Figures & data
Figure 2. Different wire structure heat exchangers with high aspect ratio tested for thermal–hydraulic performance: (a) continuous wire structure; (b) pin fin structure; and (c) woven wire structure (adopted from [Citation18,Citation21,Citation22]).
![Figure 2. Different wire structure heat exchangers with high aspect ratio tested for thermal–hydraulic performance: (a) continuous wire structure; (b) pin fin structure; and (c) woven wire structure (adopted from [Citation18,Citation21,Citation22]).](/cms/asset/a95c6636-2817-4614-83f0-4a88e8ee50d5/unht_a_1562741_f0002_c.jpg)
Figure 4. Boundary conditions of the in-line (a) and staggered (b) cross-section model [Citation18].
![Figure 4. Boundary conditions of the in-line (a) and staggered (b) cross-section model [Citation18].](/cms/asset/27dfb765-e7b6-4146-8d2c-ca2b46f0cba1/unht_a_1562741_f0004_c.jpg)
Table 1. Definition of nondimensional input parameters to simulation model with minimal and maximal values in parametric study.
Table 2. Grid Convergence Index (GCI) based on Richardson method [Citation27] for Nusselt number and friction factor.
Figure 6. Pressure difference, velocity, and temperature of a 2D in-line wire structure simulation with = 10,
= 3,
= 20, and
. Contour lines for pressure difference are equally distributed. Velocity streamlines are colored based on the temperature scale.
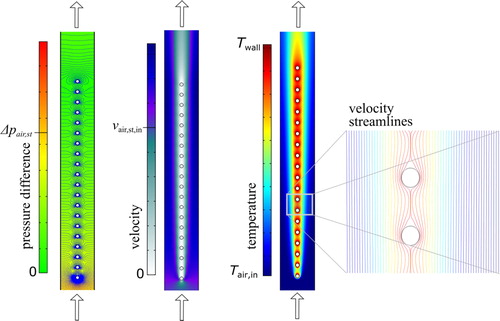
Figure 7. Nusselt number and Fanning friction factor of an in-line wire structure for a developed flow as a function of Reynolds number and geometry parameters and
.
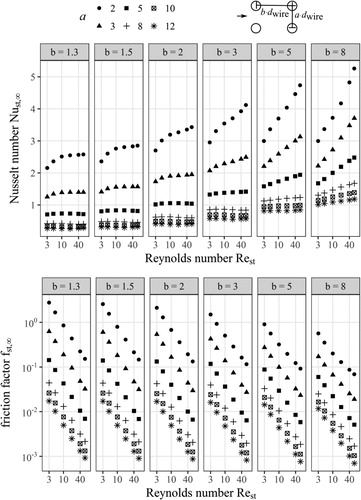
Figure 8. Correlated global (solid line) and local (dashed line) Nusselt number, and
, respectively, for an in-line wire arrangement, as a function of the number of wires based on the simulated global data points (squares) for
and fixed values for
. Downstream of the thermal entrance length (dotted line), the flow is declared as thermally developed.
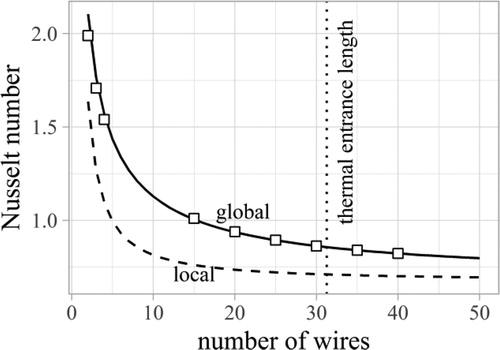
Figure 9. Correlated global (solid line) and local (dashed line) friction factor, and
, respectively, for an in-line wire arrangement as a function of the number of wires based on the simulated global data points (squares) for
and fixed values for
. Downstream of hydraulic entrance length (dotted line), the flow is declared as hydraulically developed; in-line arrangement.
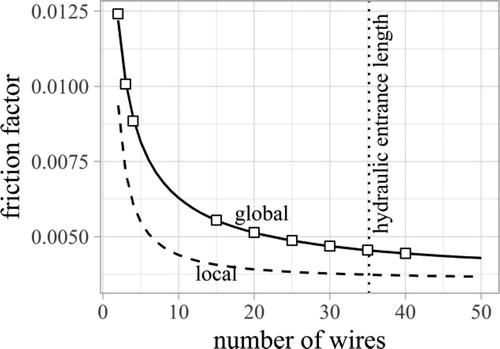
Figure 10. Predicted (correlated) values versus simulated values for (a) the Nusselt number and (b) the Fanning friction factor
. Data are based on EquationEqs. (13)
(13)
(13) and Equation(19)
(19)
(19) . The predicted values are correlated via the number of wires
(see ) for specific Reynolds numbers
and geometry parameters
and
for an in-line arrangement.
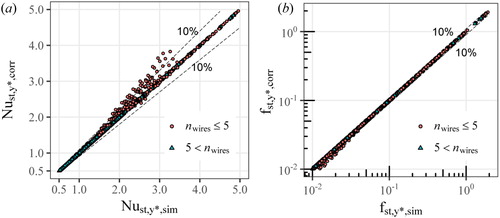
Table 3. Derived correlations for and
for an in-line wire structure.
Table 4. Derived correlations for coefficients of and
for in-line wire structure based on the EquationEqs. (13)
(13)
(13) and Equation(19)
(19)
(19) .
Figure 11. Auxiliary coefficients(a),
(b),
(c), and
(d) needed for calculation of correlated Nusselt number and friction factor based on for in-line arrangement. Geometry parameter
is shown on the contour lines.
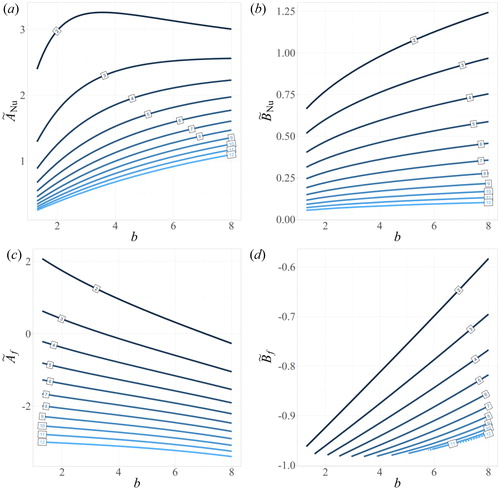
Figure 12. Nondimensional entrance lengths and
for an in-line arrangement based on the Reynolds number
and geometry parameters
and
. Entrances lengths below 0.1 are not shown.
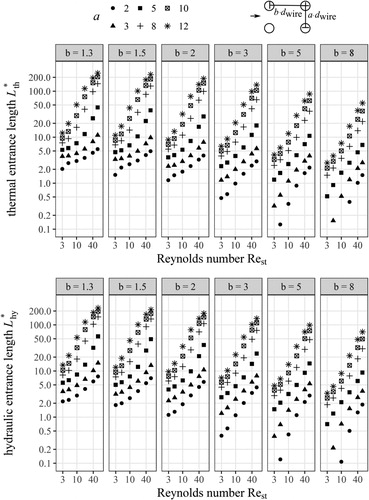
Figure 13. Predicted (correlated) values versus simulated values for (a) the Nusselt number and (b) the Fanning friction factor
for a developed flow. Data are based on . The predicted values are correlated via the Reynolds number
and geometry parameters
and
for an in-line wire arrangement.
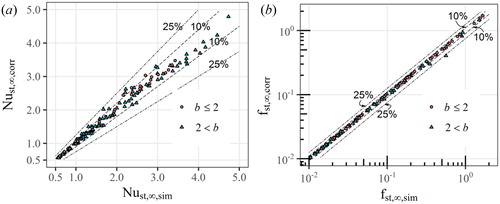
Figure 14. Predicted (correlated) values versus simulated values for (a) the Nusselt number and (b) the Fanning friction factor
. Data are based on EquationEqs. (13)
(13)
(13) and Equation(19)
(19)
(19) ( and ). The predicted values are correlated via the Reynolds number
, geometry parameters
and
, and the number of wires for an in-line wire arrangement.
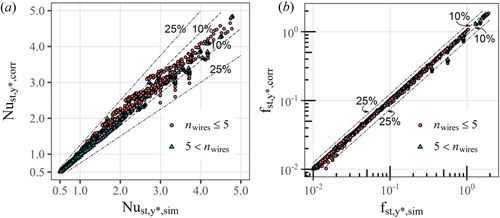
Table 5. Percentage of correlated data which satisfy a relative residual error below 5% and 10% for ,
,
, and
.
Table B1. Predicted correlation for coefficients of and
for staggered wire structure based on the EquationEqs. (13)
(13)
(13) and Equation(19)
(19)
(19) .
Table B2. Percentage of correlated data which satisfy a relative residual error below 5% and 10% for ,
,
, and
in staggered wire arrangement.