Figures & data
Figure 2. Coarse aggregate used in the experiment: (a) lean iron ore coarse aggregate and (b) limestone coarse aggregate.
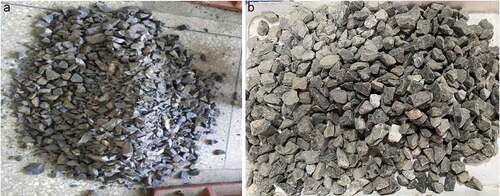
Table 1. Physical and mechanical properties of various coarse aggregates.
Table 2. Statistical distribution of harmful chemicals and iron content in lean iron ore.
Table 3. Preliminary mix proportions.
Table 4. Compressive strengths of mixes.
Table 5. Surface fracture ratio of coarse aggregate to hardened cement paste.
Table 6. Test results for each mix.
Table 7. Average results of impact test indexes.
Figure 12. Linear regression results for number of impacts N1 at initial cracking: (a) A1, (b) A2, (c) A3, and (d) A4.
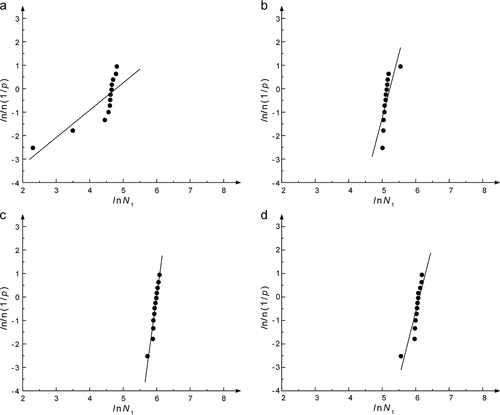
Figure 13. Linear regression results for number of impacts N2 at final cracking: (a) A1, (b) A2, (c) A3, and (d) A4.
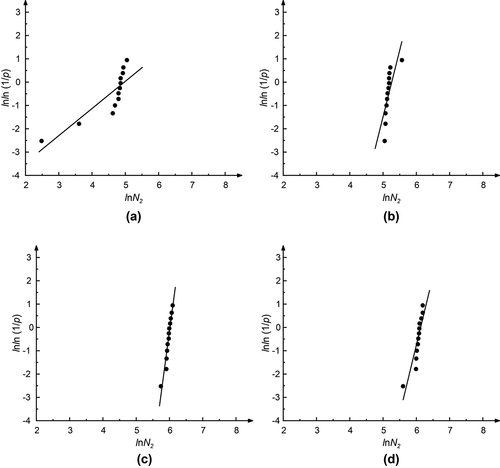
Table 8. Weibull fitting results.
Figure 16. Relationship between strength grade and number of impacts between initial and final cracking.
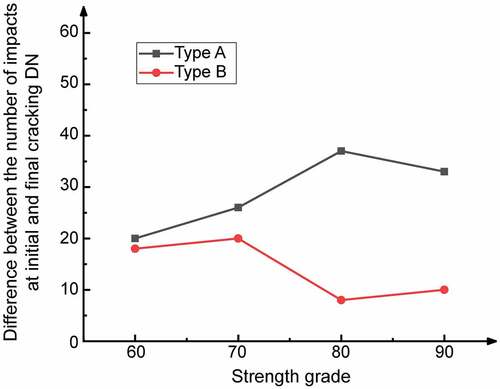
Table 9. Ductility index.
Figure 17. Relationship between impact resistance and strength grade according to different concrete mix types (conventional and lean iron ore mix).
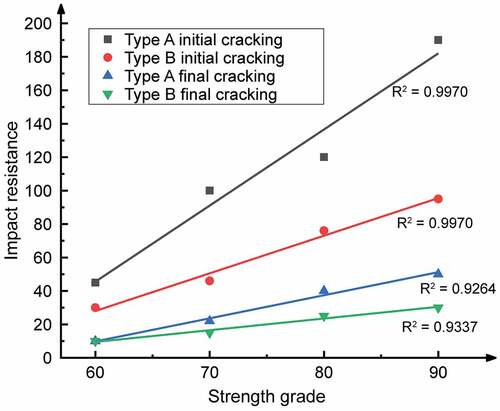
Table 10. Construction records.
Table 11. Lifespan extension of precast lean iron ore concrete piles under harsh geological conditions.