Figures & data
Table 1. Printing parameters for FDM-printed 3D graphene strain sensor.
Figure 1. (a) schematic of FDM-printed graphene strain sensor. 3D modeling of dog-bone-shaped strain sensor with parallel (b) and zigzag (c) direction of filament deposition. FDM-based graphene strain sensor printed, with microscope images for parallel (b1 and b2) and zigzag-patterned strain sensors (c1 and c2).

Figure 2. (a) I – V curves of the printed sensors for 45° and 180° patterns at a varying voltage gradient from 0 to 1 V. (b) sensing performance of the composite strain sensor under tension with applied strains ranging from 0.05% to 0.25%. (c) sensitivity of the sensors calculated through regression analysis. (d) calculation of gauge factor for 45° and 180° patterns. (e) response of the 45° and 180° patterns to equivalent lateral forces with different pressures for two times.
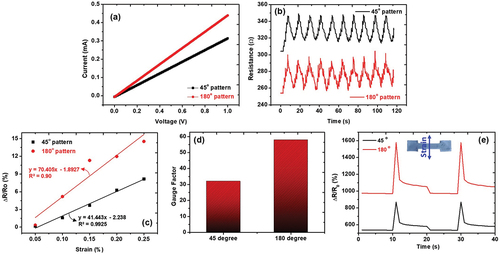