Figures & data
Figure 1. Flow chart for numerical optimization, where the geometry modification is based on numerical minimization scheme, not the flow physics.
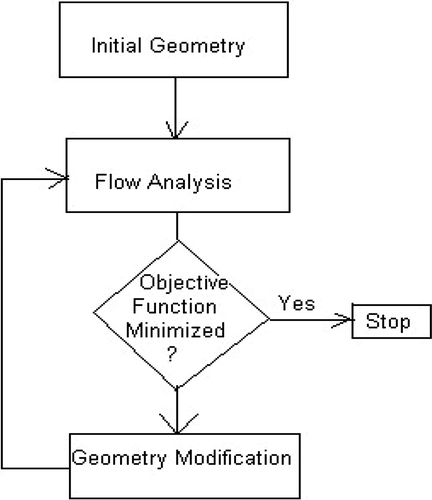
Figure 2. Flow chart for hybrid inverse method, which requires convergent solutions for both analysis solver and inverse solver in each blade modification iteration (BC–boundary conditions).
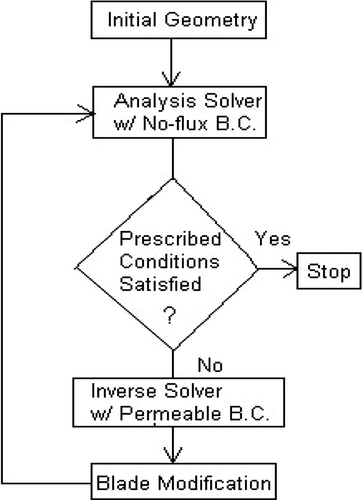
Figure 3. Flow chart for the current inverse method, where the blade modification is an integrated part of the time-marching iteration (BC–boundary conditions).
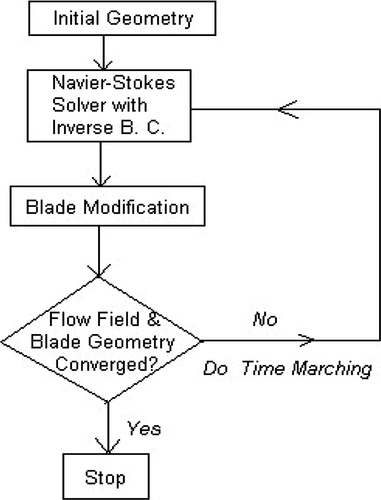
Figure 4. (a) Rotor 67 efficiency and total pressure ration comparison and (b) Rotor 67 exit spanwise profile of total pressure and total temperature comparison. INV3D vs. test data.
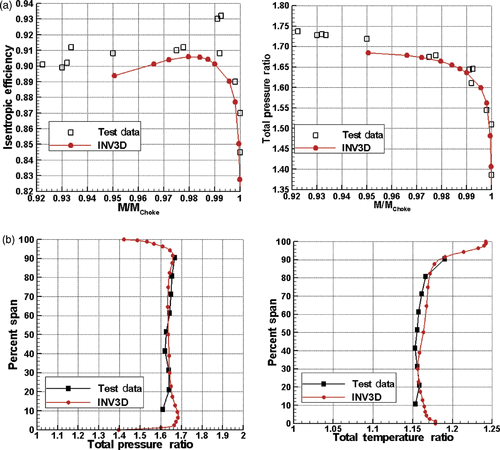
Figure 6. Numerical instability in camber generation when tip clearance is present. The circles represent the camber wrap angle calculated from the direct integration of camber control equation (Equation Equation13(13) ).
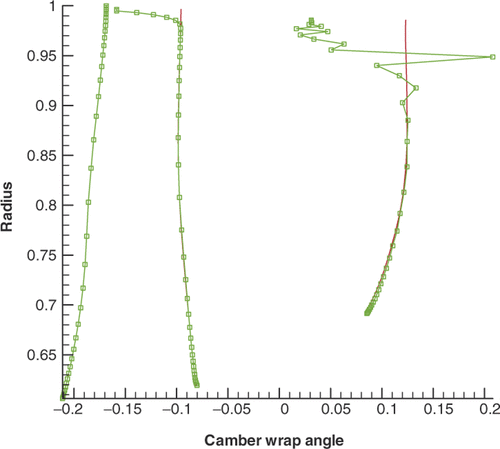
Figure 8. Blade geometry at (a) hub, (b) midspan and (c) tip. Solid line: target blade; Dash line: initial blade; Circle: blade produced by inverse method.
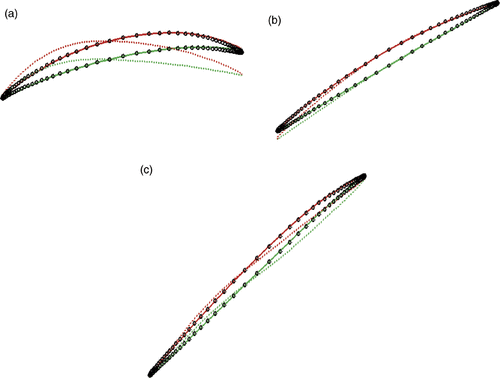