Figures & data
Table 1. Grid, number of iterations and CPU time for a test case.
Figure 8. (a) Geometries of Michael nozzle and initial guess. (b) Initial and target wall pressure distributions.
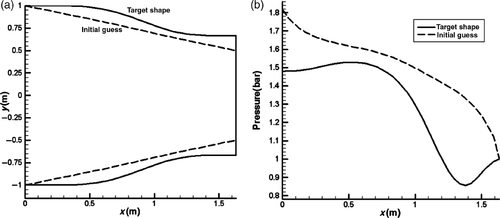
Figure 14. (a) S-duct geometry after 350 modifications with the target shape and (b) their corresponding wall pressure distributions.
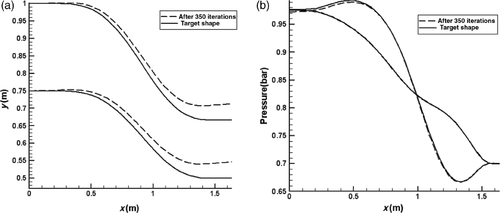
Figure 16. Wall shape modification from straight convergent duct to the supersonic nozzle with normal shock.
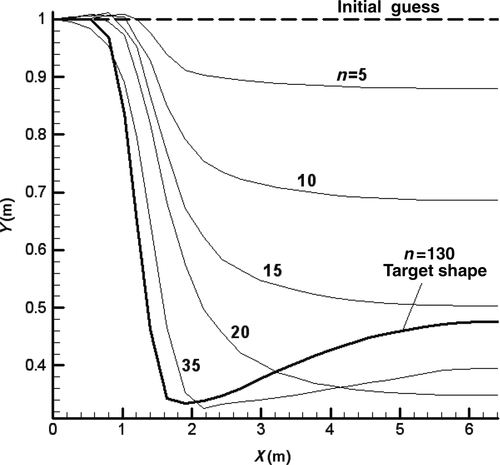