Figures & data
Table 1. Thermophysical properties of the mould and part constituents.
Table 2. Kinetics parameters for THERMEL1 natural rubber.
Figure 3. Example 1, cooling inside the mould – – Temperatures and vulcanization rate computed at different points of the part.
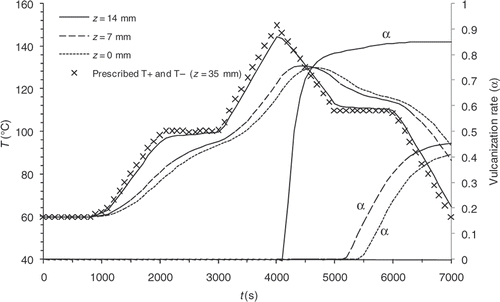
Table 3. Discretization of the prescribed temperatures.
Figure 4. Experimental and theoretical temperature values achieved in different points of the moulded part during a moulding cycle.
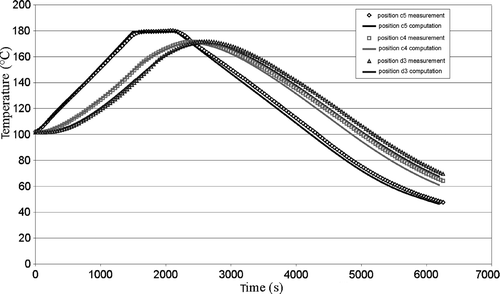
Figure 5. Comparison between the vulcanization front position obtained experimentally (a) and calculated (b).
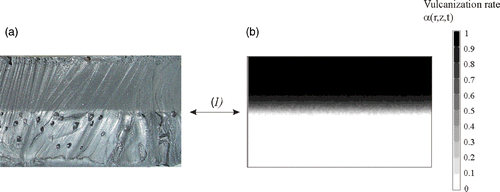
Figure 6. Example 2, 1000 s cooling outside the mould: ,
– temperatures and vulcanization rate computed at different points of the part.
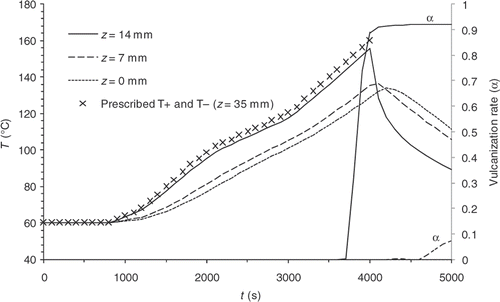
Figure 14. Least squares criterion versus iteration numbers – a: Example 1 (Nt = 12); b: effect of the initial cycle; c: Example 1 (Nt = 1).
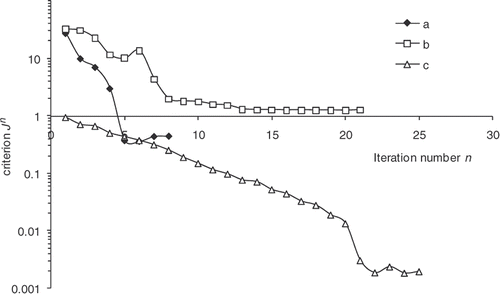
Figure 20. Vulcanization rate within the part thickness – a: desired vulcanization rate; b: vulcanization rate obtained with estimated cycle; c: vulcanization rate obtained with initial cycle.
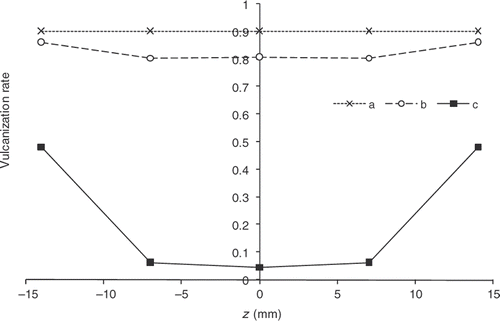
Figure 22. Chemical reaction progress within the part thickness. Desired vulcanization rate: 0.9 – a: α obtained at the end of heating in the mould with the estimated cycle, b: α obtained at the end of heating in the mould with the initial cycle, c: α obtained at the end of cooling outside the mould with the estimated cycle, d: α obtained at the end of cooling outside the mould with the initial cycle.
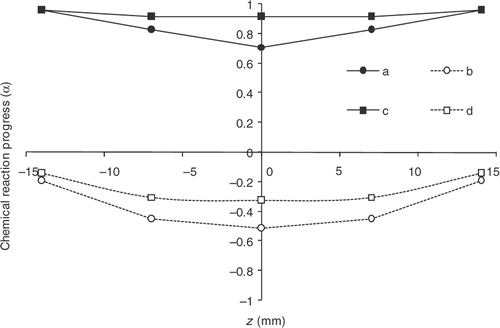