Figures & data
Figure 1. Procedure for RSM [Citation34].
![Figure 1. Procedure for RSM [Citation34].](/cms/asset/9d38cf3e-8baa-47bc-9b0b-510674b0205a/nmcm_a_2143531_f0001_oc.jpg)
Table 1. Variables that affect the damping ratio.
Table 2. Experiments and the respective results.
Table 3. ANOVA for reduced cubic model.
Figure 18. Contact spring schematic [Citation10].
![Figure 18. Contact spring schematic [Citation10].](/cms/asset/dc816270-fbb2-4d27-b742-678861a50726/nmcm_a_2143531_f0018_oc.jpg)
Figure 22. Radius ratio vs. Reynolds number.[Citation40]
![Figure 22. Radius ratio vs. Reynolds number.[Citation40]](/cms/asset/e57476dc-d38c-4fa7-b73a-24591eb6917f/nmcm_a_2143531_f0022_oc.jpg)
Figure 23. Velocity distribution with the changing eccentricity (Figures illustrate the change in maximum velocity with increasing eccentricity).
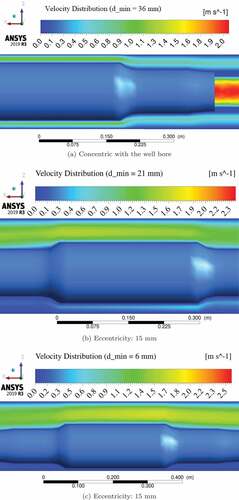