Figures & data
Figure 6. Comparisons between model predicted fuel mass flow with the experimental data during four start-up events.

Figure 7. Start-up cumulated fuel predicted by the model (with and without correction) compared with the experimental data.
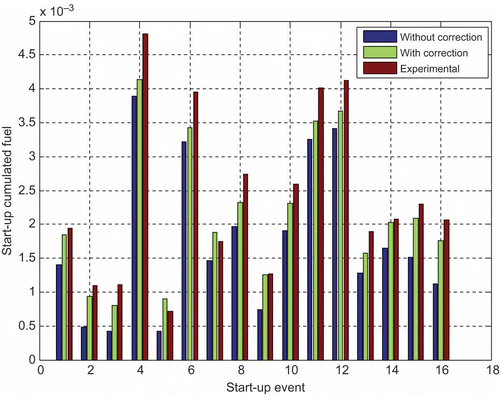