Figures & data
Table 1. Details of literature review with kind of fiber and treatment method.
Figure 2. (a) The TGA curves of UCF (black)、AACF (red) and ACF (blue) under optimal conditions. (b) the DTG curves of UCF (black)、AACF (red) and ACF (blue) under optimal conditions.
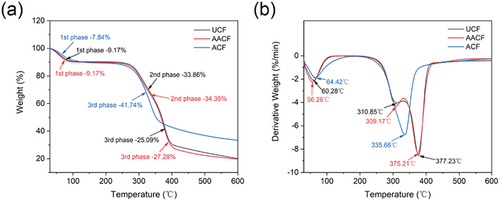
Table 2. Peak value of change in FTIR spectrum.
Table 3. ANOVA for coir fiber tensile strength.
Figure 6. Microscopic SEM images of the surface of UCF (a), a part of the surface of UCF (b), surface of AACF (c), a part of the surface of AACF (d), surface of ACF (e), and a part of the surface of ACF (f).
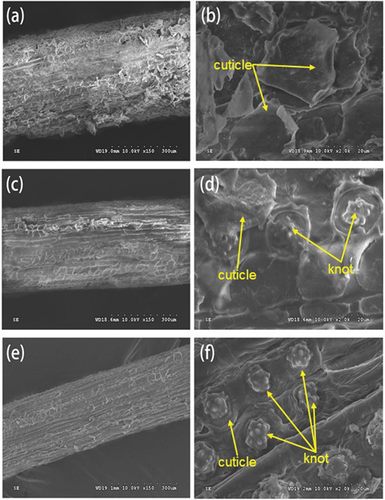
Figure 7. The tensile stress–strain curves of PEB (a), ULC (b), USC (c), AALC (d), AASC (e), ALC (f), and ASC (g).
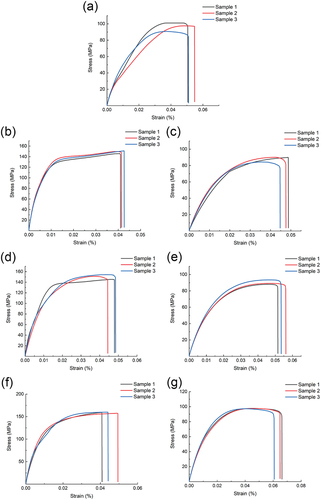
Table 4. ANOVA for composite tensile strength.
Figure 9. The flexural stress–strain curves of PEB (a), ULC (b), USC (c), AALC (d), AASC (e), ALC (f), and ASC (g).
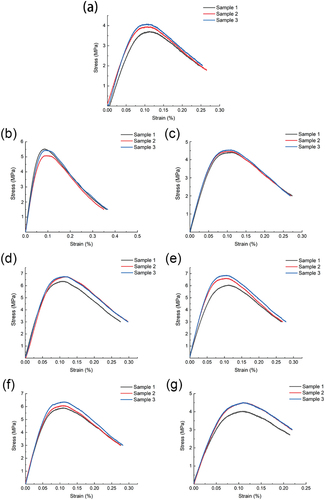
Table 5. ANOVA for composite flexural strength.
Figure 11. Microscopic SEM images of ULC fracture surface (a), USC fracture surface (b), AALC fracture surface (c), AASC fracture surface (d), ALC fracture surface (e), and ASC fracture surface (f).
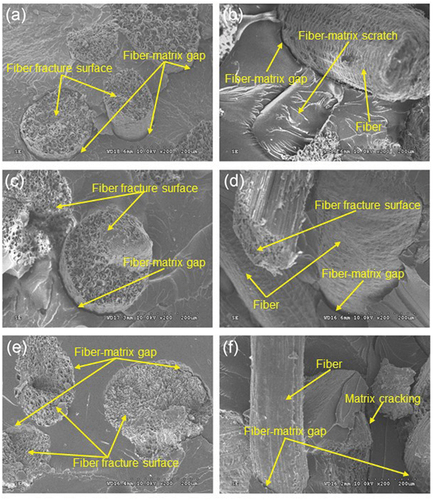
Figure 12. Percentage increase in weight of the composites at room temperature (a), Tukey test for different specimens (b).
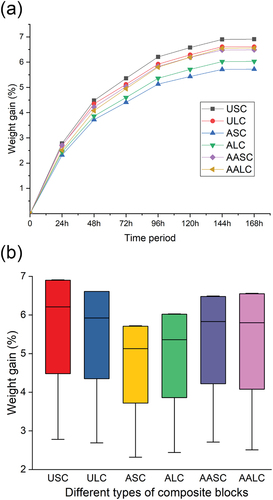
Table 6. ANOVA for composite hygroscopicity.