Figures & data
Table 1. Maximal and mean velocity value of the identification data in the test case 1.
Table 2. Influence of RM order.
Figure 3. u velocity field of the DM (left) and the RM n = 8 (right) for Re = 1000. Available in colour online.
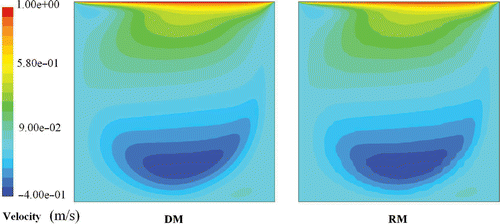
Figure 4. v velocity field of the DM (left) and the RM n = 8 (right) for Re = 1000. Available in colour online.
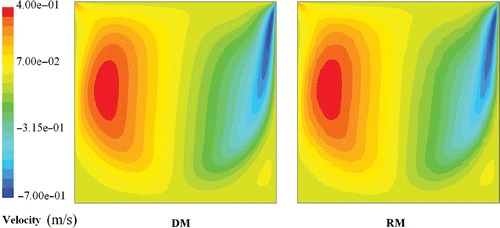
Figure 5. Stream function ψ fields of the DM (left) and the RM n = 8 (right) for Re = 1000. Available in colour online.
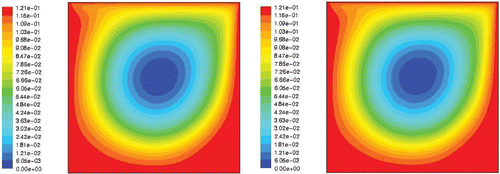
Figure 6. Vorticity ω fields of the DM (left) and the RM n = 8 (right) for Re = 1000. Available in colour online.
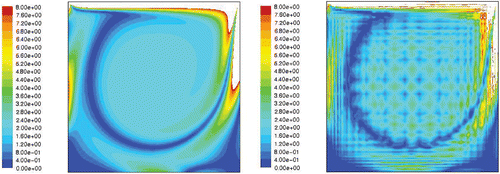
Table 3. Maximal and mean value of the DM velocity field at Re = 1000 and the corresponding errors of the RM n = 8.
Figure 7. Comparison of DM and RM: velocity profiles of u component at x = 0.5d. Available in colour online.
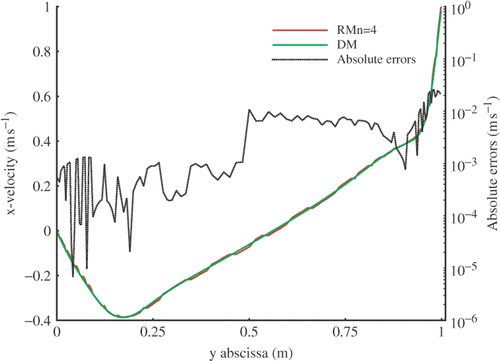
Figure 8. Comparison of DM and RM velocity profiles of v component at y = 0.5d. Available in colour online.
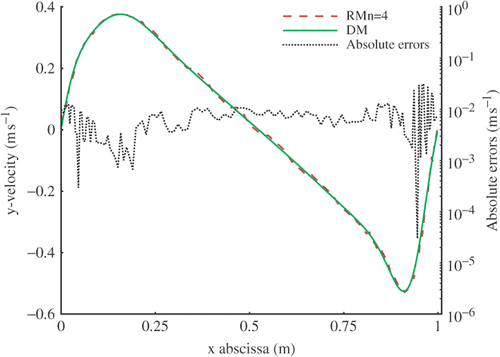
Figure 10. Centerline axial velocity (left) and axial outlet velocity profile (right) of the DM for Re = 100.
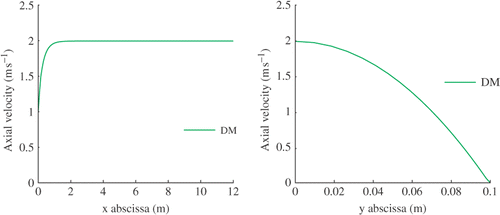