Figures & data
Table 1. Primary structural materials in aircraft models [Citation13,Citation18,Citation20].
Table 2. Primary structural materials in a mid-range civil transport [Citation1,Citation2,Citation13,Citation18,Citation20].
Figure 3. Two-frame experimental collapse test [Citation14].
![Figure 3. Two-frame experimental collapse test [Citation14].](/cms/asset/d852c407-c27a-4f47-b6cf-f23760b9d39a/tcrs_a_1273987_f0003_b.gif)
Figure 5. Acceleration from A320 drop test and comparable floor simulation from Hashemi et al. [Citation14].
![Figure 5. Acceleration from A320 drop test and comparable floor simulation from Hashemi et al. [Citation14].](/cms/asset/d25ffa90-2a11-452d-bb72-f4bfd8f3758e/tcrs_a_1273987_f0005_b.gif)
Figure 8. Six half-frame von Mises stress level comparison: (a) Metal, (b) quasi-isotropic composite, (c) ply-by-ply composite.
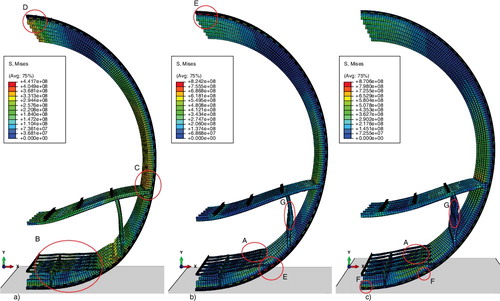
Figure 9. Six-frame (half-barrel) plasticity level comparison: (a) Metal, (b) quasi-isotropic composite, (c) ply-by-ply composite.
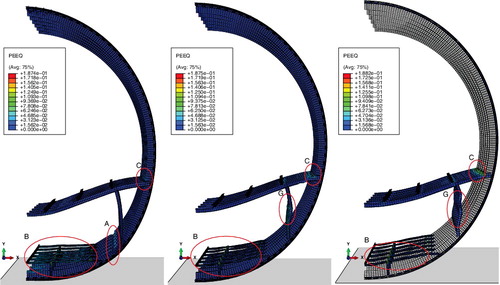
Table 3. Model masses.
Table 4. Average and measured accelerations.
Figure 13. Six-frame model Eiband plot showing the severity of impact. Redrawn from [Citation6,Citation22].
![Figure 13. Six-frame model Eiband plot showing the severity of impact. Redrawn from [Citation6,Citation22].](/cms/asset/bf6b26a7-4aa0-4b61-a275-58d900496f64/tcrs_a_1273987_f0013_oc.jpg)