Figures & data
Figure 5. The exact time histories of the dynamic load on the 9, 77, 111, 145 nodal points (see ), which are represented by the dotted line (···), dash–dot line (– -), dashed line (— —) and solid line (—) respectively.
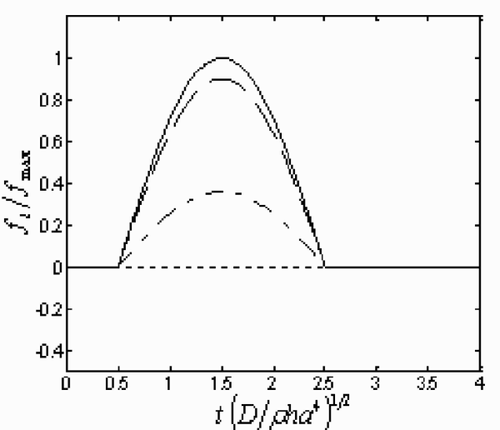
Figure 6. The time histories of the strains on the 9, 77, 111, 145 nodal points, which are represented by the dotted line (···), dash–dot line (– -), dashed line (— —) and solid line (—) respectively.
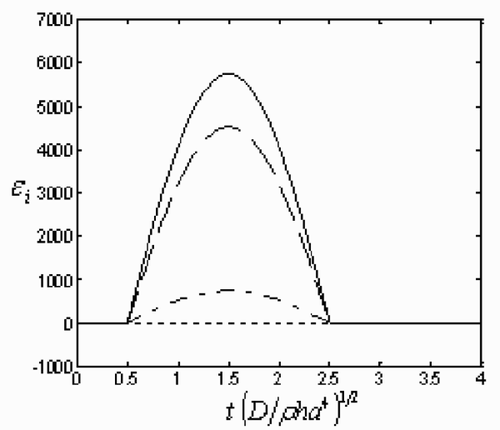
Figure 9. The directly derived time histories of dynamic load on the 5, 23, 32, 41 nodal points (see ), which are represented by dotted line (…), dash–dot line (—-), dashed line (— —) and solid line (—) respectively on the plot. Here FEM mesh division of the plate region is 8 × 8. The noise levels are: (a) 0%; (b) 0.001%.
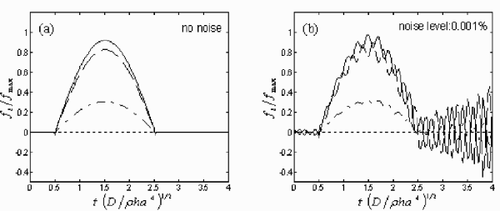
Figure 10. The regularized time histories of dynamic load on the 5, 23, 32, 41 nodal points (see ), which are represented by the dotted line (···), dash–dot line (– -), dashed line (— —) and solid line (—) respectively on the plot. Here FEM mesh division of the plate region is 8 × 8. The noise levels are: (a) 0%, (b) 1%, (c) 2% and (d) 3%.
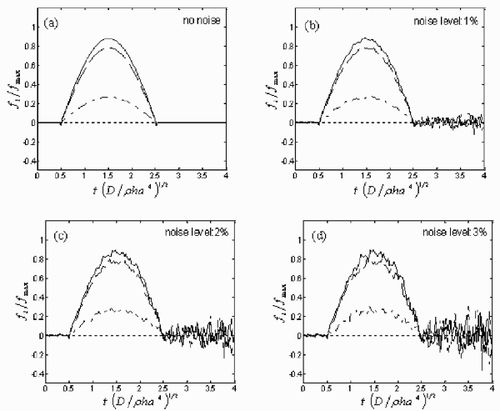
Figure 11. The regularized time histories of dynamic load at the left bottom end point P and the center point Q of the plate (shown in subplot (a)), which are represented by the dotted line (…) and solid line (—) respectively. FEM mesh divisions are: (b) 6 × 6; (c) 8 × 8; (d) 10 × 10.
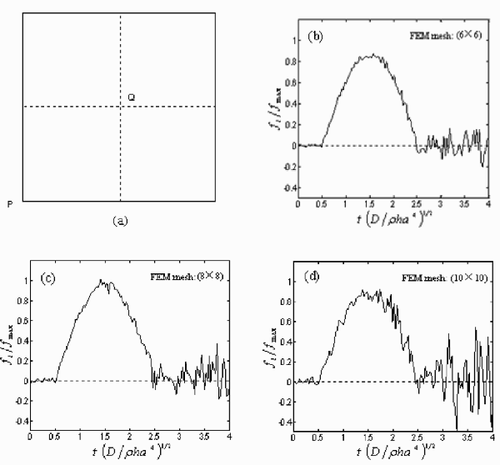
Figure 12. The regularized time histories of dynamic load on the 9, 77, 111, 145 nodal points (see ), which are represented by the dotted line (···), dash–dot line (—-), dashed line (— —) and solid line (—) respectively on the plot. Here FEM mesh division of the plate region is 16 × 16. The noise levels are: (a) 0%; (b) 1%; (c) 2%; (d) 3%.
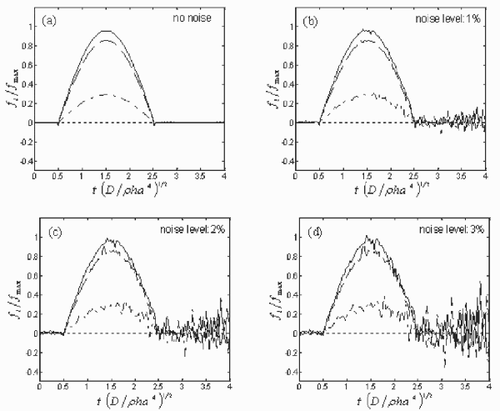
Figure 13. The regularized time histories of dynamic load on the 5, 23, 32, 41 nodal points (see ), which are represented by the dotted line (···), dash–dot line (—-), dashed line (— —) and solid line (—) respectively on the plot. γ, the real part of Laplace parameter p, is appointed as: (a) 2/T; (b) 3/T; (c) 4/T; (d) 2Π/T. The white noise level is 3%.
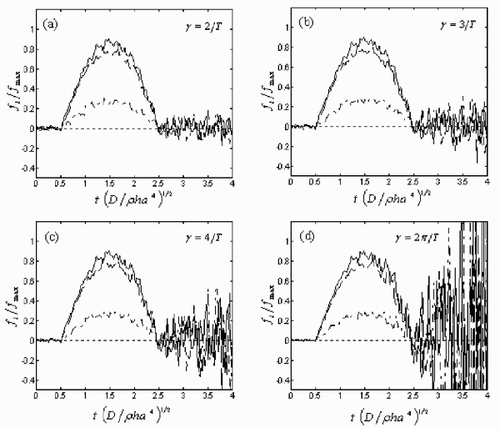
Figure 14. The exact dynamic load distributions applied to the square Kirchhoff plate at eight different times.
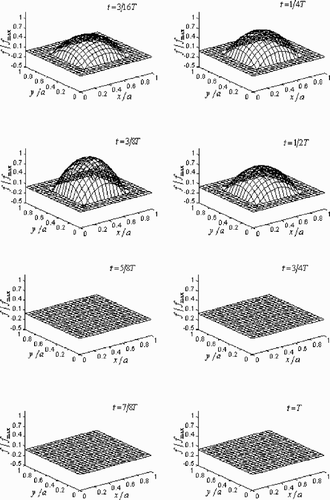