Figures & data
Figure 1. Multi-Layers Insulated Sandwich Panel with Shear Connectors (Insulated cores are removed for illustration purpose).
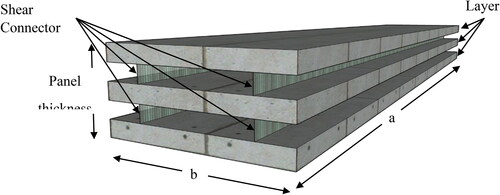
Figure 6. Shear force distribution on 5-layers sandwich panel (a) side view, (b) plate-section, (c) typical shear force diagram.
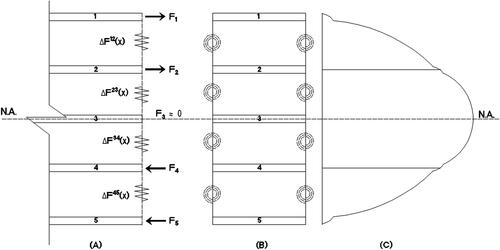
Figure 8. Multi-cell box section [Citation10].
![Figure 8. Multi-cell box section [Citation10].](/cms/asset/c2ac73f2-20df-4af1-a3c4-b117c3df2b12/umcm_a_1998736_f0008_b.jpg)
Table 1. Shear connector stiffness for single box.
Table 2. Shear connector stiffness for WF.
Table 3. Shear connector stiffness for cantilever.
Table 4. Shear connector stiffness for 2-cell.
Figure 14. Connector shear forces for 4-layers (2-cell) with different DCA: (a) 100%, (b) 75%, (c) 50% and (d) 25%.
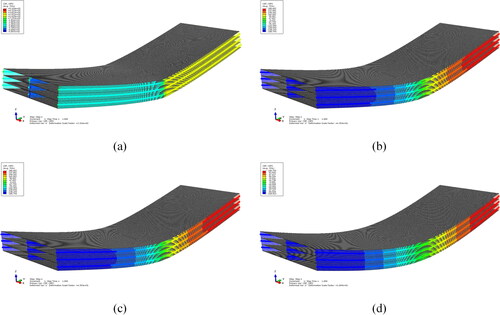
Figure 15. Connector shear forces for 4-layers (2-cell) with 100% DCA (Layer elements are not shown for clarity).
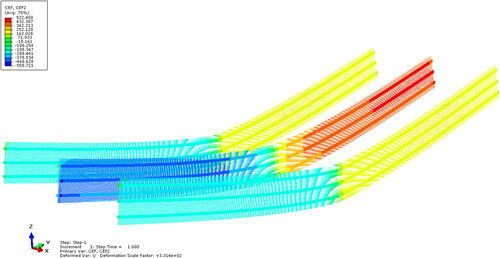
Table 5. Average stress for single box (MPa).
Table 6. Average stress for WF (MPa).
Table 7. Average stress for cantilever (MPa).
Table 8. Average stress for 2-cell (MPa).
Table 9. Geometry of different number of layers.
Table 10. Material properties.
Table 11. Shear stiffness of multi-layers sandwich panels.
Table 12. Deflection and stress results of multi-layers with CFRP.