Figures & data
Figure 1. Computational grid in a curved nozzle with various control volumes and boundary conditions.
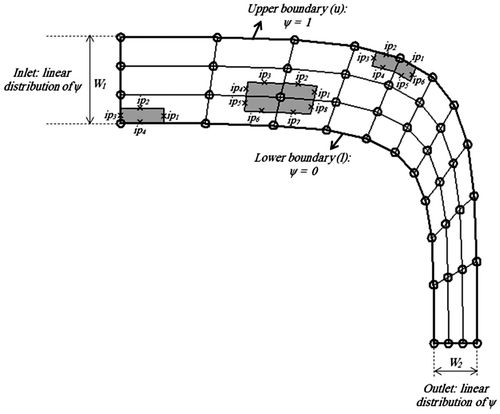
Figure 4. Three Solution algorithms in the context of duct design problems: (a) proposed and classical iterative algorithms (b) direct design.
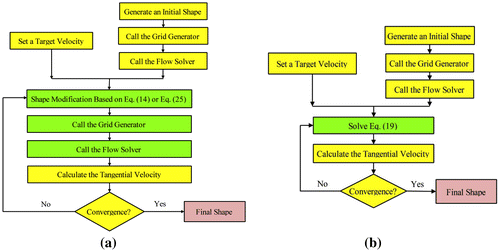
Figure 5. Boundary control volumes in the proposed algorithm: (a) inappropriate control volumes, (b) appropriate control volumes.
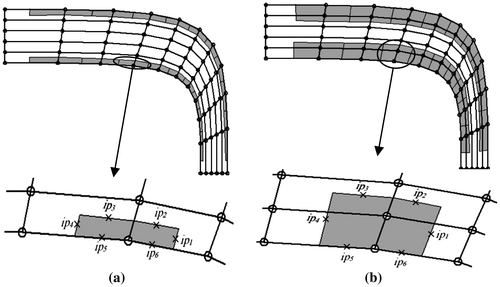
Figure 7. Design of a curved nozzle: (a) Initial guessed and final shape, (b) Tangential velocity for initial guessed and final shape.
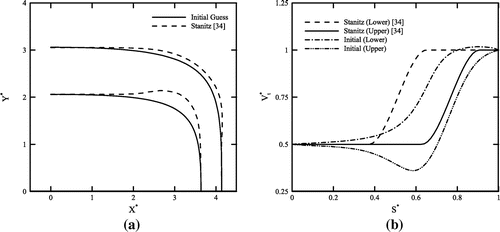
Figure 10. Design of a straight nozzle: (a) initial and final shapes, (b) initial and target tangential velocity distributions.
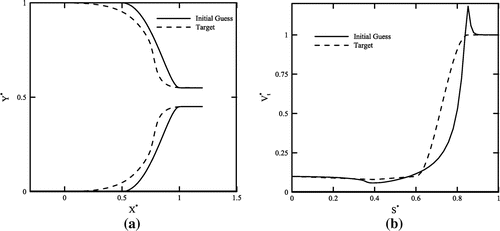
Figure 12. Design of a s-shaped nozzle: (a) initial and final shapes, (b) initial and target tangential velocity distributions.
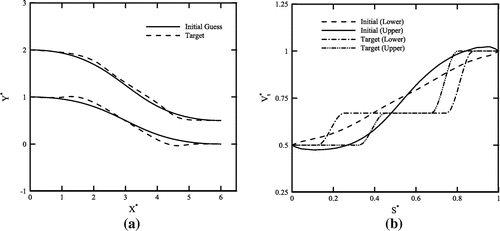
Figure 14. Computational grid in a conducting body with various control volumes and boundary conditions.
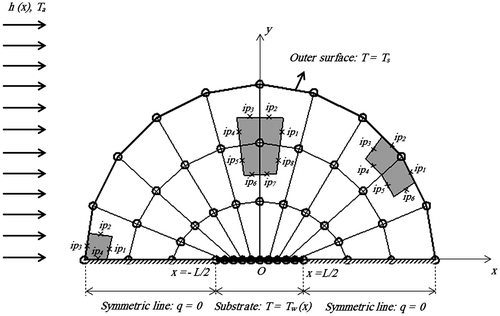
Figure 15. Design of a conducting body with uniform substrate temperature: (a) initial guess with computational grid, (b) final shapes obtained by three different algorithms introduced in this study.
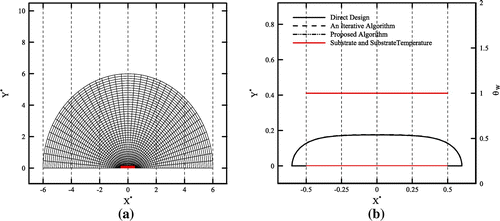
Figure 17. Design of a conducting body with linear substrate temperature: (a) initial guess with computational grid, (b) final shapes obtained by three different algorithms introduced in this study.
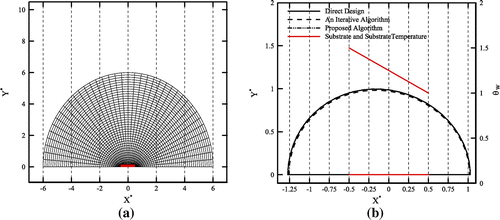
Figure 19. Design of a conducting body with nonlinear substrate temperature: (a) initial guess with computational grid, (b) final shapes obtained by three different algorithms introduced in this study.
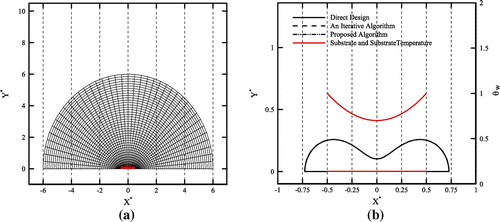
Figure 20. Convergence histories in the conducting body with nonlinear substrate temperature example.
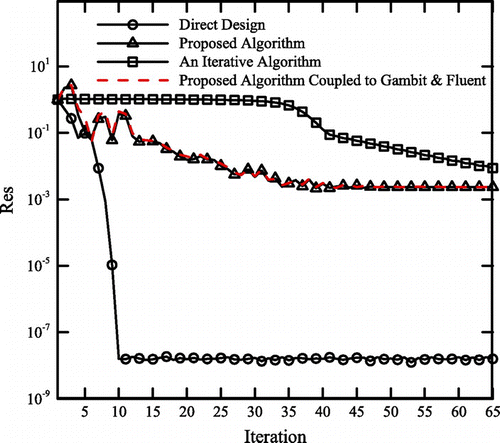