Figures & data
Table 1. Geometrical dimensions of the simulation tubes.
Table 2. Properties of working fluids.
Table 3. Mesh independence test.
Figure 3. Validation of RSM with experimental data of inward helically corrugated tubes and empirical correlations of smooth tube.
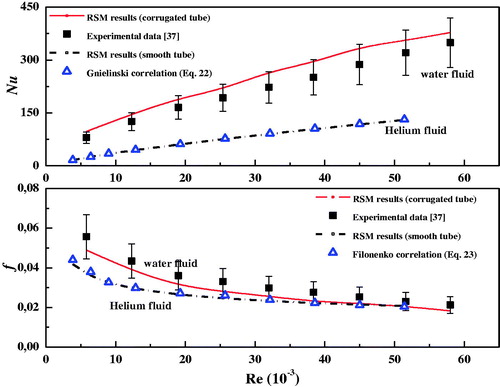
Figure 8. Distribution of the local heat transfer entropy generation rate for the five cases (Re = 20,030).
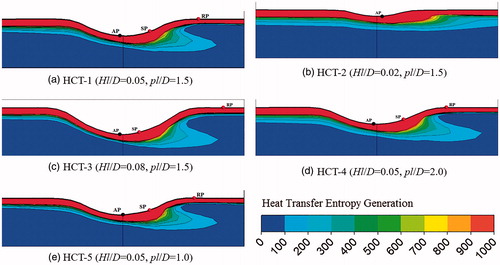
Figure 9. Distribution of the local friction entropy generation rate for the five cases (Re = 20,030).
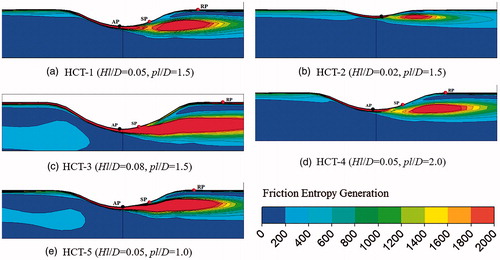
Figure 10. Distribution of the local total entropy generation rate for the five cases (Re = 20,030).
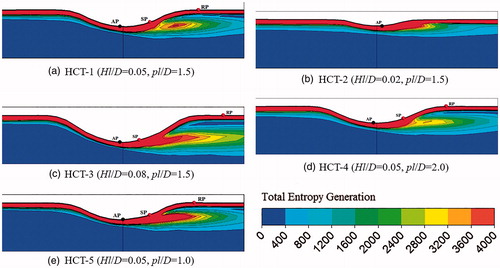