Figures & data
Figure 1. Geometries of a six-start spirally corrugated tube. (a) Geometric model of tube and (b) Geometric parameters of tube.
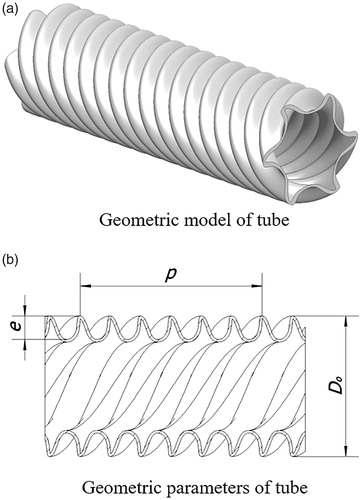
Table 1. Geometric parameters of six-start spirally corrugated tubes with different pitches.
Table 2. Shell side Nusselt number of six-start spirally corrugated tubes with different pitches.
Figure 7. Shell side temperature distribution of six-start spirally corrugated tubes with different pitches.
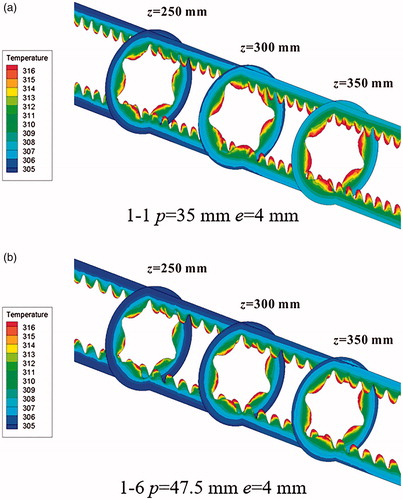
Figure 8. The shell side flow resistance coefficients of six-start spirally corrugated tubes with different pitches.
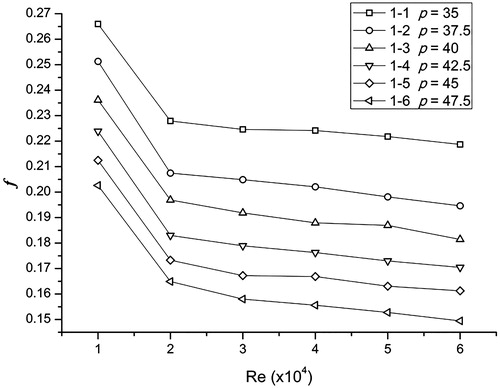
Figure 9. Ratio of the shell side flow resistance coefficient (fc/fs) between six-start spirally corrugated tubes and smooth tubes.
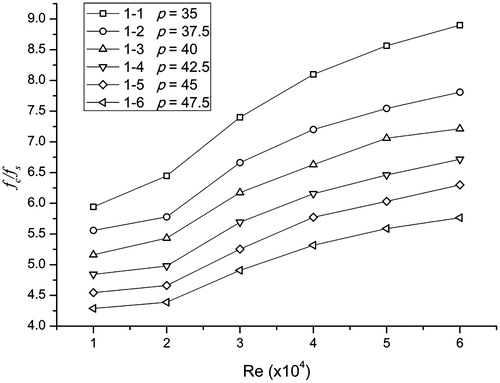
Table 3. Geometric parameters of six-start spirally corrugated tubes with different corrugation depths.
Table 4. Shell side Nusselt number of six-start spirally corrugated tubes with different corrugation depths.
Figure 11. The shell side flow resistance coefficient of the six-start spirally corrugated tubes with different corrugation depths.
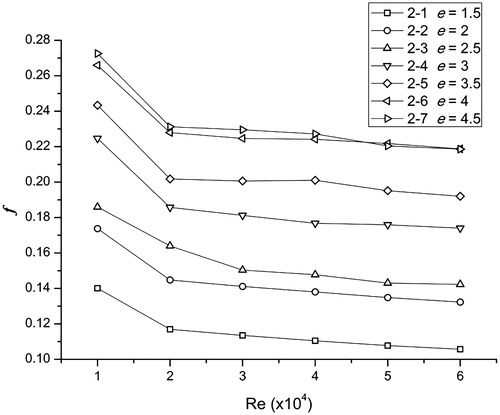
Figure 12. Ratio of the shell side flow resistance coefficient (fc/fs) between six-start spirally corrugated tubes and the smooth tubes (a) Model of Nusselt number (b) Model of flow resistance coefficient.
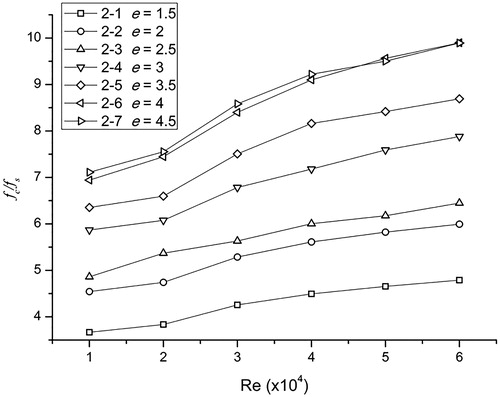