Figures & data
Figure 1. Schematic representation of the main contributors to a rolling bearing’s impedance: (a) Equivalent circuit of a rolling bearing consisting of contact capacitances. (b) Equivalent circuit of a contact capacitance consisting of the Hertzian and the outside area.
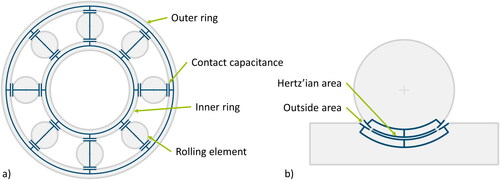
Figure 2. Schematic of the spindle with the three bearing points B1, B2, and B34 and the current/voltage flow for the impedance measurement.
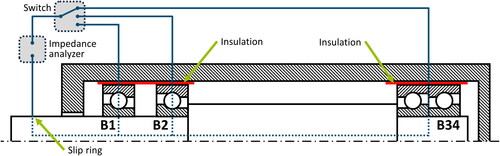
Figure 4. Time signal of the absolute impedance of bearing B2 during a free-running test at 10,000 rpm for one shaft rotation (6 ms).
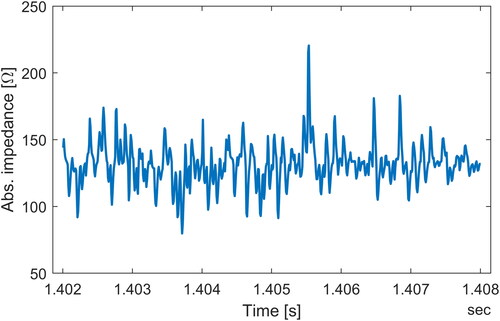
Figure 5. Comparison of different results of the impedance measurement at bearing B1 during a free-running ramp-up from 0 to 30,000 rpm.
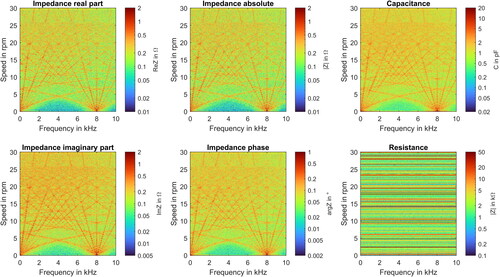
Figure 6. Waterfall diagram of bearing B1’s absolute impedance during a free-running ramp-up from 0 to 30,000 rpm.
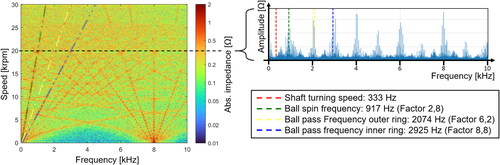
Figure 7. Highlighting of the modulation of the two line clusters in the waterfall diagram of impedance measurement at bearing B1 during ramp-up.
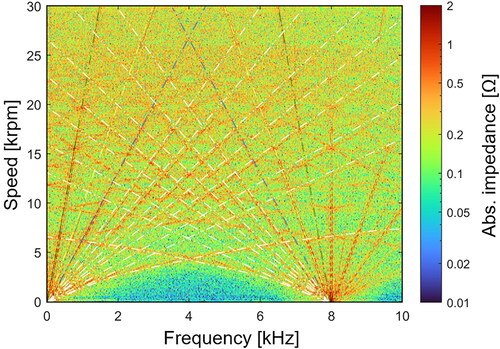
Figure 8. Comparison of the waterfall diagrams of the absolute impedance (a) and vibration measurement in x-axis (b), y-axis (c) and z-axis (d) for bearing B1 during ramp-up.
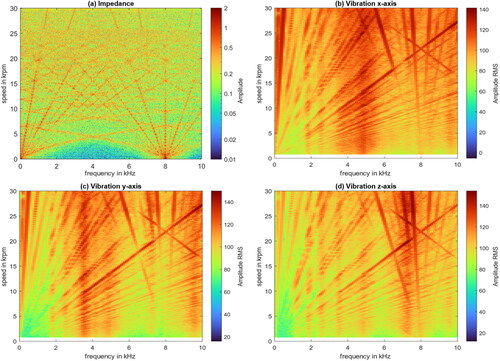
Figure 9. Change in the impedance of bearing B2 under axial load in the time domain (left) and frequency domain (right). The load was applied at second 10.
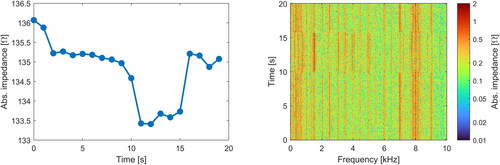