Figures & data
Table 1. Concrete mix proportions.
Table 2. The chemical composites of ordinary Portland cement.
Figure 3. Mode of failure for standard A) compressive strength of cubes, B) tensile strength of cylinders.
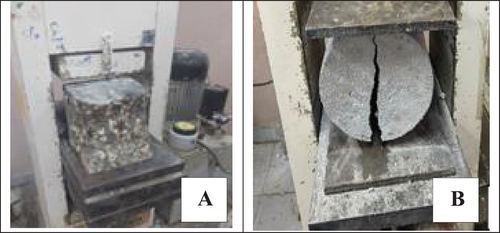
Table 3. The yield strength, ultimate strength and elongation.
Table 4. Ultimate tensile strength versus corresponding strains and modulus of elasticity of GFRP and BFRP.
Table 5. General description for longitudinal tensile reinforcement of all the tested SWB specimens.
Table 6. Presentation of first cracking load, initial crack displacement, maximum load, maximum deflection, ductility index and energy absorption for tested beams.
Table 7. FEM material properties for concrete.
Figure 18. Stress-strain relationship for steel and FRP reinforcement [Citation25].
![Figure 18. Stress-strain relationship for steel and FRP reinforcement [Citation25].](/cms/asset/49331f1d-b56f-41cf-918c-cc7eaf6664c5/thbr_a_2309818_f0018_oc.jpg)
Table 8. FEM material properties for reinforcing steel bars.
Table 9. FEM material properties for BFRP bars.
Table 10. FEM material properties for GFRP bars.
Table 11. Experimental results versus FE model results.
Table 12. Comparison between experimental results versus theoretical expectations.
Table 13. Comparison between experimental results versus theoretical expectations.