Figures & data
Figure 3. (a) Structure of directly buried ductile iron heat-supply pipeline (b) socket connection structure.
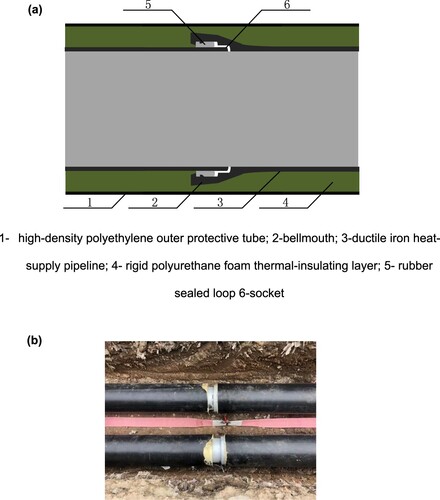
Table 1. Pipe geometry of each pipe diameter.
Figure 8. Boundary conditions for the heat transfer analysis of two-line heat-supply pipeline buried directly under the soil.
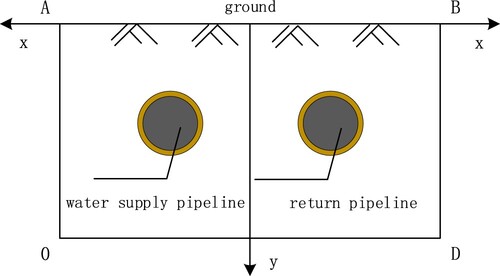
Figure 9. (a) Layer-wise temperature distribution of soil in different months (b) Monthly distribution of temperature at different burial depths.
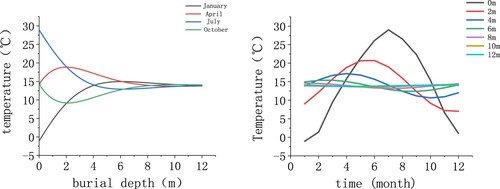
Figure 10. (a) Position diagram of adiabatic surface (b) Temperature distribution along x-axis with different burial depths; (c) simulation of temperature field in the calculation domain.
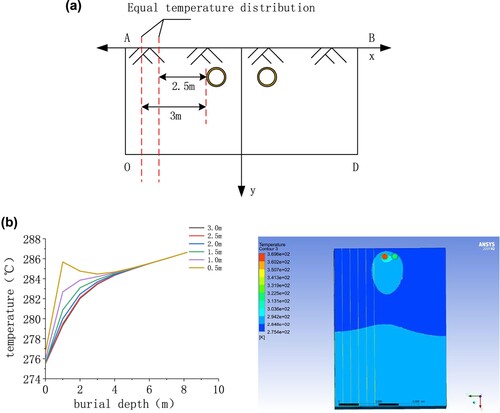
Table 2. Temperature of water supply and return pipes under 11 specific working conditions.
Figure 17. Temperature numerical solution and experimental value of main body of water supply pipeline.
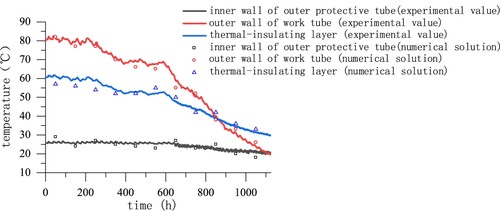