Figures & data
Table 1. Natural rubber ingredients.
Table 2. Fixed coefficients of Yeoh and Neo-Hookean model (Khaniki et al. Citation2021; Khaniki et al. Citation2022b; Khaniki et al. Citation2022c).
Figure 11. The X-axis displacement contour of the (a) experimental test (b) finite element of the beam.
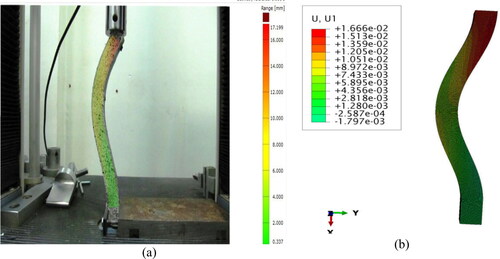
Figure 12. The Y-axis displacement contour of the (a) experimental test (b) finite element of the beam.
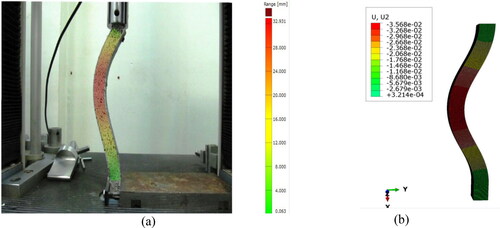
Table 3. Variations of linear eigenvalue versus geometry, material properties and eccentric loads.
Figure 19. The training, validation, test, and whole model performance evolution versus the Epoch number.
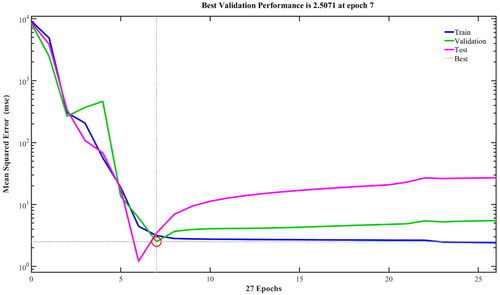
Figure 20. The regression schemes for four subsets: (a) training, (b) validation, (c) test, and (d) full evaluation.
