Figures & data
Figure 1. Scheme of the dryer: the transportation path of the fibre belt and the flow directions of the drying air are indicated as well as the insertion of water and the moisture measurement.
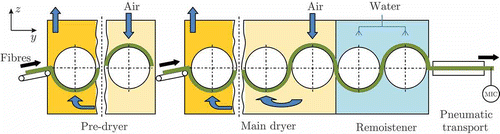
Figure 2. Scheme of a plane fibre web element with index i: X moisture content in the fibres, Y humidity of air, m
F
mass of dry fibres, mA
mass of dry air, mass flow of dry fibres,
mass flow of dry air,
actual mass flow of evaporating water, and h specific enthalpy. Subscript A stands for air, V for vapour, i for element index, and in for the respective input value.
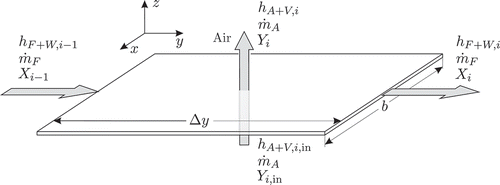
Figure 5. Validation of identified disturbance model. The disturbance is given by a variation in fibre sheet thickness.
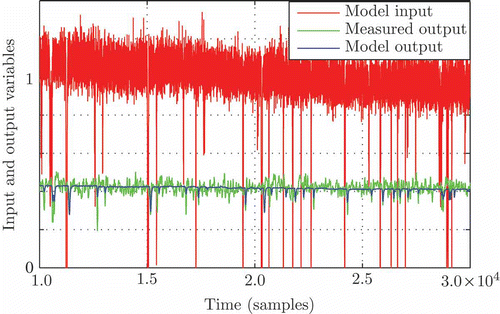
Figure 7. Validation with different fibre types at different operation points; the numbers at the axis ‘process location’ are the numbers of the drums, ‘eod’ means ‘end of dryer’ (after the moistener), ‘pt’ means ‘pneumatic transportation’ and ‘om’ stands for ‘online measurement’.
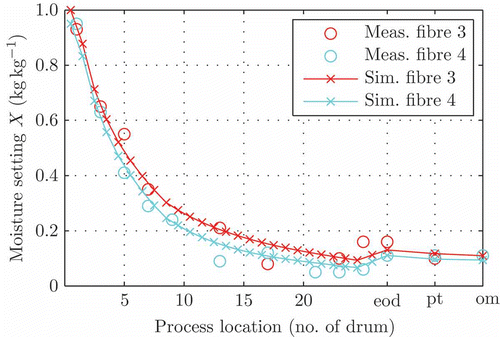
Figure 8. Simulation of transient behaviour; X 0 is the incoming moisture setting of the fibres, X 1 until X 8 is the moisture setting at each drum. At t = 1500 s X 0 takes a step to X 0 = 0.9, at t = 2500 s the fibrous web becomes thinner and at t = 3500 s temperature of drying air decreases by 5°C at every drum. Moisture settings Xi are normalized.
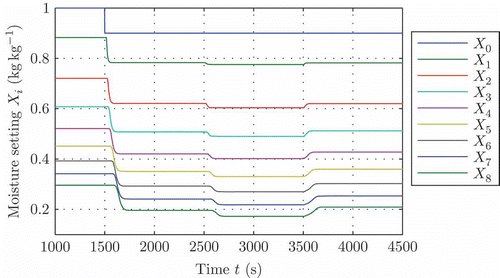
Figure 9. Sensitivity analysis of temperature levels in the dryer; the predryer consists of the drums 1–8, the main dryer of the drums 9–24.
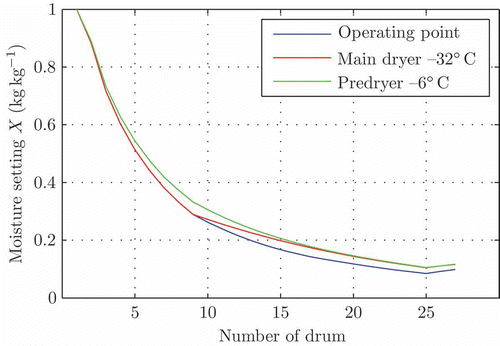
Figure 10. Dynamical Validation: (a) the output signal y with its typical variance is shown; (b) a case with measurable disturbance (fibre sheet thickness) is depicted.
