Figures & data
Figure 1. (a) Adhesion test specimen showing butt-jointed specimens consisting of 3-mm thick asphalt mastic sandwiched between two 15-mm thick by 23 mm diameter aggregate substrates. (b) Specimen with bottom substrate partially submerged to ensure water enters aggregate–mastic interface before entering bulk mastic material.
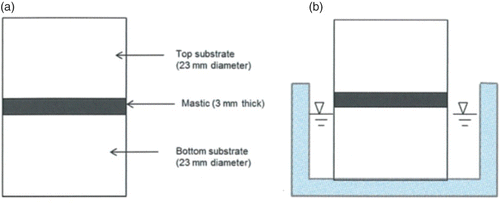
Figure 3. Asphalt mastic cohesive strength test. (a) Specimen dimensions, (b) samples in water bath, and (c) tensile strength test set.
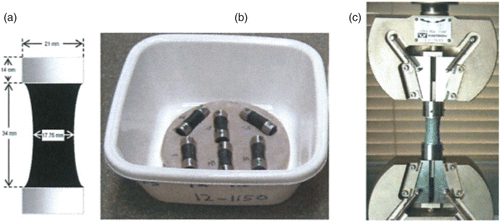
Table 1. Mineral composition of aggregates.
Figure 4. Octane sorption isotherms for aggregates (1.18 mm size fraction) used for fabricating mastics. Higher absorption for granite suggests that the aggregate is more porous than limestone.
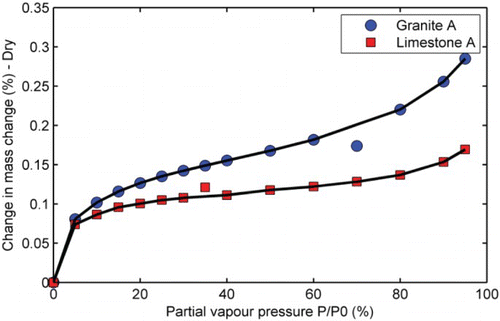
Figure 5. Water absorption in granite aggregate at 20°C. Excellent agreement between the Peleg model predictions and the measured data.
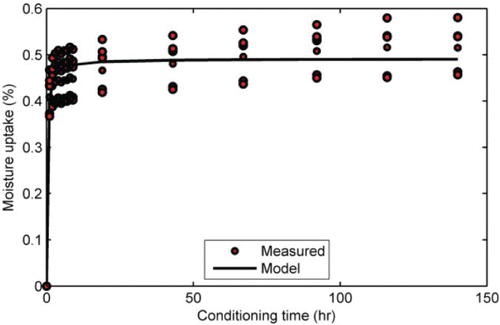
Figure 6. Moisture uptake of asphalt mastic containing different mineral aggregates and fillers. The sudden drop in moisture indicates the start of the drying phase after about 112 days of moisture conditioning. LA, limestone aggregate; LF, limestone filler; GA, granite aggregate; GF, granite filler.
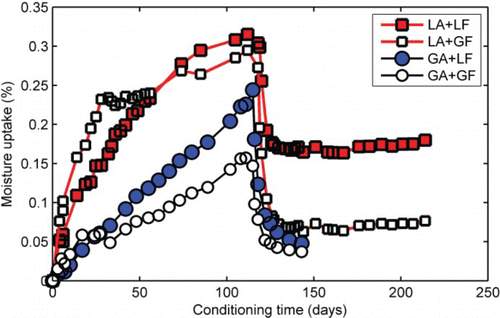
Table 2. Moisture diffusion properties of mastics.
Table 3. SFE and thermodynamic work of adhesion and debonding of aggregate–bitumen.
Figure 7. Loci of failure for moisture-induced damage in aggregate–asphalt mastic systems showing effect of conditioning time and aggregate type. (a) Mastic containing limestone aggregate and limestone filler (LA+LF) after 20 hours of moisture conditioning, (b) mastic containing granite aggregate and limestone filler (GA+LF) after 20 hours of moisture conditioning and (c) mastic GA+LF after three 168 hours of moisture conditioning. Stripping of mastic containing granite aggregates was more severe than limestone aggregate mastics.
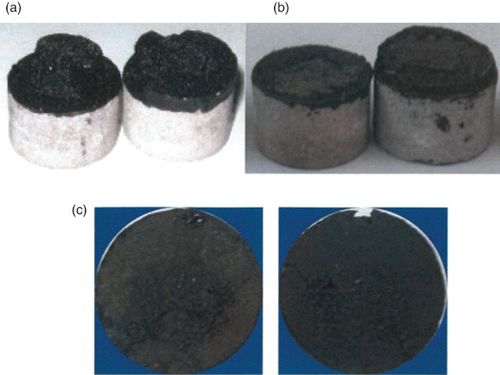
Figure 8. Effect of moisture conditioning time on stress–strain behaviour of aggregate–mastic butt joint. For majority of the mixtures, moisture conditioning resulted in strength reduction and increased brittleness. LA, limestone aggregate; LF, limestone filler; GA, granite aggregate; GF, granite filler.
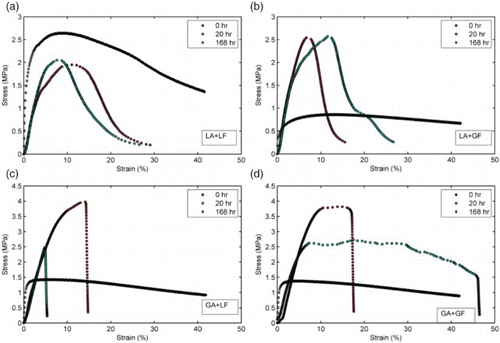
Figure 9. Effect of moisture conditioning time on bond strength of aggregate–mastic butt joints. Moisture caused negligible strength degradation in limestone aggregate mastics (a) compared to granite aggregate mastics (b). Mastics containing granite aggregates lost about 20% and 80% of their adhesion strength within the first 20 and 168 hours, respectively (c). LA, limestone aggregate; LF, limestone filler; GA, granite aggregate; GF, granite filler.
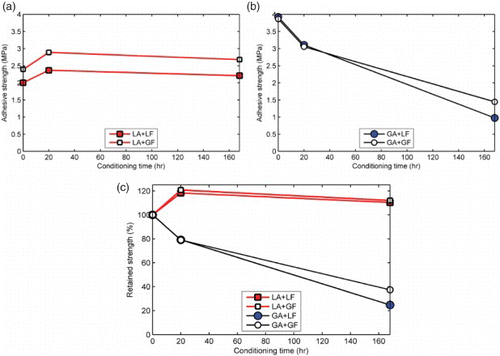
Figure 10. Relationship between aggregate-mastic bond strength and square root of conditioning time for mastic containing granite mastics. The excellent (R2=0.98) linear fit between adhesive strength and square root of moisture conditioning time suggests a diffusion process controls mastic bond strength degradation. GA, granite aggregate; GF, granite filler; LF, limestone filler.
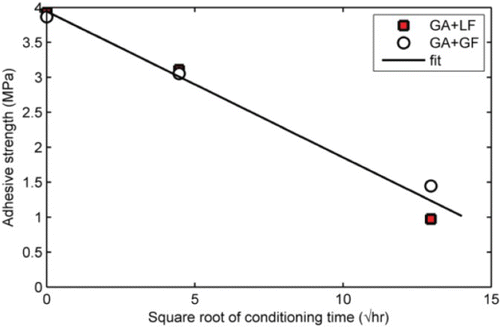
Figure 11. Effects of moisture conditioning on fracture energy of aggregate–asphalt mastic bond. Mastics containing granite aggregates retained only less than 10% of their original fracture energy after 168 hours of moisture conditioning compared to about 80–100% in the case of limestone aggregate mastics.
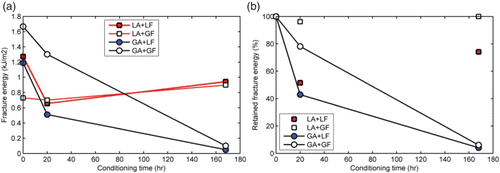
Figure 12. Aggregate–mastic adhesion strength loss versus moisture uptake and conditioning time for granite mastic GA+LF. Similar results were obtained for mastic GA+GF.
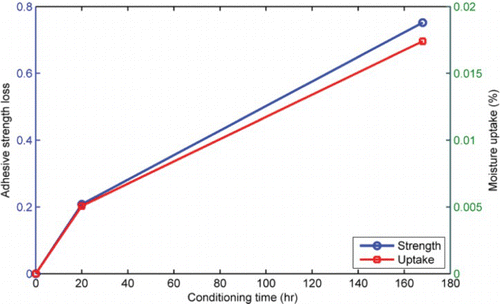
Figure 13. Correlation of moisture content of mastic with strength showing excellent correlation for GA+LF. Similar results were obtained for GA+GF.
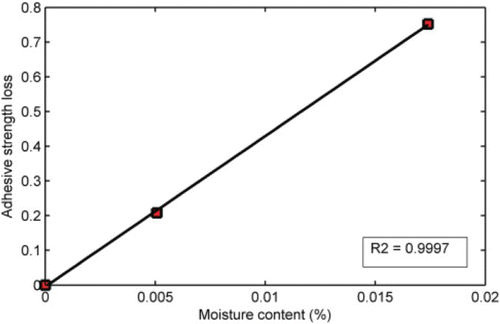
Table 4. Effect of reusing aggregates substrates on mastic adhesive bond strength
Figure 15. Effect of moisture conditioning at 20°C on cohesive strength of asphalt mastics. Tensile strength was obtained using a loading rate of 20 mm/min at a temperature of 20°C. (a) Limestone mastics and (b) granite mastics.
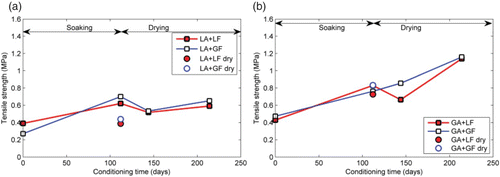
Figure 16. Effect of moisture uptake at 20°C on cohesive strength of asphalt mastics. (a) Data for asphalt mastics containing limestone aggregates and (b) data for asphalt mastics containing granite aggregates. Tensile strength was obtained using a loading rate of 20 mm/min at a temperature of 20°C.
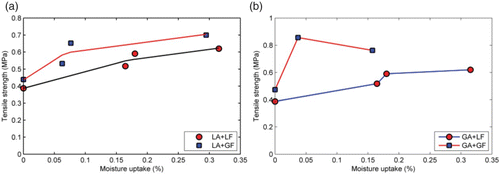
Figure 17. Effect of moisture uptake at 20°C on adhesive strength of asphalt mastics. Data for asphalt mastics containing granite aggregates. Tensile strength was obtained using a loading rate of 20 mm/min at a temperature of 20°C.
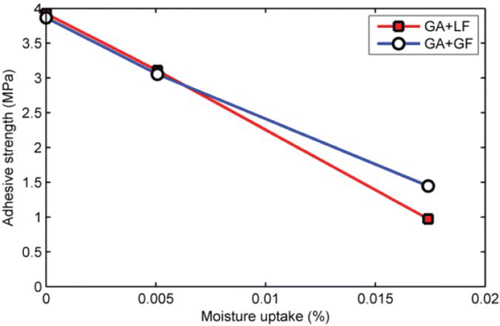