear plots during machining of tungsten at (a) 40 m/min and (b) 60 m/min cutting speed.
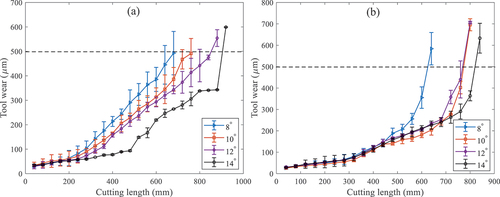
Figure 10. Performance evaluations of the 1D CNN and ANN on the validation and test sets: (a) learning curve of the 1D CNN; (b) test set prediction of the 1D CNN; (c) learning curve of the ANN; (d) test set prediction of the ANN.
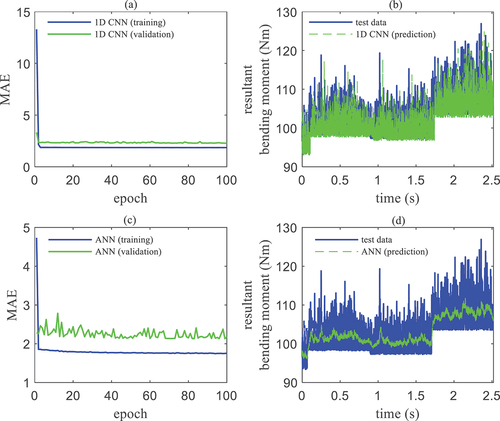
Figure 11. Forecasted signals using 1D CNN and ANN compared with measured signal for (a) pass 2; (b) pass 5; (c) pass 8; (d) pass 11.
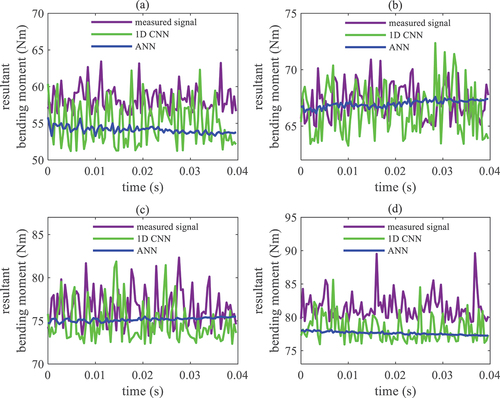
Figure 12. Forecasted signals using 1D CNN and ANN compared with measured signal for (a) pass 14; (b) pass 17; (c) pass 19; (d) pass 20.
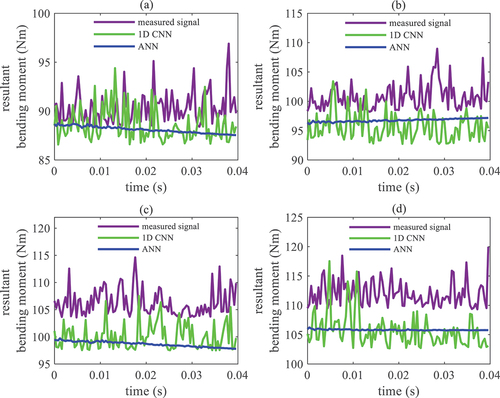
Figure 13. Mean bending moment for each machining pass for (a) ground truth and prediction per algorithm; (b) prediction error per algorithm.
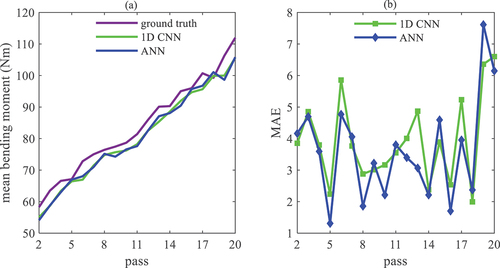
Figure 14. Confusion matrices for the classification of tool conditions by the RF for (a) 0.04 s window; (b) 0.08 s window; (c) 0.12 s window; and (d) 0.16 s window.
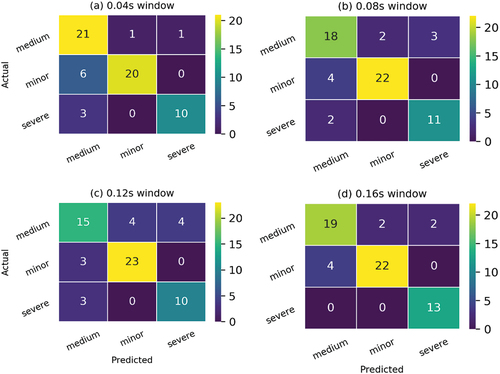
Figure 15. Confusion matrices for the classification of tool conditions by the SVM for (a) 0.04 s window; (b) 0.08 s window; (c) 0.12 s window; and (d) 0.16 s window.
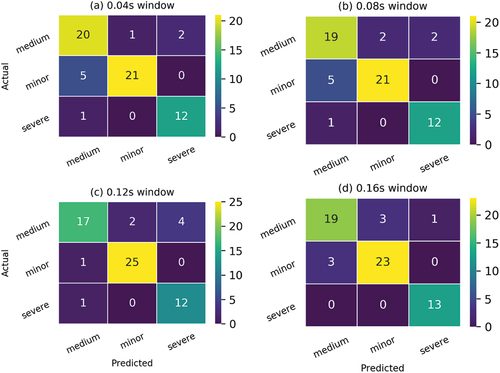
Figure 16. Confusion matrices for the classification of tool conditions by the XGBoost for (a) 0.04 s window; (b) 0.08 s window; (c) 0.12 s window; and (d) 0.16 s window.
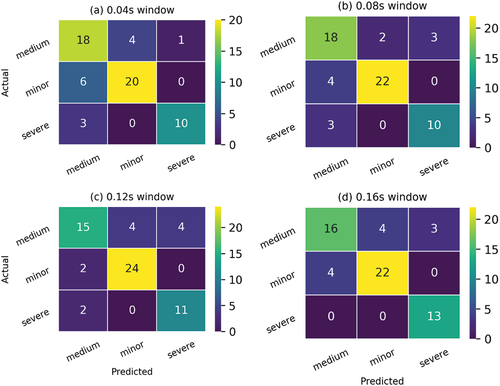
Figure 17. Confusion matrices with/without rake angle and cutting speed as encoded features for RF, SVM and XGBoost when trained on statistical features.
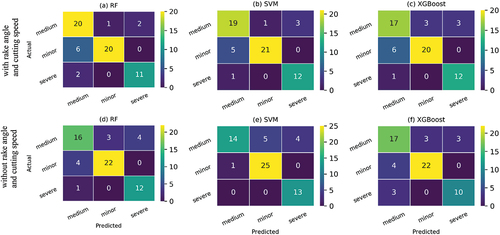
Figure 18. Confusion matrices on validation set for (a) RF, (b) SVM, and (c) XGBoost when trained on statistical features.
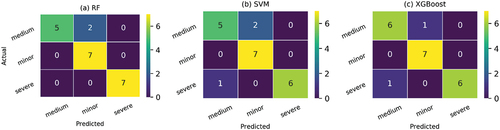
Figure 19. Confusion matrices of each algorithm on test set for each algorithm when trained on (a)-(c) CWT features and (d)-(f) WS features.
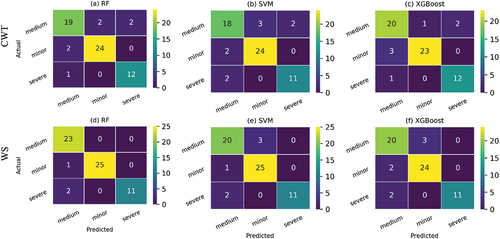