Figures & data
Figure 1. The shape of the profile created along the warp of the plain woven fabric; SMDwarp =18.428 mm.
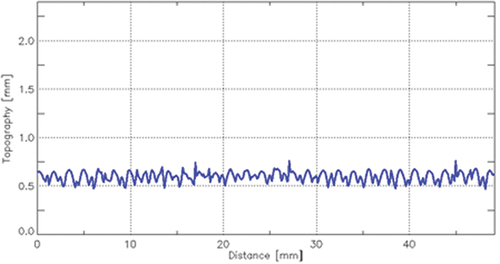
Figure 2. The shape of the profile created along the warp of the hopsack woven fabric; SMDwarp =18.481 mm.
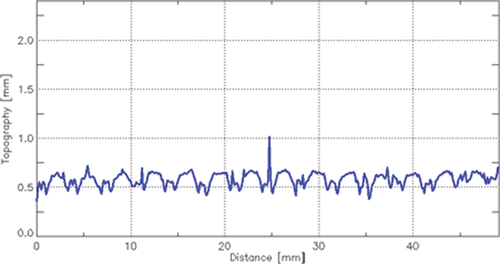
Figure 4. Relationship between the geometric structure of surface and functional properties of fabrics.
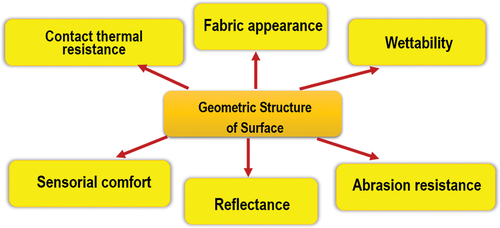
Table 1. The basic structural parameters of the investigated fabrics.
Figure 7. Exemplary picture of data from the profilometer after waviness elimination for the twill fabric.
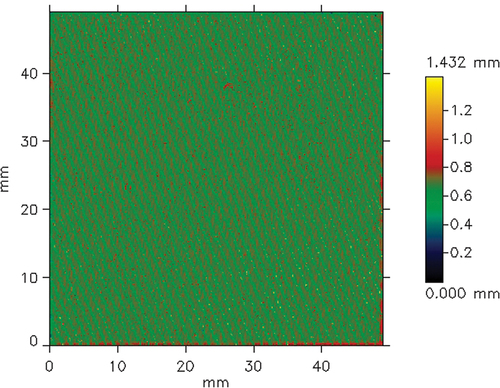
Table 2. Results of profilometric measurement of surface geometry of the woven fabrics.
Table 3. The results of the one-way Anova for the parameters characterizing the surface geometry of the investigated cotton woven fabrics.
Figure 12. Exemplary profile of the investigated fabric sample: a) placement of the profile, b) shape of the profile.
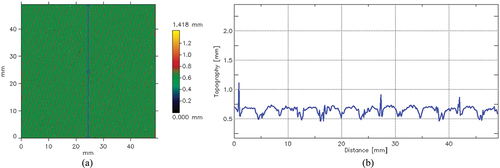
Figure 13. Exemplary profiles of the plain woven fabric: a – along the warp (blue line), b – weft (red line).
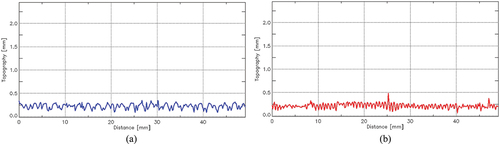
Figure 14. Exemplary profiles of the twill woven fabric: a – along the warp (blue line), b – weft (red line).
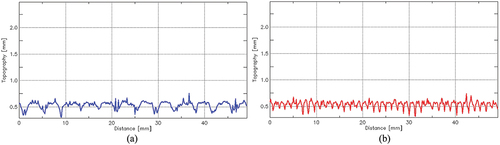
Table 4. The data from the histograms illustrated the height distribution on the fabric surface.