Figures & data
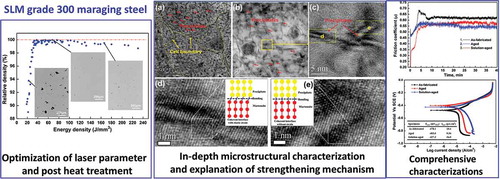
Figure 3. Representative OM and SEM images taken from the horizontal (a)–(c) and vertical (d)–(f) cross-sections of the AF specimen.
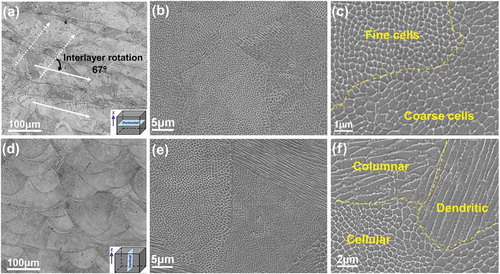
Figure 4. EBSD analysis of the vertical cross-sections taken from the as-fabricated specimen: (a) color inverse pole figure (IPF) showing grain orientation distributions and (b) corresponding pole figure (PF), (c) grain size distribution, (d) high-magnification IPF and (e) grain boundary map.
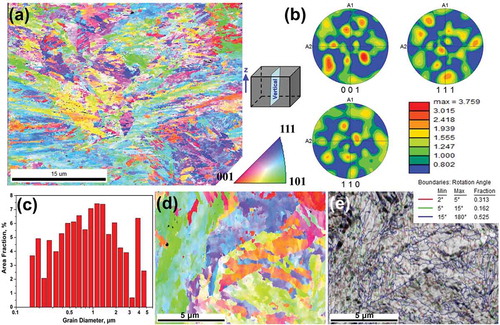
Figure 5. TEM images of AF specimen: (a) BF-TEM image taken from the horizontal cross-section showing cellular structures, (b) zoom-in image of (a) showing high-density dislocations, and (c) BF-TEM image with corresponding SAED taken from the vertical cross-section exhibiting acicular martensites.
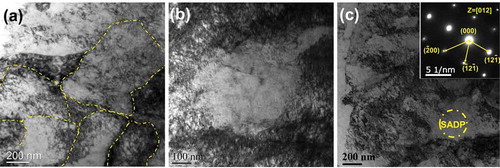
Figure 6. TEM analysis of precipitate characteristics in age-treated specimen: (a) BF-TEM overview showing massive nanoprecipitates embedded in amorphous matrix, (b) zoom-in BF-TEM image of (a) showing precipitate morphology, (c) zoom-in image taken from the given region of (b), (d) high-resolution TEM (HRTEM) image showing the coherent interface with elastic strain; and (e) HRTEM image showing the complete coherent interface.
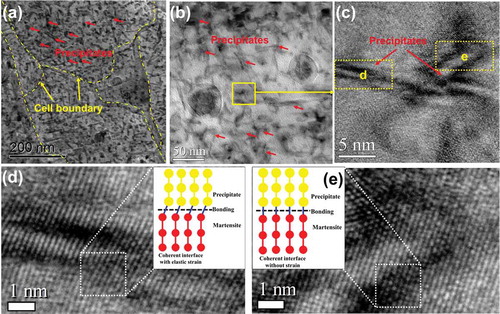
Table 1. Comparison of the mechanical properties for grade 300 MS fabricated by SLM and conventional wrought method.
Figure 8. Impact energies (a) and fracture morphologies (b) of as-fabricated and heat-treated MS specimens with horizontal and vertical building directions.
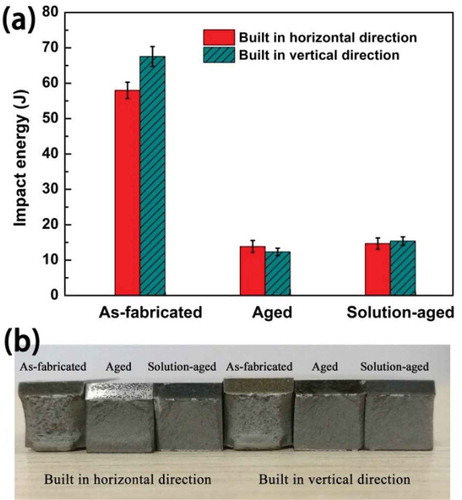
Table 2. Tribological properties of SLM fabricated MS specimens.
Figure 9. Friction coefficient (a), 3D wear track morphology (b), and sectional line profiles of wear track of SLM specimens.
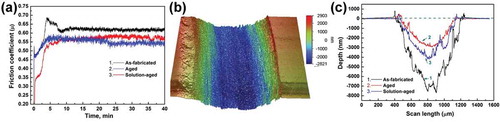
Figure 11. Potentiodynamic polarization curves and summarized relative corrosion properties of as-fabricated and heat-treated MS specimens.
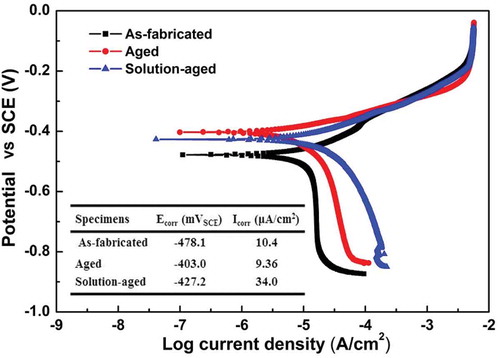