Figures & data
Figure 3. Detailed schematics of the computational model. (a) Wedge duct configuration; (b) Dimpled endwall configuration; (c) Pin fin and dimple configuration; (d) Dimple configuration.
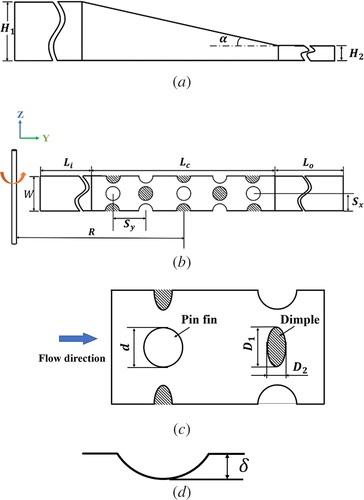
Table 1. Studied cases.
Table 2. Grid independence check.
Figure 7. Comparison of the area-averaged Nusselt number on the dimpled endwall for ranging from -0.4 to 0.4.
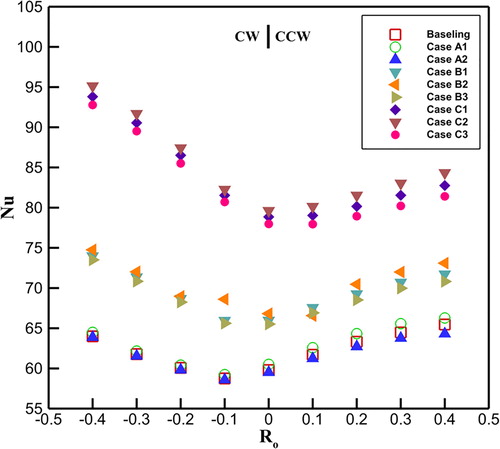
Figure 8. Comparison of the Nusselt number distributions at the dimpled endwall surface for the Baseline, Case B1 and Case C1 at = 0.3.
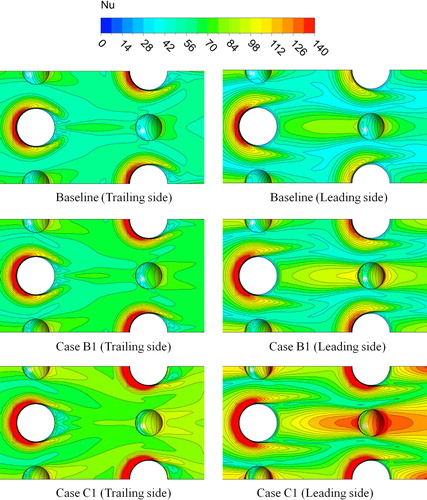
Figure 9. Comparison of the vorticity isosurface and streamline distributions in the vicinity of the pin fin for the Baseline, Case B1 and Case B1 at = 0.3.
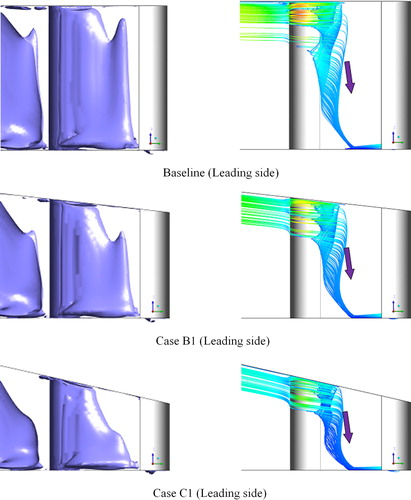
Figure 11. Comparison of the limiting streamline distributions at the dimpled endwall surface for the Baseline, Case B1 and Case C1 at = 0.3.
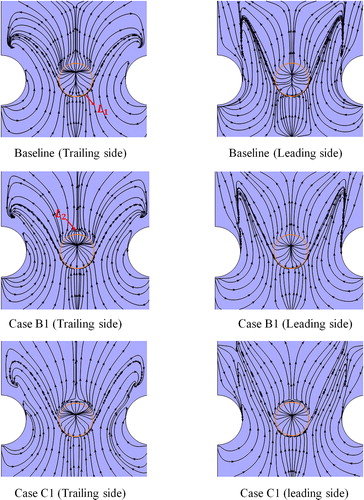
Figure 12. Comparison of the Nusselt number distributions along the centerline on the dimpled endwall surface for Cases C1, C2, and C3 at = 0.3.
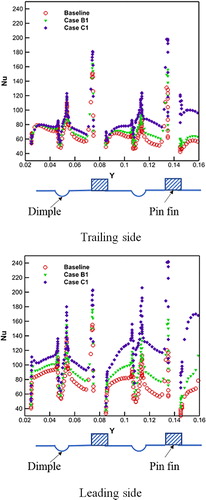
Figure 13. Comparison of the Nusselt number distributions on the dimpled endwall surface for Cases C1, C2, and C3 at = 0.2.
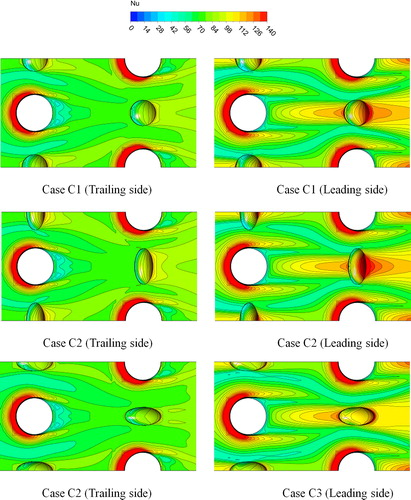
Figure 15. Comparison of the TKE distributions at the central streamwise plane for Cases C1, C2, and C3 at = 0.2.
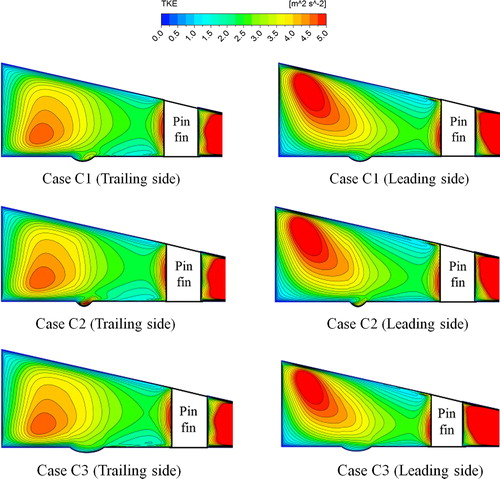