Figures & data
Figure 1. Heating unit with stratified storage tank, control unit, loading pump, burner, counter current heat exchanger, and temperature sensors (NTC 1 and NTC 2).
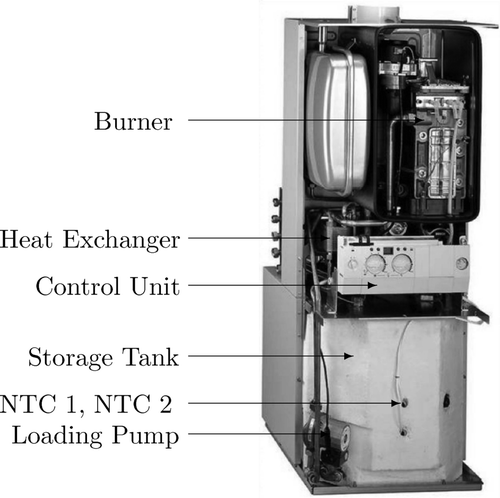
Figure 3. Graph of the finite state automaton describing the operational modes of the plant. For the sake of simplicity, transitions are labeled only unidirectionally, i.e. for each there exists a corresponding transition
.
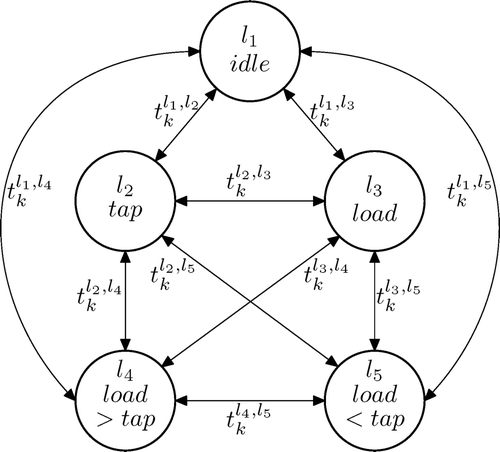
Figure 4. Sketch of the counter current heat exchanger with primary and secondary side temperature profiles Θpr(x,t) and Θsec(x,t) as well as the respective flow velocities v h(t) and v l(t).
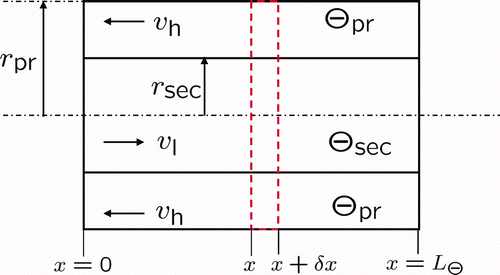
Figure 5. Setup of the burner composed of the fan with the fan speed n F and the heat exchanging unit (pipe system) with the primary and secondary side temperatures τpr(ζ, t) and τsec(ζ, t) as well as the respective flow velocities v g(t) and v h(t).

Figure 6. Sketch of the heat exchanging part of the burner with the primary side, wall, and secondary side temperatures τpr, τw, and τsec as well as the respective flow velocities v g(t) and v h(t).

Figure 7. Left: labeled scheme of the storage tank with respective in- and outflow velocities v l,d(t) and the resulting plug flow velocity v(t). Right: cross section of the storage wall with corresponding diameters d m , m = 1,2,3, heat conduction coefficients λ m , and heat transfer coefficients α n , n∈{i, a}.
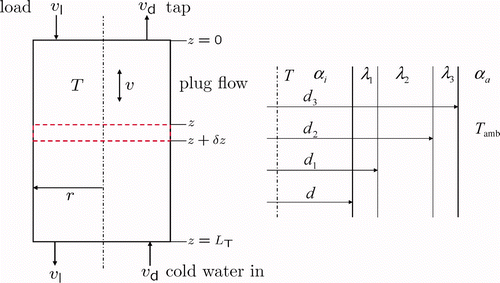
Figure 9. Structure for the classification of discretization schemes using exact system inversion of the distributed parameter system Σ.
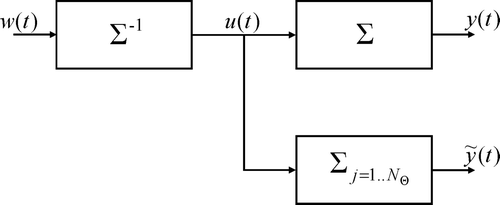
Figure 10. Left: transient and stationary distortion due to spatial discretization of the heat exchanger PDE using N Θ = 50 compartments. Right: magnified version showing the transition between the transient and stationary region.
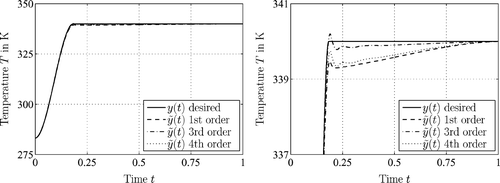
Figure 11. Simulation results of the plant model for loading and tapping scenarios. Top left: tapping and loading velocities v d and v l. Bottom left: variation of the fan speed n F. Right: 3D temperature profile T(z,t) of the storage tank.
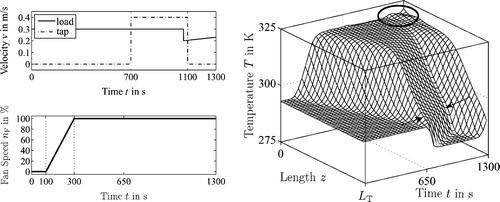
Figure 12. Left: plot of the measured and simulated outlet temperatures of the primary and secondary side of the counter current heat exchanger. Right: measured and simulated temperature profiles at the secondary outlet of the condensing boiler.
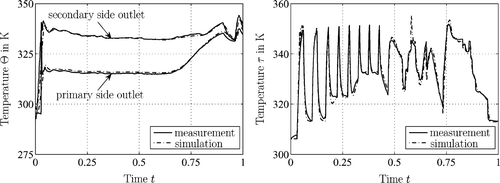