Figures & data
Figure 2. Electrostatic oiling machine. (a) Cross section. (b) Front view of the electrostatic oiling blades.
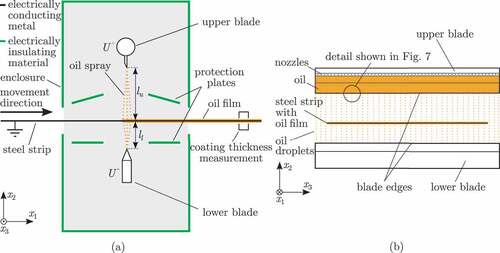
Figure 6. Photograph of the oil spray at the upper blade (lateral view, captured through inspection window of the EOM) with detail showing the measurement of the droplet velocity and diameter, scale: 1px 28 μm.
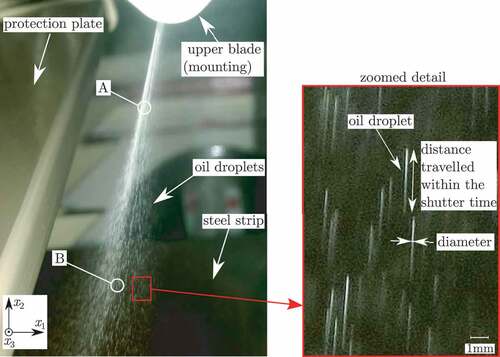
Table 1. Operating points for the parameter identification, ,
, and
.
Table 2. Comparison of (simulated) forces per unit mass acting on the droplets, positions defined in ).
Table 3. Comparison of measured and simulated absolute (mean) droplet velocities ,
and (mean) droplet radii
,
at the positions A and B, respectively,
,
, and
.
Figure 9. Simulation results without a break-up model for ,
,
, and
. (a) Droplet radii. (b) Droplet velocities.
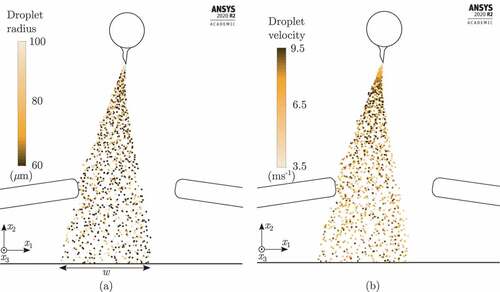
Table 4. Simulated absolute (mean) droplet velocities ,
and (mean) droplet radii
,
at the positions A and B, respectively, without a break-up model and
,
, and
.
Table 5. Comparison of calculated droplet radius limits according to (15) (for K = 0.7) with measured and simulated (mean) droplet radii at position B,
,
, and
.
Table 6. Dependence of the output variables on the input variables.